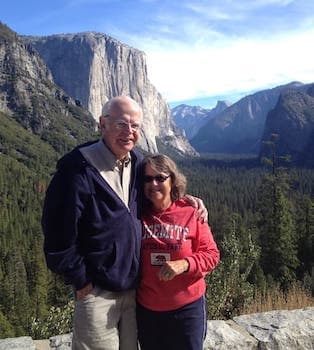
Curated with aloha by
Ted Mooney, P.E. RET
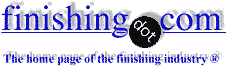
The authoritative public forum
for Metal Finishing 1989-2025
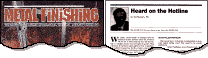
-----
Conductive paint/lacquer Q&A for electroforming
Q. I am looking for a lacquer-based conductive paint that dries quickly and can be applied by brush, without leaving any brush marks. I will be using it for electroforming shells, crystals, etc. I have been using a silver based lacquer conductive paint from a jewelry supply company in Albuquerque, N.M., however supplies are a bit iffy right now. They have been on back order for almost a month now. I would like to try other suppliers if anyone can suggest some that have the type of product I am looking for. Thanks.
Vance McCollum- Summerville, South Carolina
July 15, 2021
A. Hi Vance. That subject has been discussed here a dozen times. In addition to this thread, please see topic 57992, or use the search engine to find everything. But brush marks are largely a question of how much thinning is done. In order to avoid brush marks, premium brass chandelier manufacturers may dilute their brass lacquer so thin that seven sequential coatings and dryings are required.
One approach mentioned by Goran Budija in topic 55101 is to mix bronze powder into highly thinned nitrocellulose lacquer. We can discuss various types of metallizing approaches, but sorry, we've learned to no longer post brand or sourcing suggestions (why?)
Luck & Regards,
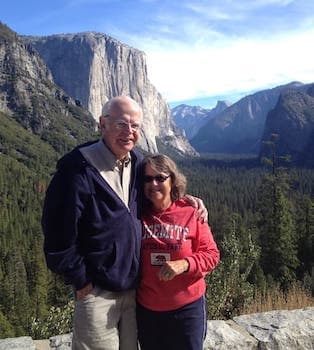
Ted Mooney, P.E. RET
Striving to live Aloha
finishing.com - Pine Beach, New Jersey
July 2021
July 24, 2021
Q. Hi,
I've been working on electroplating some plastic models I have.
The main issue I have encountered is getting my hands on a conductive paint suitable for the purpose here in New Zealand. I have tried several options including making my own from graphite powder and zinc based paint (over 90% zinc), neither or which provided a good conductive surface. I am using a pen based plating approach rather than a tank.
Is this coat suitable for further plating? My final finish will be a nickel plate, but considering electroplating more copper on first to build up the thickness (copper plating supplies are a lot easier to obtain here than nickel).
Thanks!
Peter.
- Auckland, New Zealand
A. Hi Peter. Even professional platers have occasional problems with peeling & blistering (lack of sufficient adhesion) ... so nobody will be able to tell you whether or not zinc paint followed by copper sulphate followed by electroplating will offer sufficient adhesion for your plastic models. But in general, copper is more ductile and less highly stressed than nickel, so I think your plan is good.
But your idea of zinc rich paint ('cold galvanizing' paint) followed by copper sulphate just might be a terrific -- inexpensive, readily available, easy -- metallizing approach for the electroformers here! Thanks!
Luck & Regards,
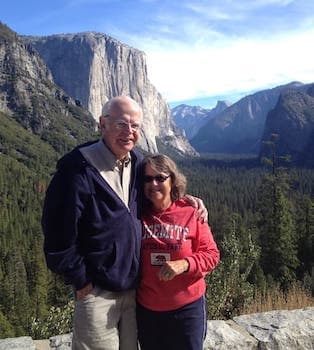
Ted Mooney, P.E. RET
Striving to live Aloha
finishing.com - Pine Beach, New Jersey
July 2021
? Hi Peter,
I was intrigued by your comment:
"I noticed that copper sulphate has a redox reaction with the zinc in the paint which seems to form a nice conductive coating of copper, as long as I don't apply any mechanical pressure between the zinc going black then copper it seems to be fairly stable."
But I can't figure out what is meant by the phrase,
"between the zinc going black then copper".
Can you elaborate on this topic? Thanks, Jeff
Scientist - San Ramon, California
October 20, 2021
⇩ Related postings, oldest first ⇩
1998
Q. I am looking for a Electrically Conductive coating (with copper, not silver -- too $$) to put onto a nonmetallic surface. I then want to plate copper onto the item, then nickel, then gold. I am experienced in plating, but I have never looked into plating nonconductive items until now. I refuse to believe I cannot find a more affordable coating or create my own blend for a much lower cost. I am looking for a very thin paint (to keep detail of piece after coating). I say paint because I know of little else that would adhere to an organic surface. The coating also has to not react with a cyanide copper bath.
I am open to all suggestions.
DAVID ALLENA. People have developed some new systems for metallizing printed circuit boards which use carbon (or graphite?). I don't believe that the price of the technology has much to do with the cost of the conductor. It's like the cost of developing a new drug; the research is what takes most of the money.


Tom Pullizzi
Falls Township, Pennsylvania
1998
A. David,
We have tried a number of different conductive paints and have mainly used Electrodag from Acheson Colloids. I believe they have a nickel based paint which would be cheaper than the usual silver base. Your problem will be in using cyanide copper as the alkaline cyanide solution is a good paint stripper. We have always used acid copper or silver over these products.
