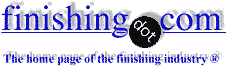
-----
White spots in anodizing
Quickstart:
Readers who are unfamiliar with anodizing of aluminum and its lingo may wish to start with our "Intro to Aluminum Anodizing".
There are many potential causes of white spots on anodized aluminum, so not many truisms can be offered. Robert Probert's "Where Do 'White Spots' on Anodized Aluminum Come From?" is a good introduction, and thread 437/77 also addresses this same problem.
With so many possible causes, a lot of data must be supplied for readers to help you find the most likely cause. Read on ...

Q. I have an anodising production line for aluminium billets and extrusions. I am currently experimenting with anodising aluminium castings, but white spots are appearing at random locations. Is there a process that needs adjusting when anodising billets/extrusions compared to castings? I am using type 2 anodising with electropolishing preparation, followed by desmutting. The anodising parameters are a temperature of 22 °C and a current of 1.4 A/dm2 for 30 minutes. The aluminium casting is made with a mixture of pure aluminium and waste aluminium billet (series 6) in a 1:1 ratio, with degasser tablets and drossing flux added during the manufacturing process.
Faisal Aprialdi- Indonesia
May 2, 2025
A. Hi Faisal,
You'll see that we moved your inquiry to a different thread than you submitted it on; this thread seems to offer more suggestions with regard to castings. The first question I would have is whether the spots appear on raw casting surfaces or on machined areas of the casting because machining will open up porosity. Robert Probert, among other posters, offers some excellent advice below.
Luck & Regards,
Ted Mooney, P.E. RET
Striving to live Aloha
finishing.com - Pine Beach, New Jersey
Q. The aluminium casting that I used has been machined. Is the white spot a defect in the anodising or the casting material? Because I used the same anodising parameters on the aluminium billet and extrusion, and there were no problems.
Faisal Aprialdi- Indonesia
May 5, 2025
A. Hi again Faisal. I don't think "defect" is necessarily the right word or concept. When a square peg doesn't fit into a round hole I don't think it's necessarily a defective peg or a defective hole, but an incompatibility 🙂
Sometimes castings are poor quality and have too much porosity, but any time you anodize a casting you expose the porosity which all castings have to some degree, and it becomes necessary to adjust the anodizing and its pretreatment steps to minimize its effect on the product. Please carefully read the many informative comments on this page ....
- Ward Barcafer asks if you have a nitric acid dip after anodizing -- it is also recommended by Robert Probert and other readers. So that would be suggestion #1 if your process works fine on parts which are not cast.
Luck & Regards,
Ted Mooney, P.E. RET
Striving to live Aloha
finishing.com - Pine Beach, New Jersey
![]() |
Q. I've used nitric acid dipping after anodizing, I even tried neutralisation with baking soda but the white dot problem is still there.I've used nitric acid dipping after anodizing, I even tried neutralisation with baking soda but the white dot problem is still there. Faisal Aprialdi- Indonesia A. Greetings Faisal Retired - Newport, tenn |
Q. Thanks for the advice, is the additional time of about 10 minutes done with the same current density?
Faisal Aprialdi [returning]- Indonesia
A. Yes.
Do not let the parts become dry. give them a good water rinse after whatever tank they came out of when you saw the spots. then take them back to anodize tank with same current. Just double check to be sure you are drawing current.
Retired - Newport, Tennessee
May 13, 2025
Ed. note: Please let us know how this works out, Faisal.
Q. I have ensured good water rinsing and did not dry every process in anodizing. The spot is clearly visible after sealing. I have also tried to add an additional 10 minutes and even an additional 30 minutes, but the spot is still there. Now, I am trying to change the aluminium casting parameters in the hope that the spot will disappear. I will inform you further of the results.
