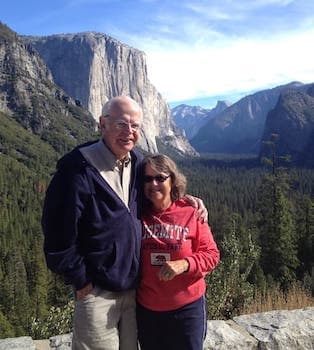
Curated with aloha by
Ted Mooney, P.E. RET
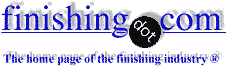
The authoritative public forum
for Metal Finishing 1989-2025
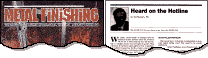
-----
Choosing Plating Rectifier Voltage & Current

Q. What would be a correct choice for voltage whilst selecting a Decorative Chrome plating Rectifier?
At many job shops Chrome burning is a regular feature, despite other parameters being in control. I doubt if this is on account of using a higher voltage rectifier such as 16 or 24 Volt, when in actual use the required Voltage will be only 4-6 Volts.
Does burning occur if a higher Voltage is used to obtain the required amperage? Is using an 8 or 12 Volt Rectifier a better choice for obtaining higher amperage at a lower voltage or vice versa?
Thanks in advance.
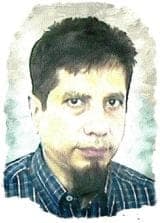
Khozem Vahaanwala
Saify Ind

Bengaluru, Karnataka, India
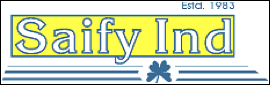
2000
A. Hi Khozem. As you know, Ohm's Law demands that voltage and current are directly proportional; so, for a fixed resistance, you can't raise or lower the current or voltage without proportionately raising or lowering the other. So the only way to vary the required voltage is by varying the anode to cathode distance.
But a rectifier should never be grossly oversized because it leads to extreme ripple, inefficiency and other problems. So, if you know that you never need more than 12 volts, get a 12 volt rectifier, not a 16 or 24 volt one.
The same things that cause burning in other plating solutions cause burning in chrome . . . the difference is that the operating window for chrome plating is very small because burning will occur at too high a voltage/amperage whereas no plating at all will occur at low voltage/amperage (say, less than 100 Amps/ft2).
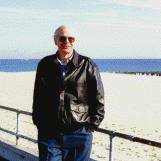
Ted Mooney, P.E.
Striving to live Aloha
finishing.com - Pine Beach, New Jersey
A. I will carry Ted's reply one further step. If you currently never exceed 6.0 volts, buy a 6 volt supply. If you occasionally get any higher, buy a 9 volt unit. If you use a 3 phase unit rather than a single phase unit, you will virtually eliminate ripple without a choke or huge capacitors. Ripple is extremely bad for chrome.
James Watts- Navarre, Florida
Q. In India the general rule is to use only 3 phase Rectifiers on account of incoming line voltage problems hence I'm reasonably certain that ripple is not a major concern. However people tend to use higher Voltage rectifiers on account of versatility .
I wish to add a sequel to my above question :
When general parameters are normal, then what should be the correct distance of the component from the anode at say 150 amps /ft2 to avoid burning without compromising coverage?
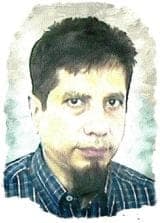
Khozem Vahaanwala
Saify Ind

Bengaluru, Karnataka, India
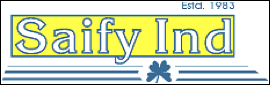
A. I have seen anodes as far away from the cathodes as about 15" to 18" when plating bumpers or plating shafting vertically, but the rule in any plating is to get the anodes as close as practical, and 1-1/2 to 2 inches is common in hard chrome plating--so I don't think that there is a distance that is too close for decorative chrome plating as long as you can assure that they never touch.
But chrome has horrendously poor throwing power / covering power; so if one area of the part is significantly recessed you may need greater anode to cathode distance so that the relative distances from the closest and furthest anode to cathode distance don't vary excessively. For example, if the part has a 2" deep recess, it probably won't work for the nearer points of the part to be 2" from the anodes and the recess to be 4" from the anodes (twice as far away). In that case you might need to go to, say, 10" nominal anode to cathode spacing, so the ratio of closest to furthest anode to cathode is 10" vs. 12" instead of 2" vs. 4".