Regards
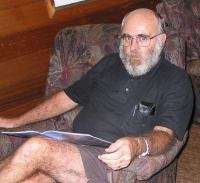
Bob Lynch
plating company - Sydney, Australia
1997
A. Some 15 years ago we did plating over items like flower buds, insects, and leaves. We made the surfaces conductive by "painting" on a carbon colloidal suspension which was marketed under the name of "Aquadag"
I believe the supplier, whose name I cannot recall is now defunct.
It was necessary to plate an undercoat of copper, and only acid copper was suitable. We intended to try a sulphamate bath as alternative, but the customer passed away before we could. (He was a retired professor of botany).
Maybe you could source an equivalent to Aquadag. It worked really well.
Raymond Sebba- Capetown, South Africa
1998
A. The name 'Aquadag' isn't defunct as of this writing, Raymond. Acheson Colloids offers the Electrodag series, and claims ownership of the names Electrodag, Aquadag, and the rest of the dags. They are in Port Huron, MI. But there are several other brands of similar products.
Ted Mooney, P.E.
Striving to live Aloha
finishing.com - Pine Beach, New Jersey
1998
A. This type of coating is widely used to "bronze" baby shoes by coating with a conductive paint such as Aquadag then electroplating.
Indium - tin- oxide (ITO) (mixture of In2O3 and SnO2) is a transparent (colorless) conductive oxide. It is deposited on surfaces by PVD techniques but would also be useful as a conductive powder.
Donald M. MattoxSociety of Vacuum Coaters
Albuquerque, New Mexico
"Handbook of Physical Vapor Deposition (PVD) Processing" (2010) [on AbeBooks or eBay or Amazon affil links]
and "The Foundations of Vacuum Coating Technology" (2018) on AbeBooks or eBay or Amazon affil links]
A. If you're attempting Cu - Ni - Au for thin film processes, then PVD (sputtering), vacuum evap., or a combination of either w/ Au up-plate is the only way to go for adhesion under high temperature. If you're attempting this coating on an organic such as a plastic, you may want to look into what the PCB industry uses for plated thru holes. Specifically, palladium catalyst activation processes with following plate-up. For this latter technology, contact your plating chemical supplier (I use Technic). Good luck
Jeff A [last name deleted for privacy by Editor]1998
A. Dave,
As Don mentioned earlier, this process is used in the bronzing of "baby shoes." However, the applications are limitless.
Todd MillerOceanside, California
1998
Q. Does anyone know where I can find information on the exact ins and out of gold plating organic materials? I already do gold plating on chrome objects . . . is the process similar or do you need copper baths or nickel baths?
Wayne Haraga- HONOLULU, HAWAII
1998
A. Hi Wayne. For a start, try our FAQs on the subject. Gold plating onto previously chrome plated items is the world's easiest plating because all the hard stuff (polishing, buffing, cleaning, activating, copper plating, and extremely corrosion resistant nickel plating) has already been done to very high quality standards. Gold plating of organic materials will be much harder, involving sealing, metallizing, copper plating, and nickel plating before the gold plating. Good luck. Aloha.
Regards,
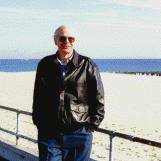
Ted Mooney, P.E.
Striving to live Aloha
finishing.com - Pine Beach, New Jersey
1998
A. Like many of the postings you have already received, when plating non-metallics I have found that you must use an Acid Copper system. The Copper paint can be made by using a nitrocellulose based lacquer and filling it with very fine copper powder which you can buy from a Lab supplier (for small quantities at exorbitant prices) or in larger quantities from any reasonable Metal supplier.
One of the secrets that has not been mentioned is that once the non-metallic surface has been coated with the "conductive paint" it must be left to "cure" and the "Cure" time depends on how thick the "conductive paint" is. My experience is minimum cure time is 24 hours but the longer the better (up to 7 days is sometimes needed).

John Tenison - Woods
- Victoria Australia
by Warner Electric
on AbeBooks
or Amazon
(affil links)
A. Anybody who wants to electroplate non-metallics should find a copy of "How to Electroplate for Fun and Profit by Warner Electric Co. 1950 ==>
It describes the following process.
2. Dry brush or spray with DEGREASED pure bronze powder.
3. Acid copper plate a base coat.
Q. In my attempts to electroplate nonconductive materials I have tried to make nitrocellulose lacquers conductive by adding carbon black. Contacts in the conductive polymer industry have provided me with samples of highly conductive carbon structures in powder form, but my recipes have not yet yielded usable results. This method of creating surface conductivity would be extremely economical; any advice is welcome.
Rob Anzellotti1998
A. Hi Rob. Yes, its doable. As Tom Pullizzi alluded to early on in this thread, similar products are used these days to metallize printed circuit boards in lieu of the older and more traditional process of tin/palladium activation followed by electroless copper plating. Although the chemistries are proprietary, you can probably find good hints from white papers on google, and solid information from patent searches. The search term "direct metallization" may be helpful. Good luck.
Regards,
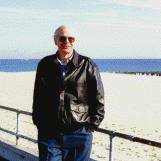
Ted Mooney, P.E.
