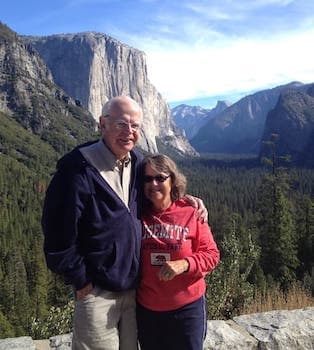
Curated with aloha by
Ted Mooney, P.E. RET
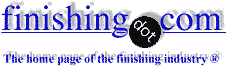
The authoritative public forum
for Metal Finishing 1989-2025
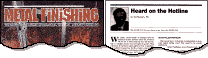
-----
Conductive paint for plating on plastic, flowers, etc.
Q. I need help plating on non-conductive surfaces. I am trying to plate flowers. I am currently using a copper conductive coating both sprayed and brushed on, they are then tinned and then nickel plated. I have had problems with both constancy and with the length of time to apply. I spoke with a company that sells a silver conductive paint while this may or may not be more effective I don't think it will solve the problems I having. I would like to find a more cost and time effective method than the one I am using. Any advice or product information would be greatly appreciated....Bob
Robert Browngold plating - Montour Falls New York
1999
A. Although I've never plated flowers myself, I believe that if high volume is involved you will get faster & more accurate results by starting with lacquering and then a two-part silvering solution (simultaneous spray of silver nitrate and a reducing solution) than from a conductive paint.
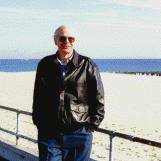
Ted Mooney, P.E.
Striving to live Aloha
finishing.com - Pine Beach, New Jersey
A. I tried finding a spray paint or coating to use last summer, when I tried my hand at non-metallic substrates. I found that an inexpensive spray coating that had 95-97% zinc powder in it works great, and the price under $3.00 a can. Give it a shot, industrial/commercial supply houses have it.
Good luck.
Philip Lee Camp- Phenix City, Alabama
2002
? Are you referring to cold galvanizing spray? ⇨
Chris Cardino- Doyline, Louisiana
October 19, 2023
Ed. note: Philip's posting was from a very long time ago and he is unlikely to reply, but we share your interpretation; I don't know if it was actually available for $3 in 2022, but that's not a realistic price in 2023 :-)
A. Graphite paint coating is alkaline coating. I had no problem adding a touch of lacquer for better spray/finishing quality.
The graphite coating is high solids, low resins and small amount of a "hot" carrier solvent[s] most likely MEK and a touch of Xylene (sold to be a non stick sliding surface, it is sold in unadulterated graphite powder, just enough resin ingredient to bind. Being such a virgin product I have experimented with different paints and clear resins with overall success.
Do anticipate heavy and quick settling; mix often. Thin solution and succession of multi dips have immersive coating of a conductive material. To make stayfast of shape and composition of material one could spray a coat or two of shellac as it is quick drying and minimally reactive to surface adherence, and dries to a decent rigidity.
To maintain minimal effects a coating can give, thin to a very low resin and high carrier solvent. It evaporates to a minimal film, repeat.
I wonder how the spray can "dryfilm" lubricant would work for conductive coat? I've used for certain finishing applications and it is simply graphite mixed with acetone and has no resins. I prefer the nonstick alkyl coat -- it is perhaps 85-90% solids, similar to galvanize brush on paint, making it an adaptive material for experiments.
- Effingham, South Carolina
October 28, 2023
⇩ Related postings, oldest first ⇩
Plating on glass
Q. Dear specialists,
This web-site database contains a lot of questions/answers on the plating the metals on the glass. But restrictions of my task force me to ask about this again. For laboratory research I need to make the inner surface of fused silica capillary (360 µm OD, 100 µm ID, 0.5 m length) conductive. In literature and on this web-site I have found a lot of information about metal plating on the glass. But I encountered great problems when tried to realize any of the methods described.
The capillaries are covered outside by polyamide protecting film, therefore plating process cannot be hot, to avoid the film destruction. The inner diam is so small and the length is so big, that it is impossible to use vacuum deposition. The silver mirror having good adhesive property and strength, which could be created without any problem on the outer surfaces by two-nozzle spray, cannot be created at the inner surface (I tried to reduce the speed of silver deposition by diluting and lowering pH in order to allow solution to fill the capillary before the silver starts to deposit. But silver layer never appeared to be strong and adhesive and always exfoliates and clogs the capillary).
I also cannot create the tin oxide film, because this process needs too high temperatures.