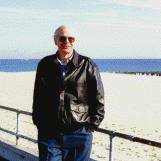
Ted Mooney, P.E.
Striving to live Aloha
finishing.com - Pine Beach, New Jersey
Multiple threads merged: please forgive chronology errors and repetition 🙂
Q. I am looking to purchase a rectifier for the purpose of chrome plating, I have discovered that there are different methods of control, but I don't know the pro's and con's of each. Could somebody please explain the differences between variable transformer, tap switch, and SCR control? Also, I assume I'll need up to 1500 Amps output to handle auto bumpers, if this is incorrect please let me know. Thank you.
Brian C- Surrey, BC Canada
2000
Tip: This forum was established to build camaraderie among enthusiasts through sharing tips, opinions, pics & personality.
The curator & some readers who publicly share their info will be less likely to engage with those who don't.
A. Hi Brian. The required amperage will depend on how many bumpers you plate at a time and how big they are. You should figure that you will probably not be able to chrome plate at all at less than 150 ASF, and 200-250 ASF is pretty typical, so 250 ASF is probably not excessive as a rectifier sizing specification.
SCR control means 'silicon controlled rectifier' control and is a solid state control method, a modern style, and probably the least expensive and simplest of the automatic control methods. The incoming waveform is 'chopped' to control the outgoing current. However, this means that when the rectifier is operated at substantially below its rated current, the incoming sine waves are chopped into 'shark fin' shape, with the result that there can be substantial ripple (AC component) in the outgoing current, which can interfere with proper plating.
Variable transformer rectifiers achieve control by varying the number of turns in the primary vs. secondary coil, so they are better at achieving reduced ripple at low output. However, they are not solid state, but use a motor to adjust the transformer, so they have moving parts. They are probably more expensive and less reliable than SCRs.
Tap switch rectifiers are manual. As the name implies, there are taps in each of the three windings, and you manually turn a handle attached to brushes to vary the primary to secondary voltage. Nothing wrong with them as long as you don't need automatic control. Good luck.
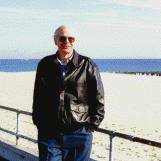
Ted Mooney, P.E.
Striving to live Aloha
finishing.com - Pine Beach, New Jersey
2000
by Weiner & Walmsley
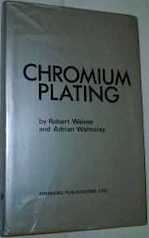
on AbeBooks
(rarely)
or eBay
(sometimes)
or Amazon
(sometimes)
(affil links)
A. Ripple is normally controlled by chokes or capacitors. Both are effective for a given percentage of the load that they are designed for. They all work fine at that point or at 100% output which is hard on the unit.
Solutions, buy a three phase unit. It will be a full wave unit, so you will be using 6 "phases" which have a significant overlap making ripple of no consequence unless you try running a 1500 amp unit at 50 amps.
The true state of the art is a supply that runs at mega HZ or giga HZ and uses a true chopper, not the one that Ted mentioned. These are tiny units vs a normal power supply. They generate very little heat, so are more efficient at all power settings. The electronics portion is a sealed unit with heat sinks so none of the lousy atmosphere gets to the critical components. Draw back-- They cost more. I am not sure how big they are now. 5 years ago, they were only available in the 300 amp area, but that has been steadily going up.
- Navarre, Florida
James is right that the state of the art is to use solid-state "chopper" circuits to generate high frequency rather that operating at 50/60 Hz because this greatly reduces the size of the components. In the plating industry, this technology is called "switchmode" rectifiers.
Regards,
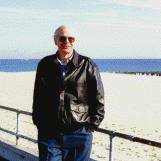
Ted Mooney, P.E.
