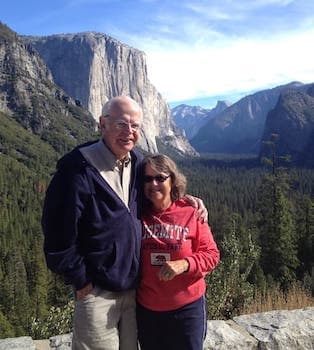
Curated with aloha by
Ted Mooney, P.E. RET
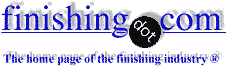
The authoritative public forum
for Metal Finishing 1989-2025
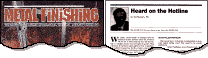
-----
White spotting on black anodising
Q. How to avoid white dots in sulfuric acid anodizing with red dye & black dye?
1) our Part material is 7075
2) Used for Aluminium Jig
3) we do type II AS PER MIL-A-8625 / MIL-PRF-8625
[⇦ this spec on DLA] CLASS 2
4) sealing - DI WATER & Nickel acetate seal
5) voltage - 16 volt
6) alkaline degreasing (9 min), Rinse
7) deoxidizing (3 min), Rinse
8) Nitric dip (3 min), Rinse
9) Sulfuric acid anodizing (19 °C)(18 microns thickness), Rinse
10) Dragout rinse
11) nitric dip (5%)(90 SEC) , Rinse
12) Dye Ph-(3 to 5)(15 Minutes) , Rinse
13) Nickel acetate seal (30 minutes), Rinse
14) Dryer - (55 °C)
Employee - Chennai / Tamilnadu, India
January 11, 2024

⇩ Related postings, oldest first ⇩
Q. Over the past year or so we have experienced a new problem. See pics.
We are getting small white spots on finished parts. Parts come to us and appear clean.
From two different customers:
- who provide us with machined 6061 extrusions
- we do either black or grey anodize
- we have tried many cleaning options:
- soap only - soap + desmut + etch + desmut
- water rinse + soap only
- water rinse + soap + desmut + etch + desmut
When questioned about what lubricants are being used during machining, both customers said they are ?water based?.
One of our chemical suppliers advised us that instead of using a soap cleaner to remove a ?water based? lubricant, we should simply use a water rinse or water spray rinse before the soap. We did this & it appeared to help the problem, but the issue keeps coming & going with no rhyme or reason.
Anyone have any input or help to offer?
- Long Island City, New York
2004
A. David, first look for pits in the incoming metal. Next look for chlorides in the dye tank. Then measure the voltage between the titanium rack and the stainless steel coil, then impress a reversal of that voltage with a lab rectifier. Then take two aspirin and call me in the morning.
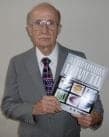
Robert H Probert
Robert H Probert Technical Services

Garner, North Carolina
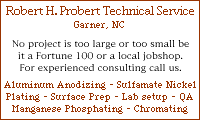
2004
Q. I HAVE A PROBLEM WITH WHITE SPOTS ON A BLACK ANODIZED FINISH THIS IS AN ON GOING PROBLEM
HAS ANYONE ELSE HAD THIS AND SOLVED IT PLEASE
ELECTRO PLATERS - BRAINTREE, ENGLAND
2007
for Shops, Specifiers & Engineers
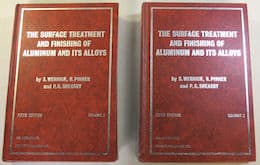
avail from eBay, AbeBooks, or Amazon
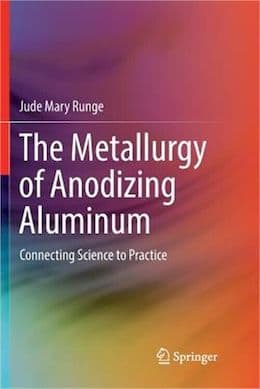
avail from eBay, AbeBooks, or Amazon
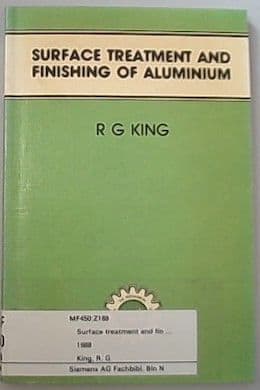
avail from eBay, AbeBooks, or Amazon
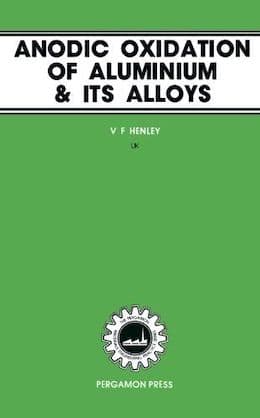
avail from eBay, AbeBooks, or Amazon
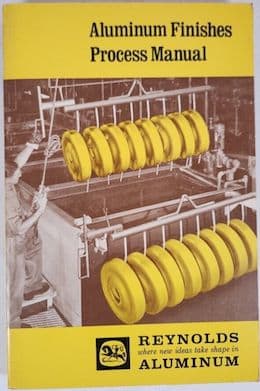
avail from eBay, AbeBooks or Amazon
(as an Amazon Associate & eBay Partner, we earn from qualifying purchases)
![]() |
