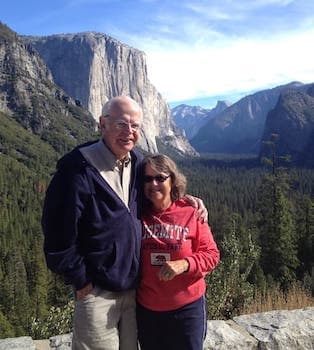
Curated with aloha by
Ted Mooney, P.E. RET
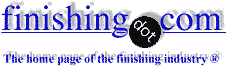
The authoritative public forum
for Metal Finishing 1989-2025
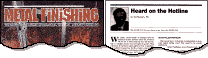
-----
Passivation of 303 stainless steel
1996
Q. I came across a message from Anne Baic, posted 02/25/91 regarding reaction in passivation of CRES. I am currently experiencing the same phenomena which she described on the 303 stainless steel.
Twice now we have smoked the same part for the same customer, while we have had no problem running other 303 stainless steel. We are also using the 25% Nitric acid bath with 2% by weight Sodium Dichromate per QQ-P-35C (canceled) [link is to free spec at Defense Logistics Agency, dla.mil] type II bath.
Reaction that occurs begins with a gassing on the surface and a distinct odor of sulfur. I do know that sulfur is added to the material to make it a "free Machining alloy", and this where the odor originates.
You can see the intergranular attack that results from this firing off phenomena. I have seen special passivation procedures from Carpenter Steel on the passivation of 303 & 400 series alloys, but no one has been able to tell me what conditions will cause this problem, or what actual mechanism is taking place in this reaction.
Do you have any further information on this phenomena?
THANKS,
JOHN
plating shop - San Jose, California
A. Hi Juan. We've now built a FAQ on Passivation of Stainless Steel which you may find interesting, Juan. Good luck.
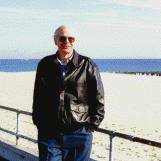
Ted Mooney, P.E.
Striving to live Aloha
finishing.com - Pine Beach, New Jersey
1996
1996
A. It would be impossible to diagnose your problem unless we were able to have one of the pieces prior to processing for examination.
I would not look too much further than the customer that you are passivating the 303 stainless job for answers to this problem. What's done is done and you cannot change the outcome. What you could do on future lots is as follows:
What we have done to correct a similar passivating problem, is to ask the customer to supply one or two pieces of the suspect alloy that has not been machined to the final dimensions; but is of the same alloy and heat treatment to use as a test vehicle!
1. The test consists of close examination of the material under approximately 20x magnification.
2. Cleaning of the parts and reexamination under 20x magnification for any problem that may be evident prior to passivation.
3. Removal of enough solution from the intended passivating bath to passivate the parts - in a test vat in case of a problem.
4. This method has not failed to warn us of an impending passivation problem and save a passivation solution as a bonus.
5. If you are not satisfied with the above method, then take one piece of the actual lot of parts and repeat the procedure above.
We have had enough strange occurrences in the passivation bath, that has alerted us to proceed with extreme caution on a new part and complete customer involvement on a troublesome part. This has been very beneficial in eliminating passivation sporadic unexplained attacks.
Joseph Hillockanodizing shop - Philadelphia, Pennsylvania
A. Sir, I am not sure that I would call it an Intergranular attack, more like a chemical destruction of the part. It does, attack the grain boundaries in most cases. Joe's comment of running a test part is certainly the way to go.
I do not remember ever having a chemical attack on 304 or 316, but 303 and 303 free cutting have caused the problem you had. I have had the customer swear that it was from the same lot number of one that worked fine. 300 series is not heat treatable, but I think that the increased attack has to to with the grain structure , which is controlled by its exposure to heat. I have tried numerous pretreatments and have used lab grade chemicals to make a beaker of solution and it still was attacked. One thing that I never tried, was pre-baking them. A real metallurgist would have to tell you the proper temp. It could be quite high.
Our customers would call it free cutting and frequently could not tell us what it really was. The 303Se caused the greatest pain. As I remember, most 303 does not have sulfur in it. The 0.05 molly in it should make it more attack resistant than 302, but I do not remember any problem with 302.
Different subject, but wait till you try to pass salt spray or copper sulphate ⇦ this on eBay or Amazon [affil links] testing on 316 that the customer has polished with a 410 wire wheel. 24 hours in the acid would not do it.
James Watts- Navarre, Florida
1996
A. A similar problem occurs in the electropolishing of sulfur-bearing alloys. The gassing is caused by interaction between the acid and the sulfide residues in the alloy. In electropolishing, the reaction is violent enough to cause pitting. We have some excellent photos of the result, taken under magnification of about 50X, 200X, and 1000X.
