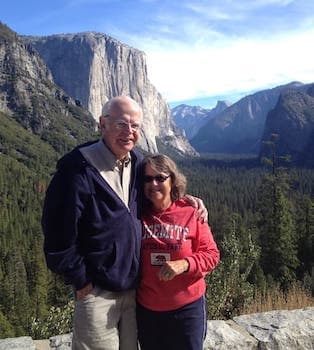
Curated with aloha by
Ted Mooney, P.E. RET
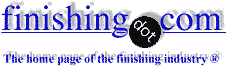
The authoritative public forum
for Metal Finishing 1989-2025
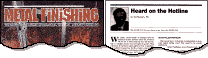
-----
Peel-off strength of Electroless Nickel on Aluminum
Quickstart (no readers left behind):
Electroless nickel plating is not used directly on aluminum because aluminum instantly acquires an oxide coating which is not a proper base for plating; rather the aluminum is zincated first (immersed in a highly caustic zinc solution which causes a replacement/immersion coating of zinc onto the aluminum. Readers can search the site for 'zincate' to learn more about this step or sequence of steps.
Some commenters believe the next step should be an alkaline electroless nickel strike rather than an immediate "high build" electroless nickel formulation -- read on.
Although MIL-C-26074
[⇦ this spec on DLA] has been withdrawn and replaced by SAE AMS-C-26074, the Mil spec is instantly available, and free, so for learning purposes it may still be an excellent tool.
[editor appended this entry to this thread which already addresses it in lieu of spawning a duplicative thread]
Q. I coated aluminum alloy with electroless nickel with a pH of 7 for 5-10 minutes and a temperature of 75-80 °C before bright nickel and chrome, but the results sometimes peel off. Is the temperature too hot or the dipping time not long enough?
Hobbyist - Ngawi, Indonesia
March 28, 2025
A. Hi Muhtardianto. We'd need more data to help you. It's not clear if you did fully correct cleaning, etch, desmutting, and zincating before your electroless nickel, or whether you didn't recognize that it's necessary and simply dipped your aluminum into electroless nickel plating solution.
Please give us full details of your process sequence, and what alloy of aluminum you are trying to plate, and I'm confident we can help you.
Luck & Regards,
Ted Mooney, P.E. RET
Striving to live Aloha
finishing.com - Pine Beach, New Jersey
⇩ Related postings, oldest first ⇩
Q. We have designed an aluminum (6063) terminal block which is EN plated then soldered directly to a circuit board but we've found that a smaller force than expected detaches it if given any load - the bond between nickel plate and aluminum fails.
My question is: What peel-off force range should I expect from this process (our plater advises only 1-2 PSI). We have done our best to isolate the part from any force but we are having failures during assembly.
Thanks
electronics manufacturer - Gateshead, Tyne & Wear, UK
2006
A. I can exert more pressure than 1-2 PSI with my fingernail. I doubt that figure (as stated) greatly. Poor adhesion on aluminum is a result of either the cleaning or the zincate step. There is no good visual indication of the quality of the zincate, so it is done poorly in a number of shops. We used an alkaline EN strike followed by a mid phosphorous EN and had excellent adhesion.
James Watts- Navarre, Florida
A. Shooting this plater might be an appropriate corrective action. More profitably, accept payment for not publishing their name with their inane 1-2 PSI comment on the Internet. Did they certify to some standard?
To withstand plating stresses (coating internal stresses and CTE stress cooling from plating temperature), EN-to-aluminum adhesion should be 5000-10,000 psi. Adhesion can be improved and internal stress relieved by baking (e.g., 120 °C for 1 hour for heat-treatable Al alloys), but this will reduce solderability. The 180° bend test and uses such as die/mold and engine piston coating suggest adhesive strengths of 25,000-50,000 psi are achievable.
Many possible causes of adhesion problems; see threads
878,
4074,
4487,
12880,
14954,
21801,
22414,
23303,
27627...
For an EN-plated Al block, the quench test can be used: Heat the item for 1 hour at 250 °C, then "quench in room temperature water. The appearance of blisters or peeling is evidence of inadequate adhesion."