Faisal Aprialdi [returning]- Indonesia
⇩ Related postings, oldest first ⇩
for Shops, Specifiers & Engineers
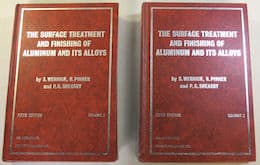
avail from eBay, AbeBooks, or Amazon
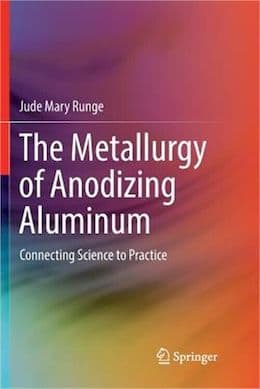
avail from eBay, AbeBooks, or Amazon
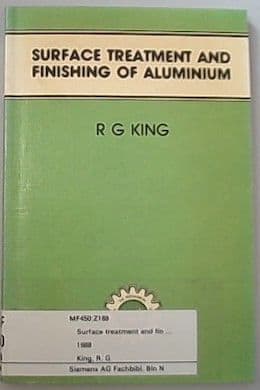
avail from eBay, AbeBooks, or Amazon
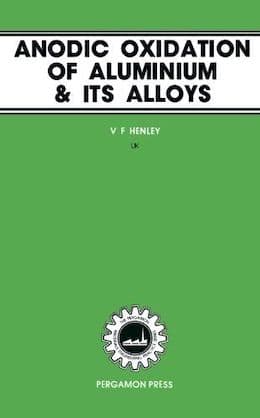
avail from eBay, AbeBooks, or Amazon
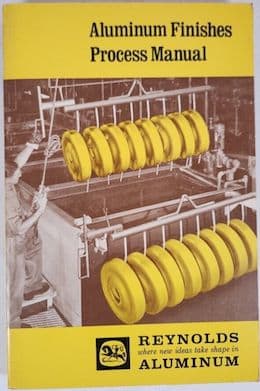
avail from eBay, AbeBooks or Amazon
(as an Amazon Associate & eBay Partner, we earn from qualifying purchases)
Q. Can someone explain the complete process with respect to Black Anodizing alum. castings (Alloy 771.2)
The problem we are having is white spots (after plating) on the milled surfaces but not on the raw casting surfaces. Could this have something to do with inner cavities trapping the chemicals used during plating? I heard from my co-workers that if the part is not baked properly or long enough after the cleaning that chemicals would leach out and cause the white spots. (Looks like exposed alum. surfaces not plated.)
If this is inherent with alum. castings, can someone suggest a different alloy that's less prone to having porosity present.
Bill Velazquez- Hauppauge, New York
2001
A. I have been anodizing for a little while and do not claim to know a lot but I have read and also experienced that cast alum. cannot be anodized, only forged alum. can be anodized.
Mike Lowery- Huntsville, Alabama
A. Bill, yes, due to the porosity of castings, producing a uniformly colored anodize is difficult but usually the opposite of what you describe would hold true.That is the milled surfaces would look even and the natural cast surface would appear spotty.The spots on the milled surfaces may indicate contamination from chemistry of blind holes or poor rinsing before dye.
Most wrought materials will be significantly less porous than any casting.
Bill Grayson- Santa Cruz, California, USA
A. This is the same thing that I am experiencing, the lab states it is Si segregation; is the material high in Si?
Maybe together we can help each other.
Regards
Wendell Goodson- Garland, Texas
Q. Good Afternoon Weldon,
I am glad I am not the only one experiencing this problem. The alloy currently being used is 771.2 and it has a concentration of .1 of Silicon.
By the way our foundry has recommended we try 356 T6. I personally do not believe it's the alloy but more the lack of internal controls at the foundry which leads to impurities and pin holes developing in the castings. But in any event we will give 356-T6 a try to see if we have positive results. The only other option is to machine from solid material. Come to think of it , 356 T6 has a much higher concentration of Silicon 6.5 to 7.5, so maybe high concentration of silicon may not be the cause. Where's all the platers out there, come on guys, you must have a solution to this problem or how about all you foundries, help us out here, please.
Bill Velazquez [returning]- Hauppauge, New York
A. This is a common issue when dealing with porosity such as anodizing castings or jig plate, plating zinc die castings, etc. Certainly, castings can be anodized they just are not going to look as pretty as a nicely machined extrusion will. There are a number of techniques that can be used to mitigate the effects of porosity and how well they work depends upon the finisher's expertise and the nature of the porosity encountered.
One of the issues may not be the cleaning chemicals leaching out but sulfuric acid leaching out following the dying/sealing process as sulfuric is viscous, etc., and it will dissolve away the coating and remove the dye as it bleeds out. That is particularly common with what you have described.
One method is to rinse in a rinse containing ~5% nitric following the anodize bath prior to the dye bath. That replaces the sulfuric acid contained in the pores with nitric which is much easier to rinse out (less viscous) as well as giving one a better coating for dying with slightly softened, wider pores.
Another technique used is to "pump" the pores following each bath with alternating hot water rinses and cold water rinses. Sometimes a neutralization bath with 10% bicarb can be used following the anodize bath.
