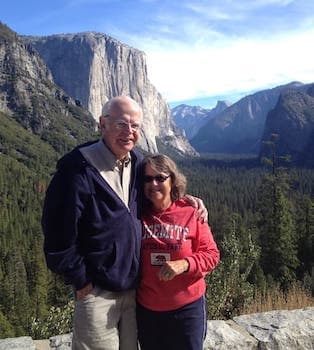
Curated with aloha by
Ted Mooney, P.E. RET
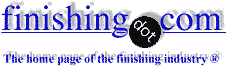
The authoritative public forum
for Metal Finishing 1989-2025
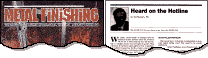
-----
Black anodize turning bronze color
Q. We have some aluminum parts that were black anodized. Alloys 6061 and 5052 were used in the same assembly. When the units were returned from the field, the anodize had changed to a bronze appearing color on both the 5052 and 6061 parts. The units are not exposed to sunlight or adverse atmosphere in installation so I wouldn't expect fading to be an issue. Does anyone have an explanation of what is happening here?
Lou Volka- Farmingdale, New York
2002
----
Ed. note: Fading of black anodized parts is a very common problem, addressed countless times on this site, so readers may also be interested in
- letter 2459, "Discoloration of Black Anodized Aluminum Parts"
- letter 22602, "Black Anodized parts fading to brown / bronze",
- and letter 31658, "Black anodized parts fading - Non-UV cause".
A. Heat can make black anodize parts fade to bronze or gold in a hurry. A poor seal will accelerate the process.
Victor Waldman- Naugatuck, Connecticut
A. I suspect that the parts were poorly sealed...poorly sealed parts will fade even if exposed only to fluorescent light. Another, but less likely culprit, would be inadequate coating thickness, or perhaps the dye used had very poor lightfastness. You didn't say how long it took for these parts to fade, but I'd bet my lunch on the bad seal.
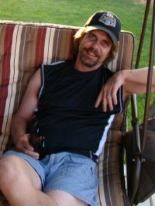
Marc Green
anodizer - Boise, Idaho
A. 1. The first thing that comes to mind is inadequate sealing.
2. The second thing is iron contamination in the rinse water and/or the seal.
3. The third thing is copper in the anodizing solution from previous 2000 series alloy work where the copper is so high in concentration that it occludes in the pores later to bleed due to, again, inadequate sealing.
4. Also, some very cheap black dyes are very fast to fade, ask the vendor what the light fastness number is on the black dye he is using, it should be 7 or 8.
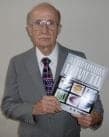
Robert H Probert
Robert H Probert Technical Services

Garner, North Carolina
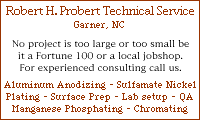
My thanks to all of the responders to my question of black anodize fading to a bronze color. You all seem to have a consensus that poor sealing is the culprit. I will be taking this up with the anodizer.
Thanks again for your help.
- Farmingdale, New York
2002
A. No problem, Lou.. its nice to get a "Thank You" every once in awhile! Send your anodizer a coupon of the same alloy as your parts, have him run it with his next load, then ask him to preform a dye-stain test. If he's worth his salt, he'll know how to preform the test, and it will pass.
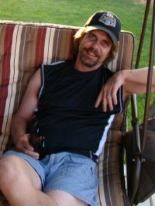
Marc Green
anodizer - Boise, Idaho
A. As to the discoloration on your black anodized parts, what type of process did the parts go thru prior to anodizing? If you get any oxide impregnated into your part, that will cause surface rust to start to bleed thru the anodize. Maybe someone used some type of oxide sandpaper to deburr the parts?
