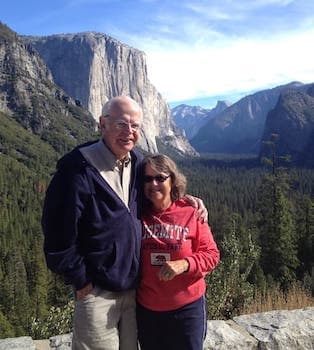
Curated with aloha by
Ted Mooney, P.E. RET
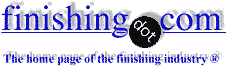
Chrome Plating Introduction & FAQS
Why is the Chrome plating on my Wheels Peeling? Can I Stop the Rusting? What is Hard Chrome? Dip Chrome? Show Chrome? Triple Chrome? Black Chrome Plating? Color chrome? Read on . . .
What is 'Chrome'
Chrome is slang for Chromium, one of the 92 naturally occurring chemical elements. Chrome is a metal, but it is not useful as a solid, pure substance. Things are never made of solid chrome. Rather, when you hear that something is chrome, what is really meant is that there is a thin layer of chrome, a plating of chrome, on the object (the bulk of the object usually being steel, but sometimes aluminum, brass, copper, plastic, or stainless steel).
A cause of occasional confusion is the fact that people may tend to describe any shiny finish as "chrome" even when it really has nothing to do with chromium. For example, brightly polished aluminum motorcycle parts, electropolished stainless steel boat rigging, vacuum metallized mylar balloons and helmets, semi-shiny painted wheels, and nickel plated oven racks are sometimes called 'chrome' by the lay person.
Indeed it's not always easy to tell real chrome plating from other finishes if the parts are not side by side. When a chrome plated finish sits right next to another bright finish though, the other finish usually won't compare very favorably :-)
by Robert K. Guffie
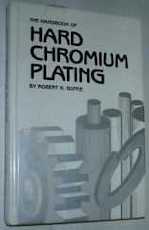
on AbeBooks
(rarely)
or eBay
(rarely)
or Amazon
(affil links)
Chrome plating is more reflective (brighter), bluer (less pale, grayish, or yellowish), and more specular (the reflection is deeper, less distorted, more like a mirror) than other finishes. Put one end of a tape measure against a bright finish, and see how many inches of numbers you can clearly read in the reflection -- you can see skywriting clearly reflected in top quality chrome plating. And there's a hard to define "glint" to chrome plating that almost nothing else has.
What's the difference between "Chrome Plating", "Chrome Electroplating", "Chrome Dipping", "Chroming", etc.?
Nothing. Chrome is always applied by electroplating, it is never melted onto parts in the fashion of chocolate on strawberries, sprayed on like paint, or applied in any other way than by electroplating. Note the previous paragraph, though, that everything that is somewhat reflective is not necessarily real chrome plating.
Is all chrome plating about the same, then?
Not quite. There are two different general applications for chrome plating: "hard chrome plating" (sometimes called 'engineering chrome plating' or 'functional chrome plating') and "nickel-chrome plating" (sometimes called 'decorative chrome plating').
Hard Chrome Plating
Most people would not be very familiar with hard chrome plating. Hard chrome plating is chrome plating that has been applied as a fairly heavy coating (usually measured in thousandths of an inch) for wear resistance, lubricity, oil retention, and other 'wear' purposes. Some examples would be hydraulic cylinder rods, rollers, piston rings, mold surfaces, thread guides, gun bores, etc. 'Hard chrome' is not necessariy harder than other chrome plating, it is called hard chromium because it is thick enough that a hardness measurement can be performed on it, whereas decorative chrome plating is only millionths of an inch thick and will break like an eggshell if a hardness test is conducted, so its hardness can't really be measured directly.
Hard chrome plating is almost always applied to items that are made of steel, usually hardened steel. It is metallic in appearance, and can be shiny, but is not necessarily decorative. Hard chrome plating is not a finish that you would want on a wheel or bumper.