Striving to live Aloha
finishing.com - Pine Beach, New Jersey
Q. I'm very interested to learn about gold and silver plating organic materials like leaves, nuts and even big things like apples and oranges. Can anyone give me a tip of books and a company where I can buy the products at an affordable price and also get information and support? Can I use a cheaper transformer or I have to buy the more expensive ones? Is it difficult and costly to learn? I have worked in silver before, but not too much. Thank you very much.
Bo Erlandsson- Cape Coral, Florida
1999
A. Hi Bo. The Warner Electric booklets suggested by Donald Warner are probably good ones if you can find a copy (availability is on-again / off-again). Sorry, but we can't recommend suppliers in this no-registration-required forum (why?) -- it draws spammers like fleas, with some of them even posing as satisfied customers and posting with fictitious names :-)
I've probably said this too many times, but when onesy-twosy plating of natural materials, it is an art more than a science, and pleasing results will require artistic ability -- I have none, so my advice is of limited value :-)
Luck and Regards,
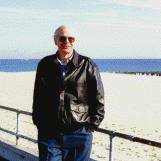
Ted Mooney, P.E.
Striving to live Aloha
finishing.com - Pine Beach, New Jersey
Q. I am trying to restart an operation I dropped in the 60's. I bought an outfit for plating baby shoes from Warner Electric in the Midwest I think. I believe they are out of business today. I too am looking for supplies similar to those I used from Warner. The item to be plated was dipped in a rather viscous liquid that dried hard and allowed much detail to come though. The metallic coating was a copper dust propelled from an aerosol can had contained a solvent which allowed the particles of copper to embed and attach themselves to the surface of the impregnated item having an copper suspension wire attached for the plating process.
The item, after proper coating with the copper dust was hung from a bar which agitated via motor driven cam, in a copper sulphate bath. They sold copper anodes and a complete line of grinding and polishing compounds, also a great degreasing powder. I successfully plated many natural items such as apples, acorns and plastic statuary as well . I lost all records of bath formulae and will try the suggested root killer ⇦ this on eBay or Amazon [affil links] . If anyone and suggest more on this I'd appreciate it. I still have the power supply which is rated at 6 volts and 10 amps adjustable.
Thanks,
Frank GaleaSculpture - Olyphant, Pennsylvania
2004
2004
We need a lacquer to mix with our conductive coating powder, to make conductive coating paint. We electroform foliate [trees, flowers, etc]. Our first conductive coating paint was pre-mixed, and it worked very well on tree leaves that we have successfully electroformed [using a safe, non-cyanide copper solution], with amazing results [no lumps or wrinkling, etc., due to 6-day leaf-preservation method we concocted]. But the conductive coating paint pre-mix is too expensive. So, we purchased the powder in order to mix our own.
We were told that Dupont Clear Automotive Lacquer is a good lacquer to use in order to mix the conductive coating powder to make conductive coating paint. We've looked on the web, and we get the impression, from reading a few things, that certain kinds of automotive lacquer have been banned by the EPA, and will no longer be made by Dupont, etc. We wish to purchase some anyway [please: no lectures on jail terms].
Do you have any specific recommendations for what to use to mix with the conductive coating powder? Can we use a shellac, such as Bulls Eye Shellac? Also, how thin can we make the paint (so that we can stretch it to last)? Thank you.
Byron Smith- Northbrook, IL, USA
Q. I am interested in finding out more about electroplating a non-metallic object such as a flower. I was thinking of copper dusting my flower first before electroplating it. I was wondering what methods are there to copper dust my flower, or just any way of making my flower a conductor so that it can be electroplated.
Renee Gohstudent - Singapore
2007
Hi, Renee. Please try your best to express your question in terms of what has already been said in rhe postings before yours so we can keep moving forward. Repetition is the kiss of death for threads. Thanks!
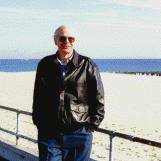
Ted Mooney, P.E.
Striving to live Aloha
finishing.com - Pine Beach, New Jersey
2007
Q. Hello,
I've tried to use Aquadag on non-conductors like ceramic items to make them plateable. Unfortunately the graphite layer remains water soluble and rinses off very easily regardless of temperature and the (mentioned a few posts earlier) curing time. It also seems to be quite poorly adherent to surfaces I've applied it onto, even though they were thoroughly degreased.
There are surely platers familiar with Aquadag usage here, could anyone give any hint how to use it properly for plating purposes? Would it, for instance, need to be mixed with some kind of varnish for water resistance and adhesion improvement? Any suggestion will be greatly appreciated.
Regards,
- Poznan, Poland
November 25, 2008
WHILE IT'S AVAILABLE:
You may wish to download "EMI-RFI_Shield_Coating_Manual.pdf" from oem.sherwin-williams.com/pdf/guides/EMI-RFI_Shield_Coating_Manual.pdf while it's available. It doesn't answer your specific question, but does give good insight into the Electrodag products like SP-017.
Q. I found a Sherwin Williams about 40 miles from me that sold Electrodag SP-017. It is listed as a "highly conductive coating". I've seen posts that say that Electrodag works, but not this one [for me]. The pigment is listed as a silver coated copper, so I figured it would work. I spent a little under $300/gal, which is a lot cheaper than silver spray, especially since it is to be thinned 2:1 with MEK. I figured I'd say a prayer and give it a shot, but no luck for me. If anyone has used this successfully, or knows exactly which Electrodag they've used successfully, please let us know.
