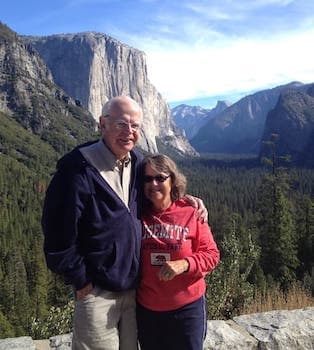
Curated with aloha by
Ted Mooney, P.E. RET
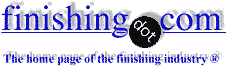
The authoritative public forum
for Metal Finishing 1989-2025
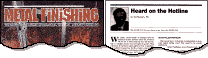
-----
System for Phosphate Removal from fasteners
Q. How to remove phosphating layer on the part without disturbance. (This is affecting on Induction Hardening).
Mukund Maruti Yadavself - PUNE, Maharashtra, India
June 27, 2019
A. Hi Mukand. We appended your inquiry to a thread where a similar question was already answered. Second opinions and further exposition can be found on threads 5957, 4175, 36207, 54141, 11442, 15099, 41670, 0914. Search the site for still more. Good luck.
Regards,
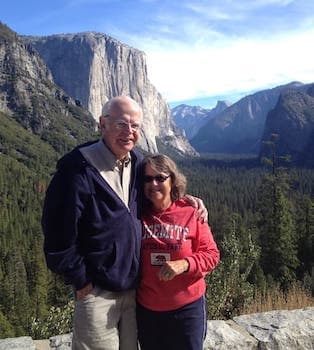
Ted Mooney, P.E. RET
Striving to live Aloha
finishing.com - Pine Beach, New Jersey
June 2019
⇩ Related postings, oldest first ⇩
Q. I don't think anyone has a solution for me but ... I would like to set up an in line parts washer that would not only clean my fasteners, but also remove the phosphate coating off the wire. The coating weight is approx. 1000 mg.per sq. ft. The emersion time will be only one to two minutes, due to the speed of our header machine. I can't use any acids due to our customers specs. Is there anything else we can use? Also, is there any way to determine if all the phosphate coating has been removed? Sincerely,
Mike adams- Rockford Illinois.
1999
A. Mike- Your parameters are pretty constraining, but phosphate removal before fastener forming is very common. A caustic, chelated cleaner running at near 200 °F should do the trick, although only 1 or 2 minutes should really be 4 or 5 minutes to get a good strip
As for the test, sure. A copper sulphate
⇦ this on
eBay or
Amazon [affil links] test can be used to check for complete phosphate removal. Hopefully this helps. Good Luck.
chemical process supplier - Gurnee, Illinois
1999
A. I agree with Dan, that a chelated caustic stripper would fit the description that you are looking for. However, you mentioned that your customer does not want you to use acid to descale. Why is that? Is it because of hydrogen embrittlement? If that is the case, you can use an organic acid such as citric acid
⇦ this on
eBay
or
Amazon [affil links] to descale the phosphate coating. Organic acids, unlike mineral acids such hydrochloric and sulfuric acids, do not impart hydrogen embrittlement. To strip the coating in the extremely short time that you have available, you may have to go to a solution of about 8-10 oz./ gal. of citric acid , at a temperature of 160 °F or more. citric acid is relatively expensive to use, compared to mineral acids, and you run the risk of chelating heavy metals when waste streams are co-mingled in your waste treatment system.
To test whether you have stripped off the phosphate coating, use a spot test with 5% molybdate (sodium or ammonium is ok), acidified with 30-40% nitric acid. This forms the blue phospho-molybdate complex which would be a positive test for residual phosphate coating. If a non-blue dark spot forms, this indicates that all of the phosphate has been stripped. You can use this test regardless of the strip used. If you use a phosphoric acid-containing strip, ensure that you have very good rinsing prior to the spot test, as the Phosphoric acid will interfere and give you a false positive result.
- Euclid, Ohio
1999
Q. Have a good day Sir;
I am kindly in asking you about the phosphate finish area, because I make the reception of drilling stabilizers but I have doubt that thread connections not be phosphate if there is a method of knowing if that or not.
-I expect your cooperation-
Best Greetings.
drilling company - OUARGLA, ALEGERIA
September 8, 2013
Q, A, or Comment on THIS thread -or- Start a NEW Thread