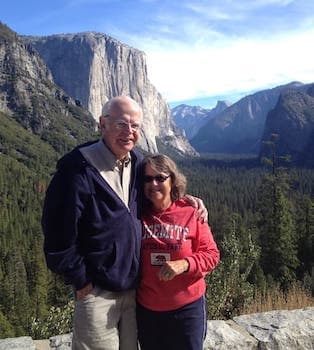
Curated with aloha by
Ted Mooney, P.E. RET
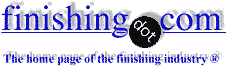
FAQ: Problems with Passivation of Stainless Steel
The passivation of stainless steel is problematical. Little reference to it is found in many of the industry's 'must have' books, such as The Canning Handbook [on
eBay,
Amazon,
AbeBooks affil links], the Electroplating Engineering Handbook ⇦ this on
eBay,
AbeBooks, or
Amazon [affil links]
, the Metal Finishing Guidebook and Directory, The Properties of Electrodeposited Metals and Alloys by Safranek, or the Products Finishing Directory.
But there are a few references in the printed literature:
- A couple of pages of theory and recipes can be found in 'ASM Metals Handbook Volume 5: Surface Engineering'.
- The February 1988 issue of Metal Finishing magazine has an article by D.K. Verma entitled "Surface Preparation of AISI 400 Series Stainless Steel Components".
- Specifications QQ-P-35C (canceled) [link is to free spec at Defense Logistics Agency, dla.mil], ASTM A967, and AMS2700
on passivation of stainless steel. - Dozens of references in the "Shop Problems" column of Metal Finishing magazine (including a very interesting one in the December '96 issue), and the "Plating Clinic" column in Products Finishing magazine over the years, as well as a few in the similar troubleshooting columns in Industrial Finishing magazine and Plating & Surface Finishing.
Some of the contributions by the magazine columnists are quite interesting, revealing that part of the problem is that people don't 100% agree on why passivation is done, or its basic function!
- For example, columnist William Snyder ,writing in the May '82 Plating/Anodizing Forum in Industrial Finishing says: "Remember that the intent of passivation and its precleaning is to remove any trace of carbon steel . . ."
- But by the March '83 issue he was saying: "Over the years, people have talked about passivation as a process that removes ferrous contamination from stainless steel parts; it doesn't. . . Thousands of dollars are wasted every month by manufacturers going through complete passivation cycles when all they need is proper cleaning . . ."
For sure the questions are going to continue. So don't be reluctant to contribute your experience. And don't be embarrassed if your experience hasn't been too hot. Because if you have destroyed parts in attempting to passivate them, you are a member of a very large club. People around the world have been smoking parts left and right!
However, due to the generous disclosures of a number of people who contributed to our letters page, there is a lot to be learned right here. Here is an edited version of letters that have appeared here--
Passivation of 440A Castings
(1990)
... we have difficulty passivating a 440A casting. I suspect our problems are caused by inhomogeneities in the castings... the parts are 440A in the solution heat treated condition. The passivation process is 50% nitric at 140-150 °F for 30 minutes. Every now and then we have to repassivate parts that were remachined. These parts are in the hardened condition (quenched and tempered) and they rust within a few hours of passivation. The as-cast surfaces rust worse but the machined surfaces rust also.
ANNE BAIC
(1990)
ASM's Volume 5 "Surface Cleaning, Finishing & Coating" of the Metals Handbook, from American Society for Metals, Metals Park, Ohio 44073 is a great reference book. From my reading of it, the first possibility is that you haven't properly cleaned the parts after machining and the oil is preventing proper passivation.
TED MOONEY
Reaction in Passivation of CRES
(1991)
We are doing passivation of stainless steel per QQ-P-35 using Type II (25% Nitric with 2% dichromate at 120-130 °F). Once in a while we come across a batch of parts which for some unknown reason react with the bath. We have smelly fumes, fizzing of parts and etching, usually resulting in ruined parts because critical dimensions are lost. It has happened twice on 416 and last week on 303 CRES, which to me is the easiest stuff in the world to passivate. What am I doing wrong? The thing which complicates the matter is that the condition is not repeatable: The same parts which reacted the first time will react again, but the bar stock they were cut from will react one day and not the next, other parts from the same bar may or may not react, and the bath operates fine with all other parts, including parts in the same BASKET as the ones which react!