Thanks,
- Joliet, Illinois
March 11, 2009
Q. What was the problem that you encountered with the Electrodag SP-017? It has been recommended to me for use in electroplating organics such as leaves and flowers. And the company that manufactures electrodag suggested that it may be used as a dip coating. I am interested to know how it worked out for you. Thank you,
I use a carbon graphite paint to electroplate nonconductives. It seems to keep more detail than any other paint or powder I have used. And it is very good for dipping because carbon has a low density it seems less inclined separate, therefore a more uniform coating is achieved. But the problem is that the carbon is not very conductive so it takes an hour longer to plate.
Aaron Fishertrading - New York, New York
March 17, 2009
A. Hi, Aaron. If preserving fine really fine detail is essential you might think of two-part silvering rather than conductive paint. You will lose no definition at all. This is what is used to metallize masters for vinyl records, and was used on videodisks (today PVD vacuum processes are used to metallize CD and DVD masters).
Regards,
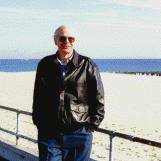
Ted Mooney, P.E.
Striving to live Aloha
finishing.com - Pine Beach, New Jersey
March 17, 2009
Q. Do you think that it would be possible to achieve a conductive coating of silver on a leaf by spraying the silvering solution and reducer at the same time using an ordinary household spray bottles? This would be instead of using the dual nozzle spray gun and compressor.
Aaron Fisher [returning]trading - New York, New York
March 20, 2009
A. Hi, Aaron. 2-part silvering has been around for centuries, long before dual nozzle spray guns were available, so I'm confident that it is possible.
The highest resolution, however, is obtained by spraying while the object is on a spin table to thin out the coating, so any compromises you make will limit the resolution somewhat. Even a children's toy spin art table might (or might not) help. Good luck.
Regards,
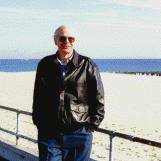
Ted Mooney, P.E.
Striving to live Aloha
finishing.com - Pine Beach, New Jersey
March 21, 2009
Q. I would like to electroplate something plastic. I found an online dealer that sells "graphit 33" which is (as the name would suggest) graphite based. Would it be possible to simply spray a plastic object with Graphit 33, and then electroplate it with pyrite through a simple salt water and electricity electroplating process? I am a complete novice and this would be the my first electroplating. I would really appreciate any help, because I am slightly overwhelmed by the aforementioned process.
Thank you for your time
- Rockville
April 26, 2011
A. Hi, Michael.
Plating on plastic probably should not be your first attempt at electroplating because it is more difficult than plating on metal. Plating something with iron should not be your first attempt, either, as iron plating is more difficult than most metals because of its propensity to oxidize to a higher valence state that it can't be plated from. You can't use salt water as the electrolyte because ions of the metal you are plating must be soluble in the electrolyte, and iron will not be soluble in salt water. Please see our FAQ on "How Electroplating Works" as well as our FAQ on "How to Electroplate Organic Materials", and start with something simpler :-)
If you are just trying to get an item plated, as opposed to starting a hobby, there are jobshops listed in our Jobshops Directory that can help you. Good luck.
Regards,
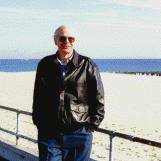
Ted Mooney, P.E.
Striving to live Aloha
finishing.com - Pine Beach, New Jersey
April 27, 2011
Q. Hi, I've been reading this thread with interest. My question is not about home chrome plating plastic - your warnings about toxicity and difficulty hit home! I would like to prep my plastic parts and take them to an electroplater here in Auckland, New Zealand.
I am casting replica automotive tail light bodies in a Polyurethane resin. The originals were chromed pot metal and have long since ceased to be available. I can add metal powder to the PU as it is cast - up to 60% of copper, brass or bronze, or stamped aluminium flake. Would these suffice as a preparation for electroplating? Or I can dust the inside of the molds with powder or paint before pouring pure PU resin in.
Any help would be appreciated.
thanks
Ross
- Auckland, New Zealand
June 3, 2011
A. Hi, Ross.
While almost any substrate can be electroplated some way or another -- probably including by the methods you propose -- the issue is usually inadequate adhesion. There are probably few applications where shortcomings in adhesion will more quickly become evident than exterior automotive parts. These items should be molded of plating grade ABS, as most OEM grills and bezels are, and then it will be possible for the plating to properly adhere in the punishing environment that cars encounter (because ABS is a multiple component plastic from which one of the components can be etched away, leaving a sponge-like surface for great "keying"). Good luck.
Regards,
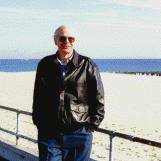
Ted Mooney, P.E.
Striving to live Aloha
finishing.com - Pine Beach, New Jersey
June 6, 2011
Thanks for the suggestion to use plating grade ABS. My google searches for this however show that ABS must be injection molded. My hobby uses silicone molds and cold - poured urethane resin. Injection molding is beyond me. Cheers
Ross
- Auckland New Zealand
June 17, 2011
Q. I'm brand new to the electroplating process. I have some organic items (leaves/pine cones/berries, etc.) I'd like to plate with copper. I've tried a paint that contains real aluminum and I've made a solution of graphite and polyurethane. Neither coating seems to attract copper.
Here's my question: Can zinc oxide
⇦ this on
eBay or
Amazon [affil links]
, titanium dioxide
⇦ this on
eBay or
Amazon [affil links]
, powdered zirconium oxide ... metallic ingredients like these ... be used to make a conductive paint?