Ed Menchaca- Whittier, California
Multiple threads merged: please forgive chronology errors and repetition 🙂
Black hard anodize is turning brown
Q. I have a black hard anodized finish in accordance to MIL-A-8625 / MIL-PRF-8625
[⇦ this spec on DLA] C, type III, Class 2, applied onto a aluminum plate 6061-T651/T652. These anodized parts are sitting in some facility in Asia. We have an initial report of rusting, on parts that have a Nitrite finish. This is still under investigation. Today I got some pictures of Black Anodized finish with brown discoloration. I have never seen this on anodize and I am wondering if anybody has seen this type of problem before. I have some pictures to share with you...
Any info would be great.
Gerry Piccone
- Montreal, Quebec, Canada
2005
A. Yes I've seen it plenty! It's the lack of a quality seal (or possibly no seal at all!). The mil spec is ambiguous when it comes to Class 2, Type III dyed hardcoat. The spec mandates "unless otherwise stated, Type III coatings shall be unsealed." Now anodizing house supplies unsealed dyed anodic coatings, however, where is it otherwise stated to seal the dyed hardcoat. Our shops take on it is that sealing is implicitly stated by indicating the parts are to be dyed.ASTM B136, anodic seal integrity test will quickly tell you if the parts are sealed or not - if you drop a little nitric on it and it turns instantly white, it's not sealed! The safest thing for an OEM or designer when calling out Type III, Class 2 coatings is to specify "nickel acetate or equivalent seal required."
P.S. Of course I might be wrong! If your nitrided parts are prematurely rusting, is it possible that your parts are in an overly aggressive corrosive environment that no coating can withstand. I recently had a relative spend a couple of weeks in China, Shanghai in specific, and he came home with a terrible cough he blamed on the air there. It took him a month for his throat to recover.
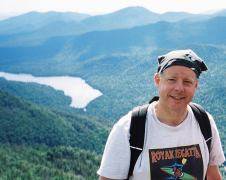
Milt Stevenson, Jr.
Syracuse, New York
Q. We have type II, class 2, black anodized aluminum parts that are fading to a bronze/brown color (in a matter of a few months) except where someone has a finger/hand print. Military spec is 7.1.2
Some of the parts were single and some were duplex sealed.
The thickness of the coating is .7 mil
The ADT is 609
The coating weight is acceptable >1000 mg
Not sure if it is the organic dye or a bad sealing process. We have used two different platers with the same results.
Need help,
- Huntsville, Alabama
2005
Black Anodising Turning Blotchy & Bronze
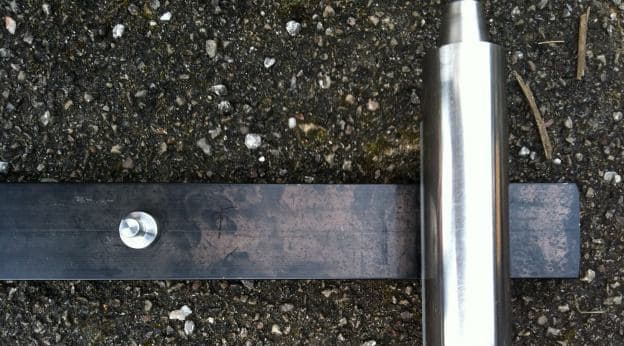
Q. Hi,
I'm puzzled as to why the new equipment I bought 2 months ago has started to show fading on the black anodised parts.
The only thing that may have come into contact with the anodising is possibly a cleaning product a trainee used. It's a foam cleaner called AFC antistatic foam cleaner.
www.electrolube.com/products/maintenance-service-aids/130/105/
I did a test on the underside of the same anodised parts over several days by spraying it on & leaving it but it hasn't had any effect.
Thanks in advance,
Kevin
- United Kingdom
April 9, 2014
A. Suggestion. Do a seal test and re-post.
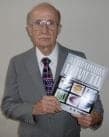
Robert H Probert
Robert H Probert Technical Services

Garner, North Carolina
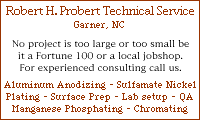
Q. Thanks for the reply.
I'm the end consumer for this product. Do you suggest I go back to the manufacturer and request a seal test?