-- Electroless Plating, pp. 180-181, Mallory & Hajdu, eds. (1990) ⇨
Ken Vlach [deceased]
- Goleta, California
Finishing.com honored Ken for his countless carefully researched responses. He passed away May 14, 2015.
Rest in peace, Ken. Thank you for your hard work which the finishing world, and we at finishing.com, continue to benefit from.
A. The shear bond strength of properly pretreated aluminum is at least 16,000 psi. Proper pretreatment of aluminum requires cleaning, deoxidation, etching and a double zincate immersion to guarantee good adhesion.
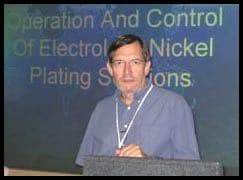
Ron Duncan [deceased]
- LaVergne, Tennessee
It is our sad duty to note Ron's passing on Dec. 15, 2006. A brief obituary opens Episode 13 of our Podcast.
by Fabienne Delaunois et al
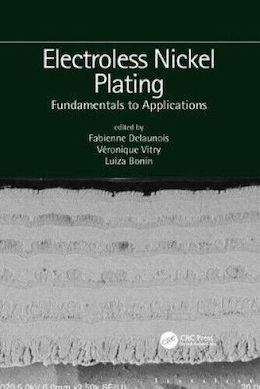
on eBay or
AbeBooks
or Amazon
(affil links)
by G. G. Gawrilov
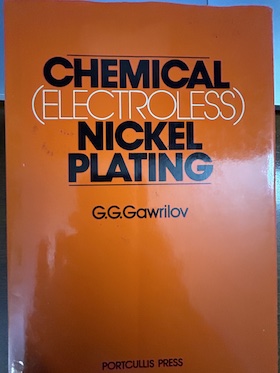
on AbeBooks
or eBay or
Amazon
(affil links)
Thanks for all the help. Unfortunately the plater is our manufacturing subcontractors supplier not ours so getting anything meaningful out of them is taking time.
Q. Certification to standards has been mentioned, what standard would be appropriate in Europe? A standard would probably be the most suitable.
I guess this might be 'a question too far' so some pointers as to how I can find out for myself would be equally useful.
electronics manufacturer - Gateshead, Tyne & Wear, UK
A. I believe the current European spec. is
ISO 4527:2003
(BS EN ISO 4527:2003 in the UK) Metallic coatings. Autocatalytic (electroless) nickel-phosphorus alloy coatings. Specification and test methods.
Description: Metal coatings, Coatings, Electroless plating, Nickel, Nickel alloys, Phosphorus, Heat treatment, Surface defects, Chemical composition, Chemical analysis and testing, Calibration, Density, Physical properties of materials, Adhesion tests.
Cross references to ASTM, EN and ISO specs.
This International Standard does not apply to autocatalytic nickel-boron alloy coatings, nickel-phosphorus composites and ternary alloys.
- Goleta, California

Rest in peace, Ken. Thank you for your hard work which the finishing world, and we at finishing.com, continue to benefit from.
UPDATE Through some testing and help from a local university we have discovered that our failures are actually due to shock fracture not peel off.
The failure is of the nickel/phosphorus coating which is made shock sensitive due to the interaction of phosphorus and aluminium during the soldering process and stressed by the relative thermal expansions of the aluminium and nickel. This stress is 'locked in' by the freezing of the solder attaching it to the circuit board and a total failure is then initiated by a fairly small shock to the assembly.
electronics manufacturer - Gateshead, Tyne & Wear, UK
Thanks for the research and the update!
Now the problem mutates to: what is special about your application that is causing this? Particular aluminum alloy, phosphorous level in your electroless nickel, composition or application temperature of your solder, etc.
Because the thing is, thousands of plating shops do electroless nickel plating of aluminum components which are subsequently soldered to circuit boards. Something is either very special about your application, or something is being done during pretreatment, plating, or soldering which is causing this sensitivity to shock which other applications are not suffering.