Striving to live Aloha
finishing.com - Pine Beach, New Jersey
by Clarence H. Peger
(You're unlikely to find this for sale ... but copies are in select libraries)
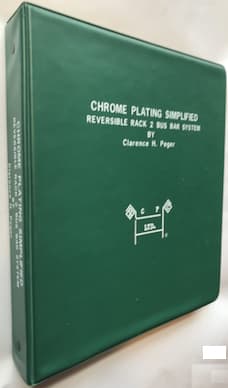
from AbeBooks
* rarely available *
or eBay
* rarely available *
or
Amazon
* rarely available *
(affil links)
by Robert K. Guffie
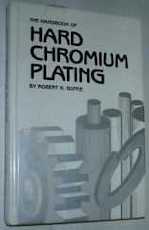
on AbeBooks
(rarely)
or eBay
(rarely)
or Amazon
(affil links)
Q. Can I do hard chromium electroplating with a 1000 A / 6 V rectifier ?
NAOUI KADOURSARL SODEC - Algeria
2006
A. Yes, Naoui
Although 12 volts is more typical for rack plating, if you have anodes very close to the part (maybe an inch or two), it is possible to plate with 6 volts. In fact, Clarence Peger suggests only 4.2-4.7 volts with his reversible rack plating system. Of course, 1000 Amps will only plate parts up to perhaps 2 square foot in surface area (which counts both sides).
For general rack style plating, however, Robert Guffie says 9 volts minimum, 12 volts suggested. Please explain your situation in more detail. Thanks.
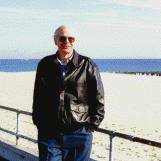
Ted Mooney, P.E.
Striving to live Aloha
finishing.com - Pine Beach, New Jersey
Q. Sir,
In chrome plating rectifier how much ripple is allowed? in 250 kw rectifier how much ripple will generate in 10,000 Amps current rating. Transformer primary wave is pure sine wave form.
Maintenance incharge - B'lore, Karnataka, India
2007
A. Hi Natarajan. The ripple will depend on a number of things including what percentage of the rectifier's capacity you are using and what rectification technology is used, G., but the mathematical ripple in rectifying a 3-phase sine wave to DC is 5 percent. You can read a lot of detail about this, and a number of opinions in thread/topic 1424.
One of the readers in the referenced thread offers his opinion that the shape of the disturbance is as important or more important than the actual amount of ripple. Further, opinions differ on how much ripple is allowable. But for the briefest answer, it is usually said that ripple should be held to 5 percent or less for chrome plating. Good luck.
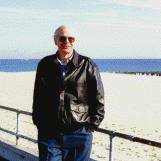
Ted Mooney, P.E.
Striving to live Aloha
finishing.com - Pine Beach, New Jersey
2007
RFQ: Looking for chrome rectifier min 5k 3 phase/220 north Jersey
Andrew M [surname deleted for privacy by Editor]broker - Newark, New Jersey, USA
November 23, 2009
Ed. note: This RFQ is outdated, but technical replies are welcome, and readers are encouraged to post their own RFQs. But no public commercial suggestions please ( huh? why?).
Q. I'm currently hard chrome plating with a 5000 amp, 6 volt, water cooled, tap switch rectifier. I have trouble getting past 2100 amps max. My busing, cabling, fixturing, etc. all seem to properly sized and there is less than 4 inches between my anodes and cathodes (parts). My parts are small diameter (1/4 to 5/8"), long length (4' to 12' long) and I suspect that they are a source of significant resistance. So, I think I need higher voltage to overcome the resistance. Two other plating shops I've spoken to say they do hard chrome plating with 12 volt rectifiers. Does anyone else out there use a 6 volt rectifier for hard chrome? If not, what voltage do you recommend?
Peter KrasuckiPlating shop - Webster, New York, USA
March 17, 2011
![]() |
A. Hi Peter, ![]() David Shiu - Singapore March 18, 2011 A. Hi Peter, ![]() Vikram Dogra Irusha India - Chandigarh, India March 20, 2011 |
Q. Vikram - I forgot to mention that I'm plating 5 to 10 parts per load. So the total surface area for 5 bars at 1/2" x 12' is 1131 square inches. At 3 amps per square inch I would need 3393 amps. With the rectifier turned all the way up I only get about 2100 amps.