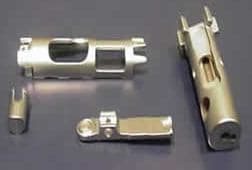

Hard chrome plated components, courtesy of U.S. Chrome Corporation of New York
There are variations even within hard chrome plating, with some of the coatings optimized to be especially porous for oil retention, others "thin dense chrome", and so on.
Many shops who do hard chrome plating do no other kind of plating at all, because their business is designed to serve only engineered, wear-type, needs. If a shop says they do 'hard chrome only', they have no service that most consumers would be interested in.
Decorative Chrome Plating
Decorative chrome plating is sometimes called nickel-chrome plating because it always involves electroplating nickel onto the object before plating the chrome (it sometimes also involves electroplating copper onto the object before the nickel, too). The nickel plating provides the smoothness, much of the corrosion resistance, and most of the reflectivity. The chrome plating is exceptionally thin, measured in millionths of an inch rather than in thousandths.
When you look at a decorative chrome plated surface, such as a chrome plated wheel or truck bumper, most of what you are seeing is actually the effects of the nickel plating. The chrome adds a very slightly bluish cast (compared to the slightly yellowish cast of nickel), protects the nickel against tarnish, minimizes scratching, and symbiotically contributes to corrosion resistance. But the point is, without the brilliant leveled nickel undercoating, you would not have a rust-resistant, reflective, decorative surface.
By the way, there is no such thing as "decrotif chrome plating". That is just a misspelling of 'decorative'.
"Sacrificial" vs. "Barrier Layer" Coatings and Why Quality is Crucial for Chrome Plating
First an aside: Some readers may be familiar with the replaceable zinc anodes used on ships and outboard motors to protect the hull or motor from corroding. What the zinc anodes do is sacrifice themselves to protect the steel. Zinc is "anodic" to steel, and what that means is that when the steel is under attack and about to lose electrons (which would cause the steel to oxidize and convert from solid metal to rust), electrons will flow from the zinc to the steel to maintain the balance and protect it, so the zinc corrodes instead of allowing the steel to corrode. Galvanized roofing materials are coated with zinc, and function the same way: the steel is pretty safe from corrosion as long as there is some zinc left on it to sacrifice itself.
Now, could you use a nickel anode or chrome anode instead of a zinc anode to protect a boat's steel hull from corroding? Absolutely Not! Steel is "anodic" to the nickel, instead of the other way 'round. The current flows the wrong way. The steel will sacrifice itself to protect the nickel and chrome. So now imagine a steel item that is plated with nickel and chrome but there is porosity or pinholes in the nickel plating ... the steel will rust away, sacrificing itself to try to protect the nickel! If you've seen a 50-year old junked rat-trap of a truck or car, you may have seen bumpers with thin pieces of curling nickel chrome, and almost no steel, where the bumper used to be.
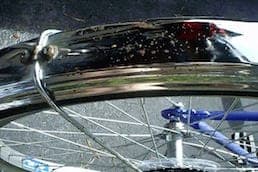
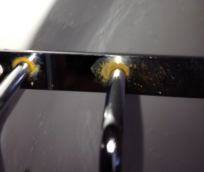
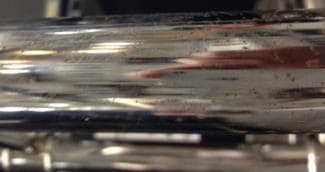
^- 1. Bicycle fender with low quality nickel-chrome plating, rotting away in 3 months as the steel sacrificially corrodes to protect the nickel-chrome plating
2. Bar rack designed for indoor use ^ after one day outdoors in the rain
3. New bathroom accessories on display at a "big box" store, with tiny little rust pits before you even buy them -^
Unlike "sacrificial" coatings like zinc plating or galvanizing where porosity or a hole or bare edge may be no big deal, porosity in nickel-chrome plating is a disaster that doesn't merely fail to protect the steel, but greatly accelerates the corrosion of the steel. Chrome plating is a "barrier layer" plating; once the barrier is breached by a pinhole, very rapid rusting is unavoidable. A low quality chrome plating job with pinholes or porosity is much worse than no plating at all; the plating electrochemically forces the underlying steel to rust.