Another technique is to use a spray rinse above each rinse tank. The one that has worked best for me in the past is the nitric pre-dye rinse. The amount of material being etched during the cleaning process also impacts the porosity problem, it is best to only bubble etch if etching at all, etching off the "skin" usually increases the porosity problem. Sometimes it may be best to just use a brief triacid etch and avoid any alkaline cleaning and employ a nitric pre-dye rinse.
There are finishing houses that have the expertise to deal with the problem you have encountered and rather than just trying wholesale what I have mentioned above I would suggest you try having your parts processed at a finish house that specializes in decorative color-match anodizing, or find someone who is used to black anodizing jig or tool plate. Some castings are not going to anodize as well as others not only due to the alloying constituents but because the casting process can lead to varying amounts of porosity within the same alloy being cast.
Ward Barcafer, CEFaerospace - Wichita, Kansas
Q. Hi,
I am having these tiny white spots on Black Anodized parts. They are not too many but many enough to get rejected in the quality check. Any creative thoughts as how to avoid this problem?
Thanks,
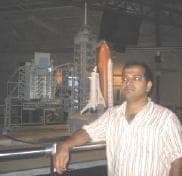
Hemant Kumar
- Florida, USA
2002
![]() |
A. Is your part a machined casting? Machining on castings invariably open up pores in the casting which entrap a small amount of sulfuric acid during anodizing and then bleach out the dye after dyeing and sealing. If this is the case, you might allow the parts to soak in a warm rinse for a while to help the acid leach out before dyeing. Don't make it too hot or you will seal the anodize. Even this might not work because you never know how much acid has soak into the pores. Sometimes the spots don't appear for a long time. Good luck. Guy Lester- Ontario, California, USA A. This is the most common tech service complaint. If you are using 7075 alloy, note that all salts of zinc are white. Calcium buildup (evap., add, evap., add, etc.) in the dye or seal will leave behind white spots. Chlorides anywhere will sometimes show a white spot. Too high dissolved aluminum in the anodizing, like above 12 gm/L, will cause white spots. Dirty rinse water can cause white spots. sulphate drag into the dye, especially with 7075, will cause white spots. Plain nitric deoxidize on high alloy does not get rid of the non-aluminum alloying ingredients - use a proprietary iron based deoxidizer. First thing to try: 5% Nitric Acid Dip between the anodizing and the dye. Start looking for pits and white spots after the anodizing, then look at the dye, then look at the seal, Take two aspirin and call me in the morning. ![]() Robert H Probert Robert H Probert Technical Services ![]() Garner, North Carolina ![]() |
A. Another possibility would be that you are getting galvanic corrosion during the dyeing process.. make sure your work is completely insulated from the tank during dyeing.
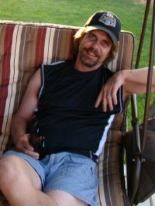
Marc Green
anodizer - Boise, Idaho
A. You did not mention if you use DI water or tap water. If you use tap water for your operation. Chloride ions may be the reason to cause the pitting you have.
S. Y. Yuen- Hong Kong, China
Q. We are having an ongoing issue with white spots on some pieces we black anodize. Parts are 6061 machined plates - not cast or jig plate. They come to us very clean. We have tried all different cleaning - soap only, no etch - heavy etch - etc.
The weird thing is that this is almost entirely confined to one account. We do black on 6061 all day long for others and do not see this issue. The customer tells me they use a water based machining oil and I spoke to the mfgr. of that oil and we see no problem.
We go through extensive rinsing & cleaning and still can't get rid of the issue. We have used both titanium & aluminum racks & it does not seem to make a difference - We have masked all holes, even when not needed & still no difference.
I have attached a pic - any input would be appreciated.
plating shop employee - Long Island City, NY USA
2007
A. Probably:
1. dissolved aluminium content high;
2. current density high;
3. bath temperature low;
4. it's not 6061.
- Singapore
A. David
It could be overaged aluminum, particularly if the spotting occurs only on non-machined surfaces. Try an acid (HF) etch before anodize.
- Colorado Springs Colorado
A. I'm sure you've considered this, but any chance that your customer's finishing operation could be embedding particles not compatible with anodizing in the part?