This equipment is track used on film sets so in my mind it's highly unlikely the anodising has come into contact with anything aggressive enough that could do that, Industry standard WD-40
⇦ this on
eBay
or
Amazon [affil links]
is the only thing regularly used to free run the wheels on the track.
The finger markings and strange blotchy appearance looks as though it has been in contact with a liquid. Although what look like splatter marks are in reverse i.e. dark & not faded.
I know it's very tricky, but I wanted to at least have some clues to the possibilities of how this could happen before taking this up with the manufacturer.
Thanks
Kevin
- United Kingdom
![]() |
A. The fading or turning purple/bronze is common with an organic based dye. You need a metallic based one. Note that I am not referring to architectural 2 step anodizing. - Navarre, Florida A. Kevin - Colorado Springs, Colorado A. Unsealed or partially sealed anodic pores will bleed and smear dye from humidity cycling of the air. WD-40 solvent will pick-up and smear dye from unsealed or partially sealed anodic pores. Do an ASTM B136 seal test and re-post. ![]() Robert H Probert Robert H Probert Technical Services ![]() Garner, North Carolina ![]() |
First off, thank you very much everyone for their valuable input, it's very much appreciated.
In reference to the ASTM B136 seal test. Unfortunately, as I understand it, this type of test is beyond my facilities and capabilities. However, the light test will be very easy for me to perform in a controlled manner and I will undertake this immediately. As soon as I have some results I'll post them up here.
Thanks again.
Kevin
- United Kingdom
Q. Hi again,
I did a light test as suggested by Willie Alexander.
This came up with a positive result. The light source was a small focused circle of light about an inch across on the underside of the anodised sleeper part of the track. Part of the light falling onto the anodised surface was masked using gaffer tape.
I will post some before/after pictures to show how the anodising has faded where the surface was exposed to the light source, and remained darker where it was covered up.
Any suggestions as to why this has happened are extremely welcome. Also, any advice on if or how I should approach the manufacturer would be much appreciated. Bearing in mind I am an end consumer/purchaser of the equipment and do not have anything to do with the commissioning or manufacturing processing of it.
Thanks in advance.
Kevin
- United Kingdom
April 15, 2014
A. OK, so you cannot do the ASTM test with nitric acid, then at least dip a cotton ball inacetone ⇦ this on eBay or Amazon [affil links] Warning! highly Flammable! or alcohol, and wipe it across the black dyed surface - if it picks up black color, then the pores are NOT sealed.
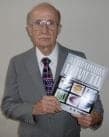
Robert H Probert
Robert H Probert Technical Services

Garner, North Carolina
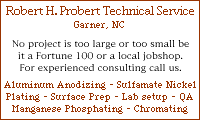
A. Kevin, Robert is most likely correct in that the parts probably weren't sealed well. A couple of other causes could be that the black dye used in the anodizing process did not have good light-fastness properties, or that the coating was not thick enough to allow the dye to absorb deeply into the pores.
Keep in mind that dyed anodizing is not the best coating for continuous exposure to light, and it will eventually fade, even if it is properly applied, and sealed. But certainly you should expect much better results than what you're currently seeing.
Regardless, you are an unhappy customer whose purchase is not performing up to par. As with anything else you'd buy that didn't perform as expected, I'd return the product, and ask for a refund, or a replacement. It would be up to the manufacturer to stand behind their product. Obviously some do, and some don't. If they don't, I guess you're stuck, and chalk it up to a lesson learned not to buy equipment from that manufacturer again.