We agree with Joe Hillock that the problem lies with the selection of the alloy by the manufacturer of the parts. We would suggest that you contact Norman Schmidt at Carpenter Technology in Reading, PA, and get some literature on SCQ stainless steels to send to your customer. Use of a new alloy might very well cause a change in the manufacturing techniques, but if the problem is big enough, the part manufacturer should learn how to solve it.
Contact us if we can offer further assistance.
Ed BayhaMetal Coating Process Corporation - Charlotte, North Carolina
1996
A. Hi Guys,
The intergranular attack of 300 series SS in the nitric acid and dichromate solutions may be caused by segregation of sulfur at grain boundaries due to inadequate heat treatment. The passivating agent consisting of nitric acid and dichromate is the oxidizing agent strong enough to oxidize sulfur at grain boundaries into sulfur dioxide which is one of gases observed at the sample surface. Gases occurring at the surface also contain nitrogen monoxide and nitrogen dioxide which both are the products resulting from the reduction of nitric acid. It is because of sulfur oxidation and high tensile stress arising from the sulfur dioxide produced that intergranular attack develops. Furthermore, as we all know, the reduction of nitric acid is an autocatalytic process. This accelerates the intergranular attack.
Ling Hao- Grand Rapids, Michigan
1997
A. The problem with the passivation may have to do with the size distribution of the sulfide inclusions in these parts. The free-machining character of 303 SS is due to presence of manganese sulfide inclusions formed from the high sulfur content (<0.15% for 303 compared to >0.03 % for 304). The size and shape of the sulfide inclusions will depend on the actual sulfur content and the processing of the steel. If the inclusions in one batch are larger than the next batch, different behaviors could be obtained in the passivation bath. I have seen some extreme variation in the inclusion size and frequency in otherwise similar stainless steel products.
A second alternative may be a chemical contamination from prior processing held by these inclusions. The large inclusions in 303 can create "pockets" in the surface that hold machining fluids or other chemicals to which the parts have been exposed in process.
I would check with your customer to find out about all prior processing. The inclusion morphology can be checked by a metallurgical evaluation. I doubt that heat treating is a factor in this case - neither inclusion size and shape nor the sulfur distribution will be affected by heat treatment.
The previous suggestion to do test batches is a good one. You may even be able to see the differences in the inclusions distribution on the part surface with a good stereo microscope.
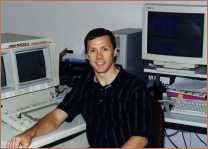
Larry Hanke
Minneapolis, Minnesota
1998
Q. We passivated some spring steel parts in our Type 6 passivation tank and they completely dissolved. Any ideas?
My plater cross referenced the material to 301 but I believe that is was either 302 or 304.
metal finishing - Washington
September 18, 2013
A. Holly,
I assume you are referring to Nitric type 6 in either QQ-P-35C (canceled) [link is to free spec at Defense Logistics Agency, dla.mil] or AMS2700. If you check the treatment table in either, type 6 is acceptable for 301, 302, and 304. Are you certain the steel you are using matches one of these grades and that the recommended process time was followed? Are these springs very small or thin, perhaps?
You should have generally less trouble with parts getting etched or dissolving if you use citric acid based passivation, is that a possibility for you?
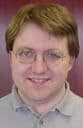
Ray Kremer
Stellar Solutions, Inc.

McHenry, Illinois
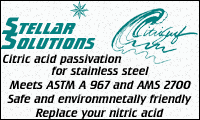
September 24, 2013
Pickling inox 303
Q.
I have a passive stainless steel 303 order with ASTM A967 type II, we make descaling in 15% HNO3 + 1% HF, then passive in 40% HNO3. The resulting product is black, losing its brightness. Show me how to fix it
student - ho chi minh city, vietnam
December 16, 2018
A. Tan Hoang,
I think there may be some confusion here. "Type II" from QQ-P-35 would be a correct treatment for grade 303. This is 20-25% nitric with 2.5% sodium dichromate added.
ASTM A967 refers to this as "Nitric 1". If you are using "Nitric 2" from ASTM A967 (20-45% nitric), then it is the wrong bath mixture for 303.
303 also generally works well in the citric acid treatments if preceded by a hydroxide bath treatment to remove the sulfur from the surface.
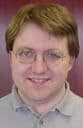
Ray Kremer
Stellar Solutions, Inc.

McHenry, Illinois
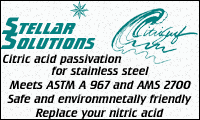
December 20, 2018
----
Ed. note, Feb. 2015: Readers may also be interested in letter no. 20840, "303 Stainless Steel Passivation Problem".
Q, A, or Comment on THIS thread -or- Start a NEW Thread