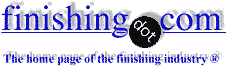
-----
Black Anodized parts turning brown
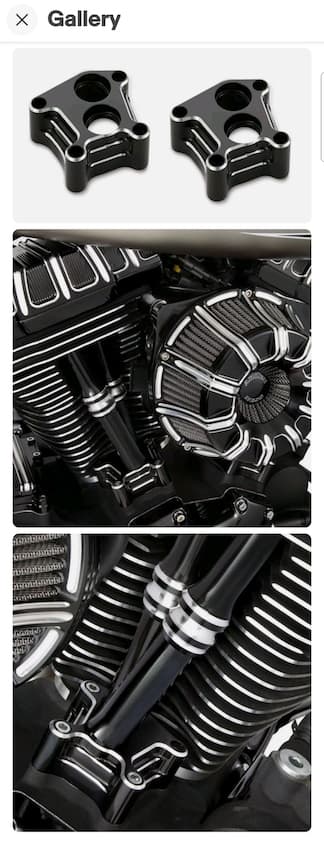
Q. Aloha!
This is regarding my 2010 Harley Davidson FLHX Street Glide...
I recently purchased several "covers" and other equipment (i.e., floor boards, heel/toe gear shift linkage, lower rear brake pedal, etc), all billet black anodized aluminum.
After a few weeks in the sun some parts began to sun bleach causing a horrid sight to my beautiful bike. These parts are now a metallic brown color and getting lighter by the week.
The specific parts that are sun bleaching are hit or miss as not all parts came (not available) from the same source.
Before I replace the parts, I'd like to know what I can do ahead of time to mitigate this issue to ensure this does not happen again. Thankfully the issue is with the inherently less expensive parts like the rocker box covers, tappet covers, foot pegs and the like...
Is there some sort of sealant or other product I can apply prior to installation or re-apply periodically that would guarantee not to have this issue in the foreseeable future?
Every single part is a "two-tone" machined finish with the anodized black covering the majority of each part and has a bare aluminum trim edging as an accent (please see photo attached)
Mahalos in advance for any advice to keep it black!
Best,
- Nevada City, California, USA
A. Hi Brian. When you look at buildings with aluminum awnings, handrails, and roofs, you'll see that they are almost always within the color range from champagne to bronze. The main reason is that it is possible to deposit metal into an anodized coating which will generate this color and be completely resistant to UV fading, whereas other colors (including black) require organic dyes (similar to fabric dyes) which to varying degrees will suffer from UV bleaching.
We have appended your inquiry to one of several similar, long, and detailed threads. Some of it is highly technical and addressed to anodizing shops rather than end customers, but can be summarized as good black color stability requires thick anodizing, high quality UV-rated dyes, and proper sealing (here we refer to a process done in the shop to swell the anodize pores closed, not to any sort of clear coat).
I hate to be the bearer of bad news, but the parts which are badly fading are probably simply not of high enough quality for a motorcycle exposed to sun and heat.
Krylon seems to me to claim that their UV-resistant clear coat can protect stuff like this. I'm not so sure, but if you try it please let us know what happened.
Luck & Regards,
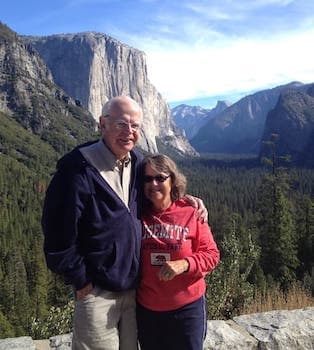
Ted Mooney, P.E. RET
Striving to live Aloha
finishing.com - Pine Beach, New Jersey
October 2021
⇩ Related postings, oldest first ⇩
Q. I have been anodizing for approx. 20 years and have NEVER run into this problem:
I have one customer whose parts are Black Anodized and come out like "jewelry" every time. However, about half the parts he gets back from us and forwards to his customer start turning brown after some time. None of my other customers have this problem. The parts are 6061 and Mic 6. I don't think it's an atmosphere problem, because I have a dozen of his parts hanging in my shop for almost a year and they still look beautiful. I've changed my seal using different brands and seal them longer than I do others and it still doesn't prevent this. What could the problem be? Has anyone else ever run into this before? I'd appreciate any advice.