Now I try to plate the gold, but experience the same problem - gold layer is not adhesive. My current process includes:
1) glass surface etching by HF,
2) sensitizing by NiCl2/borane-tertbutylamine reducer (not by SnCl2/PdCl2) - similar, but not equal to as described by Feldstein in US patent 3993799 (1975), and
3) plating in KAuCl4 + borane trimethylamine mixture, pH=12 (adjusted by NaOH) (similar although not equal composition to as described by Burke et al, US patent 4142902, (1979)). Temperature is always room temperature. Rinsing in distilled water is done after each step. For first experiment I try to plate on the glass stick, not inside the capillaries. I use double distilled water for solutions preparation, not deionized water. I needed to modify the recipes from patents because I could not find all chemicals described.
What I do wrong? What is the main direction of search could you recommend?
I would appreciate for any comments on my question and also for any information how to make the glass surface conductive by other methods, different from metal plating?
Sincerely,
Sergei AksyonovArizona State University - Tempe, Arizona, USA
2001
A. Do you want to invent a patentable way to coat your product, or do you want to coat your product?
Have you exhausted the possibility of using proprietary chemistry? Many of the problems from a patent to a useful product have been worked out.
Or at least use proprietary chemistry first, then try to equal or do better with a novel chemistry, then file the patent!
Best Wishes,


Tom Pullizzi
Falls Township, Pennsylvania
Q. Dear Tom Pullizzi,
Now I need to make conductive (only from inside) fused silica capillaries only for laboratory needs. I didn't think about inventing something new, but I feel I go that direction.
You are right, there are a plenty of patents about the electroless plating. I searched through several dozens of them. But close view reveal, that all of them use two-three basic approach with slight modifications.
Particularly, I didn't found any information about good one_solution method for silvering. All of them use two sprays -- this is because of the demand that silver salt and reducer must meet together only on the plated surface. Really, if one places two droplets (silver salt and reducer) on the glass and slowly connect them, then excellent bright silver appears on the boundary between two droplets, and never under the droplets. The sludge is formed in the volume of mixed silver salt+reducer deposits on the glass, making the growing silver layer (formed under droplet volume) porous and non-adhesive :-(. This is an essential of the two-spray method.
For my purpose (thin capillary) I essentially need one-solution method. It should contain some sludge inhibitor, which nevertheless allows silver to deposit on the glass.
Actually I found one well described one-solution silvering method in one book on glass blowing from 1950's, but close analysis showed, that sludge effect is overcome by thick silver deposition, thus making silver layer strong enough, although allowing some sludge to be incorporated in the layer. This will not work for me because capillary is too narrow.
Feldstein in one his patents describes the additives (Pb, Sn, etc. salts) which, as he claimed reduce the sludge formation. But nevertheless he used two-spray method. I tried this approach, but sludge appeared in volume before the silver began to deposit on the glass.
I see one way to overcome sludge-in-volume, this by adding some silver-chelating agent or micell-formator. But what could it be? It should be some substance, that covers the silver suspension particles as they appear and prevents their further growth but does not prevent extended silver layer to grow.
Sincerely,
Sergei Aksyonov [returning]Arizona State University - Tempe, Arizona
A. Hi Sergei. I think you misunderstood Tom's reply which was to buy a time-proven proprietary solution from a vendor who has fully developed it over the years, rather than going back to the patent (which discloses as little as possible) and having to do all that development work yourself.
For example, when you say: "some silver-chelating agent or micell-formator. But what could it be?", Tom is suggesting that you buy a proprietary from a supplier who has already answered that question. Good luck.
Regards,
Ted Mooney, P.E. RET
Striving to live Aloha
finishing.com - Pine Beach, New Jersey
A. Here in Israel there are quite a few plating shops for plating decorative glass items. They all use conductive paint that is sprayed on the glass. On top of the paint layer they plate acidic copper and cyanide silver, both at room temperature.


Sara Michaeli
Tel-Aviv-Yafo, Israel
Q. Thank you, Sara, but probably it is not what I am looking for. Nobody can spray inside 0.1 mm inner diameter capillary with length ~0.5 m.
Sergei Aksyonov [returning]Arizona State University - Tempe, Arizona
2001
A. Instead of trying to coat the inside of a long capillary, make the capillary of metal and coat the outside with glass or another insulating material.
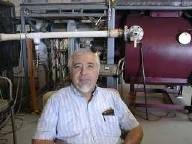
Jim Treglio - scwineryreview.com
PVD Consultant & Wine Lover
San Diego, California
! Dear Jim Treglio,
Thank you for the idea which is a real inventor's approach! I thought about something like this but other restrictions of my task do not allow to use this method.
