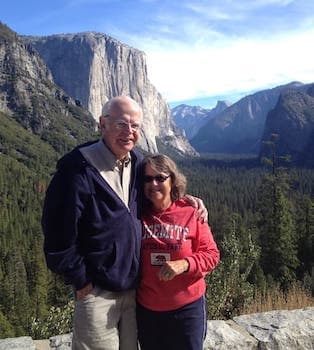
Curated with aloha by
Ted Mooney, P.E. RET
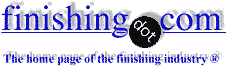
The authoritative public forum
for Metal Finishing 1989-2025
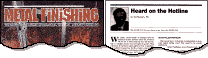
-----
Zincating of aluminum: single or double and why?
Q. Hi,
Is there any method to replace or eliminate Zincate Double process & do direct alkaline copper before final acid tin plating on aluminium substrate?
I'm experiencing problem w.r.t. adhesion of Cu & Sn on Aluminium substrate.
Finishing engineer - Noida India
January 23, 2022
A. Hi Arvinda. There are proprietary alternatives to zincate, like Bondal (a nickel-zinc immersion process) and Alstan (a stannate immersion process followed by tin plating). I have heard claims that electroless nickel has sometimes been successfully done directly on aluminum. But the basic issue is that aluminum instantly forms an oxide surface, so a replacement process rather than direct electroplating is required.
Luck & Regards,
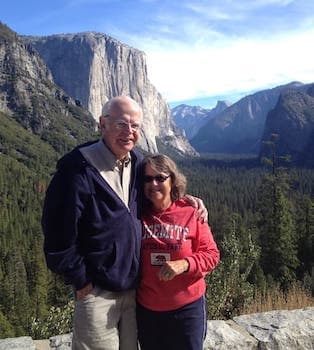
Ted Mooney, P.E. RET
Striving to live Aloha
finishing.com - Pine Beach, New Jersey
January 2022
⇩ Related postings, oldest first ⇩
Q. I am actively working on NiP plating pretreatments. If anyone has any suggestions as to how to improve adhesion with a two step zincate. Mainly, I would like to contact those working on these types of problems to discuss options. has anyone used the recycling methods from Oak Ridge? Also, what aspects of the NiP bath effect adhesion?
Tom Read- San Jose, California
1998
A. Dear Tom ,
I am generally not a fan of double zincating , having said that I know of shops where it was the answer to ongoing problems , However , in my opinion the best zincate is one that gives an even dark grey color without any splotches or light colored patches , to achieve this I would recommend a dip time of approximately 2 minutes , agitation of the zincate ( not violent but enough to keep it moving ) and most importantly frequent analysis to establish a drag - out figure and hence a solution maintenance schedule .
What you must remember is that the Zinc dissolves in the NiP very quickly and any patches that bare up before plating has initiated will give rise to bad adhesion problems , remember also the rate of dissolution of the Zinc film increases rapidly as the temperature increases .
Have you considered an Electrolytic Strike of say Watts Nickel between Zincate & NiP coating ?
Regards

John Tenison - Woods
- Victoria Australia
1998
1998
A. John is right, the zincate layer dissolves in the NiP solution, that's why you should use a special NiP with high PH (8-9) that are specially formulated for EN plating on aluminum. You can use a high PH En solution to plate a flash EN layer and then enter into a regular low PH (4.6-5) for the heavy layer plating.
Beside, I hope you use a cleaner and deoxidizing agent prior to the double zincate.


Sara Michaeli
Tel-Aviv-Yafo, Israel
Multiple threads merged: please forgive chronology errors and repetition 🙂
Q. On the subject of - Zincating aluminum . As a process engineer for a relatively new plating company, I am always looking to prove why certain methods are incorporated into certain processing of base metals. Aluminum is one of which requires Zincating of the surface, and while that's not hard to get platers to understand , the "why" of zincating, what is most difficult is to get them to understand the why of "double" zincating and the benefits. Yet while I stand at the aluminum pre-plate line , I see single zincates more than I do doubles, I yearn to get some one to back me on the reasons for this double zincate- VS- single.
I am responsible for corrective actions on rejects and thus I answer them as to blistering/poor adhesion off aluminum, with " improper surface treatment" We plate EN direct on aluminum, and also live entry cyanide copper strike. So here is my request. HELP me explain better the benefits of double -VS- Single Zincate on aluminum. And any other input you can give on the processing of cast alum.
Thank you much.
todd Huehn- Blaine, Minnesota
1999
![]() |
A. Hi todd. When you zincate aluminium, well, aluminium and zincate change each other. The first etching in zincate is to build up etch structure in the aluminium area only for pure aluminium not cast aluminium. You remove this zincate layer in hydrofluoric acid or nitric acid and etch in the zincate for a second time about 20 sec; this zincate has a hexagonal compounding with the aluminium substrate. If you do this for example on cast aluminium, the aluminium area will then get a high contamination in the area because the area is too much to etch. This contamination can be hard to remove and can also destroy the EN bath. Most Lab reports will show you this. The zincate compound is harder when you double zincate. I hope this will help you. I have really tried to translate this into English. Regards, ![]() Anders Sundman 4th Generation Surface Engineering Consultant - Arvika, Sweden 1999 A. Todd, the shortest answer I can give is this: The difference between the single vs. double zincate is that the first film is rather thick and spongy. You can see this by the dark color on the parts. As you strip the first coating off and re-apply it you see a much different appearance. This is because the second coating is thinner and more dense than the first. The zincate strip doesn't take the first coating off entirely, thereby providing a good base for the second coat. The differences between parts plated with one zincate dip vs. two are usually better adhesion due to the E.N. or copper strike bonding much better to the part. A single zincate film will tend to dissolve more quickly in a plating bath before the initial coating is formed. Sometimes this leads to blistering and peeling of the coating when stressed or heated. ![]() Jim Conner Anoplex Software ![]() Mabank, Texas USA ![]() 1999 |
Is double zincate required for Electroless Nickel Plating on Aluminum?
Q. Is Double Zincate or a Copper Flash included in the Electroless Nickel Coat spec. AMSC26074 Class B or spec AMS2404?
Steve Soderberg- Denver, Colorado, USA
2002
A. If you have no answer or want to be absolutely sure you can buy the complete AMS2404 text (Aerospace Materials Specification) and check it yourself. It'll cost you less than US$60.
Guillermo MarrufoMonterrey, NL, Mexico
2002
2002
A. With respect to MIL-C-26074E, the direct answer is no. However, to meet the adhesion or salt spray requirements, your EN process may require the pretreatments mentioned for certain substrates. There is no 'Class B;' Classes 1-4 refer to heat treatments, and Grades A, B and C refer to minimum EN thicknesses. Caveat: haven't seen MIL-DTL-26074F yet, a Controlled Distribution Document.
FED-QQN-290 (replaced by AMSQQN290) (Electrodeposited Nickel) does have specific requirements for copper underplating on steel, zinc and high-Zn brasses. This spec. does not mention plating on aluminum.
Ken Vlach [deceased]- Goleta, California

