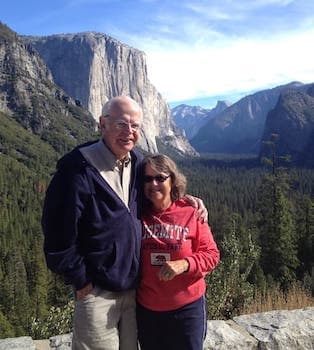
Curated with aloha by
Ted Mooney, P.E. RET
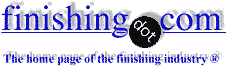
The authoritative public forum
for Metal Finishing 1989-2025
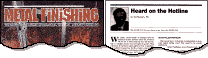
-----
Copper-nickel plating peels off aluminum
April 26, 2021
Q. I am using a zincate process to plate nickel-chrome over cast aluminum with no problem (It's zincate + bright copper + bright nickel + chrome).
But in order to get golden color over some products I am using a golden electrophoretic lacquer. The process is that after bright nickel a flash layer of silver is plated over the part and then electrophoretic lacquer is applied and
cured in 180 °C oven for 45 minutes.
Using the oven, the plating peels off aluminum only on the polished surfaces
(it works fine on shot blasted or sand blasted surfaces and plating only peels off from polished surfaces of the part).
I appreciate any help or suggestions.
Thank you
- Philadelphia Pennsylvania
May 5, 2021
Ahamad,
A. Peeling problem nickel/chrome plate on aluminum, check cleaning and nitrate contamination in your zincate or electroless nickel. Make sure zincating time is not too long.
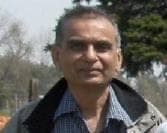
Popatbhai B. Patel
electroplating consultant - Roseville, Michigan
A. The wildest I can think of is that after heating you only have partial "mechanical" adhesion with the porous (die or sand) cast aluminum. Adhesion is worse over the polished area because there is no advantage of mechanically "locking" into the pores. At 180 °C for 45 minutes the copper and silver have diffused up and down and causing stresses in the nickel, then the varied coefficients of expansion from the heat pops it loose.
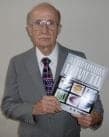
Robert H Probert
Robert H Probert Technical Services

Garner, North Carolina
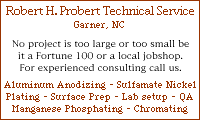
May 6, 2021
⇩ Related postings, oldest first ⇩
2004
Q. Dear All,
I'm a sales manager of a China factory and we've delivered some garden light to Sydney. These lights are made of aluminum with plating of copper+nickel. But now I have a return which plating is peeling off: I can see there's white powder hung on the aluminum, actually between copper coating and aluminum. I'm wondering how this happened. I guess it's due to weather reason in Sydney(big temp difference in morning and night?) or bad cleaning before plating?
Thank you for your help.
Vincent Dousales manager - Guangzhou, Guangdong, China
A. Hi Vincent. Weather has little to do with this problem, and is no excuse. When plating peels off like this, the parts were not properly plated!
Plating onto aluminum is a many step process. Yes, it could be improper cleaning (or etching, or desmutting), or a problem in the zincating, or a problem in the copper cyanide plating tank.
It's difficult troubleshooting this via an internet forum, but on the other hand, this is one of the more spectacular failures I've seen ... so it shouldn't take much effort to make a huge improvement :-)
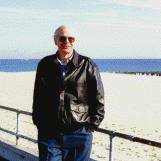
Ted Mooney, P.E.
Striving to live Aloha
finishing.com - Pine Beach, New Jersey
2004
A. The most common way to plate aluminium is to use the zincate process, followed by nickel. Copper plating onto zincate layers can be problematical and is usually avoided wherever possible. However, correct pretreatment of the aluminium prior to zincating is essential; otherwise the zincate layer is of no use. I would suspect the following things:
1) Is it the correct grade of aluminium for plating?
2) Was the pretreatment correct?
3) Was the zincating done correctly?
4) Is the nickel of the correct stress?
5) Are the process solutions all in specification?
Can you also please explain why copper is used instead of nickel as a direct metal layer on the aluminium?
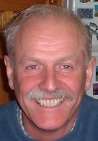
Trevor Crichton
R&D practical scientist
Chesham, Bucks, UK
2004
I can't disagree with you that copper plating onto aluminum can be problematical, and if nickel plating is better, that's great! Thanks! But I'll have to disagree about 'the most common way'. I've seen countless cyanide copper on zincate installations, a number of alkaline electroless nickel on zincate installations, but never an electrolytic nickel on zincate line :-)
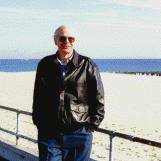
Ted Mooney, P.E.
