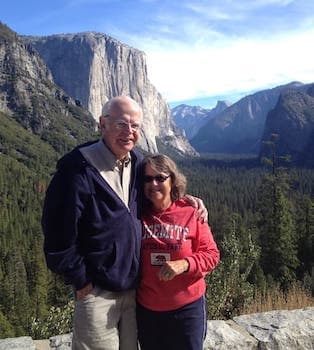
Curated with aloha by
Ted Mooney, P.E. RET
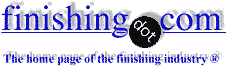
The authoritative public forum
for Metal Finishing 1989-2025
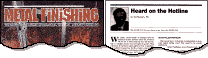
-----
Copper Nickel Chrome Plated Parts Fail CASS Test
Q. I want to replace a Bright Chrome finish that includes copper as base, bright Nickel, and ASTM B556 Chromium, because the parts are failing the ASTM B368 CASS test before 60 hr. This is happening due to Faraday Cage or 3/4" rule. Can you recommend a softer metal coverage that will hold better? The hole 1 1/2 diameter throw rule seems to be in place too. The x-ray test is showing very thin plating and the microscopic images shows a lot of cracks on the surface.
Any advice please!?
George Serb- Newmarket, Ontario, Canada
2001
A. Hi George. While it's true that ions in a plating bath prefer to take the path of least resistance, such that the plating thickness is greater at corners than in recesses, I don't think the term 'Faraday Cage' is applicable to this phenomenon.
I'm not sure what you mean by '3/4 inch rule' -- maybe you're referring to the fact that thickness specifications often require a minimum thickness for any spot on the part that can be touched with a 3/4" dia. ball? Similarly I don't know your '1-1/2 diameter throw rule', but perhaps it relates to an expectation of plating coverage in holes to a depth of 1-1/2 times their diameter. This may be possible for some types of plating, but I think it is unrealistically optimistic for chrome plating.
QUICKSTART:
CASS is an acronym for Copper Accelerated acetic acid
⇦ this on
eBay
or
Amazon [affil links] Salt Spray, a modification which is believed to be a better accelerated test for nickel-chrome plating than the standard salt spray test. One specification for CASS testing is ASTM B368.
Please see our "Understanding Chrome Plating" page if unfamiliar with nickel-chrome plating. "Tri-nickel" means there are three different layers of nickel plating of different galvanic potentials underneath the chrome plating, in an effort to carefully control the electrochemical potentials to drive corrosion forces laterally rather than penetrating down to the substrate.
I would start with the chrome coverage problem and figure out what you need to do. A Hull Cell test will reveal whether your plating solution is deficient or whether you need an auxiliary anode to get chrome coverage in the recesses. It should not be too hard to gauge progress because you will be able to see from the yellowish color of the nickel where you are failing to get chrome coverage.
Once you have good chrome coverage, if you still are failing the CASS test, you need to get better nickel thickness distribution. Again a Hull Cell will warn you if the solution is deficient. If it isn't, your experience with auxiliary anodes will guide you toward one way to solve the current distribution problem, and the use of simple polypropylene shields to block the high current density areas is another.
Can you expound on these 'lot of cracks'? I don't know quite what you are talking about there, but if the nickel plating is cracked, it may be further indication of something amiss with the solutions. While you can get improved thickness distribution by electroless nickel plating in place of your nickel chrome plating or prior to it, you probably shouldn't discard this ideal solution, copper-nickel-chrome plating, just because it has to be done well. Although it's an expensive solution, you could electroless nickel plate before the nickel-chrome plating. Good luck :-)
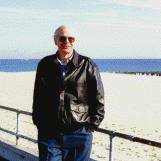
Ted Mooney, P.E.
Striving to live Aloha
finishing.com - Pine Beach, New Jersey
How to achieve 96 hours of CASS
Q. What is the suggested process to achieve 96 hours of salt spray hours (CASS test) for Nickel chromium plated fabricated parts (containing weld joints)
GOPINATHAN NARAYANANMOTOR COMPANY - HOSUR, TAMILNADU, INDIA
2003
A. Hello sir,
You need Good Pretreatment. No rust , No dirt. Clean plateable surfaces. You need Semi-bright sulfur free Ni 18 microns. You need a second layer of 12.5 to 15 microns of bright Nickel. Followed by 0.25 minimum Bright decorative chrome.
