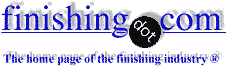
-----
Need Ductility in Nickel Electroplate

Q. We need to Nickel Electroplate some steel parts in a barrel process, to GM 4254M code 20 (5µm). The main concern is that the parts are then subjected to a crimping operation, where a flange on the piece is bent 180 degrees, and there cannot be any peeling of the deposit. The appearance has to be between a bright finish and a semi-bright finish.
The crimping operation or bending is very severe, as the thickness of the flange is considerable. We have been able to get good results only sometimes with a 2µm thickness.
Our Nickel bath is: Nickel sulphate 200 g/L; Nickel chloride 80 g/L; Nickel metal 51 g/L; Boric Acid 45 g/L. and pH of 4.0 to 4.2. Our brightener system is composed of two additives.
Can someone help?
1998
A. These problems are usually related to the amount of brightener present in the tank, but sometimes a review of your plating operation is necessary. You should be able to consistently pass this test, but give us more information on how you run the process. For instance, how and when do you add brightener, acid, wetting agent. How closely do you control temperature of processing solutions?
For your other work out of this line: Pick up two handfuls of the plated work and rub them together. Drop the parts. Do you see sparkles left in your hands? Then there is too much brightener for this crimping work.
Also see www.finishing.com's consultants directory.
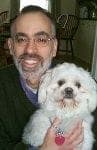

Tom Pullizzi
Falls Township, Pennsylvania
A. If ductility is what you are after then Nickel Sulfamate is the bath you need, Nickel from sulphate contains too much internal stress and will delaminate when worked. Also you can try Copper pre-plate under the Nickel layer. This stress-relieves the mismatch at the interface between the Nickel and steel.
Regards,
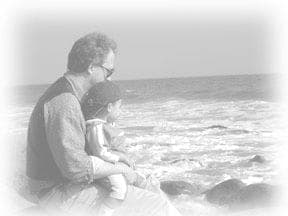
Dave Kinghorn
Chemical Engineer
SUNNYvale, California
Q. I want to thank Tom and Dave for your help.
I want to add the following, so that you understand better our problem;
Our line is a 6 barrel tank with 3,000 Liters.
We use a primary brightener at 35 to 40 ml/Lt.,added by analysis.
A maintenance brightener is added manually, first diluting 4 liters of brightener in 50 Liters of water, and from this mix, we add manually 200 ml. per barrel load when the barrel is first put into the tank. There are no wetting agents used. Once in a while we add a Booster by analysis or when more throwing power is needed.
The pH is controlled with Sulfuric acid diluted at 10% by volume.We regularly add at the beginning of the shift (checked with pH papers or strips) and if needed at half shift.
Temperature is controlled manually between 48 to 55 degrees C.
We just did a series of tests with a very severe pickling, to see if the problem was adhesion or ductility or the two. The first test was performed with a Chloridric Acid at 20% conc. for 15 minutes with an inhibitor and then an immersion in a hot activator (patented).
The second test was prepared the same way, but with a 5 minute cyanide copper plate.
The two tests came out very good, but the second was better.It only had very small peeling areas on the edge of the flange. There was some peeling but not as much as before.We had a 90% acceptance.
Can this info help ? Can it be only adhesion problems, or also ductility. We still need to improve the results and your help is greatly appreciated.
Thank you in advance.
Enrique Segovia [returning]A. Enrique,
Your particular plating application in Europe is done one way, and only one way:
NICKEL SULFAMATE!
Industrial Processing
1998
Q. Hi, Ray Delorey
Regarding the nickel sulfamate, is it a pure nickel sulfamate or mixing with certain amount of nickel sulphate or nickel chloride ? Any suppliers to recommend for trying ?
Thank you
- Singapore
February 24, 2023
A. Hi Chris,
Ray is probably neither reachable nor monitoring this site 25 years later, but we'll try his ancient e-mail address.
Sulfamate nickel is essentially nickel sulfamate, no nickel sulphate; but there may be a little chloride or bromide to assist in anode dissolution.
My understanding is that the nickel sulfamate process no longer has a champion, so you may have to buy pure salts rather than going to a proprietary process provider ... but, sorry, we can't suggest vendors or sources anyway ( huh? why?)
