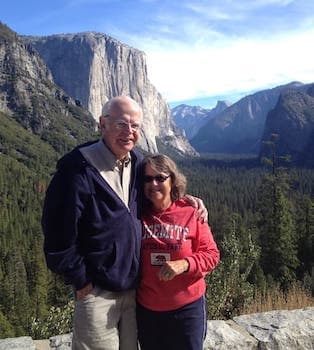
Curated with aloha by
Ted Mooney, P.E. RET
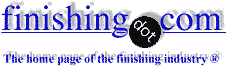
The authoritative public forum
for Metal Finishing 1989-2025
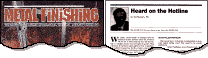
-----
Pitting in aluminum anodizing seal tank: Magnesium anodes vs. rectifiers

⇦ Tip: Readers want to learn from Your Situation 🙂
many readers skip abstract questions.
Q. Are there any fool proof methods for eliminating stray currents from stainless steel anodise seal tanks?
Fred P Hayduk- Wadsworth, Ohio
June 4, 2024
Ed. note: We appended your inquiry to a related thread so you'll have some ideas to review while you await personalized answers.
A. What's wrong with your anodized parts?
Are you sure source of problem is "stray current in sealing bath"?
The only way I know to prevent stray current issue is grounding between bath and ground with a cable.
- Sakarya Turkye
June 5, 2024
⇩ Related postings, oldest first ⇩
for Shops, Specifiers & Engineers
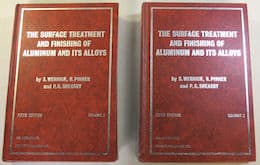
avail from eBay, AbeBooks, or Amazon
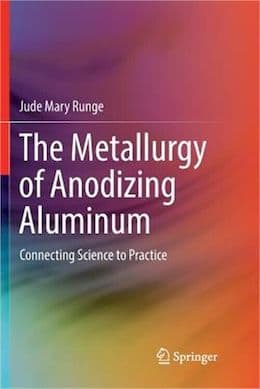
avail from eBay, AbeBooks, or Amazon
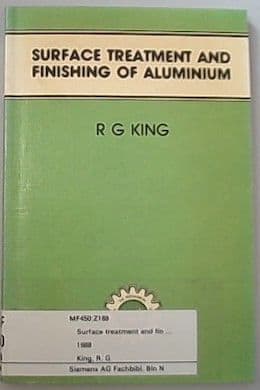
avail from eBay, AbeBooks, or Amazon
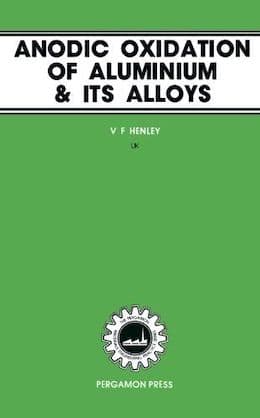
avail from eBay, AbeBooks, or Amazon
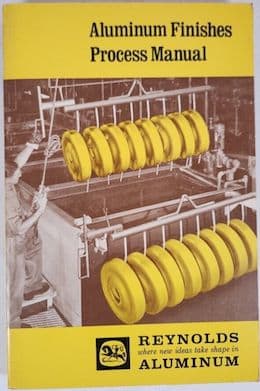
avail from eBay, AbeBooks or Amazon
(as an Amazon Associate & eBay Partner, we earn from qualifying purchases)
Q. I would like to have information about how to set-up a Galvanic Corrosion Protector capable of preventing galvanic corrosion/pitting of aluminum parts processed on titanium racks in anodize dye and seal tanks. I know of at least one product on the market, but I would prefer to manufacture my own equipment to avoid high equipment costs.
Any help would be appreciated.
Bill Crider- Tulsa, Oklahoma
1998
A. Sir,
Your problem should be fairly easy to overcome:
A few things to try:
1) Put magnesium rods on sides of racks when in dye & seal. These rods are available from Servi Sure in Chicago.
2) There is a rectifier that puts out a current to negate the galvanic action taking place. I believe it is available from Vulcanium & possibly Servi Sure.
Get back to us if you would like more info.
David A. Kraft- Long Island City, New York
Ed. note -- Readers: This very helpful 1998 posting suggests brands & sources, but the decades have proven that the disadvantages of public brand/source suggestions outweigh the advantage. Please try to avoid suggesting brands & sources ( huh? why?)
A. Correct that magnesium is the best way to eliminate the galvanic corrosion since Mg is the only useful metal which is anodic to aluminum. If you attach the Mg bars to the rack, they will be corroded by the rest of the anodizing solutions. If you attach them to the tank they will protect the aluminum on the rack BUT will also provide galvanic protection to THE REST OF THE TANK. This means they degrade faster. The best set up is to attach them to metal pads which the work bar can set on. Make sure the Mg is in electrical contact with the pad and is in the solution. Insulate the pads from the rest of the tank (including the bolts if you bolt the pads to the tank). When the work bar is in place the circuit is complete (solution-Mg-pad-work bar-rack-Al parts) and the Mg is the most anodic of the circuit. When the work bar is removed the circuit is broken and the Mg doesn't give up the electrons.
Lee Branch- Richmond, Virginia
Ed. note: Very insightful suggestion, Lee. Thanks!
Magnesium Bars to eliminate Current in Post Anodize Treatments
Q. Hi,
We have been experiencing major galvanic pitting in anodizing 7075 T6 aluminum parts. Out of our nickel acetate seal, the parts looks as though someone sprinkled salt on them, and as you wipe away the salt, black pits are very apparent.
We are racking on a Ti Hi-Lode racking system, and has come to our attention that the difference in conductivity between the Aluminum Part and the Ti rack, along with Ti's ability to be a capacitor out of the anodize bath is creating a potential causing this pitting.
We have added Magnesium bars to the bath, and when connecting the bars to the flight bar via a copper cable, the problem was eliminated in small test lot Qntys. Now, we have begun to increase the square footage, and the pitting is reappearing. Is there a ratio of magnesium to Al, Ti, Tank volume. etc. that needs to be maintained? Why are the Ti racks discharging in the Nickel Seal as opposed to the dye? Any information on the use of Magnesium in post anodize treatments would be greatly appreciated as this information seems hard to find and our chemical supplier seems to not be too familiar with the practice.
Plating/Anodize Employee - York, Pennsylvania
October 4, 2010
A. Jordan
The magnesium rod is a sacrificial anode, designed to pit/corrode before the aluminum does. Personal experience shows that they do work better when they are electrically in contact with the titanium racks -- hung on the same bar. If your tank is SST, the phenomena can be worse. I have only seen this happen in the dye with heavily alloyed aluminum. If your dye tank is the same material as your seal tank, it might suggest a contaminant such as chloride. Do you use DI water to make-up and top-off?
- Colorado Springs, Colorado
Q. Thanks for your response Willie. The tank is polypro, and was made up with DI water, however during a period of DI regeneration, the tank was topped off with City water. Our city water is of decent quality, and in fact, our dye tanks were made up completely with city water. In any case, the thought of contamination in the seal bath has crossed my mind before. I will research chloride levels in post anodize treatments and run a chloride analysis on the bath. Some other interesting details about this issue: After connecting the magnesium bars directly to the part load, the pitting was removed completely from the outside of the part, the only occurrence of pitting appears on the inside of the part where solution has the chance to pool (these parts are conical and racked in a horizontal fashion).
Jordan Somerville [returning]- York, Pennsylvania
A. Read the galvanic voltage between the stainless steel and the titanium. Double check the pH in dye and seal, then use a small lab rectifier with the positive on the stainless steel heater and the negative on the titanium rack (this is the reverse of the voltage you earlier read), turn the voltage up to whatever you previously read (probably 1.08 volts) and hope you have enough amps for the area.
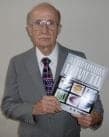
Robert H Probert
Robert H Probert Technical Services