Regards
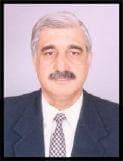
Asif Nurie [deceased] [deceased]
- New Delhi, India
With deep sadness we acknowledge the passing of Asif on Jan 24, 2016
A. Dear Mr Gopinath,
96 hours CASS is a tall order. Tri- Nickel followed by microcracked chrome will probably get you past 48 hours.
Regards,
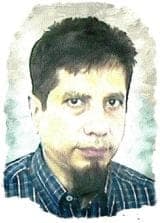
Khozem Vahaanwala
Saify Ind

Bengaluru, Karnataka, India
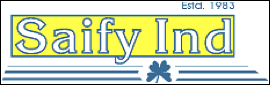
2003
A. Dear Gopi,
Nothing like experimenting with different processes of cleaning, bath filtration and thickness.
- India
2003
A. DEAR SIR,
96 HOUR SALT SPRAY CAN BE EXPECTED BY 20 MIC HARD CR OR ELECTROLESS NICKEL. I RECOMMEND YOU ELECTROLESS NICKEL.
- Tehran, Iran
2003
Multiple threads merged: please forgive chronology errors and repetition 🙂
Want 96-hour CASS Test with Single Layer Nickel
Q. Hello guys,
What should the process sequence of Ni-Cr plating to get 96 hours CASS test? We do single bright nickel plating (followed by decorative chrome) on the brass lever, and facing a problem of hairline cracks on the components. These cracks(including the nickel layer) are observed after 32 hours during the CASS test, but it does't has any corrosion in the spit area after the test finished. and the following are the thicknesses of the plated layers:
Nickel: highest: 40 micron ; lowest: 10 micron
Chrome: highest: 1.2 micron ; lowest: 0.3 micron
What could be the reason?
student - China
2003
A. Thank you for giving me the opportunity to run my opinion up the flag pole and see what people have to say, Xiaolin: which is that there is no correct thickness because single layer nickel plating should not be used if 96-hour CASS test is required :-)
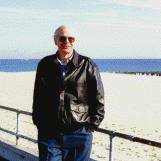
Ted Mooney, P.E.
Striving to live Aloha
finishing.com - Pine Beach, New Jersey
2003
A. Dear Xiaolin,
40 microns is much too thick for a single deposit, the stress will make the deposit crack. You should use a semi-bright Ni and then a bright Ni layer. Contact a plating chemical supplier and they will be able to help you.
Regards,
- Hong Kong
2003
Nickel-chrome Saree Guards Don't Pass 48-hour CASS
Q. We do vibratory finishing to MS tube saree guard component of motorcycle for 1 hour with Acidic compound and polishing with alkaline in same media. We get very good finishing ready for nickel chrome plating. The shine is good and Ra value also below 0.3 microns, but it fails salt spray test with Ni Cl -50 gms /lit & Cu Cl 0.23 gm/lt with temperature of about 50 degrees in 30 hours from certain weld joint areas only. Can you suggest suitable method to improve the salt spray life up to 48 hours?
Sona BhatiaPlating shop - Mumbai, India
2005
A. CASS test is a function of additive chemistry for duplex nickel layer. You have not mentioned what type of plating you are carrying out.
You can try periodic reversal cleaning in alkaline+cyanide type cleaner for good results.
- Mumbai, India
2005
2005
A. Mr Bhatia
Ask your principal to give you a spec sheet of thicknesses to follow for SB nickel, Tri Nickel and then Bright Nickel followed by Chrome plating.
Here is a rough guide for that 48 Hour CASS dream..
SB Ni. 15 - 17 Microns
Tri Nickel. 2 microns
bright Nickel 7 to 12 microns
Chrome 0.3 - 0.35 microns
Hope you get the CASS results with this direction.
Regards
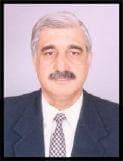
Asif Nurie [deceased]
- New Delhi, India
With deep regret we sadly advise that Asif passed away on Jan 24, 2016
A. Mr. Bhatia,
Improve the filtration in all the SB/Tri/Bright nickel baths.