The steel companies tell me there may be some surface phenomenon going on, but they are unable to be specific or even to tell me how to prevent it.
ANNE BAIC
(1991)
Nitric acid is a very powerful oxidizing agent and thus will react very strongly with anything that is oxidizable: which would include organics still on the part, or a tramp metal such as aluminum.
TED MOONEY
(1996)
What is the proper procedure for passivating 400 series stainless steel? We occasionally experience etching of the material. This is especially a problem with heat-treated 440 series stainless.
Keith Rosenblum
(1996)
I have a job to treat passivate 416Se...I used 20% nitric acid and 2% dichromate mixing solution at room temperature. When I put the part in the solution,the part became black in not more than 30 sec. I don't know what happened. But many reference say that this solution can treat this type stainless steel.
Wen, Niann Tsyr
(1996)
416Se is a personal horror story. One lot worked beautifully. The next pitted, regardless how it was treated. We tried every pretreatment in the book, including glass bead blasting and running the material through the rinse tanks after the passivate tank in reverse order before going into the passivate tank. Nothing worked. I personally think that it had to do with the hardness of the material. The customer swore it was made from the same material lot. If you have not done much passivation, always run a "rabbit". This is a part or a few parts that precede the main batch. This will tell you if there is a problem and save spoiling an entire lot. 400 series will cause you more problem than others and any time it has a suffix like Se, you can expect trouble, more than if it does not.
James Watts
(1996)
I agree with James. 400 series is a nightmare, especially if the part is heat-treated. We have found that parts are less likely to etch with a new passivate solution than with an old one, although a new solution certainly has not guaranteed us the absence of problems. If you are passivating for cleaning purposes only and not for a specification, maybe you can clean the parts in a caustic cleaner only and avoid the passivation solution?
Keith Rosenblum
ECO Finishing
Passivation of 303 stainless steel
(1996)
I came across a message #1619 from Anne Baic, posted 02/25/91 regarding reaction in passivation of CRES. I am currently experiencing the same phenomena which she described on the 303 stainless steel.
Twice now we have smoked the same part for the same customer, while we have had no problem running other 303 stainless steel. We are also using the 25% Nitric acid bath with 2% by weight Sodium Dichromate per QQ-P-35 type II bath.
Reaction that occurs begins with a gassing on the surface and a distinct odor of sulfur. I do know that sulfur is added to the material to make it a "free Machining alloy", and this where the odor originates.
You can see the intergranular attack that results from this firing off phenomena. I have seen special passivation procedures from Carpenter Steel on the passivation of 303 & 400 series alloys, but no one has been able to tell me what conditions will cause this problem, or what actual mechanism is taking place in this reaction.
Do you have any further information on this phenomena?
JUAN OCAMPO
(1996)
What we have done to correct a similar passivating problem, is to ask the customer to supply one or two pieces of the suspect alloy that has not been machined to the final dimensions; but is of the same alloy and heat treatment to use as a test vehicle!
1. The test consists of close examination of the material under approximately 20x magnification.
2. Cleaning of the parts and reexamination under 20x magnification for any problem that may be evident prior to passivation.
3. Removal of enough solution from the intended passivating bath to passivate the parts - in a test vat in case of a problem.
4. This method has not failed to warn us of an impending passivation problem and save a passivation solution as a bonus.
5. If you are not satisfied with the above method, then take one piece of the actual lot of parts and repeat the procedure above.
We have had enough strange occurrences in the passivation bath, that has alerted us to proceed with extreme caution on a new part and complete customer involvement on a troublesome part. This has been very beneficial in eliminating passivation sporadic unexplained attacks.
Joseph Hillock
(1996)
I am not sure that I would call it an Intergranular attack, more like a chemical destruction of the part. It does, attack the grain boundaries in most cases. Joe's comment about running a test part is certainly the way to go.
I do not remember ever having a chemical attack on 304 or 316, but 303 and 303 free cutting have caused the problem you had. I have had the customer swear that it was from the same lot number as one that worked fine. 300 series is not heat treatable, but I think that the increased attack has to to with the grain structure, which is controlled by its exposure to heat. I have tried numerous pretreatments and have used lab grade chemicals to make a beaker of solution and it still was attacked.