A. Fairly common with cast and some extruded aluminum. exactly what material and shape are you black anodizing? - Navarre, Florida A. My guess would be galvanic pitting caused by either running aluminum parts on titanium racks or other galvanically dissimilar aluminum alloy (that is from the parts being anodized). Other potential causes might be entrapped sulfuric acid electrolyte in pits (if parts are castings). Or it could be excessive chlorides in the sulfuric electrolyte. Or perhaps embedded abrasive particle that is preventing the underneath aluminum from anodizing. There are plenty of possibilities as others will build on these! Pictures are easily posted and in cases such as failure analysis are worth 10,000 words! Check these out, be on the lookout for others and good luck (we've all been there!). ![]() Milt Stevenson, Jr. Syracuse, New York A. 1. What is free acid and dissolved aluminum? Aluminum sulphate is White. Put a 5% nitric acid between the anodizing and dye. ![]() Robert H Probert Robert H Probert Technical Services ![]() Garner, North Carolina ![]() A. Danny, Aerospace - Yeovil, Somerset, UK A. I would guess that a few things are possible here: plating company - Toledo, Ohio |
A. We have also faced similar problem during Black anodising. If it is happening only on 7075 alloys, then the problem is in base material wherein the Zinc is precipitated, and I agree with one of the answers given.
This could be avoided by dipping in mixture of Nitric acid 30% and HF 10% for less than a minute and then rinsing thoroughly (important, otherwise you will get into bigger problems) and anodise. By increasing the conc. of sulfuric acid by about 20 gram per litre more than you are already working will also help in avoiding pits in 7075 alloys.
If this problem is with all the alloys of aluminium then the obvious reason is Chloride contamination and high conc. of dissolved aluminium.
metal finishers - Bangalore, India
June 20, 2011
Q. We are Sulfuric anodising and dyeing black, with the larger items we wire using ali wire. Smaller items we tried using titanium 3 prong jigs through a hole, but we end up with white spots randomly all over the components (100 off per jig) 100 off with white spots.
Director - ESSEX, UK
October 27, 2009
![]() |
A. Hello Andrew, Sample Manager - Newark, Ohio, USA October 30, 2009 A. Alloy? Nitric Dip between anodize and dye? Titanium Rack and stainless dye tank? Free acid and Dissolved aluminum? First seen: after dye, after seal? Calcium/Magnesium content of the seal? Pits in the metal to start as seen with a 10X loupe? ![]() Robert H Probert Robert H Probert Technical Services ![]() Garner, North Carolina ![]() October 30, 2009 A. Hi ![]() Anne Deacon Juhl - - Trustrup Denmark |
A. Check for anodize solution contamination, electrical contact, rectifier electrical output, change rinse. If still problem, change the black solution. If problem still, change desmut solution and check the caustic solution (it may be contaminated). Good luck.
Carlos Carrera- Miami, Florida, USA
November 2, 2009
Q.
Hello!
My name is Leonardo Villalobos and work in a large company to Anodized Aluminum perfume and cosmetics.
I am having many problems with spots (points) in White uncolored black pieces. I wonder if anyone can help me figure out the cause of the problem. The process is as follows:
Aluminum 1,100 (small parts for perfumery)
Clean parts
matting
Washing (3 times)
neutralization
Wash (2 times)
Anodizing (electrical current density 1.2 for 30 minutes)
Washing (4 times)
Color (mixture of two dyes)
Wash (1 time)
Sealing (8 minutes hot sealing)
Washing (3 times)
drying
I need help please!