Striving to live Aloha
finishing.com - Pine Beach, New Jersey
2004
My main experience with aluminium plating was in the engine bearing industry, where nickel was plated onto aluminium alloys as a barrier layer. Adhesion of the nickel to the aluminium was therefore critical to the success of the product. As far as copper is concerned, I have only had limited experience of it and as far as I know it is not very common in the UK. It may be more widely used in the decorative sector, but I cannot be sure. However, where it is done, the copper must be either pyrophosphate or cyanide, otherwise the adhesion fails. The "trick" to getting the good adhesion we required was to use a very good cleaning and etching process coupled with desmutting.
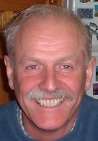
Trevor Crichton
R&D practical scientist
Chesham, Bucks, UK
2004
A. That is a huge sized grain structure to the aluminum. My guess is that it was excessively etched and either did not have a zincate step or had an improperly applied zincate. Note that there is virtually no visual indication of a bad zincate at that step. You tend to find out with a bend test or salt spray failure or some other destructive test. (or field failure)
James Watts- Navarre, Florida
2004
2004
Thanks again, Trevor, I had never even heard of that process, while seeing numerous examples of what you apparently considered rare. I guess we're not quite a global village yet after all :-)
Good point, Jim. I didn't see what I was looking at.
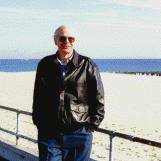
Ted Mooney, P.E.
Striving to live Aloha
finishing.com - Pine Beach, New Jersey
A. Vincent,
My first recommendation: What I can see from the photo is there is a corrosion contamination from the zincate hydroxide. Make an analysis of the white powder to see if it a contamination of the zincate. If the contamination is from the zincate, I recommend you change the copper strike to electroless nickel, "not alkali nickel strike".
Second: If all treatments and plating parameters are right make sure you get into the copper solution with pre-contact "entry with the current on".
Regards,
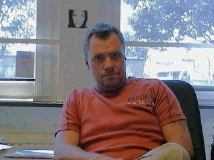
Anders Sundman
4th Generation Surface Engineering
Consultant - Arvika,
Sweden
2004
A. Vincent, plating onto aluminum is a complex process. Correct preparation of aluminum parts before cyanide copper strike is very important. I think that your problem is the zinc layer? -- contamination in the zincate.
Ted, we plated zincated aluminum. Instead of the cyanide copper we used the electrolytic nickel bath. We have success with this nickel strike. The layer on aluminum has very good adhesion and heat resistance. I suppose that Trevor thought about this nickel strike.
Regards,
Waldemar Tomankiewiczmetal finishing - Cracow, Poland
2004
A. Agree with all the comments so far, but would point out that conditions in Sydney (it's a very large in area city) can vary from coastal with salt spray to dry and hot if you go 30 miles west. We do a lot of plating on aluminum for electrical power applications and always use an electroless nickel strike prior to bright nickel plating (and subsequent tin plating) and our products are in all weather conditions around the east coast of Australia. Suggest that both cleaning and copper (specially if it was cyanide copper) could be the problem.
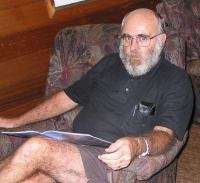
Bob Lynch
plating company - Sydney, Australia
2004
2004
A. Lots of good comments. I'll bet the plater believes the fallacy "If a little is good, more is better." Problem appears to be over-etching and over-zincating. Zincate solution thus can become trapped in the thick porous zincate, within over-etched aluminum grain boundaries and around non-etched intermetallics. Corrosion from this highly caustic solution lifts off subsequent plating. Useful reading for all platers is the article "Adhesion of Electroless Nickel Deposits to Aluminum Alloys" by Don Baudrand of Macdermid, available at https://www.pfonline.com/articles/079906.html
Reduce the durations of etching and the second zincate. An ambient temperature alkaline (pH 9) electroless nickel strike is good, and prevents zinc contamination of subsequent plating solutions.
Finally, institute quality controls, e.g., bend testing for adhesion and salt spray testing as suggested by Mr. Watts to verify correct processing and avoid shipping defective parts to customers.
- Goleta, California

Rest in peace, Ken. Thank you for your hard work which the finishing world, and we at finishing.com, continue to benefit from.
2004
A. Dear Vincent,
We plate 100,000's of M2 each year in China using the following method.
Non etch soak clean.
Etch.
De-smut.
Zincate.
Nitric acid zincate strip.
Zincate.
Watts type Ni strike (with live current entry).
Acid copper....etc.