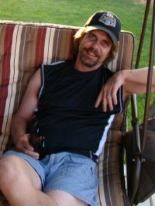
Marc Green
anodizer - Boise, Idaho
2007
Q. We have a problem in black anodizing bath per attached pic.
As we have seen, there are lots of white spots over there, as if pores of surface not filled by black color. But interestingly, it occurred only on this profile. On another profile which is black anodized in same bath, we didn't see any [white spots]. All profiles are extruded 6063 series and electrocoloring bath's composition is 2 gr/lt Sn and 20 gr/lt sulfuric acid and 40-50 gr/lt stabilizer. But I don't suppose it's related to bath. So I want to ask generally;
1- is this problem related extrusion quality?
2- is this problem related our anodizing process?
3- our electrocoloring bath's duration (for black color) is about 20-25 minutes. Is that too long for black color? (we check electrical reasons).
Sincerely
- sakarya,turkey
March 14, 2014
Q. I am really hoping someone can help. We are having severe spotting on 356-T6 machined castings. This gets worse from time to time and the vendor always says it is porosity and there is nothing they can do, fix your casting.
From reading this thread does the test plan below seem logical?
1) run 10 parts using a 5% Nitric rinse and compare?
2) run 10 parts using pump hot cold alternating rinse and compare?
3) run 10 parts using 10% bicarb and compare
Is there anything else I should try other than a new vendor?
RFQ: I will take suggestions for the new vendor as well:-)
Paul Dykstra- Shelbyville, Illinois, USA
November 18, 2014
A. The white spots are very probably caused by the pores in a casting. If you have visible pores, there is not much that the anodizer can do.
Vacuum impregnation would seal the pores, but they would not anodize, so you would have the same problem.
A new source of the castings might help.
- Navarre, Florida
A. Hi Paul,
There are a couple of things you could do to try and improve the integrity of the castings. Firstly you can try Hot Isostatic Pressing (also known as HIPping). Secondly you could try vacuum impregnation (usually done with a sodium metasilicate type material).
Both of these techniques are designed to either reduce or mitigate the effects of porosity.
If you have a big problem with porosity then you need to look at the casting technique. I am not a casting expert so really can't advise other than to say try a consultant if this is really a big problem.
Aerospace - Yeovil, Somerset, UK
November 19, 2014
Ed. note: James' and Brian's postings preceded the addition of the photo to the thread. Their suggestions may or may not change after they see the graphic.
![]() |
Q. We use a lot of Aluminum castings. However, we only have one customer that requires Anodizing for corrosion resistance. In our opinion the porosity is not that severe. The strange thing is that porosity seems constant bu the spots come and go. I have not tried HIP'ing these parts but am familiar with the process. We have tried impreg and it did not help. - Shelbyville, Illinois, USA A. Paul - Colorado Springs, Colorado A. Good day Paul. - Whitby, Ontario, Canada |
Thanks to everyone for the feedback. I sort of lost track of this thread before the holidays. We will try some of the suggestions and I will report back the results!
- Shelbyville, Illinois, USA
January 4, 2015
Q. Hi All,
My customer's part found having white patch on thread holes of the part after anodic coating as per MIL-A-87625F, CLASS 2 BLACK.
The material is Forged Aluminium 500.
I need some advice to tackle this matter.
Cheers,
Kabilan
- Singapore
April 28, 2015
A. Hi Kabilan. As you see, there have been photographs posted, specific suggestions offered, recommendations of books given, etc... it can be a complex matter which will require you to post a lot of data. Still ... threads are usually not anodized, and are therefore usually aluminum colored rather than black. Are you sure you are seeing "white patches" as opposed to non-anodized threaded areas which your anodizer deliberately avoided anodizing? Thanks.
Regards,
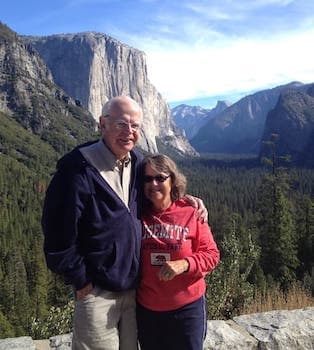
Ted Mooney, P.E. RET
Striving to live Aloha
finishing.com - Pine Beach, New Jersey
Black spots on black dyed sulfuric anodizing with hot water seal
Q. Dear All
I am a technologist and Lab head Al finishing plant.
Black dyed sulfuric anodized with hot water seal produces white powder.
The sealing sol'n consists of RO water with dilute phosphoric acid and sodium hydroxide. Very light sol'n... pH adjusted to 5.5-6.4.
RO cascade rinse is performed before sealing.
The process initially runs fine, but the tanks lasts for a very short time until white powder appears on black parts.