Peter Krasucki- Webster, New York, USA
March 21, 2011
![]() |
A. 3 options: Decrease the anode to cathode spacing or use a more conductive solution or use a larger power supply. - Navarre, Florida A. Peter in that case you would def need a 12 V rectifier ORRRR...take my idea go for a conforming anode. 1/2 inch spacing would be too much to ask for for a 12' long anode so try a 5/8" or 3/4" spacing , you might just be able to plate it at 6 V with desired results.. (I mean faster plating rate / energy saving and above all cost towards a new rectifier.. go for it..) ![]() Vikram Dogra Irusha India - Chandigarh, India |
A. 1. 6V is too small for hard chromium plating.
2. The solution plays an important role in the conductivity of this process. A properly operating solution should have a conductivity of 450-500 mS/m. Metallic impurities decrease rapidly the conductivity which means that you need more V for the same Amp.
3. Try to reduce Cr3 and iron.
4. If you are not able to get rid of the impurities then the remedy is increasing the CrO3 concentration.


Sara Michaeli
Tel-Aviv-Yafo, Israel
Q. How to calculate the rectifier capacity in terms of amps?
How related to our job to be coated?
- coimbatore, India
April 9, 2014
A. Hi Abdul. I'm not sure if I understand your question, but you simply multiply the surface area of your job in square feet by the required current density in amps/sq.ft. (or the surface area of your job in square decimeters multiplied by the required current density in amps/sq.dm.). The current density requirement might vary depending on the workpieces you are processing and the method, but 200-250 Amps/sq.ft, 20 Amps/square decimeter is probably enough for decorative chrome plating, but hard chrome plating should probably be done at about twice that.
If you can explain the details of your situation, I think we can help you further. Good luck.
Regards,
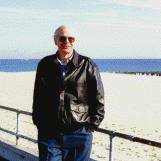
Ted Mooney, P.E.
Striving to live Aloha
finishing.com - Pine Beach, New Jersey
Q. Hi I have a triple chrome plating kit from a hobby plating company and I need help with volt and amps.
I have a power supply that has a gauge for volts and goes up to 25 volts and a gauge for amps that goes to 50 amps and a dial that is for adjustment. Now, say I need 2 amps to plate my part, do I just adjust the knob till I get 2 amps on the amp gauge and don't worry about what the voltage is, or must I worry about the voltage also.
- Harrisburg Pennsylvania usa
September 30, 2015
A. Hi Tom. Voltage and amperage are locked together by Ohm's Law: V = A x R, so there is actually no way to vary them independently anyway.
The plating solution will have a resistance that you can't change except by moving the parts closer to or further from the anodes. So if you choose the amperage, you have to let the rectifier produce however many volts it needs to get there. Chrome will not plate at all until about 1 Amp per square inch, so 50 Amps would do a part of up to about a maximum of 25 square inches surface area (counting both sides). If you are doing some kind of "imitation chrome" however, it isn't actually chrome, and probably plates at about 1/4 to 1/3 that much current. Good luck.
Regards,
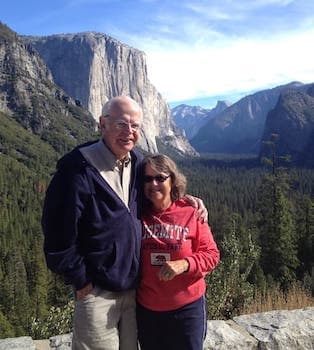
Ted Mooney, P.E. RET
Striving to live Aloha
finishing.com - Pine Beach, New Jersey
October 2015
Q. Hello and good day to everyone here around. I am a newbie and I would like to do a small experiment about chrome plating at home but I don't have enough knowledge about what basic and right equipment to purchase and use.
I am hoping that someone could help me around here regarding the basic equipment. I am planning to chrome plate about a size of a body of an electric guitar. I think it's about 20 inches in height and 14 inches in width with a 2 inches thickness . Definitely, the container of the item would be a bit bigger than the item that I am going to plate. With that size, I would like to ask what kind of rectifier I'm gonna need to buy? How many amperes? How much volts do I need to use to plate it properly? And lastly would that be all the equipment needed?
I hope I can get an answer regarding these matter. Thank you so much for taking the time reading my letter.
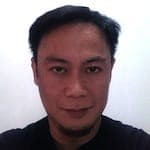
Benjamin Lucero jr.
- Manila, Philippines
October 17, 2015
A. Hi Benjamin. If the part is 628 square inches, you'll need a minimum of 750 Amp rectifier (1000 to 1500 Amps would be better) at probably 9 volts minimum. But a lot more equipment is required: please see our "Introduction to Chrome Plating". You should surely start with small scrap parts rather than with something large or important though! You will nickel-chrome plate dozens of parts before obtaining marginal success.