Colorist - Jundia, Sao Paulo, Brazil
August 21, 2012
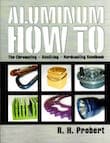
Aluminum How-To
"Chromating - Anodizing - Hardcoating"
by Robert Probert
Also available in Spanish
You'll love this book. Finishing.com has sold almost a thousand copies without a single return request :-)
A. Hi Leonardo.
There are different types of white spots, so fastest progress will probably be made if you send a quality photo of the spots to mooney@finishing.com for posting here. Thanks.
Regards,
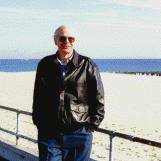
Ted Mooney, P.E.
Striving to live Aloha
finishing.com - Pine Beach, New Jersey
August 21, 2012
A. The most likely, but not only cause is entrapment of anodizing solution in porosity. It looks like you have a good rinsing cycle, so you'll need a good microscopic examination of the aluminum to look for porosity in the raw material, or as the result of machining operations which may smear slivers into the surface.
Do other parts processed through the same process show the same problem?
Although your process looks good, you could try additional rinsing after anodize to see whether it will help. Alternate warm/cold rinsing might help.
Also try a few parts without the etching step to see whether you might be over etching.
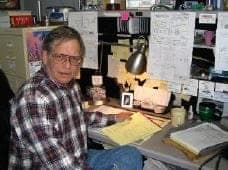
Jeffrey Holmes, CEF
Spartanburg, South Carolina
August 23, 2012
A. 1. Try a 5% Nitric Acid dip between the anodize and dye, as in anodize-rinse-5% nitric-rinse-dye.
2. If the dye tank is stainless steel and the rack is titanium, you have a galvanic problem. Takes some parts off the rack and dye on stainless steel hooks, if that works, come back and we will tell you 4 alternatives to fix the problem.
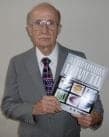
Robert H Probert
Robert H Probert Technical Services

Garner, North Carolina
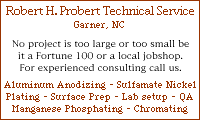
August 24, 2012
A. Hi Leonardo,
First of all, check your DI water conductivity (if you use it in rinsing after anodizing). The max reading should be 10 micro siemens.
2nd: After cleaning, you could try to dip the part in Ammonium Bifluoride tank (conc.: 50 g/L, RT). If not confident, you could try in small/lab scale first.maybe 50 pieces
3rd: you should control your Hot water sealing quality in term of pH. the ideal pH is >4.5 & above
Aluminum 1,100 (small parts for perfumery)
Clean parts
rinsing
Ammonium Bifluoride dip
rinsing
matting
Washing (3 times)
neutralization
Wash (2 times)
Anodizing (electrical current density 1.2 for 30 minutes)
Washing (4 times)
Color (mixture of two dyes)
Wash (1 time)
Sealing (8 minutes hot sealing)
Washing (3 times)
drying
Thank you.
- Malaysia
November 23, 2012
Q. Hello,
long time reader first time poster. After working for 7 years in the industry I started a small anodizing and black oxide job shop in Croatia.
We finish small to medium size machined parts made out of alloys: 5083, 2007, 6082, 7075, 5754 (the order of quantity). We do type 2, hard coat and certain colors. The problem that's been going on since the beginning of the operation is white spots on black colored anodizing (any color really). The only constant is that it only happens on 5083 alloy. I've tried all the recommendations found on this forum and many other sources but can't get rid of the white spots for good.
The process for black anodizing of 5083 goes as following:
1. Degreaser 50°C, 10 minutes, spray rinse
2. Alkali etch 50°C, 10 sec, 2 stationary rinses 1 spray rinse
If the parts have blind holes, each hole is manually spray rinsed before acid stage of the treatment
3. Desmut nitric acid 350-400g/l (35-40%) not heated, 10 minutes, 1 stationary rinse, 1 spray rinse, 1 demineralized water rinse
4. Anodizing (H2S04 190 g/l, Al<15 g/l) 25 minutes at 15V -> 15 um (0.6 mil) 2 stationary rinses
5. Nitric dip (same as desmut ) 1 stationary rinse 1 spray rinse, 1 demineralized water rinse
If the parts have blind holes, each hole is manually spray rinsed then demineralized water rinsed before dying
5. Dye (Sanodal deep black hbl liq) 45-50°C 15 min
and after dying white spots appear....