Thank you,
- Milwaukee, Wisconsin, UNITED STATES
2003
----
Ed. note: Fading of black anodized parts is a very common problem, addressed countless times on this site, so readers may also be interested in
- letter 2459, "Black Anodized parts fading to brown / bronze",
- letter 15825, "Black anodize turning bronze color",
- and letter 31658, "Black anodized parts fading - Non-UV cause".
![]() |
A. This is a total wild ass guess. If you do not think that there is something in the atmosphere of his shop different from your shop, then I would look at what he is using for fluorescent lamps. There are several options other than the normal cool or warm white. A guess is that he is using one of the newer relatively high initial price units. These have a huge frequency of light range. My guess is a considerably higher amount of UV. James Watts- Navarre, Florida 2003 A. I've encountered this when black parts are exposed to temperatures above 250 °F. Is that a possibility? ![]() Marc Green anodizer - Boise, Idaho 2003 |
A. 1. The first guess is a seal problem. So you changed seals. Did you perform any seal testing to ascertain the sealing quality? Even Q-tips
⇦ on
eBay or
Amazon [affil links] dipped in
acetone
⇦ on
eBay
or
Amazon
[affil links] Warning! Flammable!
, if it picks up dye - it ain't sealed ! There are several ASTM seal tests.
2. Do you use an iron based deox? Is the iron dragged into the anodizing and occluding. Three of the iron oxides are "brown".
3.What is the dissolved aluminum in the anodizing tank? Too much clogs the pores and interferes with dye absorption and subsequent hydration of the aluminum oxide (sealing).
4. What is the anodizing temperature. It affects pore size which affects dying and sealing.
5. Anodize thickness affects dye absorption and sealing.
6. Has the customer changed aluminum alloy?
7. Light Fastness of the dye ?
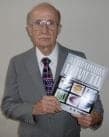
Robert H Probert
Robert H Probert Technical Services

Garner, North Carolina
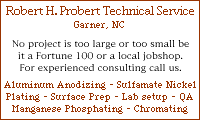
A. If the parts leave your shop black, and then sometime later turn brown (less than black), the answer is one of three things:
1) The part is exposed to excessive Heat.
2) Lightfast quality of your dye stuff is poor. You could have a great seal, but if your dye stuff has poor lightfastness, your part will fade - when exposed to UV/sun.
3) Poor seal.
- Anaheim, California
2003
Multiple threads merged: please forgive chronology errors and repetition 🙂
Black Anodize Problem
Q. We are currently using powder coating of aluminum extrusions and are having intermittent problems with the paint flaking off. We would like to use a black anodize but are told by our plater that sulfuric anodize die black will eventually change colors.
I am told by a anodizing company in North Carolina they use a specification 215R1 Class 1 that can produce a 0.7 or greater buildup with a black color. I just need a coating that is black that will not scratch , peel or change colors. What do you recommend.
aero components - Euless , Texas
2004
QUICKSTART:
In conventional black or color anodizing, the parts are dipped into an organic dye after the anodizing, and the dye is absorbed into the open pores of the anodizing. Then the parts are "sealed" (the top surface of the aluminum is hydrated by steam, very hot water, or warm nickel based chemicals to swell the tops of the pores closed, keeping the dye in, and dirt out).
However, for architectural applications, where the components will be exposed to the sun for long periods, greater resistance to UV fading is achieved by depositing metal rather than organic dyes into the anodizing pores because metal is not subject to UV degradation. Electricity is required for this step, so the term "two step" anodizing has been coined to describe it.
Most two-step colors tend towards champagne or bronze rather than a true black. So sometimes an organic dye is used after the "two-step" to tweak the color. This is often called "overdyeing", and it means dyeing "over" the metallic coloring rather than "excessive" dyeing.
A. Dear sir,
Aluminum extrusion can be blackened by two step color anodizing provided the thickness of oxide layer is more than 10 microns.
plating and anodizing - Tehran, Iran
2004
A. Extrusions can be anodized and dyed black successfully. The color fading depends on the environment and conditions the parts are exposed to. Sunlight and Fluorescent light will fade the dye. If you achieve .70 mils (7 tenths of a thousandth) and are using a dye that has a good colorfast rating, and go for an architectural seal time in nickel acetate seal you will have the best results. Extrusions will also look much better if they are deoxidized prior to etching.
