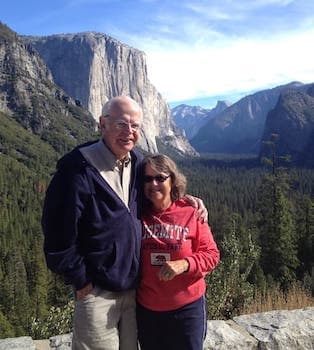
Curated with aloha by
Ted Mooney, P.E. RET
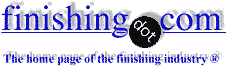
The authoritative public forum
for Metal Finishing 1989-2025
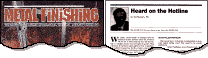
-----
Black anodized parts fading - Non-UV cause
Q. We make a product that is made of several aluminum castings that we source from a variety of vendors. All are anodized black.
Recently we received a couple parts back from our customers where the anodized pieces had lost varying degrees of their colour. The black had faded to a dark purple, light grey, or in some cases almost completely leaving the raw silver-coloured aluminum showing.
As several castings, from different batches and vendors, were affected, I think I can eliminate a problem at manufacturing. But the fading was not characteristic of UV damage, as all exposed surfaces (top, bottom, sides, inside bolt-holes, hidden corners) are equally affected. Also that the part is from the inside of a machine, where there should be no UV exposure. And area covered with RTV silicone or with another part has remained black.
The parts are still hardened, so they have not lost their anodization. And the fading was in areas inaccessible to the customer, so cannot have been from some harsh cleaning solution.
The only viable possibility is that the dye was affected by a gaseous material... so what could possibly fade dye in anodized aluminum that can be found in gaseous form?
Jeff E [last name deleted for privacy by Editor]electronics manufacturer - Burnaby, BC, Canada
2004
----
Ed. note: Fading of black anodized parts is a very common problem, addressed countless times on this site, so readers may also be interested in
- letter 2459, "Black Anodized parts fading to brown / bronze",
- letter 15825, "Black anodize turning bronze color",
- and letter 22602, "Black Anodized parts fading to brown / bronze".
A. Ozone, Chlorine, maybe ammonia ⇦ this on eBay or Amazon [affil links] come to mind. Probably many others.
Tom Gallant- Long Beach, California
2004
A. Are the components subjected to heat?
Willie Alexander- Colorado Springs, Colorado
2004
A. I've had exactly the same problem on components used in laboratory conditions housing a device that would fail catastrophically if heated to 90 °C or over. The anodiser thought that chemical or UV exposure was the cause but we never had a conclusive answer.
Nigel H [last name deleted for privacy by Editor]- Hastings, E. Sussex, U.K.
2004
2004
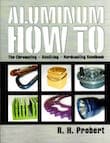
Aluminum How-To
"Chromating - Anodizing - Hardcoating"
by Robert Probert
Also available in Spanish
You'll love this book. Finishing.com has sold almost a thousand copies without a single return request :-)
Q. Thanks for all your suggestions.
To answer the heat questions, yes the components are subject to heat, but they are temperature controlled, so should never exceed about 45 °C/110 °F. Also, certain pieces are exposed to more heat than others, but the fading does not seem to follow that pattern - areas that should be quite cool have faded as much as known hot-spots. So I think we can rule out heat as a possible cause.
I'm interested in Tom's suggestions of ozone, ammonia, and chlorine. Are these known reactants for anodized surfaces? What kind of concentrations would be required?
Nigel, was the pattern of your faded parts similar, i.e., all exposed areas affected equally? Covered areas retained colour?
Jeff E [returning]- Burnaby BC, Canada
A. It seems to me that you should be considering reaction between the supposed gaseous culprit and the organic dye that was used on the anodised surface, not a reaction with the anodised surface itself.
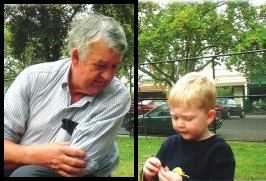
Bill Reynolds [deceased]
consultant metallurgist - Ballarat, Victoria, Australia
We sadly relate the news that Bill passed away on Jan. 29, 2010.
2004
"... so what could possibly fade dye in anodized aluminum"
A. Well, exactly what material are we dealing with here? You mentioned casting? How about the Type of Anodizing? You mentioned black anodize but I'd venture to guess it is Black Hard Anodize and is Not sealed. Either coating would require a seal to prevent fading. Hard coat is Not sealed per the mil-spec because sealing will Lower the abrasion resistance quality.
Bill Grayson- San Jose, California
2004
Q. Thanks Bill R & Bill G.
Yes, I guess we are talking about a dye problem, not an anodization problem.
I thought all anodized surfaces were sealed. These are definitely hard-anodized, but I thought they would be sealed as well. So the dye is exposed, and thus can fade without affecting the anodization itself. Hmmm.