Poor quality plating that is already showing tiny signs of rusting when you buy it is a manufacturing defect; return it, and don't let them harass you about "chemicals in your bathroom"! It is they who have chosen to distribute defective items; costly returns are the only way you can influence their policy of selling garbage.
Buzzwords: "Show chrome", "Triple Chrome Plating", "Double Nickel-Chrome"
"Show chrome" means chrome that is good enough to be on a winning entry in a car show. Although most OEMs rely on the "self-leveling" property of nickel plating to give sufficient reflectivity to roughly polished steel, chrome-lovers believe that the key to "show chrome" is to copper plate the item first and then buff the copper to a full luster before starting the nickel plating.
Whether you start with bare steel or buffed copper, at least two layers of plating follow -- a layer of nickel and a layer of chrome. But high quality plating usually requires two layers of nickel.
Salespeople are always looking for advantage, and they will use any good-sounding terms they can get away with! There are no laws that define what triple chrome plating actually means, so salespeople will be prone to call their service "triple chrome plating" if there are a total of 3 layers of any kind of plating, or "quadruple chrome plating" if there are 4. So those terms mean little.
By the way, tri-chrome is not an abbreviation for triple chrome, and hex chrome does not mean six layers. But more on that later . . .
The most important issue for durable chrome plating for outdoor exposure such as on a vehicle is that it should have at least two layers of nickel plating before the chrome: namely semi-bright nickel followed by bright nickel. The reason for this involves the anodic corrosion issues we discussed. The bright nickel is anodic to the semi-bright nickel, and sacrificially protects it, spreading the corrosion forces laterally instead of allowing them to penetrate through to the steel. OEMs demand very close control of this factor, and there is a test (the Chrysler developed STEP test) which large shops run daily to insure the right potentials. Careful control of this issue is probably the principal reason that today's chrome plating greatly outlasts the chrome plating of earlier times. If a restoration shop offers only single layer nickel plating, they must apply it really really heavy if corrosion resistance is to be guaranteed, because any porosity or pinhole will doom the underlying steel.
Experts argue whether copper plating provides any additional corrosion resistance at all, but with or without copper plating, chrome on top of a single thin layer of nickel will not hold up to the severe exposure of a vehicle! Industry professionals call the two layers of nickel "duplex nickel plating", and that would be a much better term to use than "triple chrome" and such.
Color Chrome
With the exception of Black Chrome plating, there is no such thing as colored chrome. Rather, those colored coatings are translucent paints applied over a layer of tiny aluminum flakes, and should be called "chrome-look paint"; more on this later.
Some "black chrome" is probably "chrome-look paint", but real black chrome plating is achieved with a contaminant that turns the metal smoky grey or fully black. Black chrome can be a decorative finish for automobile parts, or a matte finish for non reflective coatings on microscopes and optical equipment, or a great coating for solar collectors. We have an excellent podcast interview about black chrome.
Restoration Work
Chrome plating is hardly a matter of dipping an article into a tank, it is a long involved process that often starts with tedious polishing and buffing, then cleaning and acid dipping, zincating (if the part is aluminum), and copper plating. If it's an old diecasting, it's probably pitted, and every pit has to be drilled out and welded/brazed. For top reflectivity "Show Chrome", this will be followed by buffing of the copper for perfect smoothness, cleaning and acid dipping again, and plating more copper, then two or three different types of nickel plating, all before the chrome plating is done. Rinsing is required between every step.
When an item needs "re-chroming", understand what is really involved: stripping the chrome, stripping the nickel (and the copper if applicable), then polishing out all of the scratches and blemishes (they can't be plated over and any scratches will show after plating), then drilling & filling large pits, plating with copper and "mush buffing" to squash copper into any very tiny pits, then starting the whole process described above.
