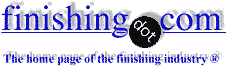
-----
Equivalent to QQ-P-35 spec for passivation of stainless steel? ASTM A967?
Q. I am a mechanical engineer trying to address a surface treatment problem. We are currently using the mil spec QQ-P-35C (canceled) [link is to free spec at Defense Logistics Agency, dla.mil] C type II to passivate our 416 SS. However, I have heard from one cleaning place that the ASTM standard ASTM A967 has replaced the MIL spec. Can anyone give me some insight as to what the differences between them are and how it affects me? Also, if the spec we are calling out is not compatible with our material, can someone suggest one to replace it?
Thank you.
Pam
Santa Clara, California
2000
A. Dear Pam,
Unless you would like to possibly destroy parts you must investigate the ASTM spec. Look at finishing.com's FAQ on passivation of stainless steel and you will learn from the experts in the field...suffice to say that I saved myself a lot of grief by going with the ASTM spec.
I don't know if you are a job shop, or a captive shop, and as you will see from the write-ins on the FAQ...it makes a lot of difference. I don't know where your alloys are purchased from, and that makes a huge difference too. Please pay particular attention to the section on tooling changes (frequency) and how they can affect the surface composition of the alloy, and the necessity for sufficient cleaning time (up to 40-60 minutes) to remove all possible oil contamination from your parts. The very characteristics that make for free-machining stainless alloys (is it 416se?) also tends to trap oils. If you have the opportunity to extend your "process improvement technology a.k.a. Deming" to your supplier, or to the manufacturing side of your operation, you may be able to minimize the possible negative effects of overheating due to infrequent tooling changes. Selecting the best possible lubricating solution (that won't impregnate itself into the alloying constituents of your alloy) will help. Ensuring that what you bought (in terms of alloy) is what you really got, is also important. If I were you, I would do some very rigorous multiple-factor variance analysis coupled with copper indicator solution tests, as well as appropriate salt spray and other testing (re: appropriate ASTM specs).
Going from nitric to either citric-based or phosphoric acid solutions would be real advantageous. In fact, if your parts are expensive, investigate electropolishing in phosphoric acid solution. I spoke to ASTM people who were responsible for drafting the spec. Though they wouldn't directly admit it, (or accept any liability for it) they were in effect saying that the reason they drafted the spec. was to encourage and in effect justify what medical equipment and other manufacturers had effectively discovered for themselves: nitric is way too dicey, QC of stainless alloys too problematic, and consistent QA of machining processes (re: bit changes and lubrication) not possible in the job-shop world. Again, I refer you to the excellent compilation of passivation problems covered by finishing.com's FAQ on the subject at their web-site. Good luck, and here's hoping you can get the nitric out of your shop!
Spokane, Washington
2000
Multiple threads merged: please forgive chronology errors and repetition 🙂
Status of QQP-35C?
Q. Can anyone clarify the status of QQ-P-35C [from DLA] ? Has it been discontinued or has it been reinstated? Does ASTM A967 take its place in all applications? Thanks for your help!
Victor Waldman- Naugatuck, Connecticut
2002
A. Victor:
QQ-P-35C has been cancelled in favor of ASTM A967 except for aerospace use. For aerospace you must use the AMS specifications AMSQQP35
[canceled] (nitric only) or AMS2700 (nitric or citric).
Many aerospace customers have tested the proprietary citric acid formulations and found them to be better than nitric, so they are switching over. Hopefully we will only have the AMSQQP35
[canceled]C canceled soon, also.
Let us know if you need details.
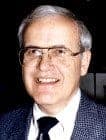

Lee Kremer
Stellar Solutions, Inc.