Garner, North Carolina
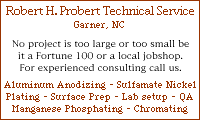
Q. Thank you for your response Robert (Thanks are extended for your numerous other posts throughout this website which have helped me troubleshoot numerous problems). I have checked the V potential between my SS coil and Rack and have come up with ~1.08 Volts as you predicted. Was this value determined though the difference in Oxidation/Reduction Potentials of SS and Ti (I am having trouble finding good information on the voltage potentials of these metals)? Or what lead you to suggest this number? These same voltages can be seen throughout the circuit we have created from the rack to the mag bars mounted on SS angle iron on the side of the tank.
To me, this would suggest that we are successfully removing this galvanic current. We have recently installed Di-electric unions on our steam coils to eliminate outside sources of current. Thanks you for your continued input.
Jordan Somerville [returning]- York, Pennsylvania
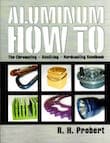
Aluminum How-To
"Chromating - Anodizing - Hardcoating"
by Robert Probert
Also available in Spanish
You'll love this book. Finishing.com has sold almost a thousand copies without a single return request :-)
A. The 1.08 comes from the many times I have seen it, that is why I published it in my book. The insulated unions will help from any other "stray current", either induced or galvanic, but it will not help with the voltage between the titanium and stainless steel in the tank. Again, use a lab rectifier. One of the rack companies used to sell a small rectifier for this purpose, but then they learned they can make more money selling magnesium bars.
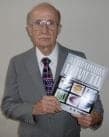
Robert H Probert
Robert H Probert Technical Services

