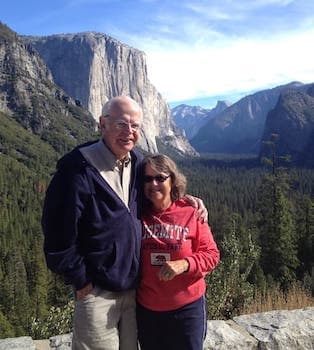
Curated with aloha by
Ted Mooney, P.E. RET
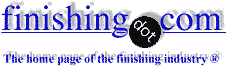
The authoritative public forum
for Metal Finishing 1989-2025
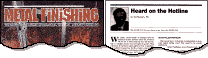
-----
Flaking/peeling of Electroless Nickel Plating on Aluminum
Q. We currently have a machine that is made of Aluminum and has been coated with a electroless nickel coating. The coating was specified as a "flash coating" After the machine has been in operation for about a year the nickel coating is starting to peel off. What would be causing this to happen. This machine is in a beef jerky manufacturing plant. The jerky has sea-salt, citric acid and vinegar power in it. Would this have any effect on the plating "peeling". Cleaning solvents being used could be bleach?
Walter Papierski- Longmont, Colorado
1999
A. Electroless nickel should be at least 0.0003" to afford any kind of protection against beef jerky mix. A flash should never be specified without a minimum thickness.
Chlorine bleach could also be a problem for porous coatings.
Best regards,
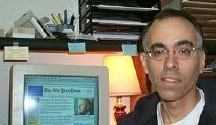

Tom Pullizzi
Falls Township, Pennsylvania
1999
2003
Q. We had a (nickel coating) flaking issue on casted A356.2 aluminum parts (with composite core) plated per ASTM B733 Type IV, SC1, Class 5 (size is roughly 2.0in x 2.0in x 0.25in). The parts we plated and visually inspected prior to shipping (UPS air and ground within north america). However, the parts were allowed to touch one another in the shipping trays (they were not individually packaged). Upon receipt, we noticed flaking on the rounded edges of the outline (it is a cast so they are drafted surfaces looking like this /__\ only with rounded edges). They were no signs of plastic deformation on the part.
This concerns me because reading the ASTM ASTM B571 (sections 2.4 and 2.5) leads me to believe that our shipping method could be construed as a coating adhesion test (sect. 2.5: "one uses any means available to attempt to seperate the coating from the substrate").
So, a blister test was performed on these parts (275 °C for 5 minutes) and visual inspection resulted in acceptable AQL.
The supplier swears that this is not a plating issue and that the shipping method was the culprit of the flaking. Partially true as individually wrapped parts do not show this flaking. However, I still think that we have highlighted a lower adhesion strength (coating on substrate) then cohesive strength of the coating (section 2.4).
I have pooled my company's plating experts from different sites/lines of business and usually, the plating tests (for different parts/intended use) are either (or) salt-spray test or a blister (heat) test. It might help me to have other people's input on which test are valuable.
My questions are:
1) am I wrong to think that we have bad plating because of these occurences of flaking? Am I misreading the ASTM B571 sections 2.4 and 2.5? We did pass the blister test.
2) what would be the tests for such a part/coating (eng. use coating, no wear, no solder, slight corrosion resistance only).
3) would the A356.2 require a different plating process that say a 6XXX or 7XXX alloy?
Thanks very much for any input.
Francis MarquisTelecom Industry - Ottawa, Ontario, Canada
A. Alloy 356 can be plated to withstand "flaking". The process for high silicon bearing cast aluminum like 356 is VERY VERY different from the process for plating on wrought metal.
Namely, the plater must increase the area of exposed aluminum metal and decrease the area of exposed silicon and most platers know how to do this.
Your plater has bridged big hunks of silicon on the surface, but the bridge was not "bonded" as zincate or stannate does not stick well to exposed silicon The shipping banged the parts together and the "bridges" flaked off.If the prep process had been better the plating would have bonded.
That said, however, be aware that thin walls in 356 are richer in silicon on the surface (a casting cooling phenomena) and this becomes very difficult and in some cases impossible to plate over.
Again, wrought surface preparation is nowhere near adequate for cast metal surface preparation+
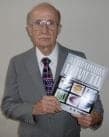
Robert H Probert
Robert H Probert Technical Services