Unfortunately, simply re-plating an old piece may cost several times what a replacement would cost. It's the old story of labor cost. The new item requires far less prep work, and an operator or machine can handle dozens of identical parts at the same time whereas a mix of old parts cannot be processed simultaneously, but must be processed one item at a time. If a plater has to spend a whole day on your parts, don't expect it to cost less than what a plumber or mechanic would charge you for a day of their time.
Blistering, peeling chrome?
If your chrome plating is peeling, this is virtually always a manufacturing defect due to insufficient adhesion of the plating to the substrate. Although exposure conditions can certainly harm chrome, and discolor it or make it pit, they won't make it peel! It can be very difficult for a plating shop to get good adhesion on some things (most commonly on alloy wheels because they are not pure aluminum), but if they can't do it they shouldn't sell it.
Three examples of peeling and blistering chrome on wheels
If your parts have peeling chrome, you should complain and not be deterred by nonsense about chemicals in your garage, how frequently you wash the wheels, etc. We'll say it again, we're that sure: peeling chrome is virtually always a manufacturing defect.
Do it yourself?
The best way to chrome plate something might be to take it to a chrome plating shop. The industry is very 'job shop' oriented, with experienced people ready to handle your parts. Before thinking seriously about doing it yourself, here's some food for thought--
Regulations
by Kushner & Kushner
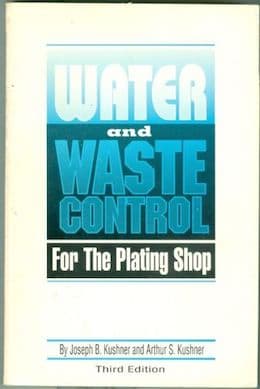
UTL on eBay
UTL on AbeBooks
on Amazon
(affil links)
Electroplating was our nation's very first categorically regulated industry. So, what does "categorically regulated" mean? It means that all of the waste products from this industry -- even very dilute rinse water -- are, as a matter of law, regulated because they are from the plating category, even if the particular substance is so dilute that it is harmless or drinkable. Mix the waste in with other waste, and the whole mass is hazardous (see EPA 'mixture rule'). A former governor of New Jersey perhaps said it best: " 'Toxic' is a matter of statute, not opinion".
In turn this means you can't discharge a drop of hose water without pretreatment and permits; it means you can't take your bad solution anywhere without hazardous waste manifesting; it means you can't accumulate it without permits either. Finally, it means that, because you created the waste, you are legally responsible for it forever regardless of how much you spend to get rid of it.
(Why are you still responsible even after you paid good money for disposal? Because the government feels that, otherwise, fly-by-night waste disposal companies will spring up, sell their services cheap, and disappear. This way, it's your problem not theirs.)
But are you subject to these regulations? If you are selling plated parts or plating services, absolutely! See EPA CFR431 and try to find an exception -- you won't. If you are doing it solely as a hobby, maybe you can get away with it if you stay lucky. But if the sewer authority wants to impose an assessment for upgrading the piping, and your neighbors know that you are plating, they will probably turn you in in a heartbeat. Read the fine print on your sewer agreement: you're forbidden from putting these wastes down the drain, and both your neighbors and the sewer authority would dearly love for you to have to bear the cost of repairs or upgrades. Is it likely to happen? No. Can it happen? Yes.
Chromic Acid
Chrome plating is done in very highly concentrated (about 32 oz./gal) chromic acid, H2CrO4 -- "hexavalent chromium" -- the stuff that made Erin Brockovich a household word. If a neighborhood child develops cancer from any cause whatsoever and his/her parents find out that you were chrome plating, God help you. Factories that use this stuff require exhaust scrubbing, they require fume suppressants that are monitored every day. The workers require medical surveillance (frequent blood tests for absorbed chromium).
If you do illegally dispose of chromic acid you will probably be caught because it leaches through the ground very readily and turns up in the aquifer, and it is not only easily detectable but it's visible at 1 part in a million, and all wells and water supplies are monitored for chrome.