If you need help, see your chemical supplier. If they can't help you, then find a supplier who can. This is not a difficult process.
Regards,
Jonathan Timmschemical supplier - Hong Kong
Q. Hi,
I'm an engineer with a solar company experimenting with the replacement of copper busbars with aluminum. For the busbars to work, they need to be electrically conductive, solderable, and ideally should be corrosion-resistant to boot.
From the discussion here, I'm a bit confused as to whether the zincated aluminum must be electroplated with copper before it is electroplated (or electroless plated) with nickel.
Would anybody here know the answer to this? And even more helpful, could somebody contrast the advantages and drawbacks of using the copper layer as a base for the nickel layer compared with simply plating nickel directly on the zinc? As a solar company, one of our biggest concerns is cost, and if we could make an equally reliable busbar with one less plating step (i.e. assuming the reduction in steps reduces cost), we would do so.
Thank you! I apologize in advance if this question is nonsensical or uses the wrong terminology, as I am new to the world of plating.
- San Jose, California, USA
December 11, 2012
A. Hi, Roger. I think the jury came in while I was out to lunch: apparently cyanide copper on zincate is no longer considered the right way to go. For maximum corrosion resistance, do alkaline electroless nickel plating on the zincate. But electrolytic nickel on the zincate would be significantly less expensive if these are large bus bars.
One more thought to muddy the waters: Atotech for many years promoted their Alstan process for aluminum bus bars. You might speak to them about whether that process is still viable. As I recall, the trade name implied "all tin", and there was no zincate -- stannate substituted for it. I can't recall whether the other step was copper plating or tin plating, but G.E. and others made countless miles of busbar with the Alstan process.
Regards,
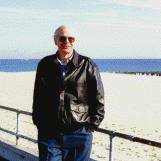
Ted Mooney, P.E.
Striving to live Aloha
finishing.com - Pine Beach, New Jersey
December 13, 2012
A. Hi Roger
Just a thought. Both zincate and electroless processes require good chemical control and some skill to achieve consistent results.
Aluminium can be both welded and soldered - using the correct solder and flux; standard solders intended for copper will not work. For corrosion resistance you could then Alochrom (or possibly anodise) and paint. Overall a much simpler process.
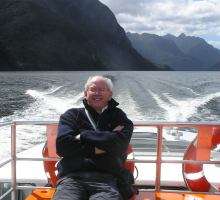
Geoff Smith
Hampshire, England
First of two simultaneous responses -- December 14, 2012
A. Years ago, we successfully plated aluminum with zincate-copper-and Watts nickel. It was extremely sensitive to blistering or peeling at the copper-zincate layer. A relatively low pH, low efficiency Rochelle cyanide copper strike was used. It was necessary to enter the bath with current on or it would peel.
The temperature, and immersion time in the immersion zincate bath was also very sensitive. We had to cool the bath in summer and heat it in winter to maintain 70-72 degrees °F at all times in order to get consistent good results.
I agree with Ted, that an alternative process may be preferable to this one.
consultant - Cleveland Heights, Ohio
Second of two simultaneous responses -- December 14, 2012
A. Electroless nickel is the best step following zincate. You can start with an alkaline electroless as Ted recommended, followed by a regular electroless, pH approx. 4.7.
The alkaline electroless is not a must, it is used mainly to extend the MTO of the regular EN.
As for electrolytic Nickel - a cyanide rochelle type copper with almost no free cyanide is a must prior to the electrolytic nickel.
I certainly would go for the EN.
But the deposit is the end of the process. The most important phase is the preplating prior to the zincate. It is complicated and is a delicate process.


Sara Michaeli
Tel-Aviv-Yafo, Israel
January 2, 2013
Nickel plating peel off aluminum part
Q. Dear Sir,
We have produced Bright Nickel plating with bright chrome plating top coat in Aluminum part,The part is used in Horn front side, After three month the plating fully removed in Aluminum part by using (car).
Please suggest why it has happened and what type of corrective action we should take to solve the issues.
Your immediate action in this regard highly appreciated.
Regards,
- Coimbatore,Tamil nadu, India
November 27, 2013
A. Hi Raja. As you see from the previous discussion, there are several different approaches to nickel plating on aluminum, but all are sensitive to operating conditions. If you can provide data about what you did, readers may be able to point out weak spots in the process. Good luck.
Regards,
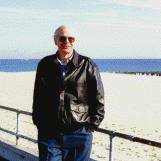
Ted Mooney, P.E.
Striving to live Aloha
finishing.com - Pine Beach, New Jersey
November 2013
Q, A, or Comment on THIS thread -or- Start a NEW Thread