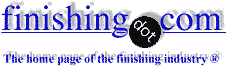
-----
Sulfur embrittlement of Ni sulfamate platings
Azodisulfonate & AUP/"magic stress reducer"
Q. Hi,
This post is very interesting! I work with nickel baths and especially with a nickel sulphamate bath. As I can see and understand from this post and many papers, azodisulfonate is produced in this type of bath by oxidation of sulphamate at the anode (platinum anode or pure nickel anode). This azodisulfonate will induce a compressive stress in the deposit.
I suppose my nickel sulphamate bath contains this azodisulfonate as the stress remains slightly compressive, even if the concentration of sulphate is very high. For information, I use pure nickel anodes and platinum anodes. Then I would like to find a method to analyse this azodisulfonate. Do you know an analytical method to do that? Does it exist a standard solution of azodisulfonate we could buy to have a reference for our analyses?
Thank you very much for your help,
Best Regards
- Berne, Switzerland
January 28, 2025
A. Hi Thomas.
Sorry, I don't know how to analyze for azodisulfonate, but agree that the topic is really interesting. I believe that AUP or "magic stress reducer", an organic that is created from the sulfamate under the right conditions with pure nickel anodes, also produces compressive rather than tensile stress. This is not the same thing as azodisulfonate according to Watson, and is superior because it does not cause high temperature embrittlement as azodisulfonate does. While awaiting some info about analysis, you or other readers might be interested in these writings:
• Dr. S Alec Watson, wrote a paper about how to engineer AUP "magic stress reducer" production, via an auxiliary plating compartment with pure nickel anodes.
• James Watts in thread 259/30 describes using insoluble anodes to produce azodisulfonate.
• Berl Stein offers a paper "Controlling Stress in Electroformed Metals" in our on-line library.
• Daryl Engelhaupt did some remarkable stress-free electroforming for the U.S. space program at Marshall Space Flight Center.
• If you've got $40 to spare, "Studies on the anodic decomposition products of sulfamate" by H. Zhang & S. -M. Park might be interesting.
Luck & Regards,
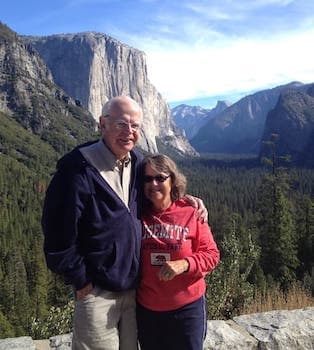
Ted Mooney, P.E. RET
Striving to live Aloha
finishing.com - Pine Beach, New Jersey
Q. Hi everyone,
Thank you very much for your reply Ted and these very useful information.
I am not sure to understand very well. The "magic stress reducer" produced at the anode (Pt or pure nickel anode that is passivated) is not this azodisulfonate? As I understood from different papers is that this "magic stress reducer" was indeed this azodisulfonate. Are you sure?
For an analytical method to measure this azodisulfonate, if someboby has an idea, let me know please. I find nothing on this analyze, but if some people detected azodisulfonate, there should be a method to analyze it, no?
Thank in advance.
Best Regards
- Berne, Switzerland
January 31, 2025
A. Hello again Thomas.
I have no expertise in the subject, but was paraphrasing the Dr. S Alec Watson paper I previously referenced. See his Section 3.1 "Stress Control in the Ni-Speed Process" where he discusses the differences between his magic stress reducer and azodisulfonate.
Luck & Regards,
Ted Mooney, P.E. RET
Striving to live Aloha
finishing.com - Pine Beach, New Jersey
⇩ Related postings, oldest first ⇩
Q. I am attempting to reproduce periodic sulfur embrittlement of Ni platings from a Ni sulfamate barrel plating process by using a Hull Cell
⇦ huh?
. The basic Hull Cell set-up is 267 mL with a NON-activated Ni anode, MgCl as a corroding agent, 2 Amps constant current, boric acid and wetting agent. A four decade old article by Greene suggests running the anode in the passivated condition to create reactive azodisulfonate that may codeposit with the Ni. Another suggestion is to use a sulfur activated anode (but literature from the suppliers of these anodes states that the sulfur is bound in a precipitate after dissolution of the anode and is not free to participate the plating process).
Can anyone offer inputs on these methods or suggest other bath variations/chemistries that may force sulfur to be codeposited with the Ni? Thanks
electronics manufacturing - Phoenix, Arizona, USA
2004
A. I very strongly doubt that sulfur depolarized anodes are the cause of the sulfur embrittlement. And while I am not a smart enough chemist to truly understand azodisulfonate and the "magic stress reducers" associated with nickel sulfamate plating, I doubt that they are the cause either. My understanding, inferred from people who are the smart enough chemists, is that these sulfur deposition problems invariably come from brighteners and leveling agents that someone deliberately put into the bath, or from oils of some sort that found their way in.
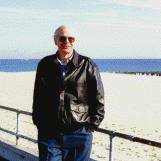
Ted Mooney, P.E.
Striving to live Aloha
finishing.com - Pine Beach, New Jersey
2004
A. I have never heard of sulfur depolarised nickel causing sulfur induced hardening or embrittlement. However, many additives, such as saccharin, have sulfur in their molecular structure and when they are co-deposited , they can cause sulfur embrittlement. This is only usually seen when the nickel is heated to over 160 °C - the higher the temperature the shorter the time needed to see it. At 160 °C it takes about 2 hrs.
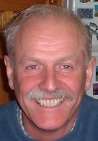
Trevor Crichton
R&D practical scientist
Chesham, Bucks, UK
2004
A. Sulfur depolarized anodes are definitely not a source for sulfur in the nickel deposition. During running a sulfamate electrolyte there is the possibility to create azodisulfonate, which is a source for sulfur in the deposition. The azodisulfonate is created at polarized anodes (Reasons for high polarization can be: To low chloride content, to high anodic current density, wrong anode material). Sulfur depolarized anodes help to prevent the creation of azodisulfonate even in low-chloride sulfamate bath.
Marcus Hahn- Lucerne, Switzerland
2004
adv.: Supplier of Copper Anodes, Nickel Anodes, Bismuth Metal, & Other Metal Products for Industry & The Arts
Q, A, or Comment on THIS thread -or- Start a NEW Thread