At first we had great success just with nitric before dye, almost no white spots for past 6 months but lately it doesn't work. Sometimes rinse in hot demineralized water (50°C 15 min) after anodizing and before nitric dip helps. Sometimes redoing the anodizing helps, sometimes it makes it worse. Generally longer etching time and thicker layers increase the size and amount of spots. Same problem with type 2 and hardcoat. There is no foundation for me to setup a repeatable process, only constant so far is that it only happens on 5083 alloy. All potential remedies are random in effect.
My observations so far:
1. Ceramic bead blasted 5083 shows no white spots, areas that are not blasted on the same part exhibit spotting.
2. Spots vary in size, shape is irregular (picture)
3. Racks are titanium, I've tied using only aluminium racks to no avail
4. Tanks are plastic there are no stray currents
5. Sometimes white spots appear only on the machined areas of the plate
6. As far as I understand it 5083 plate is porous, sulfuric acid gets trapped in the pores after anodizing. Nitric should remove sulfuric and then rinse because its not so "oily". The spots appear in the dye because of the heat which pulls trapped sulfuric to the surface. Then why doesn't heated demineralized water rinse (same temperature and same duration as dye) remove the acid from the pores?
7. I've read Surface Finishing and Treatment of Aluminum and its Alloys and Aluminum How-To back to back but received no further insight on the problem
If any additional info is needed I will gladly share.
Please Help
- Samobor Croatia
May 8, 2022
A. Hello Goran.
While your problem is not uncommon, the solution might be depending upon the source of the white spots. Past experience indicates to me that the spots are resultant from one or two sources. The first would be poor rinsing after the etch process. You are saying that the spots appear after the dye process but generally unless black dye is contaminated, the spots are already present, just not visible until the parts are dyed ... any color ... as you indicate. Returning the parts to the anodize tank with current previously used, rinse, and dye again. Many many times this condition will take care of itself.
The second source is exactly as you indicated ... machined surfaces. This is typical of castings. The as-cast surface will generally appear nice and black but the machined surface displays the white spots. The short explanation is because the machined surface has now exposed the pores and the pores hold chemicals which the parts have previously came into contact with in your process. Fortunately, the fix is the same. Take the parts back to anodize for 5-8 minutes with the same current used previously and then rinse and dye again. The appearance will usually improve greatly and many times the white spots do disappear. I would not make the situation any worse by introducing a nitric acid rinse to these parts after the anodize process. For my liking it is just one more chemical you will try to rid yourself of prior to the rinse.
Oh, and welcome to the world of anodizing. This will not be the first head scratcher that you will encounter.
supervisor - Cicero, Illinois
Saporito Finishing Co.

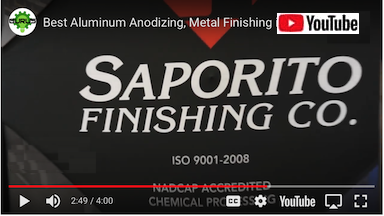
May 9, 2022
![]() |
- Samobor Croatia A.
1. Some low quality 5000's show bare mag, which is "white" and does not anodize. ![]() Robert H Probert Robert H Probert Technical Services ![]() Garner, North Carolina ![]() |
A. Hi again Goran
I am sure there is some type of theory behind the additional time but for my part it has been experience that has shown us it is possible to correct anodizing defects using this procedure. You could most assuredly experiment yourself and see if the additional tank time prior to dye would work. (Nothing would be lost except a few minutes time). Also you are indeed correct: by taking the parts back to anodize tank for that few minutes, the parts will indeed shed some color and that color will linger in the tank. (I can always tell when somebody had what we call bleed out issues). Sometimes I see the anodize tank is blue, other times it is red ... I am sure you understand what I am saying. The good news is the tank does not stay discolored for weeks but maybe a day or so max. It does not affect parts being anodized, meaning parts anodized for clear will not come out with a red tint on them. (I have never seen this happen). The degree of color loss on parts being brought back to the tanks should be directly related mostly to the dye you are using. (A less durable dye might surrender more color). When I take black back to tanks, the parts will usually come out a steel grey after the extra time.
supervisor - Cicero, Illinois
Saporito Finishing Co.