Luck & Regards,
Ted Mooney, P.E. RET
Striving to live Aloha
finishing.com - Pine Beach, New Jersey
Plating Adhesion Problem, Gold on Electroless Nickel on Aluminum
Q. I am having a problem with adhesion of my plating (electrolytic gold on electroless nickel over aluminum 6061). After environmental testing (moisture 85% temp 85 °C) there is bubbling. When viewed, it can be seen that the nickel has bubbled off the aluminum. It is interesting because if the part is not gold plated, there are no adhesion problems. It must be something to do with the current applied from the gold plating. I bake my parts for one hour at 320 °F after gold plating. This helps a bit but not much. I have tried both cyanide and non-cyanide zincate. I plate the gold at 5 ASF.
Anybody have any suggestions?
Thank you very much.
Darwin R [last name deleted for privacy by Editor]- Ottawa, Ontario, Canada
A. If the EN let go from the aluminum, I would question the quality of the zincate step. I am a very strong believer in the use of the alkaline EN strikes. It is excellent for improving adhesion. The ammonia smell is strong though.
James Watts- Navarre, Florida
Good spec for Electroless Nickel on Aluminum?
Q. Can anyone recommend the specification or callout for Electroless Nickel plating on 6061-T6 Aluminum? I need a coating with minimal heat distortion of the alum (chuck body lapped flat to .0005"), and .001 minimum thickness. The coating should be uniform in thickness, and is intended primarily for cosmetic improvement/corrosion resistance.
Thanks for any suggestions.
Mfg. Engineer (Consumer) - Issaquah, Washington, USA
2007
A. Good adhesion is probably required, too.
If selecting an electroless nickel plater, ask to see their monthly lab test reports per MIL-C-26074; most EN platers have the thickness, adhesion and corrosion tests run on both steel & aluminum test coupons.
Specify 0.0010-0.0012" mid-phosphorous EN per Class 4 of either ASTM B733 or MIL-C-26074
[⇦ this spec on DLA]. Class 4 require an adhesion bake suitable for heat treated aluminum, e.g., 120 °C (250 °F) for 1.5 hours. Have a scrap part or 6061-T6 test coupon included in the processing and adhesion tested (somewhat destructive) periodically. If adhesion is a problem, search this site for 158 inquiries on 'adhesion electroless nickel aluminum'.
Any heat distortion is actually the release of residual stresses from the initial quenching which have been unbalanced by machining. If this occurs, add a mild stress relief bake slightly warmer than the final adhesion bake, e.g., 125 °C (260 °F) for 2 hours, prior to final machining.
- Goleta, California

Rest in peace, Ken. Thank you for your hard work which the finishing world, and we at finishing.com, continue to benefit from.
Q. Good morning all,
may you suggest me some articles/texts about the heat treatment process (250-270 °F for 1-6 hours) after electroless nickel (High P) plating on aluminium alloys?
I'm interested to know:
- how this process can improve adhesion
- what the hydrogen embrittlement relief mechanism consists of and how it happens
Thank you and have a nice day!
- Emilia Romagna, Italy
April 26, 2018
A. Hi Maria,
I can think of 4 reasons why electroless nickel might be baked or heat treated.
• Components are sometimes baked simply as a test procedure. Plating has certainly been known to blister or peel, and baking it before deploying it may cause poorly adherent plating to blister, giving an early indication that it would have blistered in use.
• For improved adhesion. I do not myself understand the exact mechanism by which the adhesion improves, perhaps diffusion of the zincate, but MIL-DTL-26074 (although cancelled) may give you some insights, and discusses the "Class 4" treatment for aluminum alloys, with temperature and timing close to what you mention.
• For hydrogen embrittlement relief. This is often done on steel at about 400 °F for about 4 hours; when necessary, lower temperatures can be employed for longer times. Aluminum, especially high strength aluminum, also suffers hydrogen embrittlement, but the issue is more complex and less understood. Still, I don't think 250-270 °F for 1-6 hours will accomplish much in terms of HE relief. There are many papers available on the subject which can be located with scholar.google.com; it is a complex subject which I don't have expertise in, but I easily found many such papers, so this may answer your request for articles.
• For increasing the hardness of high phosphorous electroless nickel. This requires significantly more than 250 °F though; more like 375 °F.
Apologies that this is a complex subject, highly dependent upon the specific aluminum alloy being used.
Luck & Regards,
Ted Mooney, P.E. RET
Striving to live Aloha
finishing.com - Pine Beach, New Jersey

Q, A, or Comment on THIS thread -or- Start a NEW Thread