Dropped a beaker on the garage floor? That could be enough to poison all of the wells around you, and you do not have "pollution insurance" in your homeowner's policy.
by Polyanskiy & Belyaev
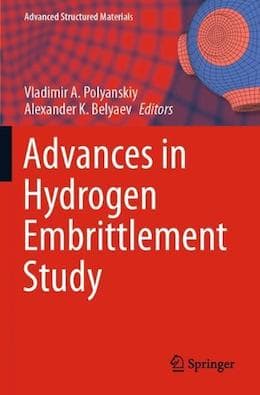
on AbeBooks
or eBay or
Amazon
(affil links)
On top of all this, many city councils have a written or de facto ban on chrome plating.
Finally, chrome plating is notorious for hydrogen embrittlement. If you don't know how to immediately and properly bake the parts to relieve the embrittlement, you can turn hardened steel parts like springs, steering linkage, and fasteners into brittle glass.
Alternatives
There are things that are easier and safer than chrome plating. If your parts are aluminum, you could learn to polish; polished aluminum can look very good indeed!
If you want an easier route to brightness than chrome plating, the new generation of "chrome-look paint" is much better than what was available even a few years ago. And you can put translucent layers on top of the shiny metallic layer to give a red chrome or blue chrome look.
Want to know more about new-generation Chrome-look paint? . . .
adv.
Gold Touch [a finishing.com supporting advertiser],
G.J. Nikolas [a finishing.com supporting advertiser]
If you insist on real electroplating, there are newer proprietary plating processes based on other metals and alloys like tin-cobalt that are still electroplating, and can still get you in trouble, but at least they don't carry the baggage of carcinogenic hexavalent chrome. Another possibility is trivalent chrome plating (this is a somewhat safer and more environmentally friendly approach to electroplating chromium than the traditional hex chrome, but the color is a bit darker and less blue). Most OEMs have not adopted trivalent chrome yet, and parts cannot be mixed because the color is a bit off.
Still With Us?
Think about this: suppose you wanted to open a restaurant. Although it might be a risky business, at least you've spent countless hours in hundreds of restaurants in your life. So you know what a menu is and what appetizers and soups and salads and entrees and desserts are. And coffee and tea and soft drinks. You know what a hostess is and what she does. You know what a waiter or waitress is, what the cook does, what the busboys do, what the dishwasher does.
You know about tables and chairs and tablecloths and silverware and glassware and dishes, pots and pans, stoves and ovens. You know about flowers and candles and romantic music and soft lighting. And vending machines, restroom requirements, no-smoking areas. You know about insects and vermin, and that you need to cook pork and eggs thoroughly. You'd recognize food poisoning or a customer choking. You know all these things from a lifetime of experience and and take them for granted.
Now, what equivalent knowledge do you have about chrome plating shops? If you've haven't spent significant time in a plating shop, you may be unprepared to even imagine what the issues are.
So if you are serious about your interest in the chrome plating business, you really ought to read a couple of books from our "must have" book list, subscribe to a couple of journals to begin acquiring a feel for the industry, start attending monthly meetings of the AESF (www.nasf.org) and a few conferences and exhibitions, and consider a plating course through AESF or Kushner Electroplating School ... and visit a few chrome plating shops.
But the best way to learn chrome plating is to work in a chrome plating shop for a little while. Think of it this way: if you aren't qualified to land a job as a journeyman in a plating shop due to lack of experience, are you really ready to compete in that business against the shop's supervisors and boss and their lifetime of experience? Why not get some hands-on training while someone else pays for your mistakes? We're NOT saying you should not take the dare and grab for a piece of the American dream -- PLEASE DO! This industry needs new blood! But educate yourself as well as possible first to give yourself a fighting chance at a successful, safe, and environmentally responsible business. Good luck!
Please feel free to ask specific questions on our Hotline-Letters page! In your inquiry please tell us that you've already read this page, as that will save time and lost motion. Good luck!