Good luck!
P.S Anodizing is not impervious to scratches, but it should not peel or flake off.
anodizing, plating - Ramsey, Minnesota, U.S.A
2004
A. There are some troubling words here. "Never" scratch or turn color. Even hard anodize can be scratched by some actions. Of course, it will be more scratch resistant than powder coat, so what is "really" meant. The most colorfast black dye will "eventually" turn color if subjected to extreme sunshine or fluorescent lighting. Two step anodizing is an exception as it is inorganic. What you mean and what the plater means has to be put down in writing or you can expect problems. A test run of parts is a great way to find out what is suitable. Oh yes, what does "black" mean to both of you? Hard anodizing of some alloys is a very dark grey--is this black?
James Watts- Navarre, Florida
2004
Multiple threads merged: please forgive chronology errors and repetition 🙂
Fluorescent lights fade black anodizing
Q. I have some 5052 AL sheetmetal parts that are black anodized (type II, class 2) that have suffered fairly drastically from the UV from the fluorescent lights in our R&D lab. They've turned a sort of iridescent brown color wherever light has hit them directly. I've read that this happens from inadequate sealing of the finish. We have MANY other anodized parts that were apparently sealed properly which have not faded one bit in the same light. I was under the impression that MIL-A-8625 / MIL-PRF-8625
[⇦ this spec on DLA]F (the standard to which we specify our parts to be anodized) specified a seal on a class 2 finish, but I recently found out that I was wrong, and "Nickel Acetate Seal" will soon be added to my standard anodizing note (unless a different process is recommended). So far, I think we've been lucky with the other anodizers we've used in that they thoroughly seal the parts regardless of the callout.
Here's the meat of the question: If these parts are indeed unsealed, can they simply be put back into a tank of dye in order to restore the black finish, and then sealed? One additional problem is that the parts are FULL of Zn-plated steel PEM® hardware, so etching the anodizing off is pretty much out of the question.
Thanks for any advice!
power systems. - Folsom, California
2005
Treatment &
Finishing of
Aluminium and
Its Alloys"
by Wernick, Pinner
& Sheasby
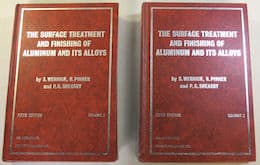
on eBay or Amazon
or AbeBooks
(affil link)
A. Since when isn't nickel acetate seal part of MIL-A-8625? The only place that it's nebulous is for Type III hardcoat, however, for Type II - IT IS REQUIRED! There is a fade test within MIL-A-8625 that is long and expensive and only done when specified in the contract, however, there isn't a snowball's chance in hell that an unsealed anodize coating will pass without it. Your anodizing source is just blatantly cutting corners and committing fraud if he's providing unsealed anodize to the military spec and certifying it as such. You should ask your local DCAS inspector for his take (name names!).
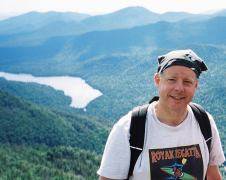
Milt Stevenson, Jr.
Syracuse, New York
2005
A. The problem you describe could be seal related, but more likely it is due to the use of inferior dye. No, they can't be re-dyed. Even if the original seal were imperfect, additional sealing has taken place in situ. If they must be black, and you can't have them stripped and re-anodized, the only solution is to paint them black.
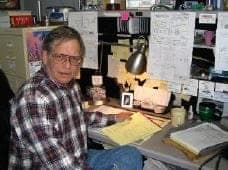
Jeffrey Holmes, CEF
Spartanburg, South Carolina
2005
A. All type II anodize is sealed per Mil-Spec. Type III is not.
Bill Graysonmetal finishing - San Jose, California, USA
2005
A. MIL-A-8625F indeed requires sealing of Class 2 (dyed) finishes -- see Paragraph 3.8.1.2. MIL-A-8625F may be downloaded from ASSIST Quick Search: http://assist1.daps.dla.mil/quicksearch/ [Ed. note: that link is now broken, see
https://quicksearch.dla.mil/qsSearch.aspx].
A cheaper dye with less fade resistance may have been used. The described parts require disassembly or very time-consuming masking in order to reprocess.
- Goleta, California

Rest in peace, Ken. Thank you for your hard work which the finishing world, and we at finishing.com, continue to benefit from.