I noticed that the pH rises with time.
I will be appreciative for any assistance.
Best regards
Shay
chemist - Israel
October 17, 2018
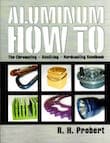
Aluminum How-To
"Chromating - Anodizing - Hardcoating"
by Robert Probert
Also available in Spanish
You'll love this book. Finishing.com has sold almost a thousand copies without a single return request :-)
A. Hello Shay. Are you sure you mean 'black spots'? From the context of your question it sounds like the problem is white spots, which is perhaps the single most common problem discussed on fnishing.com. Robert Probert offers an article about it in our on-line library, and we have about 35 to 40 threads on the subject if you search the site with the term "white spots anodize".
But I am not familiar with your seal with H3PO4 and NaOH in it. You call it a hot water seal ... is it boiling? Thanks.
Regards,
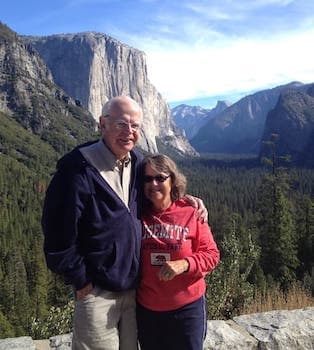
Ted Mooney, P.E. RET
Striving to live Aloha
finishing.com - Pine Beach, New Jersey
Q. Hi Ted,
Thanks for the article, and prompt response.
I have indeed obtained white spots on Aluminum treated with Sulfuric Anodize and dyed in Black. Thus, the white powder is seen well on black background. I think the water seal is the problem.
I use a hot water seal (close to boiling) which contains very low concentrations of phosphoric acid and sodium hydroxide. The pH is adjusted to 5.5-6.4.
I have bought the Aluminum How-To book from your website; excellent book, and read it all. The website is the best in the field, and I highly appreciate the great work you personally do.
I will read the article.
By the way, how do I look for further articles at the website?
Many thanks Ted.
Shay
Algat - Haifa, Israel
Hi Shay. Thanks for the very kind assessment of our efforts. Although I've acquired some limited knowledge from books and by osmosis, my hands-on experience is in plating & anodizing equipment and shop design more than troubleshooting appearance issues in anodizing. Still, as we both know, Robert Probert emphasizes how essential the purity of your seal tank is. Hopefully he'll come across this thread at some point and comment.
As for finding articles on this site, our search engine uses Google but restricts it to searching just this particular site ... I use it dozens of times every day myself :-)
Regards,
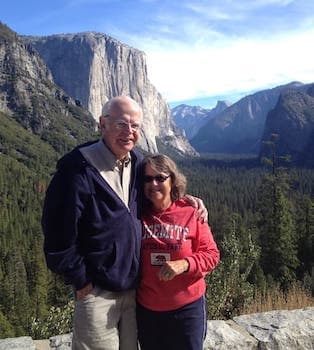
Ted Mooney, P.E. RET
Striving to live Aloha
finishing.com - Pine Beach, New Jersey
![]() |
A. Hi Shay, - sakarya,TURKEY A. If I were to hazard a guess here, are you using phosphoric acid and sodium hydroxide as a method to control your seal pH? If so, I would stop that immediately and use acetic acid ⇦ on eBay or Amazon [affil links] and ammonium hydroxide for your adjustments. I'm thinking your spots may be related to the use of NaOH. ![]() Marc Green anodizer - Boise, Idaho |
A. Marc Green has your best answer. Phosphate is a terrible contaminant to any seal. Do what Marc says, but first go back to the anodizing tank, rinse, then 5% nitric acid to flush the viscous white aluminum sulphate out of the pores (which pops out at the hot seal), then rinse again.
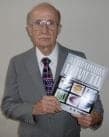
Robert H Probert
Robert H Probert Technical Services

Garner, North Carolina
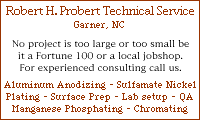
October 20, 2018
Many thanks to you all.
It has been very useful.
I will sure make the changes are mentioned.
Algat - Haifa Israel
Q. Hi all, we've been observing white spots around the welded areas of some of parts that we do black anodising on. It typically happens 1-2 white spots per part and exclusively on the weld areas of the part. As much as I believe it's a welding problem (please enlighten me if I'm wrong), is there anything that I can do on my end to eliminate these white spots?