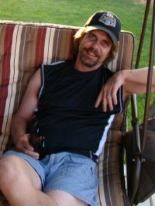
Marc Green
anodizer - Boise, Idaho
Treatment &
Finishing of
Aluminium and
Its Alloys"
by Wernick, Pinner
& Sheasby
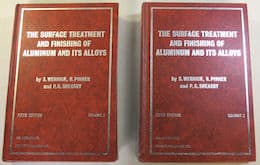
(note: this book is two volumes)
on eBay or
AbeBooks
or Amazon
(affil links)
Q. Hi All,
thanks for the responses.
I tried wiping the surface with what I believe to be pureacetone
⇦ this on
eBay
or
Amazon
[affil links] Warning! highly Flammable!
(Care+ Acetone Household Solvent) but it doesn't say on the bottle. I didn't get any residue left on the cotton wool.
So I have black anodised surface which isn't light fast but also doesn't leave residue.
Does this help at all to give a rough diagnosis or opinion of what's wrong? Is it not the sealing what is the problem but rather the lightfastness of the dye used?
I have written to the manufacturer and included the photos so will await a reply. It's easter weekend here in the UK so I won't expect to hear back until maybe mid next week.
Thanks again
- United Kingdom
A. Hi Kevin. Although your acetone rub test is not as conclusive an indicator of proper sealing as more formal tests, yes the sealing sounds okay, and the dye may be the problem. Can you determine the manufacturer, type of dye, and lightfastness rating?
Regards,
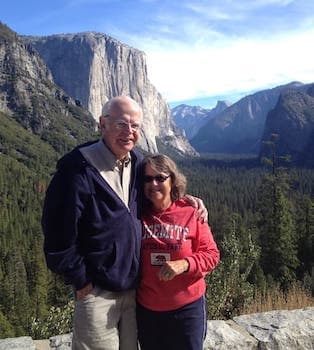
Ted Mooney, P.E. RET
Striving to live Aloha
finishing.com - Pine Beach, New Jersey
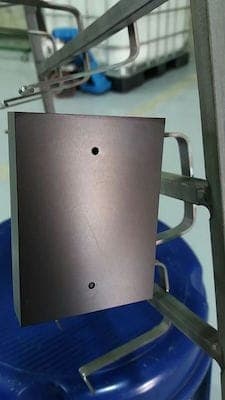
Q. We recently face uneven black Colour on Al 6061, which go for anodizing at thickness more than 15 microns, black dye with Japanese dye maker and nickel acetate salt hot sealing at 80 °C, the uneven black coating was found at the upper right corner of the part. Can anyone to help to solve this problem?
engineering services - SINGAPORE
October 16, 2016
A. Anthony
The blemish looks like chemistry dried on it during a tank transfer, or the part was not completely submerged during the dye or seal step.
- Green Mountain Falls, Colorado
Hi Willie,
Thank you very much for your advice, we will reduce the transfer time between tanks and see it any improvement...
...
Hi! Willie, the problem already solved.
Thanks once again for your advice.
Best regards,
- Singapore
October 20, 2016
Q. A lot of great information here, but I'm not completely positive that my case is a seal problem. I have a 5051 aluminum part that is black anodized. This part has 2 lasers that are placed on it. Each laser has an adapter plate that fits right into this shelf. The area under the adapter plate is still fine, you can even see the outline of the plate, but everywhere else is a different color. I originally suspected heat, which could still be the case, but after some investigation, it could also be UV light exposure (the lasers are in the UV spectrum, but should not be leaking like this). I appreciate your comments! Thanks.
- San Jose, California
February 9, 2017
A. I would suspect it's the UV exposure, which can lead back to a poor seal, inadequate anodizing thickness, or choosing a black dye that does not have good light fastness (albeit most of the black colors do). If it's extreme UV exposure, then dyed anodizing may not have been the appropriate choice in coatings.