McHenry, Illinois
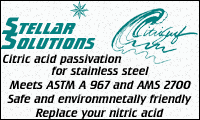
2002
A. ASTM A967 is listed as the replacement for QQ-P-35 Rev. C, so I would think it would be for all cases.
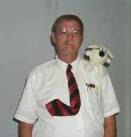
James Totter, CEF
- Tallahassee, Florida
2002
Q. Can anyone tell me what the recipe is for QQ-P-35 (nitric acid only) and the passivation temperature.
Thanks.
- Manchester, UK
2004
Why use AMSQQP35 [canceled] for aerospace instead of ASTM A967?
Q. Due to the canceling of QQ P 35 two alternatives were given, does anyone know the reason for using AMS QQ-P-35C (canceled) [link is to free spec at Defense Logistics Agency, dla.mil] for aerospace instead of ASTM A967-99? I guess what I'm asking is what is the difference between the two specs?
James GearyQuality manager - Dublin, Santry, Ireland
2004
Equivalent to QQ-P-35 TYPE IV (Type 4)
Q. I work with a great deal of military specifications that call out the QQ-P-35C [from DLA] specification for passivating 303 SS. I know that the specification has been replaced, however, many of the contracts still call out the TYPE IV (4) method of passivation, as well as require a 48 hour salt spray with no base metal corrosion. We have on occasion met with some specification issues in using new suppliers on our old product that specifies the TYPE IV. We're told the spec. and type are obsolete, but there has been no information provided as to an equivalent for the method. Do either of the replacement specifications, ASTM or the AMS, list an equivalent for the Type IV and will hold up to a 48 hour salt spray?
Armando HuezoDesign Engineer - Wood Dale, Illinois, USA
2004
A. QQ-P35C states Type IV solution has been withdrawn; see Table II for guidance. For 303 SS, Table II specifies Type II passivation solution (warm nitric acid + sodium dichromate). This solution is available in both QQ-P-35C (canceled) [link is to free spec at Defense Logistics Agency, dla.mil] and ASTM A967. The passivation of 303 SS can be problematic (pitting/frosting and early rusting), and a lengthier A-A-A (alkaline-acid-alkaline) procedure has been recommended since at least 1973. See letters 20840, 17774 and 639 as well as the FAQ: Problems with Passivation of Stainless Steel. AISI 303 is merely a composition. The passivation properties and corrosion resistance of 303 SS are greatly affected by the distribution and morphology of the MnS inclusions. Stringers are far worse than nodules. For salt spray requirements, I suggest using SS from well-known suppliers experienced in controlling these inclusions, such as Carpenter Technologies, Colt Industries, Jones & Laughlin, US Steel, BHP (Australia), British Steel, Dominion Foundries and Steel, Kawasaki Steel, Nippon Kokan, Sandvik AB, or Ugine Aciers. These companies published research results in the book Sulfide Inclusions in Steel (1975), and are not necessarily current SS producers.
Ken Vlach [deceased]- Goleta, California

Rest in peace, Ken. Thank you for your hard work which the finishing world, and we at finishing.com, continue to benefit from.
2004
A. Armando,
AMS2700 (which will eventually replace a to-be-cancelled AMSQQP35
[canceled]) does have the olde type IV listed.

Lee Gearhart
metallurgist - E. Aurora, New York
2004
Multiple threads merged: please forgive chronology errors and repetition 🙂
QQ-P-35 Compared to ASTM A967
Q. I recently sourced out a 302 stainless steel spring from a local supplier. As with all stainless steel medical instrument components, I specified a passivated finish... ASTM A967. Upon receipt of my spring component specification, the supplier contacted me and disclosed that their off-the-shelf spring was not typically provided in a passivated condition however a custom spring passivated to QQ-P-35C (canceled) [link is to free spec at Defense Logistics Agency, dla.mil] Type VI specification could be obtained. Is QQ-P-35 Type VI more appropriate than ASTM A967 for this application? If not, could I purchase the off-the-shelf 302 spring component and post-passivate to ASTM A967?
Chris CampbellManufacturer of medical instruments and implants - San Diego, California
2004
A. Chris:
Not all stainless steel springs are passivated by the manufacturers, although it certainly would be advised if it is going into any kind of humid or corrosive atmosphere. We supply formulations to many of the spring manufacturers around the world for this purpose.
QQ-P-35C has been canceled in favor of ASTM A967 for all passivation except aerospace, which should use AMS2700. The passivation specification for nitric in ASTM A967 is IDENTICAL to the now defunct QQ-P spec. In addition it allows the improved passivation using citric formulations. There is no longer the need to passivate using the hazardous nitric systems, although passivation with nitric acid is certainly acceptable.
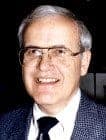

Lee Kremer
Stellar Solutions, Inc.

McHenry, Illinois
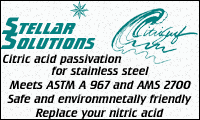
2004
PASSIVATE PER QQ-P-35, DICHROMATE SOLUTION PROHIBITED
Q. "PASSIVATE PER QQ-P-35C (canceled) [link is to free spec at Defense Logistics Agency, dla.mil], DICHROMATE SOLUTION PROHIBITED" -- WHAT TYPE SHOULD IT BE ON THE SPEC, IS IT TYPE II OR TYPE VI? WHAT'S THE DIFFERENCE BETWEEN THE TWO.
ART NOCHEMACHINING - ANAHEIM, California, USA
2004
A. If you cannot use sodium dichromate you cannot use Type II, you must use Type VI or another Type depending on the alloy.
adv.
If you cannot successfully use Type VI you can contact us with more information and we can tell you how to do it.
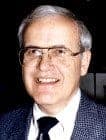

Lee Kremer
Stellar Solutions, Inc.