Luck & Regards,
Ted Mooney, P.E. RET
Striving to live Aloha
finishing.com - Pine Beach, New Jersey
Ted Mooney, P.E. RET,
Thank you so much for your reply.
- Singapore
March 6, 2023
Q. I want more information (a few words) about ductility please.
I am student (civil engr.), and I have an exercise about ductility.
Stavros BoutopoulosBoutos Bros Company - Greece
1998
A. This inquiry does not provide enough information to produce a simple answer and therefore will require a longer than usual reply. However, the inquiry does relate to one of my pet peeves. The assumption is made that because the nickel deposit is peeling it must be brittle. In reality, the assumption is at best only partially true. In my days, and there have been many, I have seen nickel deposits so brittle and stressed that they spontaneously crack but they can have good adherence. Conversely, I have seen fully ductile nickel deposits with poor adhesion. In simple terms, if the surface preparation is good, almost any nickel deposit will adhere. In the real world, however, it can be very broadly stated that brittle deposits are more sensitive to poor cleaning.
There are a number of suggestions that can be made to remedy the peeling problem in this inquiry depending on whether the peeling is 1) from the base metal only, 2) de-lamination or peeling of nickel from nickel, or 3) both circumstances. A few suggestions are as follows:
For case #1, assuming the soils have been removed, then the most likely culprit is the use of the wrong type of acid dip, the wrong concentration or an improper operating parameter. In short, the surface probably has residual oxides (either present initially or incipient), residual smuts or immersion films that can interfere with adhesion.
For case #2, many contaminants (organic or inorganic) can embrittle the deposit as can an overdose of brightening additives. The remedy here is to dummy the solution to the point where the deposit is semi-bright to dull. If the adhesion is still poor, look elsewhere. Don't settle for a simple improvement in adhesion using this procedure. The adhesion must either be good or it is bad. Ductile deposits may sometimes blister, rather than crack and peel, if the surface preparation is inadequate.
Case #3 is simply the presence of both conditions and deserves no further mention.
Another possibility not to be overlooked is the passivation of either the base material or the nickel deposit by the use of too high a current density, either in the electrocleaning or the plating operation. I suspect this possibility as the most likely culprit since most shops are trying to obtain the maximum number of loads in the shortest possible time. In many cases, the current in the barrel is simply too high for the load size.
Hydrogen embrittlement of the deposit can also occur during the plating operation, however, this circumstance can generally be checked by baking a part for hydrogen relief.
I've only listed what I consider to be the most likely causes of poor adhesion in a plating barrel. Obviously, there can be many other parameters contributing to poor adhesion such as the cleanliness of the cleaners, acids, rinses, etc.
Lou GianelosNice to hear from you, Lou. Thanks for the detailed reply!
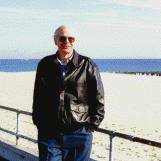
Ted Mooney, P.E.
Striving to live Aloha
finishing.com - Pine Beach, New Jersey
A. The question of ductility/adhesion on thick nickel deposits is always a matter of correct pre-treatment and/or condition of the solution.If you wish to have an extremely ductile nickel deposit then look for a sulphamate solution or preferably a low iron nickel solution. The appearance is the same but the ductility is superb. The deposit has been used on fasteners that take great deformation after plating.
Lynn LewisA. Your problem can have two reasons, wrong preplating process for your particular steel or non ductile deposit.
First of all try to plate some other parts and see whether this problem exists with another steel as well.
The second thing you have to do is a Hull Cell ⇦ huh? test so you can find out wether your deposit is ductile or not.
You mentioned that a cyanide copper layer did solve the problem. Did you try a cyanide cleaner as well? I know that cyanide cleaners are not popular but they are the best cleaners and the best activators.
When did you perform a complete treatment on your nickel solution? It is highly recommended to treat a nickel solution every six months with an oxidizer and carbon.
One more thing, you mentioned that the temperature of the plating solution is 48-55. 48 is definitely low and can cause brittleness. Try to raise the temperature to 60, it might do wonders.
Your metal is low as well, 60-70 g/l may avoid brittled deposit. Rise the nickel sulphate concentration to 250 g/l. Low metal concentration with low temperature cause burning in high current densities.