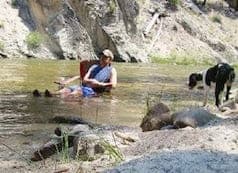
Marc Green
anodizer - Boise, Idaho
February 11, 2017
Type 3 black hard anodize turning purple
Q. So we sent off a batch of parts after type 3 hard black anodize and several months later were rejected for turning a purple/reddish color film. The parts originally seemed to be a bit duller than we would have liked, but to be honest I have ZERO experience in an anodizing shop. When we received the parts back I took a paper towel with 90% alcohol and began cleaning them. The paper towel turned black immediately.These parts require particular holes to be masked and chem-filmed. They were rejected back to our vendor to be re-chem-filmed due to splotchy/corroded areas. My understanding is that they were left in an etching bath too long causing a breakdown in the anodize seal when performing the chem-film rework.
1) Is my understanding of the issue correct?
2) Can these parts be cleaned and re-sealed? Stripping and re-anodizing is out of the question due to bores toleranced at ± .0002"
3) Is there any way for me, quality at a machine shop, to recognize issues such as this without the fancy (read expensive) test equipment anodize shops have access to?
- Parker, Colorado, United States
January 5, 2018
Ed. note: This RFQ is outdated, but technical replies are welcome, and readers are encouraged to post their own RFQs. But no public commercial suggestions please ( huh? why?).
A. Hi Sean. I'm slightly confused about who "you" and "they" are. Sounds like the ultimate customer orders the finished parts from you and you order the anodizing and chem-film services from others? But what sounds strange then is that the parts were rejected by your customer and sent back to the anodizing/chem-film shop for rework without you having a chance to see what was originally allegedly wrong with them, and now after re-work they are worse?
Since you sound like you'd like an intro to the technology, let's go through what is most common practice: hard anodized (Type III) parts are usually neither dyed or sealed; they are (depending on the alloy) charcoal or "blackish" in color as a natural consequence of the alloying materials in them. And they are not sealed because that softens them. But this is not to say that they can't be sealed and dyed like Type II parts, and even on this page there is a discussion of that approach. I am quite certain you have dyed parts.
You say the holes are chem-filmed rather than anodized, so re-anodizing should not affect the tolerance unless I am misunderstanding. You mask the chem-filmed holes and then proceed to re-anodize. Topic 33933, "Masking/stripping when chromate conversion and anodizing on same part" should give you a good introduction to what is involved in partially anodizing and partially chem-filming/chromate conversion coating (either can be done first). Whether re-anodizing, dying, and sealing actually has a real chance of working, however, I can't say because I'm a book-knowledge guy, not an anodizer. Hopefully one of our many readers who are experienced anodizers will weigh in :-)
Regards,
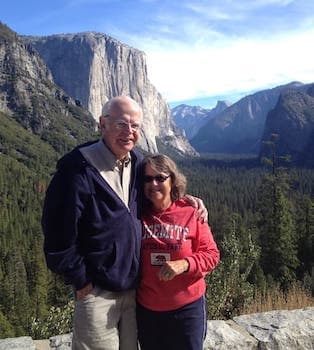
Ted Mooney, P.E. RET
Striving to live Aloha
finishing.com - Pine Beach, New Jersey
January 2018
A. Sean
1] Like Ted I am not sure of the sequence of events, but I believe you are close.
2] If the purchase order specified 'hard black anodize', the parts may or may not have been sealed, depending on the shop's practice. Your description of the IPA wipe, and discoloration later on suggests they were not sealed.
If unsealed, the coating is capable of absorbing contaminants that in your case, make restoration of the original coating unlikely. If the anodized surfaces/dimensions have tolerance of > ±0.002", I would think the close tolerance bores could be plugged/masked, the exposed anodize stripped, and then re-anodized. A refinishing step to restore surface finish and appearance might be desirable between the stripping and re-anodizing.
3] For determining if the anodize is properly sealed, you could perform the test described in ASTM B136. The test takes about 5 minutes to perform.
- Green Mountain Falls, Colorado
January 19, 2018
Q, A, or Comment on THIS thread -or- Start a NEW Thread