Also check that no traces of bright nickel solution is allowed to enter into semi bright nickel.
Thanks,
- INDIA
2005
Tri-nickel + chrome failing CASS test
Q. We have problem conducting CASS testing for tri-nickel chrome plating on automotive parts. We have already plated up to 26 micron of nickel and 0.3 micron of chrome but upon conducting CASS test we found the result to be negative. Can anyone give a solution to solve this problem.
Ang YL- Vietnam
2006
A. Try 35 microns of Nickel.


Sara Michaeli
Tel-Aviv-Yafo, Israel
2006
A. I agree with Ms. Sara: by increasing nickel you will get good results if the basic raw material is ok; check the surface roughness before going for plating, and also increase the layer of chrome up to 0.7 µm to 0.9 µm.
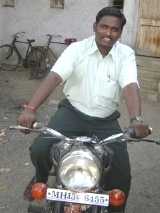
Vishwas Nangare
motorcycle accessories mfgr.
- Aurangabad, Maharashtra, India
2006
A. I would not advise a higher chrome deposit. Over 0.5 microns you will get cracks instead of micropores.


Sara Michaeli
Tel-Aviv-Yafo, Israel
2006
QUICKSTART:
STEP is an acronym for Simultaneous Nickel Thickness and Electrical Potential; a Chrysler designed test used to verify that the galvanic potential of the nickel layers is optimized so the inner layer is sufficiently more noble than the outer layer to optimize corrosion resistance.
The theory of duplex nickel plating is that the bright nickel outer layer of nickel is anodic to the semi-bright inner layer of nickel, and therefore corrosion forces will cause a lateral spread of bright nickel corrosion rather than penetrating into the semi-bright nickel. As long as we can prevent the corrosion from reaching the underlying steel, we're in good shape. Once the steel is reached, it will rust rapidly because the nickel is more noble than the steel.
A. As I know to get higher CASS result is not only the thickness of the nickel, on other hand thickness in Asia for Triple Nickel layer is maximum 20 microns, beside that to plate up to 35 microns I think a bit costly especially now where the nickel anode price is very high.
In modern nickel plating bath system for multiple layer I think we need to consider the STEP value, this value should be above 100 mV between semi-bright and bright nickel to get good corrosion resistance, beside other parameter like roughness due to poor filtration and bad housekeeping and don't forget the surface of the parts.
Good luck,
- Jakarta, Indonesia
2006
Parts used to pass 48-hour CASS, but not anymore
September 1, 2008Q. We purchase zinc (zamak 5) parts with Nickel-Chrome coatings in China.
After polishing the parts, the supplier uses 35-40 µm Cu, 15-18 µm Ni and 0.3-0.7 µm Cr and our requirement is CASS (copper accelerated acetic acid salt spray) test with grade 9 as minimum (48 hours).
It has worked well for some time, but now we suddenly get parts with result at grade 7-9 in the CASS test. We have discussed it with the Chinese supplier, but they don't have an answer or solution/idea to improve the corrosion resistance so we can get the CASS test grade 9 results again. We have discussed if the weather in China in the summer period (and warm baths) can reduce the quality of the coatings. Is this possible?
Is the Ni thickness of 15 µm enough to expect grade 9 results in the CASS test? What other reasons can there be for reduced corrosion resistance if the coating thickness is correct?
Should above layers give enough protection to continuously pass CASS test with minimum grade 9 ?
Can the zinc moulding be the reason to the problem? E.g., low temperature during moulding?
Hope anybody can give me some ideas to pursue.
buyer - Randers Denmark
A. Hi, Carsten. 48 hours is a "very severe" CASS (ASTM B368) test. So your plating needs to be very good to withstand it. You should have duplex nickel plating (semi-bright nickel followed by bright nickel), rather than single nickel plating, and microporous chrome.
Remember that the CASS test, and all accelerated corrosion tests, are Quality Assurance methods to make sure something hasn't gone wrong. Obviously something has gone wrong, but it's hard (maybe impractical) to troubleshoot a process from thousands of miles away. My own experience has been, however, that when copper-nickel-chrome plated diecastings start going bad, it's usually because the quality of the diecastings has gone down. You're not going to properly plate a diecasting that has porosity or a cold shut.