Hobbyist - Tucker, Georgia
November 4, 2011
A. No, Gale, oxides like that are not conductive. But we appended your inquiry to a thread which may help you get on the right track. Good luck.
Regards,
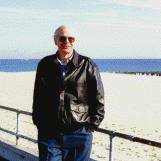
Ted Mooney, P.E.
Striving to live Aloha
finishing.com - Pine Beach, New Jersey
January 25, 2012
Q. I have been able to electroplate over graphite powder (not paint); the powder has been rubbed onto the surface. The issue now is that the rubbed powder is not sticking well to a shiny surface (the nickel was well plated over the graphite). Now after applying the powder on a rough surface to give it something to hold, the nickel plated part is not shiny, it's rough.
That was the cheap way to electroplate over plastic (will be making a video on how to do it). To me the best method of electroplating on plastic is using 2-part silvering chemicals, I will be testing this method soon. If you know what to buy it's actually not that expensive at all. I will be using a special hand sprayer (to spray both chemicals at the same time using only one hand). I am doing a thread about this. What I plan to do is spray silver the piece first, then use a small and inexpensive hobby plating system.
The first pic is of graphite powder rubbed onto a plastic spoon over a glossy surface so it's not plated at all, but it looks like it because of the shine of graphite powdered rubbed against the shiny surface.
The second pic is of that plastic spoon being electroplated in nickel (40 minutes)
The third pic is showing the finished product. This nickel plated spoon shows the graphite not holding to the non-conductive surface (but it plated well to the graphite)
The fourth pic shows a nickel plated plastic spoon over a rough surface (to give graphite something to hold to) as you can see the piece looks also rough not shiny as before.
- Managua, Nicaragua
A. I am using MG Chemicals Total Ground spray to coat clay sculptures for electrotyping. So far so good. I am totally new to all this, but I have enough electricity and chemistry to understand the variables. I am using homemade electrolyte. I want to keep the cost down. This stuff is meant for creating a grounded work surface, so it is highly adhesive and highly conductive.
Ryan Barrett- Dundas, Ontario, Canada
February 23, 2012
Q. Hi Ryan
Can you supply more info on the homemade electrolyte that you use?
Also where do you purchase the MG Chemicals Total ground spray from?
I want to use small pieces of glass and stuff from nature, Do you think your method would work for this?
Thanks so much for any info you can provide.
Judy
- Niagara Falls, Ontario, Canada
March 5, 2012
Hi, Judy. Hopefully, you'll get more info on the homemade electrolyte and an opinion about the method.
You can buy MG Chemical Total Ground from Amazon or use your search engine to find it. This site is possible because supporting advertisers provide it for camaraderie and technical information exchange. It's certainly no problem if people prefer to buy from non-advertisers -- but we can't ask our advertisers to pay the costs of maintaining distribution info here for their competitors :-)
Regards,
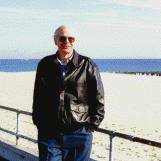
Ted Mooney, P.E.
Striving to live Aloha
finishing.com - Pine Beach, New Jersey
March 6, 2012
Q. I am Gold and Silversmith student and an engineer, and was wondering about electroplating paper.
I need to find a way to transform a fairly complex form made in thin paper in to something more durable, and more related to gold/silversmithing than simply coating the paper with varnish.
Although I have not electroplated myself before, I have a fairly good understanding of how it works as well have access to experienced platers, who I would recruit in the actual plaiting process.
So my question is what sort of material could you recommend I use to achieve conductivity on the paper surface? And since goldsmiths are advised to make jewelry nickel-free, a nickel-free solution would be preferred. As well as any advice about how to apply it to get a even coating.
- Reykjavik, Iceland
April 18, 2012
A. Hello,
Recently I came across a new process of silver spray. With this any non-conductive surface can be silver plated and the finish is extraordinary. It is a chemical process and a lot of people are moving towards it since cost is not too high and at the same time not much infrastructure is required as compared to vacuum metallization and PVD. This can give effects like gold plating as well.
You must try one of those they are really good and inexpensive.
- Mumbai, Maharashtra, India
December 2, 2013
Q. Hi Dears,
I'm a PhD candidate in materials science and now working on making copper foam through electroplating copper on a kind of open-cell polymeric foam like polyurethane foam.
Is there anybody here who have such experience of electroplating on porous non-conductors and the process of conducting them?
Hope to here from you soon
Regards
M. Gharib
- Karaj, Alborz, Iran
July 3, 2014
A. Hi mohammad gharib. Copper electroplating is a process which operates in accordance with Faraday's Law: electrons are pumped to the cathode with a power supply, and positively ions migrate towards the cathode where they re-combine with those electrons to form atoms of metal. But electricity follows the path of least resistance, so it will probably prove difficult to electroplate into foam, as all of the buildup will be on the outside rather than into the pores. Please investigate electroless copper plating, which I think has a much better chance of success; and technology was developed for through-hole plating of printed circuit boards which may help you. Good luck.
Regards,
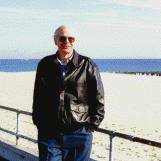
Ted Mooney, P.E.
Striving to live Aloha
finishing.com - Pine Beach, New Jersey
July 2014
Q. Thanks Ted, but it has been proved for years that with the aid of some kind of colloidal graphite or carbon-black coating, it is possible to induce conductivity to such polymeric materials and making them plateable.