A scalpel and needle & thread is not the heart of surgery, a skilled surgeon is ... similarly, some people feel that they are still relatively new to chrome plating after years at it and thousands of parts successfully plated. Good luck, but please start smaller! -- and I'd suggest getting a few months experience with some other plating before trying to deal with toxic, carcinogenic, hexavalent chrome plating solution. Good luck!
Regards,
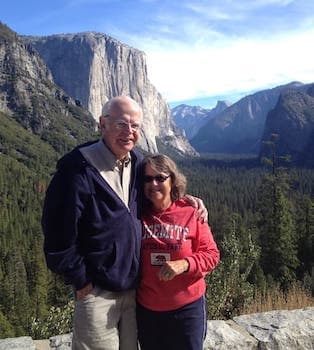
Ted Mooney, P.E. RET
Striving to live Aloha
finishing.com - Pine Beach, New Jersey
October 2015
What kind of single phase rectifier can I use for chrome plating?
Please I need your advice. I want to start decorative chrome plating on a smaller scale. Because of the power source, which is going to be a petrol generator of about 7 kva, I want to go for a single phase rectifier. What is the type of single phase rectifier I will need that will reduce the ripple that is common with single phase rectifier in order to have good chrome plating? The input voltage range between 220 to 240 volts. I will prefer rectifier with variable voltage and current. The output will be direct current.
Thanks for your assistance.
Abbey
- Lagos, Nigeria
June 27, 2016
A. Hi Abbey,
Hexavalent chromium plating needs a very smooth (low ripple) DC supply. Ideally I would start with a 3 phase generator. The rectified DC output is suitably smooth for chrome plating without additional smoothing.
The ripple from a single phase power supply has a very high
ripple and needs a great deal of smoothing before it can be
used for hex Cr. Traditionally the smoothing circuitry
consists of inductors (chokes) and large value capacitors. For low current supplies, say up to 10 amps this is fairly easy. But when when we start to consider hundreds of amps the whole thing becomes heavy and expensive.
If single phase must be used I would look at switch mode power supplies and compare costings. They have smooth DC and can have variable voltage control. In fact I would consider switch mode for 3-phase as well.
I had a quick look for switch mode on Google. I found the following link helpful:
https://www.dynapower.com/products-switchmode.php
I'm not sure Ted will allow a commercial link. I'm certainly not trying to promote them! We have small SM units all around us for in computers, cell phones etc. but it is useful to see industrial size supplies.
Does this help? Have I missed to point of your question?
Harry
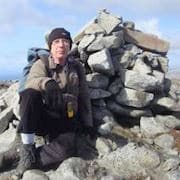
Harry Parkes
- Birmingham, UK
Thanks Harry.
Regards,
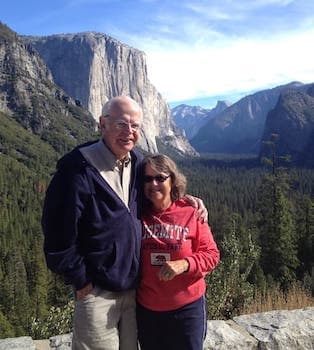
Ted Mooney, P.E. RET
Striving to live Aloha
finishing.com - Pine Beach, New Jersey
Is 12 volts enough for composite plating?
Q. I am an interested researcher in the field of composite coatings such as Ni-TiO2 and Cr-Al2O3 prepared by electrodeposition. I want to buy a rectifier for this purpose. In most articles only the amount of applied current density has been reported and there is not any information about working voltage. Is equipment with maximum current 20 A and maximum voltage 12 V proper for composite electroplating?
Please guide me to select proper rectifier for electroplating.
- Isfahan, Iran
November 1, 2016
A. Hi cousin Ali. When you plate one metal with another you consume perhaps .2 to 2.0 volts for the actual reduction operation (depending on the half-voltages of the plated metal compared to the substrate). You might consume another small amount, probably not over 1 V, as resistance in the bussing system. The biggest voltage drop is due to the resistance of the plating solution, and is proportional to the anode-to-cathode spacing. As you will know, amperage and voltage are related by Ohm's Law of A = V / R
Practically, this means that if you want to control the amperage -- which you do -- you don't get to choose the voltage: it's just whatever voltage is required to deliver the desired amperage. Practically speaking a 12 V rectifier will be adequate for most plating operations except where you are processing large parts which demand a big anode-to-cathode spacing and therefore have a high solution resistance ... and with a 20 A rectifier you won't be doing big parts. I think you'll be fine.