I've received a few more faded pieces more since my initial post, so this problem spans several finishers and batches.
Is there is some commonality in the dyes used? What generally is the makeup of a dye? And then of course, exposure to what kind of chemical gas would fade these types of dyes?
Jeff E [last name deleted for privacy by Editor]electronics manufacturer - Burnaby BC, Canada
2004
A. Hard anodize is not NORMALLY dyed as the pores tend to be tiny. If it is dyed, it is very probably type II sulfuric acid anodize. What is suspicious is it abruptly happening when parts come from several vendors who were all acceptable in the past. Statistically, this would put the problem into something that has changed at your facility, like some good employee doing a MEK / methyl ethyl ketone (or similar solvent) wipedown of the parts during assembly, or vapor degreasing them, or drying wet parts in the vapor degreaser. It could be as wild as a wipe down with simply green, or citrus based cleaner or-or or.
IF you had only one anodizer, I would look for the change at their facility, but for several anodizers, look very hard in your own house first.
James Watts- Navarre, Florida
2004
A. Well James, I beg to differ. Most of my customers want their hard anodize dyed! I work in a job shop and our customers are mostly in the micro circuit industry.
I will always communicate with my customers in regards to the sealing of Hard Anodic coating. It looks to me like his parts are hard black anodize and are not sealed, which is how 80% of my customers desire their parts to be processed.
Bill Grayson- San Jose, California
2004
A. Well Bill, different strokes for different folks. Hard anodize that is applied for true wear resistance is not normally dyed. Obviously, in the electronics arena, they do not require the maximum wear resistance and the cosmetics is very important.
This is still a subset of his problem. why fading now, from several vendors. Something had to change!
James Watts- Navarre, Florida
2004
A. Now we are in full agreement!
I would dare to state that few design engineers understand the process and consequences of dying and/or sealing of Hard Anodize. I fully agree that for the highest abrasion resistance the coating should be neither dyed nor sealed. Some applications on the other side of the spectrum require a coating that offers the best dielectric properties, or corrosion resistance. Those properties are improved by seal, as I understand it.
Apparently, to get back to the subject, a process change was made and these parts did not get sealed, hence the faded appearance.
Bill Grayson- San Jose, California
2004
Treatment &
Finishing of
Aluminium and
Its Alloys"
by Wernick, Pinner
& Sheasby
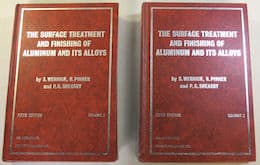
(note: this book is two volumes)
on eBay or
AbeBooks
or Amazon
(affil links)
Q. I think that the problem has to specific to some customer sites, where the product is being used. The product is made up of multiple pieces of anodized aluminum, and all are affected on these units. If I were seeing one piece being affected on multiple units I start looking internally.
I think I'll try some ammonia, chlorine, and ozone exposure to see if we can get a reaction.
Jeff E [last name deleted for privacy by Editor]electronics manufacturer - Burnaby BC, Canada
2004
A. I think it is poorly sealed,
to test this, you can try the acid dissolution test.
Is it coloured? using tin sulphate or what type of colouring?
to eliminate the sealing probability cause, I suggest you try the acid dissolution and normally the weight loss should be around 40 to 45 for good sealing, if in case its high around 70 to 80, then it can be a sign of poor sealing.
- Philippines
February 19, 2008
Q. I seem to experience a similar problem and wondered whether anyone found the root cause for it?
Whether light (fluorescent / UV/ direct sunlight) is the trigger or exposure to chemicals, did you prove that it's related to poor sealing (or any other faulty step within the cleaning-anodizing-coloring-sealing process)?
Which test was most effective to indicate faulty parts before they turn purple (e.g. ISO 2143, ISO 2135)?
Thanks!
- Israel
November 5, 2008
Q. I am having the same problem anodized aluminium extrusion bright blue colour and red colour fading all over in patches the finished product is a directory board even behind the board which is facing the wall is fading the anodizer hasn't got a clue so if you can help it would be appreciated
thanks
- Sydney, Australia
February 11, 2009
A. Anthony,
Our recent experience with the fading color of the anodized parts was apparently related to poor sealing process. We applied ISO2143 (acid drop test) as standard procedure for testing the quality of the sealing process for our vendors.
Additional testing according to ISO2135 are more difficult to implement as they require dedicated equipment (that owned by certain labs - we used the Israeli Institute of Standards) and too time consuming (weeks) and expensive to implement.
In our case the problem was related to light exposure rather then chemical attack.
I hope that it helps and good luck!
- Israel
March 19, 2009
Q, A, or Comment on THIS thread -or- Start a NEW Thread