Anyway, thanks!
P.S. All manufacturers able to make such coating are welcome.
Sergei Aksyonov [returning]Arizona State University - Tempe, Arizona, USA
2001
A. Hi again. I would add that an very easy way to make that capillary out of metal despite its shape would be to electroform it onto wax, aluminum, or other dissolvable material.
Luck & Regards,
Ted Mooney, P.E. RET
Striving to live Aloha
finishing.com - Pine Beach, New Jersey
A. adv.
We have been coating the inside of fused silica and metal capillary tubing with metals, semiconductors and dielectrics, for years. Please drop us a line. I am certain we can help you out.
- Bellefonte, Pennsylvania, US
Ed. note: We will be delighted to retract this notice if we are advised otherwise, but we believe that Surface Conversion Sciences is not in business anymore. Back in 2001, Surface Conversion Sciences was a supporting advertiser on finishing.com.
Q. Dear Sergei Aksyonov,
I have the similar problem to coat the inside surface of the microcapillary to make it conductive. Also, the metal coating need to be thinner than 800nm to make sure the visual light could go through. I read your question and all the follow-up answers here. Did you get any solution for your problem?
Any suggestion is welcome.
Limin LiuTulane university - New Orleans, Louisiana
2001
Ed. note: Our FAQ on metallizing non-metallic materials lists a number of different metallizing approaches and may be of some help to the readers. Although we have no experience to bear it out, in theory it would seem that a silver nitrate solution should be reducible electrochemically or with some sort of "time release" reducing solution to obviate the problems that Sergei is seeing with two-part silvering.
Q. I like to produce/print as if a printed circuit on glass with transparent but optically conductive tracks for putting LEDs on it and sandwiching the same between two glasses by single component, UV curable adhesive to produce laminated safety glass. The same shall be electrically connected from outside to light up the LEDS. It would give appearance of LEDs light up without wire being seen from out side.
Second, application is to put invisible tracks on automobile glass/house glass to heat them up for fog control. I am looking for a method which can be employed without much infrastructure, comparatively safe in handling. economical in price. Can some one provide the solution with name and addresses of manufacturers of the involved materials
Thanks,
hobbyist and product designer - NASIKROAD, MAHARASTRA, INDIA
2007
A. If the conductive surface does not have to be very long maybe you could use a microchip. This could be assembled with conductive layers. You could insert length of capillary into the ends to make it longer
nick schlensky- denistone, nsw, australia
April 6, 2010
Plating on flowers
Q. I want to start new work in my city. I want to plate flowers; can you help me how I can plate on flowers?
Kamlesh Bhanvadiafor plating - Rajkot, Gujarat, India
March 25, 2011
Conductive paint for plating on plastic
Q. Hello,
1. I would like to know which conductive paint is suitable for brush plating plastic, e.g. a remote control or a plastic laptop case. I saw many supplier selling silver or copper RFI, EMI shielding conductivity paint, can I use it?
2. Which surface resistivity level (after paint) is good enough for brush plating? <1 ohm or 100-1000 ohm?
3. After spraying conductive paint, can I brush plate immediately or is there any step in between?
Thank you for your time.
Regards,
Hobbyist - Vietnam
November 17, 2011
A. Hi, To,
There are multiple ways to EMI shield a laptop, and multiple ways to electroplate plastic (or to "chrome look" plastic), of course. The approach you mention of using a graphite-based, copper-based, or silver-based "paint" and then electroplating it is widely used, although it is not how the very highest quality plated plastic (automotive exterior chrome) is done.
Comments regarding the advantages/disadvantages of graphite vs. copper vs. silver vs. other approaches are welcome, but we discourage responses which suggest particular brands or sources huh? why? Please use google or another search engine for live searches of sourcing info. We try to keep finishing.com a permanent reference source for metal finishing answers, free of broken links or outdated info, and sourcing info is unfortunately incompatible with permanence :-)
Good luck.
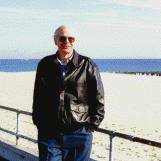
Ted Mooney, P.E.
Striving to live Aloha
finishing.com - Pine Beach, New Jersey
Q. I am a fledgling artist who is at his wits end trying to find a way to "electroform" organics. I have a really crappy rectifier (RioGrande 5-Amp, 1-20 V) which constantly fluctuates its output during my plating process leaving all sorts of bumps and blemishes on what invariably turns out to be a salmon pink plated object. What's worse, is that the water based colloidal copper paint I've been using often peels from organics (especially bone) allowing my copper sulphate
⇦ this on
eBay or
Amazon [affil links] pentahydrate solution to eat away at the organics underneath, which eventually turns the entire piece puke colored.