Regards,
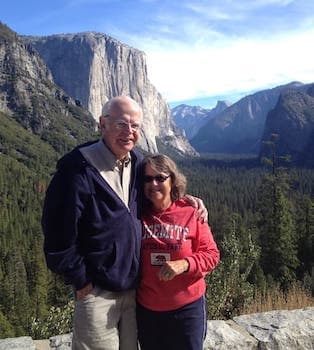
Ted Mooney, P.E. RET
Striving to live Aloha
finishing.com - Pine Beach, New Jersey
Q. Thanks for your reply.
Based on your answer 12 A and 12 V is enough for electrodeposition of composite coatings on small parts, e.g., with less than 20 cm2 surface area. Again it is emphasized that the goal is co-deposition of composite coatings including a metallic matrix and ceramic particles as reinforcement. For example in Ni-TiO2 coating in addition of reduction of existing Ni2+ ions in the bath, TiO2 particles (added in the bath) also should incorporate in the coating.
In this condition, is it enough 12 V or not?
Yours Sincerely
Ali Jam
- Isfahan, Iran
A. Hi again, Ali. Co-deposition of this sort involves occlusion. The particles are not electrically attracted to the cathode; rather, if they are in the vicinity of the cathode as the nickel or chromium is reduced onto the cathode, they become entrapped in the deposit.
This is not meant to imply that composite coating is as easy as pie -- it's quite difficult; some companies have been in business for decades by licensing their knowledge and technology. But as far as I know, the particles do not add enough resistance to the passage of current through the solution as to require higher voltage rectifiers. Good luck.
Regards,
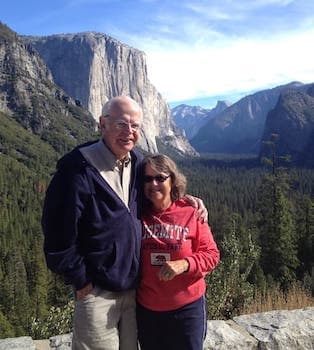
Ted Mooney, P.E. RET
Striving to live Aloha
finishing.com - Pine Beach, New Jersey
IGBT vs. Diode/SCR Rectifiers
Q. Hi all,
I have to select 20,000 amps 12 V rectifier for hard chrome plating. Which one will be good IGBT modular technology or SCR?
Thanks
Ramesh
- Brisbane, Queensland, Australia
November 30, 2016
Q. My situation: Hi I am looking to buy electroplating rectifiers of 4000-5000 amperes for copper and have been given a choice of both IGBT rectifiers and Diode rectifiers.
I can't make up my mind as to which one will be the best and what advantages one have over the other. Kindly shed some light on the above please.
Thanks and Regards,
- Delhi/India
July 19, 2018
A. Hi Arihant. While I spent a lot of time on the road visiting & servicing plating shops over the years, and would have been willing to express my opinion on such subjects in the old days, I have been largely away from plant visits for a while and don't have much actual experience with switchmode and IGBT rectifiers in use; and there is obviously not a lot of very long term reliability history yet.
opinion! But my belief is that in principle they are superior technology to diodes, just as transistors are superior to vacuum tubes, and LEDs are superior to incandescents for most lighting applications.
Transformers operating at high frequency rather than 50-60 Hz line current has made engineering sense ever since they were popularized by the personal computer business back in the late 1970's. You probably need to speak with some users of IGBT and determine whether with regard to large IGBT power supplies we are still in the early days, similar to the early days of transistor and LED unreliability; but my guess is that we are not.
Regards,
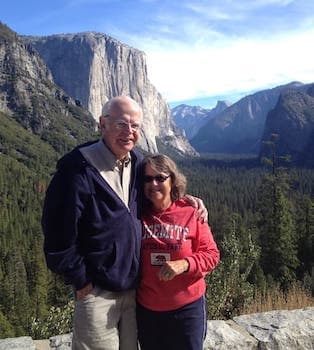
Ted Mooney, P.E. RET
Striving to live Aloha
finishing.com - Pine Beach, New Jersey
Thanks a lot Ted. Will highly appreciate if others can shed some more light on the above.