Regards,
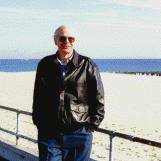
Ted Mooney, P.E.
Striving to live Aloha
finishing.com - Pine Beach, New Jersey
September 3, 2008
A. The corrosion test reveals porosity. Check the surface to be plated for pores. If none are found, the pores may be caused in your preparation procedure. Avoid etching. Be sure that the filtration is adequate in the nickel plating tank and that there is no airborne particles that can get into the plating solutions. Thicker nickel plating layer would be helpful, and the dual nickel - porous chromium is the best process for corrosion protection.
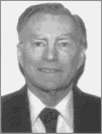
Don Baudrand
Consultant - Poulsbo, Washington
(Don is co-author of "Plating on Plastics" [on Amazon or AbeBooks affil links]
and "Plating ABS Plastics" [on Amazon or eBay or AbeBooks affil links])
October 9, 2008
Q. Sir
What is minimum requirement for CASS Test for Duplex Nickel chrome plating.
Is there any related document showing the requirement of CASS test for the same ?
- MUMBAI, MAHARASHTRA, INDIA
July 3, 2013
A. Hi Dinesh. Usually the buyer/designer will specify the CASS test hours based on how he perceives the exposure conditions to be. The National Association for Surface Finishing (www.nasf.org) has (or had) a series of "Quality Metal Finishing Guides" for various finishes. The chart below comes from page 18 of the "Decorative Copper-Nickel-Chromium" guide. Good luck.
Regards,
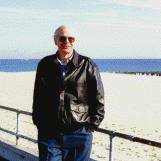
Ted Mooney, P.E.
Striving to live Aloha
finishing.com - Pine Beach, New Jersey
July 2013
Q. Hello, I am looking to have some marine bronze (C6300) chrome plated and be able to withstand harsh salt water environments.
What is the suggested ASTM plating specification (thickness layers, etc...) and what would you suggest for a ASTM B117 salt spray test duration?
Any help would be greatly appreciated, thanks in advance for your assistance.
Manufacturer - Hartford, Connecticut USA
September 30, 2013
A. Hi Stanley. As you see, we added your letter to a thread on the same subject, which should at least partially answer it for you. I'd consider that exposure "very severe". But it may be best to not use ASTM B117, and use CASS testing per the discussion. Good luck!
Regards,
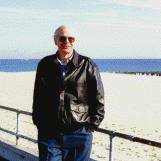
Ted Mooney, P.E.
Striving to live Aloha
finishing.com - Pine Beach, New Jersey
October 2, 2013
Q. Dear sir
Actually we have a supplier for Nickel Chromium plated stay-rod. Our minimum requirement is 20 microns but our supplier isn't able to achieve up to the mark; he is getting 8 to 9 micron. Because of that we are frequently facing rust issue. The material is okay when it is kept in packed condition but we exposed to atmosphere it got rusted within 48 hours. We have sent for CASS test; it's good up-to 42 hours in the chamber, but between 42-48 hours it got rusted. Kindly suggest how improve the process, give me some inputs.
Regards
Yuvaraj
- Chennai, TN and INDIA
March 28, 2016
A. Hi Yuva. A quality nickel-chrome finish is a wonderful and beloved finish. But a low-quality nickel-chrome finish accelerates rather than retards corrosion because nickel is a "barrier layer" coating which is cathodic to steel. If there is porosity or pinholes, the steel becomes a sacrificial anode and protects the nickel by rapidly rusting away.
You are calling for 20 microns of nickel, which is appropriate for "moderate" exposure (indoors in kitchens and bathrooms), but are getting 8-9, which is short of the minimum 10 microns for even mild exposure. The first step in improving the process is very simple: do not accept less than 20 microns. At some later date you might cut back to 15 microns if the chrome plating is top notch. Good luck.
P.S. 1: what are these "stay rods" used for?
P.S. 2: I'd be very suspicious about a claim that an 8-9 micron plating which rusts in 48 hours in the atmosphere survived 42 hours of CASS testing.