Garner, North Carolina
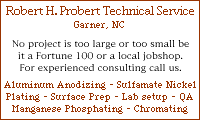
2003
Q. I'm the customer service Manager at a plating company.We have been Electroless nickel plating some tubes on the end of some radiators about 1/4" Dia. 3003 Alum. Recently the plating has been flaking off before the customer starts his soldering process. We have been going around and around with this but can't seem to cure the problem. Any Ideas?
Jay ElderPlating Shop Employee - Union City, California
January 7, 2009
March 3, 2009
A. What is the preplate cycle that you implement?
Without this info we cannot assist you


Sara Michaeli
Tel-Aviv-Yafo, Israel
July 10, 2014
Q. We are trying to improve the EN plating on Aluminum, specifically the adhesion. Thus we've come to a few conclusions and these are the steps taken:
Material = Change zincate chemical from Alumon (Enthone) to QEM2250 (Q & M Enterprises). Based on consultation with the QEM chemical supplier, the previous chemical Alumon is less compatible for reacting with current EN chemical.
Machine = Filter installation on EN tank (the filter filters out the contaminant/filtrate/deposits formed when EN plating).
Method = Tighten the chemical replenish MTO to <2 (to avoid chemical contamination).
Measurement = Installed a temperature controller on EN tank (the additional temperature controller auto adjusts the temperature).
Method = Daily chemical control 1st 40k , 2nd 35k, 3rd 20k for zincate I & II (to avoid chemical contamination).
My question is does this improve the adhesion of EN plating on Aluminum? And I need more detailed explanation if possible of how it improves it and is there any other method rather than the above? (if possible with reasons).
internship student of chemical engineering - Penang Malaysia
A. Hi cousin. We don't engage in discussions here as to whether one brand of proprietary is "better" than another, but any time a single supplier offers both the zincate and the EN process you are probably moving towards a more integrated approach, and more likely to get adequate help. The "better" chemical at any location usually proves to be the one with the more enthusiastic technical service person in that area :-)
Yes, filtration is imperative. 2 MTO is very low these days, but if economy is not paramount, usually the lower the better. Temperature control is also mandatory. Sorry, there were some conversion errors between languages, keyboards, and e-mail-to-HTML such that I don't understand your "Daily chemical control" sentence.
All of these factors affect adhesion, as does proper cleaning, and double zincating. Adhesion of zincate to aluminum, and electroless nickel to zinc, is by means of chemicals bonds rather than "tooth". So anything that impedes proper chemical reactions -- like dirt, grease, oxidation layer on the aluminum, or poorly formed zincate layer -- reduces adhesion. Good luck.
Regards,
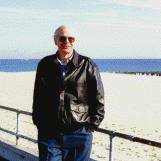
Ted Mooney, P.E.
Striving to live Aloha
finishing.com - Pine Beach, New Jersey
July 2014
Flaking of electroless nickel layer (but within the plating, not from the base metal)
January 21, 2015Q. My name is Kivanc Ekinciler and I am working as a coating engineer by a Turkish company.
We are using a mid-phosphorus electroless nickel process for several years successfully. We plate nearly 15 micrometers electroless nickel (after zincate treatment) on the aluminum (6082-T6) base metal and the adhesion quality is approved by control and acceptance tests. However, a couple of months ago, we faced up with an adhesion problem.
After epoxy-based glue being applied to the electroless nickel plated materials and letting them dry at 105 °C for an hour, it is seen that around the epoxy-based glue applied areas, there occurs electroless nickel flakes that is separated from the base electroless nickel layer, not from the aluminum base metal. It is thought that the reason can be this epoxy-based glue application, but this flake separation is also seen on the areas that epoxy is not being applied.
What can we do to solve this problem, your advice will be appreciated.
Thanks in advance.
Best regards
Coating Engineer - Ankara, Turkey
A. Hi Kivanc,
The problem could due to too high electroless nickel deposit intrinsic stress or plating basket was lift up and put back into bath solution during electroless nickel plating.
Regards,
David
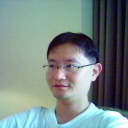
David Shiu
- Singapore
February 20, 2015

Q, A, or Comment on THIS thread -or- Start a NEW Thread