2005
A. Hello,
Okay - 2 things. The first is, a seal IS required for class 2 coatings. Whichever anodizer told you this in the case was mistaken (to be generous). Paragraph 3.8.1.2 clearly states that when class 2 is specified sealing is to be done after dyeing and recommends nickel acetate, boiling water, or sodium dichromate.
Second, there are a few different factors involved in fading, sealing is the most common, but you might also have been given an overly thin coating (preventing sufficient dye absorption) or a poor quality dye might have been used.
Either way, I would be very surprised if further black dye would be absorbed just by immersing the part and then trying to seal it better; odds are you'd get little to no result. If corrosion isn't a factor, you could try other methods to make the part black, such as using an opaque staining color from Dykem. If corrosion is a factor, you're probably best off starting over.
On the flip side... I don't think anything in the dye or seal would hurt the steel parts; so you don't stand to lose much if you go ahead and try it.
Either way, good luck. And, if it was the same anodizer that did the black parts that said sealing wasn't a requirement, I'd REALLY look for a different anodizer.
Compton, California, USA
2005
A. http://www.anodizingindustries.com/Specs/A8625F.pdf [Ed. note: that link is now broken]
There's a link to the current mil spec. If you read it, it does specify that class 2 shall be sealed, although it leaves the sealing medium up to the anodizer. The important thing the mil spec also states is that the coating must pass lightfastness tests, and salt spray tests. Both of these tests should be easily passed if the part is properly sealed. If I were you, in the future, ask your coater to certify that his coating meets that spec. In order to be able certify that coating, he should have sent samples out to an independent lab for testing. Those results should be in his files. I cannot imagine that a quality coater would not seal a type 2, class 2 coating. It's standard practice.
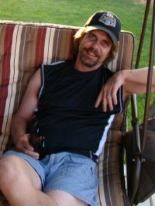
Marc Green
anodizer - Boise, Idaho
2005
2005
"Standard Test Method for Seal Quality of Anodic Coatings on Aluminum by Acid Dissolution"
ASTM B680
A. Sealing is an often short-cutted end-of-the-line dip.The proper conversion of the aluminum oxide to hydrated aluminum oxide is very important to prevent fading and corrosion. The water must be very pure. Many shops do not understand how easily a seal tank becomes contaminated with drag-in of tap water. Nor do they control the pH and temperature. Nor do they ever perform a "seal test", generic or ASTM. Because the solution ingredients are at such low concentration it is more subject to contamination than anything else in the process line. Many shops do not understand this. They think a weak solution is easy, not so, a weak solution is very critical.
You cannot re-dye your parts. You cannot re-anodize the parts with exposed iron as it will dissolve and fall out and introduce iron as a contaminate into the anodizing solution. Your parts are ruined. You may NOW perform an ASTM seal test and prove that the anodizing was never properly sealed.
Come back to us and let us know the resolution.
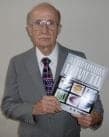
Robert H Probert
Robert H Probert Technical Services

Garner, North Carolina
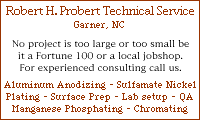
A. All Type I and II coatings per MIL-A-8625F must be "completely sealed". Nickel Acetate is not mandated, only a "suitable chemical solution" is required. This specification contains no definition for "completely sealed". One could argue that if your sealing method is sufficient to pass the monthly corrosion resistance test, then is meets the minimum specification requirements. That is unless a light fastness resistance is specified. That has never happened in my 20+ years in the anodizing business. As others have stated, light fastness is dependent on a number of factors other than just sealing.
Chris Jurey, Past-President IHAALuke Engineering & Mfg. Co. Inc.

Wadsworth, Ohio
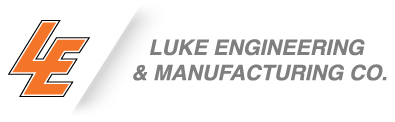
2005
A. A quick test to see if your parts are sealed is the bleach test. A drop of clorox bleach on the part for about a minute. There should be no discoloration. This is not a substitute for salt spray testing but a quick way to see if it is sealed.