Regards,
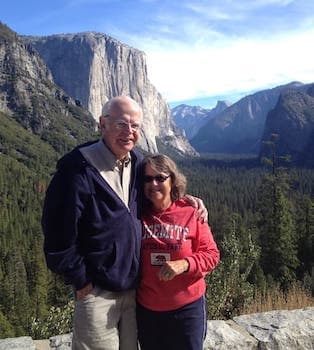
Ted Mooney, P.E. RET
Striving to live Aloha
finishing.com - Pine Beach, New Jersey
April 2016
Ni-Cr Plating on Shock Absorber Spring fails CASS Test and also Peels
January 13, 2017Q. Sir, my query is related to two wheeler Rear Shock Absorber Spring.
- We are using SAE9254 Grade Spring wire for Spring manufacturing.
- Spring is having Nickel Chrome plating process with requirement of 50 Hrs.CASS test.
- But, Spring is not getting CASS test life. Just passes 30 Hrs,only.
- Spring plating is peeling -off in compression test?
Kindly give solution to this problem. Also confirm whether SAE9254 Spring material is recommended for Nickel Chrome plating or not?
Thanks in advance.
Vishal
Iam an Engineer - Aurangabad, Maharashtra, India
Ed. note: This RFQ is outdated, but technical replies are welcome, and readers are encouraged to post their own RFQs. But no public commercial suggestions please ( huh? why?).
A. Hi Vishal. We've jump-started an answer for you by appending your inquiry to a similar thread. To pass 50 hour CASS test, while keeping the nickel thin enough to not peel from a spring surely requires duplex nickel plating or tri-nickel. Please tell us your plating spec. Thanks.
Regards,
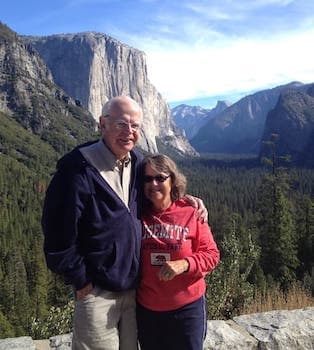
Ted Mooney, P.E. RET
Striving to live Aloha
finishing.com - Pine Beach, New Jersey
January 2017
![]() |
January 16, 2017 Q. Plating specification are as follows, - Aurangabad, Maharashtra, India A. For the spring with such type of materials, after plating carry out hydrogen embrittlement at 220 °C for 2 hrs. & mostly plating thickness will be not more than 20 microns with triplex nickel plating; having - ve step - 10 to -30 MV& + ve step 100 to 120 MV. Again for peel off see cleaning with anodic; degreasing maintain conc.50/60 GPL & temp 60/70 °C for at least 4 min.; check for water break test also. sanjay jabadem/s metalmanauto pvt ltd - aurangabad, Maharashtra, India March 7, 2017 |
Duplex Nickel Plating CASS Hours
Q. I have been approached by my customer for 20 micron duplex Nickel & 0.15 micron Chrome plating asking for 48 hours of CASS test.
Will the stated thickness of plating can pass 48 hours of CASS test.
Please guide.
Shop Owner - NASHIK, Maharashtra, India
September 12, 2019
A. Hi Avinash. I doubt it. On this and other threads, Triplex nickel is suggested. It's possible with duplex nickel, but would probably require almost twice your thickness of both nickel and chrome. Good luck.
Regards,
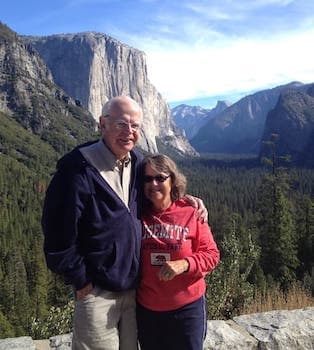
Ted Mooney, P.E. RET
Striving to live Aloha
finishing.com - Pine Beach, New Jersey
September 2019
Thanks Ted for your immediate response. I am also doubtful about this specification and hence asked the question.
Thanks again for your response.
- Nashik, Maharashtra, INDIA
September 12, 2019
Q, A, or Comment on THIS thread -or- Start a NEW Thread