I'm now seeking for an appropriate conductive colloid coat.
Regards
IUST - Karaj, Alborz, Iran
July 7, 2014
A. Hi again. Yes, of course you can use colloidal graphites to induce conductivity and metallize non-conductors. In the circuit board and plating-on-plastics industries this approach seems to be supplanting the traditional tin/palladium activation followed by electroless plating. You should be able to get these from any of the major plating chemistry providers like Atotech, Macdermid, Surtec, etc. If you can't commercially buy those proprietaries in your location, you can at least read their patents and white papers for a good understanding of their chemistry.
But please slowly read what I was talking about, which is the difficulty in the electroplating step of getting plating into the pores of the foam rather than just glomming up on the outside; for this reason I believe you will find electroless copper plating a better way to start than graphites. Best of luck.
Regards,
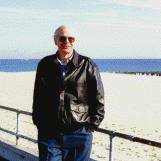
Ted Mooney, P.E.
Striving to live Aloha
finishing.com - Pine Beach, New Jersey
July 2014
July 9, 2014
Dear Ted,
your kind attention to my question is greatly appreciated.
Just to be noted that in this process polymeric foams with reticular structure are currently used.
Thanks again.
IUST - Karaj, Alborz, Iran
September 2014
Hi again. Please look into the proprietary copper plating solutions used for thru-hole plating. They use large molecule brighteners that can't fit into the through holes, with the result that everything but the holes gets covered with these brighteners which tend to shield plating from occurring, while plating is able to happen inside the thru-holes because no brighteners fit into the holes. It is perhaps possible that this will help you get plating deep into the pores of the sponge rather than glomming up on the outside, as is its normal propensity. Good luck.
Regards,
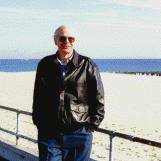
Ted Mooney, P.E.
Striving to live Aloha
finishing.com - Pine Beach, New Jersey
July 14, 2014
Sir,
Can I use acrylic base metallic copper paint on non-conductive materials to make them conductive?
Thanks
- kolkata, west bengal , India
A. Hi Jayanta. Such questions are hard to answer because in truth you can do nearly anything with nearly anything ...
Had Van Gogh tried "Starry Night" with a lump of cooking charcoal on brown kraft paper and it might still would have been a reasonable success. But in my opinion, artists & craftspersons shouldn't try to prove they can do passable work with ill-suited materials that way -- instead they should aim for exceptional work with optimal materials. So to answer your question in that sense, no, metallic copper paint is not the right metallization approach.
If your work is strictly decorative, not a circuit board or an electroform, and you want to start from a paint-like material rather than two-part silvering or circuit board metallization technology, I'd look into Aquadag, Electrodag, Sierra Silver, or another product designed specifically for the purpose. If you just want conductivity, with no plans to electroplate it, there are many products made for optimum conductivity. Please explain what the substrate is and why you want to metallize it. Best of luck.
Regards,
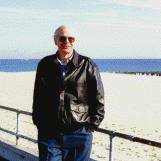
Ted Mooney, P.E.
Striving to live Aloha
finishing.com - Pine Beach, New Jersey
July 2014
Metal impregnated epoxy coating as metallizing system for epoxy castings?
September 11, 2014Q. I am currently working on electroplating cast epoxy pieces. Due to certain processing conditions, a coating must be applied and a conductive element cannot be added into the epoxy before casting. I have tried a number of things and have been successful with plating them, but I am seeing varied failure modes with little adhesive strength.
I used a product similar to electrodag as my starting point. It has a silver coated copper component, but the paint shows poor cohesive strength and the plated metal peels easily.
Other materials that were tried:
Graphite paint - cohesive failure, poor material choice
ESD paint (nickel/graphite) - metal to paint adhesive failure
Nickel filled epoxies - metal to paint adhesive failure
In the plating process, high current densities were required to get the items to plate, could this account for the poor adhesion? Also the nickel was not activated, which I can assume would hurt as much as anything for adhesion.
So my thoughts were leaning toward a copper or silver filled epoxy to create higher conductivity in the coating. Am I on the right track? Is one of these easier to activate than the other, or show better adhesion?
Is there any detractor from the addition of graphite such as lesser conductivity? Would the layered microstructure allow for easier peeling?
Thanks
- Old Orchard Beach, Maine, USA
A. [Consider] this conductive paint: GRAPHIT 33. Good for Cu electroplating in CuSO4 solution. Made in Europe. Price varies between 8 and 20 Euros. Regards.
Saulius Pakalnis- Vilnius, Lithuania
November 26, 2014
Q. I am trying to create a conductive paint using atomized copper powder. My question is, is there a difference between atomized copper powder and ordinary copper powder? Reason being, I made a mixture of lacquer, lacquer thinner ⇦ this on eBay or Amazon [affil links] Warning! flammable! and atomized copper powder and was unsuccessful in plating in a copper sulphate electrolyte using a 30 amp rectifier. My leads were glued and connected to the object and painted over with the conductive paint that I made. Is there a difference between the two copper powders? I did not get an amperage meter reading with the lead connected to the copper conductive paint and object. I'm fairly sure I had good contact. I'm wondering if my conductive paint is not conductive at all? Any response would be greatly appreciated.