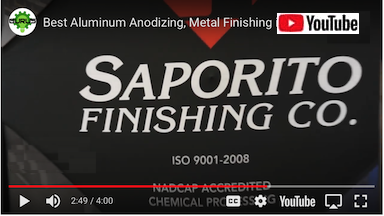
May 11, 2022
Q. Thanks Robert,
1. Only 5083 presents a problem.
2. I anodize 2007 by constant current. Starts at about 20.5 V after 3 minute ramp and drops to under 15 V after 35 minutes producing 15 µm thickness. Never had a problem.
3. I measured using both digital and analogue multimeter. No matter how hard I scratched the surface of rack and coil with the probe tips the reading was always 0.00 V.
4. Nitric post dip is the same one used for desmut. How would you define loaded with sulfuric acid? 1 g/l? 10 g/l? After proper drain and 2 rinses I can't imagine that anything that isn't stuck in pores or the bottom of blind holes is being transferred. It would probably take ages to introduce a liter of sulfuric to a 1000 l tank. 1/5 of a tank is regularly discarded and replenished with 57% HNO3.
5.The customer does their own blasting. Mostly on 5083 and sometimes on 6082.
- Samobor Croatia
A. Hello Goran,
Frankly,I suppose source of this problem out of anodizing line. Most likely it's related to metallurgical problem such as alloy composition or homogenizing. Please check alloy composition and share with us.Some element(s) may be out of tolerance and coarse MgSi layer during homogenizing.
Despite my guess out of anodizing line you would try these in your anodizing line if you want:
1-skip etching bath for one bar and check out the pits after anodizing
2-polish some profiles and anodize the profiles as polished black and check out
3-(most important) Try ACID ETCH BATH instead of traditional caustic (alkaline) etch. I am sure you won't see these pits because acid etch mechanism runs differently from alkaline etch.
Good luck
- sakarya, yurkey
A. Hey Goran
I see a familiar problem there. White Spots, Black Anodizing on Titanium Racks. No obvious cause and yet there it is. Over the past 2 years, we've been dealing with a very similar issue, the main difference seems to be temperature related between the process you run and the one we run at our plant.
We tried everything we could think of. Aluminum racks, extra rinse post anodizing, acidic rinse post anodizing, checking for contaminants (Including Chloride) and nothing gave any indication that we were on the right, or wrong, track.
Well, you have to try SOMETHING. We ordered a small sheet of 5 mm magnesium plate, attached some to an aluminum rod and fastened it to the loadbar after anodizing. Letting it run all the way through colour, rinse, seal and watched our problem disappear over night.
Even if you can't measure a current, the titanium racks work a bit like a capacitor and can be a reason for a discharge over time. This can cause galvanic corrosion which looks like white spots. The Magnesium being a more reactive metal will help avoid this.
Bear in mind, this is my experience, in our plant, but it worked and still works, every day. All I can hope is that it does so for you, should you try it. There is much more theory behind this, that I'd need to brush up on, if I were to give a more in-depth explanation of the science behind it. Also, it's not like we invented the wheel, someone else did, years ago.
Best of Luck!
Technician - Denmark
May 25, 2022
Thanks, M! There IS something new under the sun :-)
A fuller discussion of magnesium sacrificial anodes for aluminum anodizing can be found in thread 1594 but it never occurred to me that white spots could be "rectified" this way.
Regards,
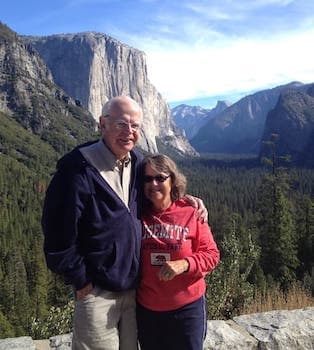
Ted Mooney, P.E. RET
Striving to live Aloha
finishing.com - Pine Beach, New Jersey
May 2022
----
Ed. note: For additional perspectives on this subject, please see letter 14441, "White spots in black anodizing".
Q, A, or Comment on THIS thread -or- Start a NEW Thread