- Delhi, India
----
Ed. note: They are very welcome to as long as brand names & suppliers aren't discussed (why?).
Q. I have two hard chrome plate rectifiers, both are 12000 (6000+6000) Amps and linked with tank. If I have small job work I use 6000 Amps if I get big job I join them together like 12000 Amps. At present my Output voltage 18V, if I use 24V is there any reflection on my job, and what is the result will come up if I use more than this?
Razack SyedIndustry - Chennai, Tamilnadu
January 19, 2017
A. Hi,
12 voltage is enough for rectifier. To have more amperage you will destroy the rectifier, because a rectifier should be working at the high amperage that it's built for.
I have seen many connections from the rectifier to the chrome bath which are wrong connections. With wrong connection the rectifier loses so much of the power (amperage) through the cable. The + and -cable to the solution should be twisted from rectifier to the chrome tank.
Regards,
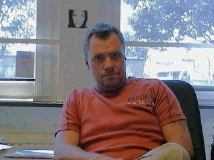
Anders Sundman
4th Generation Surface Engineering
Consultant - Arvika,
Sweden
Ed. note: With regard to combining multiple rectifiers, readers might like to review topic 56947a, "Clubbing / coupling / connecting multiple rectifiers to one plating tank"
Q. How long to run rectifier after putting in new anodes in chrome plating?
Casey Cashwell- Spartanburg, South Carolina
March 18, 2018
Dual Rectifiers vs. Single
Q. I have an offer from a rectifier company for Dual rectifier that could work separately like two rectifiers to two different tanks with separate control for voltage and current. I want to know the disadvantages of dual rectifiers, and should I have single output rectifiers instead or not?
Aly ismailelectroplating factory - Egypt
April 5, 2018
Hi Aly. I have not seen such dual rectifiers for production plating myself, although I have seen small bench-top power supplies with dual outputs, and it has been commonplace for decades to build electronic power supplies which offer both 5V and 12V from one core.
So I can't personally recommend either using them or avoiding them, but I assume the situation is very much like any other case where two devices are combined into one: you save money & space at the cost of a certain loss of flexibility and reliability. If you anticipate no production changes that would require changing either of the two output capacities, and it saves money, it sounds like a reasonable approach.
Regards,
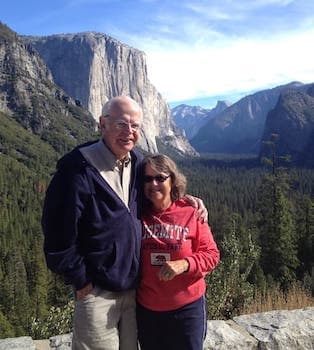
Ted Mooney, P.E. RET
Striving to live Aloha
finishing.com - Pine Beach, New Jersey
Q. Current drop from rectifier during hard chrome plating. What causes related to rectifier because rectifier gives alarm current drop. We have IGBT rectifiers.
Sudhakar chavanpace auto parts - pune Maharashtra India
April 16, 2018
A. Hi sudhakar. I would agree with you that this is probably not a process problem (assuming the parts are racked firmly enough that there is no chance of contact break) but a rectifier problem. Unfortunately, it's probably very difficult to guess exactly where in the rectifier circuit the defect is occurring.
Regards,
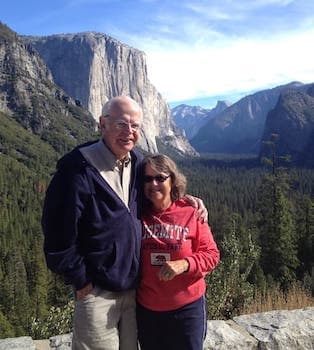
Ted Mooney, P.E. RET
Striving to live Aloha
finishing.com - Pine Beach, New Jersey
Q. Dear Sir,
What does the standard say about the maximum voltage to be used if we are looking at 100 A/sq.ft. of current flow.
We are seeking a 4000 Amps Rectifier, however; not certain on what should be the voltage we need?
Note: We are into copper plating on mild steel. Plating bath is acidic in nature. The anode to cathode distance is 5 inch.