Camson Adenuga- Missoula Montana United States
December 31, 2014
A. Hi Camson, you have to walk before you run. Please put a piece of well cleaned brass or copper into your rig and see if plating occurs (the plating probably may not stick properly, but at least you'll know some early basics like whether the rectifier is working). If you've never successfully plated anything before, we might waste time talking about your metallizing lacquer when it may have nothing to do with the problem :-)
What is your anode made of? What is the voltage? What is the approx. surface area of the object? Thanks. Good luck.
Regards,
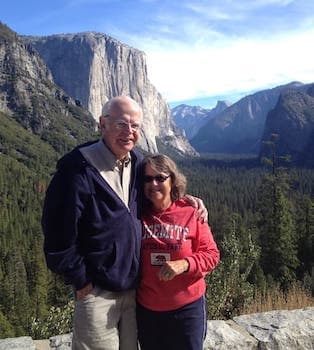
Ted Mooney, P.E. RET
Striving to live Aloha
finishing.com - Pine Beach, New Jersey
January 2015
A. Hi Cameron
Ted is right but also;-
Lacquers are non-conductive. To make them conduct you add metal powder But there must be enough metal in the dried layer for the particles to be in contact with each other or there will be no electrical pathway. That means a lot of metal and as little lacquer as practical.
Also copper oxidises very easily and even more so when it is a fine powder so it is not a very promising metal unless you can clean it after painting.
That is why most conductive paints are based on either silver or graphite
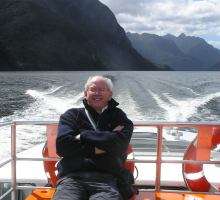
Geoff Smith
Hampshire, England
January 6, 2015
A. Copper plating on plastic or non-conducting surfaces is not very difficult but you need to commit to doing the right thing. Silver or copper or nickel filled epoxies work very well. Best to use a thermoset epoxy instead of a thermoplastic. The later usually peel or don't hold up to the chemistry. The epoxy as a thicker paste, say 2500 cps should be 65-70% filled or the conductivity will be too low and plating will be compromised. If you thin and want to spray them then thin with MEK and avoid thinning with acetone ... that affects working life of the spray mix. We have done millions of substrates using the silver filled epoxy. Test conductivity of the surface over a 1-inch distance conductivity for a layer that is 0.0002" should be just a few ohms. Higher values mean the ink is too lean in silver or copper. If using silver then you don't need activator but if you use copper or nickel you will need to use a Pd or Sn catalyst.
copper sulphate baths, high acid low metal can work quite well. Many PCB types from Atotech, or Macdermid, or Uyemura work well. Drop the current down for best results.
Patrick
Materials Scientist - North Andover, Massachusetts USA
January 10, 2015
November 24, 2017
Q. I'm digging through Electrotype Manipulation
⇦[this on
Amazon affil links] (1852) and in the second section it recommends for plating on plaster- making the initial plaster with "sour whey" instead of water and then to saturate it with "silver solution".
It goes on to say that the silver will be reduced through sunlight and produce a decent conductive surface.
I'm assuming the silver solution is silver nitrate and added after the plaster has dried.
1 Other than that should I use the conductivity test described above in regard to epoxy compounds to determine the proper ratio of nitrate to plaster ?
2 I'm plating with copper so could this work with graphite or copper dust in lieu of the silver? I'd like to keep my costs down as I could see this process getting expensive.
3 Any recommendations to replace the whey?
Thanks!
Artist - Brooklyn New York usa
A. Hi Raphael. Yes, you can certainly metallize with copper or graphite instead of silver, but you can't expect operations that are specialized to silver (like reducing it to metallic form with sunlight) to work on copper or graphite. You need to take it from the top, not just substitute.
I'm not sure what role the sour whey plays in that 1852 recipe, but I doubt that you can simply skip that step; but whey should be easily available and relatively cheap in health food stores. It's simply the liquid that's left over when you curdle milk. Good luck.
Regards,
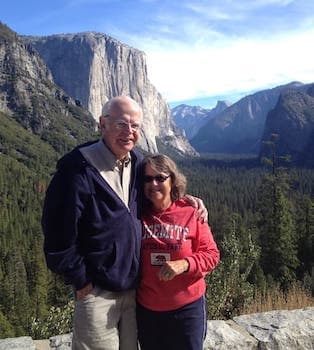
Ted Mooney, P.E. RET
Striving to live Aloha
finishing.com - Pine Beach, New Jersey
Q. I would ask if anyone has been tried to use Bare Conductive (brand) Electric Paint (Water based) on ABS Plastic and then proceed with the acid copper solution to attain the copper coating?
Qertusa Wazir- JOHOR BAHRU, Malaysia
November 22, 2018
A. Hi Qertusa. I'm fairly certain that it is do-able -- it's a truism that virtually anything can be metallized and plated. But whether it would be satisfactory depends on the application, and one of the toughest requirements is obtaining sufficient adhesion..
Copper-nickel-chrome plating of plastic automobile grills, for example, requires outstanding adhesion to hang onto the ABS in blazing sun and frigid cold, and despite abrasion from carwash brushes and spit gravel, etc.
Regards,
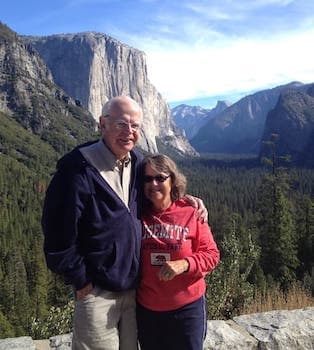
Ted Mooney, P.E. RET
Striving to live Aloha
finishing.com - Pine Beach, New Jersey
November 2018
Electroplating non-conductive material
June 18, 2020Q. Dear gentlemen, good day.