Randy Britton- Methuen Massachusetts
2007
Q. Hello, Rodney:
How did you measure the fluorescence from the anodized aluminum? Recently I measured photoluminecense of black anodized aluminum, saw strong broad spectrum in visible range, but I also got almost same fluorescence from the aluminum substrate itself. So right now I don't know if the fluorescence I got is from the anodized materials or from the substrate. The thickness of anodized coating is about 20 µ -- can green laser penetrate so thick a black anodized layer? I used green laser to measure PL spectrum. Is it normal to have broad spectrum from aluminum or oxidized aluminum?
Thanks
Best regards
instruments - Singapore
January 9, 2009
Multiple threads merged: please forgive chronology errors and repetition 🙂
Black anodized aluminum fades depending on what covers it
March 27, 2008Q. I am a mechanical engineer designing wafer handling equipment in the semiconductor industry. Among other things, we manufacture loadports where a user places a cassette of semiconductor wafers for access by a robot for processing. Cosmetics is important because our $10K tools attach to the front and are the user interface for equipment worth millions.
Recently, a black anodized sheetmetal part that covers these cassettes of wafers was returned by an angry customer because it was severely faded. Different areas of the part faded in different ways. Areas that were exposed faded after one month of exposure to fluorescent light. Areas that were covered with other aluminum parts did not fade. After the aluminum parts were removed, these parts then faded after another one month of fluorescent light. Other areas were covered by a clear polycarbonate window. These areas acted like the ones covered with aluminum. They did not fade and then later faded when the polycarbonate was removed. Finally, there was an area that was covered with some light, clear plastic with light adhesive. This is the same plastic you see on electronic devices with screens to protect the screen during shipping. This plastic was applied a day or two after the parts were anodized and removed about two weeks later. The anodizing is still black in the area that this plastic covered after a 8 weeks of exposure to the same fluorescent lighting.
I am not an expert on finishing, but I have learned a lot from this problem and from this website. There are a couple of things I cannot answer and I was wondering if anybody else would have any thoughts:
1. I am assuming that the part had a bad seal and the fluorescent light attacked the dye. But why doesn't the fluorescent light attack below the clear polycarbonate window? Does the anodized finish require light and oxygen for the dye to fade?
2. Why would the part that was covered with the light plastic stay black? Could a small, undetectable amount of residue from the adhesive in the plastic protect the surface from the fluorescent light?
I would appreciate your ideas on this matter.
Product Designer - Milpitas, California, USA
![]() |
A. A poor seal will definitely allow a panel to fade prematurely. - Navarre, Florida March 28, 2008 A. Trey - Colorado Springs, Colorado March 29, 2008 |
Method for determining type of coloring process used in Al anodizing
Q. I currently have aluminum parts being extruded and milled out of 6061 in China. A recent project requires one of these aluminum parts to be used extensively outdoors, receiving direct sunlight exposure for many years. In order to maintain the same look as our other products I asked my supplier to find an anodizer that could do electrolytic (2-step) black coloring. After a long search, he believes he found somebody. There is always a language and learning barrier when dealing with Chinese manufacturers so I need a method to determine whether or not they did the correct process. One option I considered is to have them perform a UV degradation test but I fear that will take too long. Is there a chemical or mechanical test that can be performed instead? Or is there a solid way to accelerate a UV test to under 48 hrs? Any help would be appreciated.
Brad MillerProduct Design Engineer - San Diego, California USA
October 11, 2017
A. Hi Brad. It sounds like, in addition to language and learning barriers, you are concerned about the honesty barrier as well. But in addition to organic dyes and 2-step dyeing, there is also overdyeing a 2-step with an organic, so finding one doesn't mean you don't have the other anyway; then too, poor sealing can lead to fading, as can an anodized layer that is too thin or defective in some other way.
So I think your plan of an accelerated UV test is the most workable answer, but I don't personally know the relationship between X number of hours at Y units of irradiance at wavelength Z vs. real-world fade resistance. Good luck.
Regards,
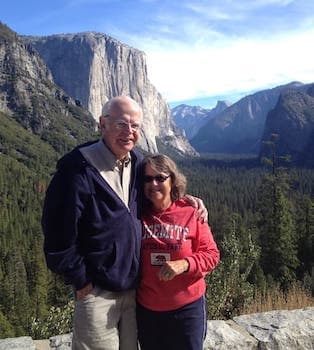
Ted Mooney, P.E. RET
Striving to live Aloha
finishing.com - Pine Beach, New Jersey
October 2017