Kai Tan- Singapore
November 1, 2021
A. Hello Kai.
Without actually seeing a picture of the condition that you are seeing, more than likely you are correct. The white spots do lend themselves to the issue of the welding. One thing that you may be able to try is after the black dye, return the parts back to the anodize tank for about 5 minutes at the same voltage as was used to process the parts. Many times the white spots will fill in after parts are dyed again. you might also try some black touch-up paint if that would be acceptable for your customer.
Other than that I would suggest that it is gong to be a condition that will have to be lived with.
supervisor - Cicero, Illinois
Saporito Finishing Co.

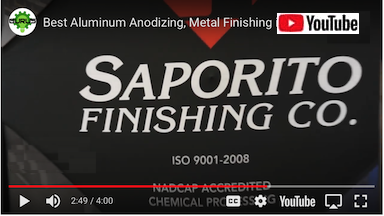
A. Not wanting to start an argument, because the suggestion might be related to electrolytic coloring (which I have no experience with), but white spots on welded areas are usually a result of porosity, these pores may be very deep and trap sulfuric acid, which leaches out during dyeing (or even later during hot sealing) and prevents dye absorption or ruins the dye around the pore, and, if regular water soluble immersion dyes are involved, then I can't see how returning the part back to anodizing tank will improve anything at all...
Improve welding practices, longer rinsing times, perhaps the short 5% nitric rinse suggested by others may also help to get the sulfuric out, these would be my primary choices to try and solve the problem
This is if the defect is indeed caused by the trapped sulfuric acid and not some other contamination of the process, high magnification pictures with scale next to defect would help to understand better what might be the problem
- Riga, Latvia
A. Janis,
what you are proposing is 100% correct. The white spots are related to solution entrapment, but this is the same principle when it come to anodizing castings that have machined surface(s). The sulfuric becomes entrapped in the pores which become more visible after machining and leaches out at the most inopportune time. Returning the castings back to anodize for a few minutes generally improves the appearance minimizing the white spots and allowing for more dye absorption. we see this situation quite regularly and the results of returning to anodize tank for about 5 minutes and dyeing again improves the visuals dramatically and sometimes the white spots are dyed and completely disappear. there is no guarantee that the white spots will always react favorably to the additional treatment but it is a very real possibility that they will be minimized greatly.
supervisor - Cicero, Illinois
Saporito Finishing Co.

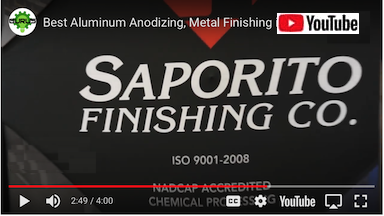
Q. Hello
We are currently running an automated anodizing line and having a consistent white spot failure mode on a certain part.
This process has been done in the past successfully (10,000+ pcs), this same failure mode consistently on this part the last 6 weeks.
We are continuing to run this recipe on other production parts with no issues.
We are currently performing modified hardcoat at a thickness of .0015" @ 55 °F @ .166 amps / in^2 @ 24v
Current material being used is extruded 6061-T6 tube stock.
Rough material is .750 turned to .724 finished diameter.
We have had another anodizing shop run the same parts with the same material - lot and heat - with success.
Current Process:
Tumble
Electro-polish
-racking on titanium split fingers-
Caustic Soap
Rinse
Caustic Etch (130 °F)
Primary Rinse
Secondary Rinse
De-Ox
Primary Rinse
Secondary Rinse
Hardcoat (current conc. @ 175-180 grams/litre sulfuric w/ anti-burn agent AA200 @ 4gram/litre)
Primary Rinse
Secondary Rinse
Nitric Acid Neutralizer
Rinse
Dye Rinse
Hot DI Water Rinse (130 °F)
Black Dye (130 °F)
Dye Rinse
Hot DI Water Rinse
Seal (MS-1)
Boil Water seal
- Chesterfield New Hampshire
December 28, 2023
A. Hi George. There are so many potential causes that it's hard to start. But if another shop is successfully processing them, my first question would be whether they are also using titanium racks.
Another thing to note is that while both illustrated parts exhibit little white dots, that 'morse code' pattern on the second part is certainly not some random chemical phenomena; it's obviously orderly and is certainly either damage to the part during processing or defective material.
Luck & Regards,
Ted Mooney, P.E. RET
Striving to live Aloha
finishing.com - Pine Beach, New Jersey
Q, A, or Comment on THIS thread -or- Start a NEW Thread