As the topic said, I want a non-conductive material to be electroplated.
I assume first step would be electroless plating, then electroplating on top of it.
There are two options, either copper or nickel.
Which one is better in this case, in terms of conductivity and as a prime plate to electroplating?
Is there any difference to consider between electrolessly plating metallic and non-metallic substrate (solution composition, steps, type of chemicals, parameters, quality test, etc.)
How much is the thickness required for each to electroplate on top of it?
Is there a standard (e.g. ASTM) for plating non-conductive material?
What are the test methods?
Thank you
- Cairo, Egypt
by American Society for Electroplated Plastics
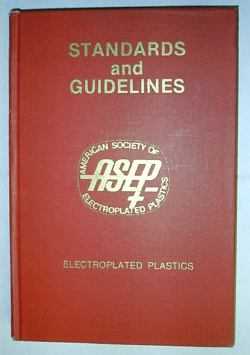
on AbeBooks
or eBay or
Amazon
(affil links)
A. Hi Salem. Electroless copper isn't much used anymore except on circuit boards / printed wiring boards because it's more expensive, and more difficult to control & waste treat, so the short answer to your question is probably electroless nickel. But even that is being replaced by 'direct metalization' in many applications.
As you see, we added your inquiry to a thread about electroplating non-conductive materials. We have hundreds of threads on that topic here, and many books have been written about it, so it's not easily discharged in a single forum posting. Everything from animal skulls through flowers & leaves on up through plastic automotive grills have been metalized and plated. Your need sounds "industrial" rather than hobbyist or artistic, so I think you're on the right track with electroless nickel, but people really can't help you until we understand what you want to do -- for example "Standards & Guidelines for Electroplated Plastics" has a 30-page chapter just on those ASTM specs you request.
What is it that you want to electroplate? What material is it made from? What is it that you want to ultimately plate it with (gold, chrome, a PVD coating, etc.)? Why do you want to plate it (appearance, corrosion resistance, electrical conductivity, wear resistance)? Thanks!
Regards,
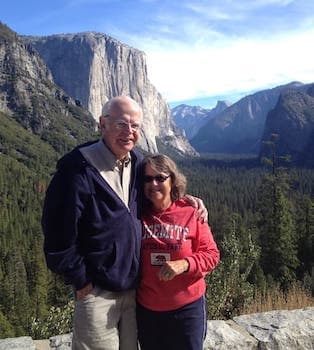
Ted Mooney, P.E. RET
Striving to live Aloha
finishing.com - Pine Beach, New Jersey
June 2020
Q. Dear Ted, thank you for your answer.
Indeed, the process I need is industrial process not hobbyist or artistic.
the requirement of my needed plating process is to add a conductivity to a non-conductive material, and to electroplate it using conventional plating methods.
I am trying to build this capability to have different materials go through this process, so really there no single material I am trying to electrolessly plate, it is more like a continuous process. This is why I am asking of an ASTM standard to look into it and modify my process based on it.
Again Ted, thank you, and if you can provide the ASTM number it would be great.
- Cairo Egypt
June 21, 2020
A. Hi again Salem. ASTM B733 is the spec for electroless nickel plating, and other standards organizations have other specs; please see thread 39060 for a general discussion of the standards. But that spec only covers the electroless nickel step itself, not the whole sequence for plating on plastic.
There are a few things you may or may not be aware of, but I'll mention them for the benefit of other readers --
1. There are many different metalization techniques; not just the electroless nickel, electroless copper, and direct metalization methods already mentioned. See our FAQ "Plating Organic Materials" for a quick introduction to some other approaches. Almost anything can be metalized for subsequent electroplating, but a principal issue is usually the need for extreme and flawless adhesion, and some methods can't deliver enough for difficult industrial needs.
2. The process for applying electroless nickel to plastic is somewhat involved. It's not one step, but many. Exact sequences and names vary, but typically etch, activate, accelerate, electroless nickel plate (with rinses between each step) would be the minimum. Thread 1020 presents typical process sequences.
3. ABS is a special plastic designed for maximum adhesion; the butadiene is dissolved in an etch, leaving millions of tiny little spherical pockets the Pd activator deposits into, and onto which the electroless nickel grows. You can metalize other plastics but you won't get equivalent adhesion because you won't have those spherical pockets.
Regards,
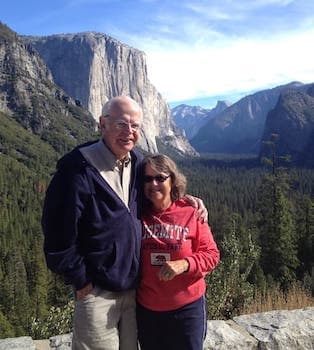
Ted Mooney, P.E. RET
Striving to live Aloha
finishing.com - Pine Beach, New Jersey
June 2020
Dear Ted.
your kind and informative response to my question is highly appreciated.
thank you very much,
- Cairo Egypt
June 21, 2020
adv.: Supplier of Copper Anodes, Nickel Anodes, Bismuth Metal, & Other Metal Products for Industry & The Arts
Q, A, or Comment on THIS thread -or- Start a NEW Thread