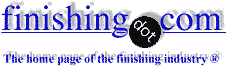
-----
Nickel sulfamate tensile stress blues
Q. We are a job shop and are required to control the tensile stress of our sulfamate nickel baths to a maximum of 9000 psi. It is generally understood that when stress is high, it is time to dummy the metal contaminants out. This usually works, but has lately not been effective for reducing the stress. The AA analysis showed very low contamination as well. I have also investigated other contaminants such as sulphate and ammonia. The baths did contain some, but I was not able to find information as to how these contaminants effect deposit stress. Any ideas? From a hotline letters search, I read mention of proprietary stress reducers. Would it be advisable to use these in my case?
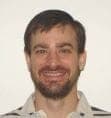
Jon Barrows, MSF, EHSSC
Kansas City
2003
A. You are probably right to keep hunting for contaminants.
I could be wrong but I don't think proprietary stress reducers are a big factor in nickel sulphamate plating. There is a "magic" stress reducer that is a byproduct of the breakdown of sulphamate, and which can be generated on an engineered basis by control of current density together with an auxiliary cell that uses pure nickel anodes. This may be overkill for plating, but is used to exactly control stress in precision electroforms. If you use the search term "magic nickel sulphamate" in our search engine you will see a lot of discussion about it and references to papers about it. Also see Berl Stein's article on line here about Controlling Stress in Electroforming. Plating is not electroforming, but there is some commonality.
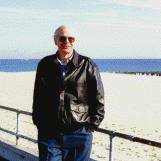
Ted Mooney, P.E.
Striving to live Aloha
finishing.com - Pine Beach, New Jersey
The following data might give you a ballpark. Stress increases around 0.3% for every part per million of ammonia ⇦ on eBay or Amazon [affil links] and slightly less for sulphate. There is no information about a method to eliminate ammonia.
Guillermo MarrufoMonterrey, NL, Mexico
When sulphamate breaks down it produces tensile inducing by-products of ammonia and sulphate. This can be due to overheating, so keep the temperature below 70 °C and preferably at or below about 60 °C. Stress can be reduced by adding sodium saccharin and this also hardens and brightens the nickel. Removal of sulphate is not easy and can be messy; the usual way is to add soluble barium salts, but I've never done it with sulphamate baths and don't know if barium sulphamate is soluble or not. ammonia can be removed by dosing the bath with activated charcoal, but that too is very messy. You may be able to remove it by doing a by-pass carbon treatment. Carbon treatment will take out most organic additives, but not all. Alternatively, dump the bath and begin again. If the stress builds up over time, look for contamination of the bath and eliminate its cause, otherwise it will return. If you want to use proprietary additives, you need to talk to a good supply house.
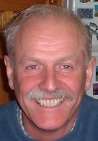
Trevor Crichton
R&D practical scientist
Chesham, Bucks, UK
A takeoff on what Ted said. Use a platinum clad anode for some of the delicate work or for getting into a LCD area and you will see a gradual drop in the stress. On a permanent basis you could set up a small cell and plate a SS cathode with a small platinum anode. Overflow this cell into the main nickel tank. It can be moved from nickel tank to tank as needed. We found this by accident several years ago. Normally it will only take a day or so a month to maintain a nice +4,000. No hardening was noticed. Some aerospace specs do not allow for the addition of saccharin, which breaks down and stress/additions will have to be monitored on a more frequent basis.
James Watts- Navarre, Florida
Thanks for all of the info. I am going to try Mr. Watt's idea for starters before trying to precipitate sulphate or dump the bath. Thanks.
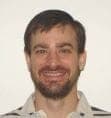
Jon Barrows, MSF, EHSSC
Kansas City
It worked great 40 amp-hours reduced stress 5000 psi in a 400 gallon tank. James Watts- I was aware that insoluble anodes reduced tensile stress, but I had it in my mind that in doing so I was creating harmful sulfamate breakdown products. Because of this belief, I have not allowed the use of insoluble conforming anodes for plating. As I see understand it now, there is no detriment as long as the use is controlled. Do you agree with this statement?
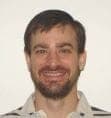
Jon Barrows, MSF, EHSSC
Kansas City
A. I hope it is ok as we used it for several years in an aerospace facility. You are correct in your thought that it does breakdown the sulfamate radical. This would be extremely bad if you tried to use nothing but an insoluble anode. As I see it, there is a small amount of breakdown anyway, so using an insoluble anode to control stress is not really out of reason. Besides, it is necessary to use one on a part now and then to get plating into a passageway or low aspect ratio hole. Sure works nice, doesn't it. Beats saccharin by a long way in ease of control.
James Watts- Navarre, Florida
Q, A, or Comment on THIS thread -or- Start a NEW Thread