Sara Michaeli
Tel-Aviv-Yafo, Israel
A. Bright appearance and engineering properties are often clashing with each other. I am plating 95% Tin 5% lead for electronic components. After prolonged discussions with my client,a multinational, the specification was changed to "smooth" from bright. Bright deposits were brittle and used to crack during assembly operation. The finished batch looked very pleasing but had no functional need to be bright.
I have done experiments on ductile nickel plating on copper wire. The ductility increased with increase in plating thickness for dull nickel deposits. Using 50 millisecond plate 10 millisecond deplate at the same current density it was possible to get over 22% elongation.
Y.V.Devalutensils - Pune, INDIA
Q. We currently use a nickel sulphamate plating over a copper base alloy, then sinter it to improve ductility. We had been experiencing severe cracking at the bends (they did fail adhesion testing per ASTM B571 -91) . We are now looking at what is called the "new" and improved ductile bath and it works: what makes it different?
Laurie Frazierelectronic components - Biddeford, Maine
1998
Q. Hello all!
I'm hoping to find a few answers here.
I have been experiencing a few problems with ductility in the electroforming process I'm following. We regularly have samples of our tank analyzed. The last analysis yielded the following results.
Tank description
Sulfamate nickel / total of 540 gallon tank
nickel 15.40 oz/gal
Boric Acid 5.8 oz/gal
ph 4.2 oz/gal
Additive 'A' 0.4 oz/gal
Snap A/M 0.250 %/vol
Ductility Good ?!
Hardness as plated 228 HK 100
Hardness of electroform 367 HK 100
I try to maintain a temp. of 110 deg. to 120 degs.
I use a constant amp. flow of 150 amps for approximately 7000 amp. hrs.
This amount of time will yield around 65ths thickness for my plate. The end product is used for printing.
I was experiencing pitting. I then used carbon filters and ran a dummy plate for 3 days. My current problem is as follows. After the plate is grown and ground to the proper thickness I have to put a bend on both ends of the plate to install it into a printing press. I am encountering severe cracking on the bends. I was told this is a ductility problem and I'm at a loss as to how to address the problem.
Any suggestions would be helpful.
Thanx, Fritz
- Plymouth Mich.
1998
A. My experience is with very heavy sulfamate nickel plating and not electroforming, so what I say may not be totally true.
Agitation, either air or solution proved more helpful than an more anti-pit.
You did not mention what your stress level is. That nasty contractometer test. It is very important to keep it as near zero as possible.
Do you have a bleeder on the ends of your roll? If not, it is an area of significantly higher current density which will lead to larger crystal size ( so the book says) which will have a much greater tendency to crack.
Stress reducers breakdown tend to cause pitting. I liked using a small platinum anode, in addition to the baskets, which broke down some of the sulfamate radical and lowered the stress. An excess of this can cause problems also.
Regular carbon treatment and dummy (LCD) are mandatory for maintaining the purity of the solution.
Excellent filtering also helps. Get a copy of Jack Berg's dissertations on choice of filter micron size.(Serfilco) Doubling your filter area not only works faster and better, it proves cost effective as the filters last 4 times as long. A smaller micron rating is normally not the optimum answer as it significantly reduces flow.
The comments are not necessarily gospel, subject to argument, but food for thought.
James Watts- Navarre, Florida
Q. Hello,
We have been recently plating bright Watts nickel for artistic brush ferules.
We are still in the phase of testing, and our major and utmost problem is that the deposit is too hard or brittle. Since our parts are slightly flattered after plating process, the deposit eventually cracks.
Is there any solution to reduce the stress of the deposit.
Thank you
Plating shop manager - Mauritius
January 31, 2017
Q. Hi again,
Before setting up our plating bath of 200 liters, we ran different tests to all the possible issues that have been discussed previously.
Our parts, which are annealed at 500 degrees and then polished in vibratory barrels, need at least 6 microns of a leveling and bright plating to have an acceptable quality.
Samples of 10 liters of bright nickel were prepared where different conditions were applied.