Our customers would call it free cutting and frequently could not tell us what it really was. The 303Se caused the greatest pain. As I remember, most 303 does not have sulfur in it. The 0.05 molly in it should make it more attack-resistant than 302, but I do not remember any problem with 302.
James Watts
(1996)
A similar problem occurs in the electropolishing of sulfur-bearing alloys. The gassing is caused by interaction between the acid and the sulfide residues in the alloy. In electropolishing, the reaction is violent enough to cause pitting. We have some excellent photos of the result, taken under magnification of about 50X, 200X, and 1000X. We agree with Joe Hillock that the problem lies with the selection of the alloy by the manufacturer of the parts.
Ed Bayha
Metal Coating Process Corporation
(1997)
The intergranular attack of 300 series SST in the nitric acid and dichromate solutions may be caused by segregation of sulfur at grain boundaries due to inadequate heat treatment. The passivating agent, consisting of nitric acid and dichromate, is an oxidizing agent strong enough to oxidize sulfur at grain boundaries into sulfur dioxide which is one of gases observed at the sample surface. Gases occurring at the surface also contain nitrogen monoxide and nitrogen dioxide which both are products resulting from the reduction of nitric acid. It is because of sulfur oxidation and high tensile stress arising from the sulfur dioxide produced, that intergranular attack develops. Furthermore, the reduction of nitric acid is an autocatalytic process. This accelerates the intergranular attack.
Ling Hao
Coatings 85
Ed. note: The following response was the winner of finishing.com's Best Letter 1995-1998 award--
A solution to a Stainless Steel Passivation problem
(1997)
In [Metal Finishing magazine "Heard On The Hotline" column] Vol 95 No.2, Feb. 1997 Anne Baic Reported a Problem found while attempting to passivate stainless steel. Other contributors concurred that they had experienced problems too, even with different types of stainless steel.
Reading the articles brought vivid memories of the same problem. I am the plating chemist at Robertshaw Controls. We were passivating 400 series SS that had been machined on a high speed lathe. The plating technicians had brought the problem to my attention and I tried all the standard investigations; temperature, concentrations, alloy check, impurity and cleanliness check, nothing explained the seemingly randomness of the vicious acid attack.
I am also responsible for Pickling operations and general metallurgy so I'm very experienced with the nature of acid reactions, and I have an extremely talented co-worker Reggie B. who knows machinability properties of stainless steels
He gave me the clue to solving this puzzle. I asked him what could be the difference between the good and bad sets of parts. He almost immediately suggested that grain structure, hardness, and surface profiles could be affected by the quality of the machine setup, the amount and the effectiveness of the cutting oil coolant, and the amount of wear on the cutting tools. Reggie explained that the part can get very hot and change hardness or in the case of a dull tool with plenty of cutting oil coolant,the surface can distort and the tool drags metal off instead of cutting it, thereby creating a distorted finish. I went to investigate the difference between different machines and took samples to test for microhardness and grain changes. In the MET lab I found no telltale hardness changes, but I noticed that the sectioned metal was hard to etch, I had to use a powerful etchant that is common to most metalurgists, a nitric - alcohol etch. The nitric acid by itself wouldn't etch the SS in a hundred years but I knew that the addition of a drop of alcohol, glycerol, or OIL would create a Organic acid that dissolve the part in seconds if allowed to remain in contact. - aha! The etchant reacted in the same way as the parts that were attacked by the 50-2-48 Nitric-Bichromate Solution. I took a sample of the cutting oil and mixed a drop of it with the passivation solution in a beaker at room temperature. The metal reacted vigorously, - all pieces, not just the problem lots. Thus I had a good clue as to the culprit - but still had one problem. The parts didn't look or feel oily, and they are alkaline washed just before the passivation process. I inspected the surface of the problem parts under the electron microscope and I found a very rough pitted surface, enough pores to cause a great problem in cleaning. The dull tool had not burnt or hardened the part but cutting oil was being trapped in the pores and being sealed into the surface.
I found that the length of time in the alkaline degreaser and vapor degreaser was proportional to the percent of good passivation lots. With a vapor degrease and a hot 4 hour alkaline soak we were able to save all of the lots, albeit this much time and effort was costly. The only real solution was to maintain tighter machining control and to change out tool bits more often. Reggie insists that the Tool bit regrinds helped contribute to the problem too. What an interesting challenge!