I'm trying to find a faster and cheaper way to coat organics than expensive paint. I stumbled upon this:
Is it possible to use this process to coat organics (esp. bone) for copper electroplating/forming using an acid copper sulphate bath?
Dicky BrucksHobbyist - Oakland, California
December 6, 2011
A. Hi, Dicky.
Unless you're talking about very small bones that can fit in the small beaker shown in the video, that strikes me as a dangerous way to metallize them. I think you need a better or more reliable conductive paint instead. It's also possible that the bone isn't really clean (scrub it with a toothbrush and powdered pumice in a little detergent, and see if that helps).
If you have a "crappy rectifier", plating will remain hopeless.
I would also suggest trying to get a proprietary acid copper plating solution rather than using straight copper sulphate. The lumpiness you experience is inherent in the process because as soon as the first bit of copper deposits, it's both a protuberance that draws current, leading to faster localized growth, and a crystal structure that the next copper atom will easily "fit". One way to discourage this large crystal growth is with proprietary brightening agents that are drawn to the area of high current density, and coat it, tending to shield it and divert the current to a lower current density area. It's not quite that simple or easy, but the principal works.
Regards,
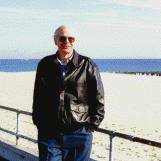
Ted Mooney, P.E.
Striving to live Aloha
finishing.com - Pine Beach, New Jersey
Q. I've seen Aerodag G spray online (google it) and was wondering if it's possible to use this for an acid copper sulphate electroforming process. My main concern is whether the resistance of carbon based paints would be too much for the low currents used in electroforming. I have a water based copper conductive paint - works, but it leaves much to be desired in terms of detail, has a long curing time, and is fairly expensive. Also every organic I've tried winds up eventually being dissolved by the acid due to weak spots in the coat, ruining the bath.
Any advice would be awesome.
- Oakland, California
December 6, 2011
Ed. note: The technical data sheet seems to imply that this product is not optimized for that purpose but that it's possible.
Polishing Copper Plating on Plastic
Q. Good morning everyone,
Hope you are all staying sane during this very strange time. I am doing some chrome plating over plastic, it's for some small parts that I couldn't find anyone near me willing to plate for a reasonable price. I have 10 years experience barrel plating zinc and zinc nickel over steel, but I have never plated anything copper, nickel, or chrome.
To do this the process that was suggested to me was a conductive spray paint, copper plate, nickel plate, chrome plate. The problem I am having is that the copper plate comes out rough because the conductive spray paint creates a rough surface. I am trying to polish and smooth the copper plate using either a buffing wheel or a vibratory tumbler, I have a small tumbler. Unfortunately it seems that every time I try to tumble the parts it just removes too much of the plating and leaves the corners bare. I tried polishing the paint and that effectively did the same thing. I am plating small plastic knobs for a hot rod I am building since I couldn't find the original knobs in chrome. Does any one have any suggestions? Please ask any questions you need answered if it might help. I don't necessarily know what questions you may need answered. Thanks for all your help in advance.
This is for my 37 ford coupe - Surprise, Arizona, USA
April 3, 2020
A. Hi Nick. I think you probably realize that conductive paint is not the ideal way to metallize plastic for subsequent electroplating, but is a make-do method because the industrial methods are complex. Even still, if your paint is leaving a rough surface, it seems better to me to try to improve that step rather than to polish the copper after plating to make up for a rough metallization layer. There are surely better metallizing compounds that would be smoother, and even if not, maybe you can thin your paint and apply multiple layers instead of a thick rough layer? When craftsmen make expensive brass chandeliers, the way they get a beautiful smooth lacquer finish is to apply a half dozen or so highly thinned coats.
Regards,
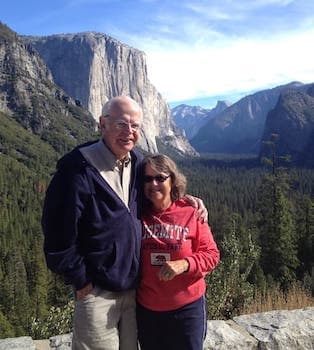
Ted Mooney, P.E. RET
Striving to live Aloha
finishing.com - Pine Beach, New Jersey
Q, A, or Comment on THIS thread -or- Start a NEW Thread