Garner, North Carolina
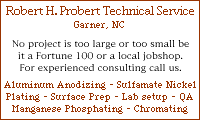
The rack manufacturers offer magnesium bars to afford authors & consultants an opportunity to earn a living suggesting a different tack :-)
Regards,
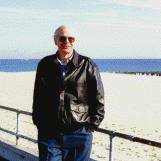
Ted Mooney, P.E.
Striving to live Aloha
finishing.com - Pine Beach, New Jersey
? Although I've been out of the "job shop" business for many years, I can't fathom why anyone would want to use SS tanks nowadays for any of their process tanks in an anodizing line. I've used poly-pro for many years (except for my hi temp seal tanks) and never had an issue. Albeit, I no longer do dyed work.
Can someone tell me any negative to using plastic tanks for dyeing?
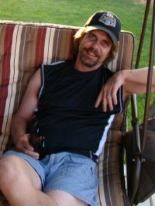
Marc Green
anodizer - Boise, Idaho
A. Marc, someone in the past was sold the tanks and if they are taken care of, they last an extremely long time.
James Watts- Navarre, Florida
A. A final idea regarding why the problem is worse in the seal tank than the dye tank is that nickel-bearing seals are probably more conductive than dyes.
Luck & Regards,
Ted Mooney, P.E. RET
Striving to live Aloha
finishing.com - Pine Beach, New Jersey
Q. I have an automated line with SS saddles and pick-ups for my flight bars. If I put something in between my saddles and pickup to insulate them from my flight bar, would it stop the pitting or would I need the magnesium rods?
Robert Rea- Keene New Hampshire usa
June 8, 2015
A. Your text was a bit brief and I am not sure I understand you. If the titanium rack full of anodized (insulated) parts is submerged in a dye solution in a stainless steel tank - then you have galvanic corrosion, pitting, etc, of the anodized aluminum parts. The titanium is positive, the stainless steel is negative, about 1.08 volts as I say in Aluminum How-To.. You can take the parts off the titanium and hang them on aluminum or stainless or plastic and the parts will dye with no attack.
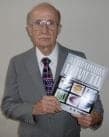
Robert H Probert
Robert H Probert Technical Services

Garner, North Carolina
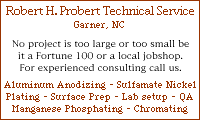
Hi Robert Rea,
It seems to me that you are suggesting that you will make a change which will prevent any metallic contact between the racks and the stainless steel tank; that should help, but doesn't guarantee that there will not be galvanic corrosion problem anymore :-(
Hi Robert Probert,
Yes, his text is brief, and I'm not clear whether he has aluminum racks or titanium racks. Lee Branch suggested a good way to implement magnesium anodes, and you have suggested the alternatives of a small rectifier to offset the galvanic current, or re-racking on compatible racks. Sounds to me like you guys have it all covered -- thanks!
Regards,
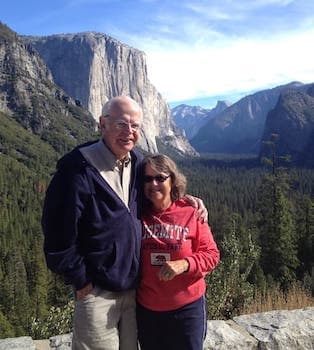
Ted Mooney, P.E. RET
Striving to live Aloha
finishing.com - Pine Beach, New Jersey
Pitting on green dyed anodized parts, but not black dyed parts
Q. Hello,
We are having some issues with anodized parts from an outside supplier. We get the same parts anodized with both green dye and black dye. We are seeing some pitting on parts that have been dyed green. When the parts come they look fine, but after oiling and being put on a machine that puts the parts through several repeated movements, we are seeing (what we think) is pitting. Both the green parts and black parts go through the same oiling and movement process, but the pitting is only occurring on the green parts. While the parts are moving, nothing rubs against the area that is pitting. We recently changed the type of oil we use, but again, the black parts get the same oil and we are not seeing any issues on the black parts. I was told there were similar issues with the old oil, so I don't think it has anything to do with the oil. I attach a photo to try and better convey the pitting, if it is pitting.
Could it also possibly be some kind of build up? I am relatively new to surface finishing chemistry and we have never seen this issue from the baths in our facility, just this outside supplier. We are going to try to work with the supplier, but would like to have some idea what is going on before we go back them. This is happening on nearly 50% of parts.
Thank you for any insight.
Danielle
metallurgy lab employee - Gallatin, Tennessee, USA
June 5, 2017
A. I suspect her black dye tank is plastic but her smaller green dye tank is stainless steel; then the galvanic current from the titanium rack to the stainless steel is pitting the anodic coating. Take some parts off the titanium rack and hang on SS or plastic and see if the problem goes away.
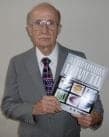
Robert H Probert
Robert H Probert Technical Services

Garner, North Carolina
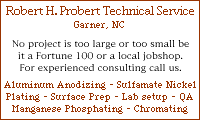
Q, A, or Comment on THIS thread -or- Start a NEW Thread