Rest in peace, Ken. Thank you for your hard work which the finishing world, and we at finishing.com, continue to benefit from.
Multiple threads merged: please forgive chronology errors and repetition 🙂
Theory behind double zincating?
Q. I am just a little bit dazzled about the fact of acid washing or removing the zinc seed deposited on the 1st zincating process, what is the reason or principle behind?
Anna PaatNXP Semiconductors (Founded by Philips) - Cabuyao Laguna Philippines
2007
2007
A. The reason is because it works better, at least in some cases, Anna. The principle is less certain to me; I suppose that in the process of zincating, the aluminum surface grain or texture is beneficially affected in some way and when you strip it and start the zincating the second time the zincate sees this refreshed aluminum surface and reacts better with it.
In terms of material conservation it would seem to me that we should investigate as a research project whether it is possible to gain the same structure that the first zincate gave using just an acid or alkali without actually having to wastefully apply and strip zinc metal.
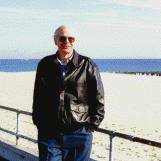
Ted Mooney, P.E.
Striving to live Aloha
finishing.com - Pine Beach, New Jersey
Multiple threads merged: please forgive chronology errors and repetition 🙂
Zincate Stripping
QUICKSTART:
Aluminum cannot be electroplated onto directly because exposure to air or water causes the instantaneous development of an insulating aluminum oxide skin.
So, instead, it is immersed into a strong 'zincate' solution (caustic soda ⇦liquid caustic soda in bulk on
Amazon [affil link]
, zinc, possibly cyanide, plus minor ingredients) which dissolves the aluminum oxide and replaces it with an immersion deposit of zinc which can then be electroplated onto.
However, it's widely understood that the process works far more reliably on some alloys and components if this initial zincate layer is stripped off in nitric acid and the aluminum component immersed in the zincate a second time ("double zincating").
Q. Why Zincate Strip is needed after performing immersion plating of zinc in Chrome Plating of Aluminium Wheels.
Surendra VermaPaint Technologist in Paint shop. - Haryana, India
2007
A. My belief is that "from experience" this gave results with fewer rejects, therefore became practice.
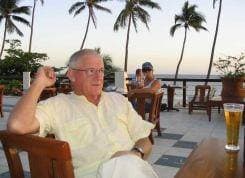
Geoffrey Whitelaw
- Port Melbourne, Australia
2007
A. Hi Surendra. The short answer is, as Geoff says, because it works better, at least sometimes :-)
This isn't seriously debated anymore (for certain types of aluminum) as it has been repeatedly demonstrated by testing over the years.
The longer answer, which is a bit above my pay grade, is that the zinc reacting with the aluminum, followed by the nitric acid reacting with the zinc deposit, followed by the zinc reacting with this "cleaner" layer of zinc produces greater adhesion. If you do a computerized literature search you will find numerous studies of this phenomena. The MFIS CD-ROM (available from Metal Finishing Information Services / Finishing Publications Ltd., Stevenage, Herts, England) for example lists about a dozen such published articles.
One of the more exhaustive references is David Lashmore's "Immersion Deposit Pretreatments for Electroplating on Aluminium - Literature Review" in Plating & Surface Finishing, April 1978, which references 40 earlier articles. Good luck.
Regards,
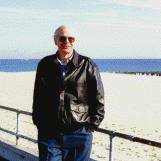
Ted Mooney, P.E.
Striving to live Aloha
finishing.com - Pine Beach, New Jersey
Q, A, or Comment on THIS thread -or- Start a NEW Thread