Our bath constituents and parameters, as per suppliers recommendation:
1) Nickel sulphate 300 g/L
2) Nickel chloride 60 g/L
3) Boric acid 50 g/L
4) Brightener 0.5 ml/L
5) Leveler 3 ml/L
6) Carrier and stress reducer (saccharin - 80%) 25 ml/L
7) Antipit agent (for mechanical and solution agitation only - surf tension 45 dynes) 3 ml/L
8) pH 4.2
9) current density 4 A/dm2
10) Temp 60 °C
11) S type nickel ball anodes in titanium baskets (in PP bags)
1)The first sample was made as per the above recommendation The deposit is bright, leveling but starts to crack when our parts are flattened at a threshold of 3 microns only. (tests were made at 3/4/5 A/dm2 - no visible difference)
2)The second sample was prepared using 75% of the recommended additives. The result was pretty much the same as the first one. (tests were made at 3/4/5 A/dm2 - no visible difference)
3)The third sample was prepared using 50% of the recommended additives. We were able to plate up to 6 microns without cracking after flattening process. However, the leveling power was subsequently affected, and the surface finish was not passed by the QC (tests were made at 3/4/5 A/dm2 - at 3 A/dm2, the deposit was too dull, with nearly no leveling power)
4)The fourth sample was prepared using the recommended amount of additives, but using only 10 ml/L of the carrier and stress reliever (saccharin). Results were same as the first sample, but with a slight loss in leveling power.
On the different tests carried out, the more brightener and leveler is the deposit, the more it is susceptible to crack after deformation.
Maybe an air agitation could help in relieving the stress of the deposit? (mine as well, haha)
Any help would be much appreciated, thank you.
- Roche Terre, Mauritius
February 2, 2017
A. I think you should seriously consider using a nickel sulphamate bath instead of a watts-type nickel; this will give you a much lower stress deposit. I would also reduce your nickel chloride in the sulphamate bath to 10/l or less - it is technically not needed. If you insist on the Watts bath, reduce the nickel chloride to 20g/l, as chloride induces stress. I assume your saccharin concentration is 2g/l, but you don't mention if it is the sodium salt or not, but you should get adequate leveling and brightening with 1g/l sodium saccharin, or less. I would also use sulfur de-polarised nickel as the anode, but use a good anode bag to prevent escape of the bits!
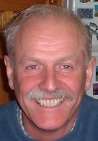
Trevor Crichton
R&D practical scientist
Chesham, Bucks, UK
Q. Hi,
Thank you Mr Trevor for your reply.
We will try to run some test in a sulphamate nickel.
As additive and leveling agent, we use a mixture which contains saccharin (no idea if its a sodium salt though), oxides of nitrogen and anhydrous sulfides.
Recommended concentration is 20 - 30 ml/L.
Our anodes are sulfur depolarised nickel spheres in titanium baskets (in PP bags).
Lately, I have been trying to plate at a lower current density, 2 A/dm2. The plating has better ductility.
The distance between our parts and the anodes is around 12 cm.
Can this factor also represent an issue on the ductility?
Thank you
- Roche Terre, Mauritius
February 8, 2017
A. The following decide stress:
1. Current Density (CD)
2. Temperature
3. Chloride
4. Flow
5. Brightener
The tensile or compressive depends on above together with pH.
Some act negatively, like high chloride more tensile. Less CD more compressive; high temperature more compressive, etc.
Can you do a simple stress test and narrow down the parameters?
I agree with using chloride 15 g/l. 65 °C temp
- Orchard lake, Michigan
A. Hi,
Trevor's suggestion is good answer to help you to get lower stress in the nickel.
You can check by a very thin sheet of metal like brass or copper foil. Connect with the metal you plate to cathode and + to the anode, hold the sheet 2-5 cm a front of the anode and see if the testing sheet tends to go to the anode or to the cathode. Make also a test and hold the foil sheet near the cathode to be sure.
That is the answer if you have tensile stress or compressive stress in nickel solution.
I always use NP-Purifier (AtoTech tradename) in the filtration in nickel solution.
Regards,
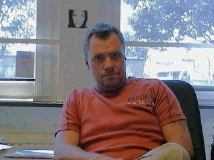
Anders Sundman
4th Generation Surface Engineering
Consultant - Arvika,
Sweden
See also:
• Topic 4503 "Nickel Coating is Brittle"
• Topic 39275 "How to reduce brittleness in Nickel Plating"
Q, A, or Comment on THIS thread -or- Start a NEW Thread