Mitchell G. Lee
Robertshaw Controls
(1997)
The passivity of stainless steels is attributable to a strongly adsorbed layer of oxygen. Sulfides (and probably Selenides) in acid media are even more strongly adsorbed, and destroy passivity by displacement of adsorbed oxygen. In the manufacture of TiO(2) by the sulphate process, I have observed that the presence of sulfide, in low ppm concentrations, causes activation and severe corrosion of SS316 in titanium/iron sulphate solution in which the alloy is normally completely passive.
A more curious example of this effect is a commercial household device which appears to remove the odor of onions and garlic from the hands. It consists of a stainless steel block shaped and used like a bar of soap.
Free-machining grades of stainless may respond more favorably to the alkaline-acid-alkaline procedure described in the ASM Metals Handbook Vol. 13 'CORROSION'
⇦[this on
Amazon affil links] p 552, as follows:
1) After degreasing, soak the parts for 30 minutes in 5% wt of sodium hydroxide (NaOH) at 70-80 °C (160-180 °F).
2) Water rinse.
3) Immerse the part for 30 minutes in 20 vol % HNO(3) + 22 gpl (3 oz/gal) Na2Cr2O7.2H2O at 50-60 °C (120-140 °F).
4) Water rinse.
5) Immerse for 30 minutes in 5 wt % NaOH at 70-80 °C (160-180 °F).
6) Water rinse.
Free machining grades should not be used in acidic environments without thorough testing, due to the internal passivity-destroying effects of sulfur or selenium.
David Hawke
Air passivation of stainless steel
(1998)
The FAQ on the wet chemical passivation of stainless steel was very interesting. The surface of stainless steel can be passivated by heating in air. However, the temperature and dew point are very important. A smooth oxide film is formed on 316L stainless steel at 450 °C and a dew point of â 0°C but small nodules and surface coarsening result when the oxidation is done above 550 °C in air with this dew point. These nodules can produce particulate contamination in gas distribution systems and the coarse oxide adsorbs water vapor more easily than does the smooth dense oxide. If the dew point of the air is lowered to -100 °C, then a smooth oxide with no nodules is formed at higher temperatures. For example a four hour oxidation of electropolished stainless steel at 550 °C and a dew point of -100 °C produces a 100-300 µ thick oxide compared to the 10-20 µ thick natural oxide found on the electropolished surface with no passivation treatment. Type 304 and 316 stainless steels are more easily passivated than are the 400 series (hardenable) stainless steels.
Don Mattox
2005
I was just surfing the net and came across many problems with the process of passivating 400 series stainless steel and I thought I would just give the web-page a suggestion. I actually came across the same problems mentioned on this page with a customer about 3 months ago. We started passivating 416 ss parts for one of my customers about a year ago and we used our standard process of 20-25% nitric acid for 30 min at 145 degrees. For 6 months everything went beautifully, however one day we passivated the same parts we were doing for months and within seconds the parts were destroyed. We investigated the problem and contacted the supplier of the stainless steel and could not find out a reason for this problem. So through trial and error I came up with a pretty good solution for passivation of 400 series stainless steel. The best process for us was to clean the parts in an alkaline cleaner (Luster OnCleaner 243S) for 25 min @ 125 degrees. After the alkaline process was completed we avoided using the nitric acid tanks and used our citric acid passivation line. We used a weak citric acid solution mixed only with deionized water. We passivated the 416 SS parts in the citric tanks for about 25 minutes at 110 degrees and the parts came out perfect. I just thought this might be helpful to your webpage.... It's only a suggestion and I can't guarantee the process will work for everyone but I know it works for us every time we get 400 series SS in for cleaning/passivating.
Sincerely,
Christopher Barnes
Scott Metal Finishing, VP
Bristol Connecticut
P.S. I have no problem with you using my name as long as I am not liable for anyone who uses this process and tries to come after me or you for using the process if a problem occurs.
If, in the course of editing these letters for our FAQs here, we have misquoted anyone, our apologies. We sincerely thank these contributors for making this page what we consider to be a valuable resource for those who have encountered etching and pitting in passivating stainless steel.