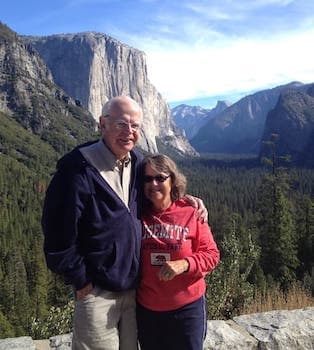
Curated with aloha by
Ted Mooney, P.E. RET
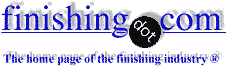
The authoritative public forum
for Metal Finishing 1989-2025
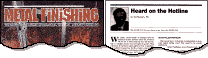
-----
Nickel Coating is Brittle

Q. I am having problems with brittle nickel coating on stainless steel wire. The nickel is plated using a nickel sulphate/sulphamate, nickel carbonate, sulfuric acid and boric acid electrolyte. Since changing the electrolyte (which had previously been working well) the coating is brittle, by this I mean it has very little ductility when bending the wire and breaks) I am deliberately not requiring good adhesion between the steel as this is removed.
Have checked the pH - it's fine. How can organic or metallic impurities be tested for?
Could something else be the problem? Can I heat treat the sample to regain ductility?
Thanks
Kayte Worrall- Ringwood, Victoria, Australia
2000
A. I do not know what a nickel sulphate/sulfamate bath is.
Sulfamate has far less internal stress that a sulphate bath does and is quite soft and malleable. It would be my choice.
sulphate nickel should not flake when bent unless it has an extremely high stress. Do a series of contractometer tests.
Next, it is possible that you are not etching the SS properly or not getting it clean enough.
Where is your strike? You can not beat a Wood's nickel strike for SS. Others may be easier, but are not as good!
Why do you mention nickel carbonate? That is only used to correct a low pH.
If you do have a sulfamate bath, use sulfamic acid to lower the pH, not sulfuric, or you will be gradually converting your bath to a sulphate tank. A gross overage of anti-pit will cause an extremely brittle plate. Low boric acid can cause a surface rise in pH and put nickel hydroxide in the plating making it brittle. What did your voltage vs amperage do when you changed the bath? You could have too much current for the new bath. Is your temperature the same? Do all of your anodes carry the same voltage while plating? There are still other possibilities as well.
James Watts- Navarre, Florida
Q. I am running a high speed sulfamate nickel process plating 18 gauge wire. 350-450 ASF, 16 oz/gal Ni, 140 °F bath temp. S-rounds for anodes, 1.5 oz/gal NiCl and boric acid to saturation in anode bags. When plating the wire to 27% Ni by weight, I only get about 6 weeks life out of the bath before the plate becomes so brittle the wire won't draw. I have analyzed for ammonia ⇦ this on eBay or Amazon [affil links] and have found as much as 600 ppm. Anybody have any ideas on the cause and/or the solution?
Kurt Sammons- Inman, South Carolina
2006
![]() |
The facility you are working at was plating 27% nickel with indefinite bath life 20 years ago. I know because I ran the operation then. Apparently personnel changes have caused the procedure to be lost. Make sure you have enough anode area and keep the operating temperature down. The problem isn't ammonia, it is sulphate from sulfamate decomposition. ![]() Jeffrey Holmes, CEF Spartanburg, South Carolina A. You do not say what your pH is or how hard it is to control. My guess is that you do not have enough anode area or it is passivating. High speed requires extreme agitation, how is yours? James Watts- Navarre, Florida A. Hi Kurt, process engineer - Malone, New York A. I'll bet you have more than 600 ppm ammonia. ammonia causes brittleness and is caused by, high anode current density, low pH, high current density, high temperature and 140 is worse 5than 120 F, and sulfamic acid that contains ammonia to start with. Do a distillation on the incoming sulfamic acid. It is very difficult to find ammonia free sulfamic acid on the open commercial market. Also, your chloride is too high. ![]() Robert H Probert Robert H Probert Technical Services ![]() Garner, North Carolina ![]() |
A. The decomposition product of sulfamic acid are sulfuric acid and ammonia.
How is your anode efficiency? It should be same as your cathode efficiency. If it is less, then you are probably generating sulfamic acid from Nickel sulfamate and electrolytic decomposing it.
You are probably using anode basket?
Try depolarized Nickel anode bars, use good anode bags, this might help prolong the life of your bath.
A. The 2005 Metal Finishing Guidebook & Directory pp.209 & pp. 224
has a good write-up on Nickel anode efficiency.
- Mays Landing, New Jersey
Q. I thank everyone for their responses. All my research has indicated that ammonia causes stress in the plate, is this correct? Unless I have my chemistry wrong, the sulfamate breaks down into nickel sulphate and ammonium sulphate. Would not high sulphate be an indicator of high ammonia?
I am concerned about our pH levels, currently 2.9-3.4., not too difficult to control. We measure twice a shift and add sulfamic acid about once a day.
I have tried using no NiCl since we are using S-rounds, it was a disaster. Will discuss MgCl with my vendor. My inclination now is to lower the temperature and raise the pH some. What is a good level for the pH?
- Inman, South Carolina
![]() |
A. pH 3.6 - 4.0, Temperature 105 °F, 1.5 oz/gal nickel bromide, no chloride. ![]() Jeffrey Holmes, CEF Spartanburg, South Carolina A. S-Rounds are far better for sulfamate than rolled depolarized because they dissolve with less current and hence make less ammonia. Your pH is too low, low pH makes ammonia, let it rise to 4.0 and hold 3.9 to 4.2. High temp also makes ammonia, try to run at 120 F. High anode current density makes ammonia. ![]() Robert H Probert Robert H Probert Technical Services ![]() Garner, North Carolina ![]() A. I have studied it but never ran a high speed sulfamate bath, only conventional and brush. Also, you already have good and educated answers. But in my opinion you should have your defective plated wire analyzed by a a well equipped and professional lab, not just the bath. There are too many things that can go wrong and raise the stress, from operating conditions to dragged in or by-product substances. Fortunately, most will leave a track to follow in the plating. Good luck. Guillermo MarrufoMonterrey, NL, Mexico |
See also:
• Topic 1269 "Need Ductility in Nickel Electroplate"
• Topic 39275 "Nickel Coating is Brittle"
Q, A, or Comment on THIS thread -or- Start a NEW Thread