McHenry, Illinois
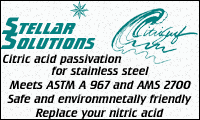
2004
Is QQ-P-35 compliant with RoHS
Q. Hi everyone,
I want to know if the QQ-P-35C (canceled) [link is to free spec at Defense Logistics Agency, dla.mil] is RoHS compliant ? Especially for type 2 which use sodium dichromate additive. Types 6, 7 and 8 seem to be RoHS compliant since they use only nitric acid solution.
I've contacted a supplier who suggested to me to use citric acid process as an alternative. Is there any other process which can replace the nitric acid?
Thank you
- Saint Laurent, Canada
2006
A. RoHS is concerned with what is on the part, not what chemicals the part may have been exposed to during its processing, Mohammed. I don't suspect that there will be sodium dichromate compounds on the parts you ship, although I hope to be corrected if someone believes otherwise. Good luck.
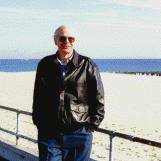
Ted Mooney, P.E.
Striving to live Aloha
finishing.com - Pine Beach, New Jersey
2006
QQ-P-35 Type Vl, better or worse than A967-05
Q. Hello ... I am a quality engineer working on root cause issue on a small stainless steel part that is required to be passivated. The industry standard has been changed and I don't know why. What is the technical difference on final finish between QQ-P-35C (canceled) [link is to free spec at Defense Logistics Agency, dla.mil] Type Vl and ASTM A967-05 (nitric 2) on 304 Stainless Steel for passivation? I didn't have any problems with the old QQ-P-35 process, but I have black residue on the parts with the newer process A 967-05. I didn't want to go back to school to figure this out. Help.
Dennis Ray Hensley- St. Louis, Missouri
2006
A. You're asking the wrong questions. The technical differences are slight and shouldn't affect 304 SS:
QQ-P-35C, Type VI: 25-45 vol% nitric acid for 30 minutes at 70-90 °F.
ASTM A967, Nitric 2: 20-45 vol% nitric acid for 30 minutes (minimum) at 70-90 °F.
Black residue could be carbide or machining residue, heat treat or weld scale inadequately removed, residual machining lubricant that reacted with the nitric, or some unusual contamination in the passivation solution.
Verify that the material is 304, not a higher carbon alloy.
Check the entire machining, cleaning and passivation process.
- Goleta, California

Rest in peace, Ken. Thank you for your hard work which the finishing world, and we at finishing.com, continue to benefit from.
2006
A. Yes, much of A967 is copied fairly directly from QQP-35C. The major change was the addition of citric acid based passivation as an alternative to the nitric and nitric/dichromate.
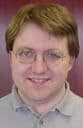
Ray Kremer
Stellar Solutions, Inc.

McHenry, Illinois
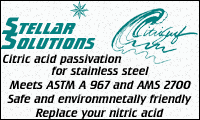
2006
Q. Dear Sir,
If customer specifies process the part Passivation as per QQ-P-35B Type-I and QQ-P-35B Type-IV ,which standard we can use for that?
Please advice for QQ-P-35B Type-I and QQ-P-35B Type-IV
plating shop employee - Bangalore,KARNATAKA, India
December 12, 2014
Hi Sanjeev.
My read of cancelled QQ-P-35 is that if your customer is the American military/DoD, you might be able to automatically use ASTM A967, except for aerospace parts which must be done to AMS2700; but if the parts are destined elsewhere you must get spec replacement orders from your customer.
Regards,
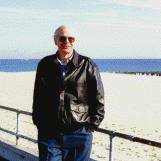
Ted Mooney, P.E.
Striving to live Aloha
finishing.com - Pine Beach, New Jersey
A. Wow, QQ-P-35 Revision B! That's impressive. Revision C was released in 1988, and then QQ-P-35 was canceled ten years later as Ted mentioned. Your customer is over 25 years out of date! Revision B is so old, the US government's "ASSIST" mil spec site doesn't even have a copy.
Just to review various things:
The Type I and Type IV baths in fact were removed in revision C, which had only Type II, VI, VII, and VIII. The ASTM replacement for QQ-P-35, A967, renumbers these to Nitric 1, 2, 3, and 4. SAE's replacement for QQ-P-35, AMS2700, brought back all the removed baths and lists them as Method 1, Type 1-8.
ASTM A967 also has a Citric section, and AMS 2700 has citric as Method 2.
Officially, only DoD users are compelled to the automatic rollover from QQ-P-35 to the two newer standards. Everybody else ought to anyway, though. It's not as though there's a substantial difference, the new standards were specifically designed to keep the text of QQ-P-35 largely intact.
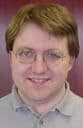
Ray Kremer
Stellar Solutions, Inc.

McHenry, Illinois
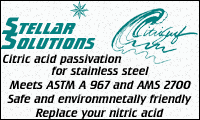
December 12, 2014
Q. Hello,
Thanks for your response.
I have another query regarding, whether QQ-P-35 Type- 1,2,3,_,_,_,_,8 are equivalent to AMS 2700E Type- 1,2,3,_,_,_,_,8 ?
Ex: If customer specifies QQ-P-35, Type-I, Can we consider the process according to AMS 2700E, Type-I?
Please advice.
Regards,
- Bangalore, Karnataka, India
December 15, 2014
A. Hi Sanjeev. Yes, Ray implies that that is the case. However, you cannot substitute one spec for another except with your customer's approval. And don't even think about claiming to be plating to a spec unless a copy of that spec is in your hands :-)
Regards,
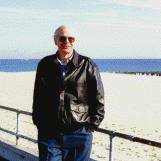
Ted Mooney, P.E.
Striving to live Aloha
finishing.com - Pine Beach, New Jersey
December 2014
Q, A, or Comment on THIS thread -or- Start a NEW Thread