- Vadodar, India
January 29, 2019
A. Hi Tirath. A complete analysis of voltage losses is a bit complex, but the solution resistance is the lion's share of it. Solution resistance can be measured as described in papers such as
http://www.ejournal.unam.mx/rmf/no495/RMF49501.pdf
or if you look hard on scholar.google.com or surfacequery.com, you may find published charts of the solution resistance of typical plating solutions (Charles Faust published a great chart for ASM International which I unfortunately lost to Superstorm Sandy).
But there is an old saying popularized by players of the card game "Bridge": A peak is worth a thousand finesses. It means, of course, that basing a strategy on theory & statistics should be forgone if you have actual knowledge which trumps it :-)
You've been operating this copper plating line for years now according to the long dialog in topic 3795, so you already have a great deal of info as a starting point -- what have been your typical voltage vs. amperage readings?
Regards,
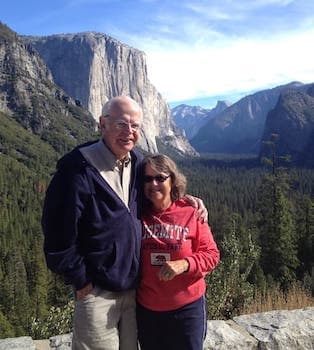
Ted Mooney, P.E. RET
Striving to live Aloha
finishing.com - Pine Beach, New Jersey
Q. Dear all,
Good Day!!
I am new to electroplating world, I need to calculate the power consumption, efficiency and all relevant information regarding 5000 Amp 6 VDC Rectifiers, about its working and designing.
I will be grateful if any of you can provide me the check sheets for predictive maintenance of Rectifiers. Also if anyone of you could proved me the link of book.
Thank you.
Regards,
- Karachi, Pakistan
September 15, 2019
Q. Hello,
I'm considering doing some copper, nickel, and chrome plating on die cast. The type of parts are vintage car parts ... like trim and dash components.
My question is very general to start with:
1- Can I be able to use 220-240 single phase power?
If it's better for three phase can I use a rotary phase converter to supply power to the rectifier?
2- How many input amps do I need to a rectifier ?
3- Can you with this very limited information suggest the size and type of rectifier ?
thanks, Jaan
- Bend, Oregon usa
February 24, 2023
A. Hi Jann.
• Yes you can use single-phase rectifiers for small parts.
• Decorative chrome plating will require an absolute minimum of 1 Amp per square inch of surface area, but 2 Amps per square inch is probably more realistic. You can take that amperage, multiply by 9 volts and get the output Watts required. Assume the rectifier is about 60% efficient and you'll have the input Watts required ... from which you can figure the input Amps.
• Rectifiers of that amperage and 9 volts should be okay. Copper and nickel plating needs about 1/4 Amp per square inch; but it may not be realistic to plan on using the same rectifier for nickel as for chrome, not only because of sizing but because the nickel plating may go passive while you are setting up for chrome.
We are always very happy to try to answer any & all questions that we can. But people of all experience ranges visit these pages: from grammar schoolers for their science projects to post-doctoral researchers wanting confirmation of highly obtuse theories by people with decades of plating research experience; from people who have been supervising $6 million copper-nickel-chrome plating installations for 30 years to people who have not yet attempted to plate a dime with copper or a penny with zinc, yet want to take on the replating of heirlooms :-)
What we try hard to do is not to accidentally lead people down the garden path spending lots of money and generating wastes which are very expensive to dispose of, with little hope of success. Have you read our "Intro to Chrome Plating" so we're on the same wavelength? Do you realize that replating of vintage diecast auto parts will start with filling of the inevitable pits, a job demanding considerable acquired skill? Do you realize that you can't do chrome plating in a basement or garage, only a plant designed for this toxic, carcinogenic, material?
You may well be more than capable of doing copper-nickel-chrome plating of vintage diecastings, you may well know a lot more about it than me -- but I don't know you, you haven't told us your experience, and we don't want our answers to impel anyone towards buying expensive plating equipment if they're not ready.
Luck & Regards,
Ted Mooney, P.E. RET
Striving to live Aloha
finishing.com - Pine Beach, New Jersey
Q, A, or Comment on THIS thread -or- Start a NEW Thread