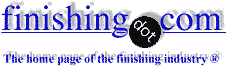
-----
Chrome plating of zinc die castings -- Problems & Solutions

by Safranek & Brooman
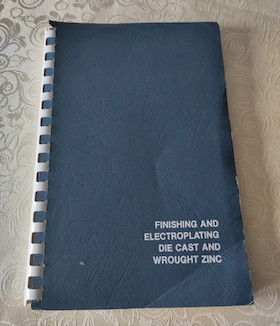
on eBay or Amazon
or AbeBooks
(affil link)
Q. Hello, I work in a facility that makes zamak 5 coating. I see pits on the coated parts. The pits I see after acid copper continue after chrome, what kind of path should I follow? Thanks.
Ilyas Ünal- Eski&sedil;ehir/Türkye
August 29, 2023
A. Hi Ilyas
Although your cyanide copper preceding your acid copper may not be thick enough, the most likely problem is probably that the diecastings are simply not plateable quality. The plating will not be satisfactory if you can see cold shuts or porosity in the castings.
Luck & Regards,
Ted Mooney, P.E. RET
Striving to live Aloha
finishing.com - Pine Beach, New Jersey
⇩ Related postings, oldest first ⇩
Q. We manufacture die cast parts. We have recently received an order to manufacture a die cast logo in zinc alloy (zamak). The part is to be chrome plated and it is expected to have a superior finish. We subcontract the plating to a local plating shop. As part of his process he buffs the parts manually and then does the plating. We have been facing high rejection on account of blemishes which seem to get highlighted after the buffing. Instead of hiding or minimising the defects, the buffing operation seems to enhance them! Is buffing essential or is there any other method we can use?
Please help!
Bomy Dabhoiwaladie casting shop, - Mumbai, Maharashtra, India
2004
A. Dear Mr. Bomy Dabhoiwala,
Here are suggestions that may help...
1. Vibratory finishing is the possible solution to uniform base metal finishing before plating.This will remove die casting flash & burrs and also even out the surface to provide a uniform base.
2. After good cleaning cycle the parts need to be plated with Cyanide Copper to minimum 4-6 microns.
3. Thereafter following good rinsing and 3% sulfuric activation the parts are plated in superior High leveling and Ductile Acid Copper process to a thickness not less than 12.5-15 microns.
4. This is followed by good rinsing and activation in 3% sulfuric followed by Bright Nickel plating to 10 microns using High leveling ductile process followed by rinsing and Chrome plating to 0.25 microns.
our job plater should know the basics of plating and you should be able to obtain a beautiful finish.
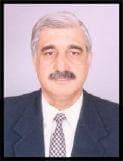
Asif Nurie [deceased] [deceased]
- New Delhi, India
With deep sadness we acknowledge the passing of Asif on Jan 24, 2016
Porosity problem in nickel-chrome plated die-castings?
Q. Hello, I am a technical sales engineers representing an electroplating chemicals manufacturing company.one of my customer has started to nickel and chromium plating on zinc die castings.we are facing a big problem of pitting that is visible after plating.we have consulted a metallurgist who told that this is base metal porosity whereas original manufactures claims that we don't have any porosity in our castings.
we have checked our cleaning system and all baths. there is no problem in our electroplating sequence.kindly tell us the best way to detect the porosity wether it is from the base metal or from our electroplating system.what is the best tool to detect
the porosity.
thanks,
electroplating consultant - Ludhiana, Punjab, India
2007
A. Rais,
The metallurgist is right and the manufacturer is wrong. Zn die castings are porous, period. The best way I know is to look at the parts under high magnification or a SEM (scanning electron microscope). I would do this at three stages. Incoming inspection, after cleaning, and after plating. I would assume that you are putting down a layer of copper under the nickel. Copper strike and copper plate. Good luck to you.
Process Engineer - Syracuse, New York
A. Die casters will always claim they produce castings without porosity, but they would, wouldn't they. In the absence of photographic evidence, I am quite prepared to believe that the castings are porous and this is the source of your problems. The best way to overcome porosity is to plate the casting with a high throwing power deposit. One of the more common ones is cyanide copper and this will fill in the holes and allow deposits with lower throwing power to be plated successfully
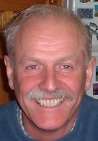
Trevor Crichton
R&D practical scientist
Chesham, Bucks, UK
A. Rais,
I think your metallurgist is right and I also think that your manufacturer of casting claims that they do not have base metal porosity is wrong.Please let your manufacturer know that pitting
(blisters) happens during or after plating is the result of hydrogen gas generated by the reaction between zinc and plating sol'n (or other corrosive solutions) entrapped in pits.So if there is no pits in casting, then there is no blisters after plating.Gone are the days that any body can get away by just washing of their hands with false claims.
But Mr.Rais, Zinc die castings have to have pores! Unless it is cast with foolproof techniques which is practically humanly impossible.
Then what to do- For that you need expert plating techniques.This forum does not allow me to impart full information in a platter for you as this technique somebodies may be the lifetime achievement as result of hard work of some(few) expert platers all over the world.
Just to give you some tips, take care in buffing- use soft cloths in final buff (smoothening, good soak cleaning, electrocleaning (anodic and NOT cathodic) and ... Go for a cyanide copper strike plating before going to Nickel.
Good luck!
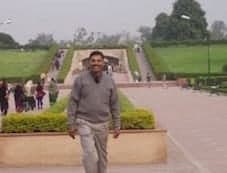
T.K. Mohan
plating process supplier - Mumbai, India
Baking Zinc Die Castings Prior to Electroplating
by Jack Dini
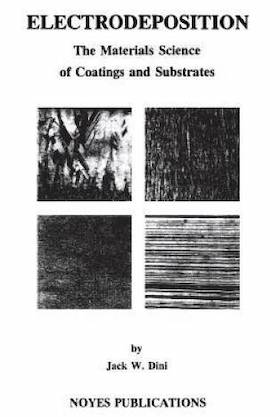
on eBay or Amazon
or AbeBooks
(affil link)
Q. We have been experiencing blistered plating on decorative chrome plated zinc die castings. We use the standard cyanide strike followed by acid copper, nickel and chrome.
We have found by baking the parts at 200 °F prior to plating has virtually eliminated the problem.
Our customer is resisting the idea of baking the parts even though we have proven it eliminates the problem.
My question is; Is it fairly common in the metal finishing industry to bake zinc die cast parts prior to plating to prevent out-gassing during and after plating?
president of plating shop - Bend, Oregon
July 27, 2009
A. You are correct.
If he rebels at the bake, let him know that you will gladly send him the parts, as plated, and that you will charge for the strip and replate each time they are returned.
His other option is to go to investment castings. Expensive!
If you lose him as a customer the world probably will be more pleasant.
Don't you love people that have the opinion of "do not bother me with facts, my mind is already made up."
- Navarre, Florida
Q. Thanks for the response, sounds like you have experience with this type of problem.
We have continued to bake the parts and are still getting a lot of resistance to the idea but so far we feel the results speak for themselves.
president of plating shop - Bend, Oregon
August 18, 2009
A. Hello all,
It's the same with even high carbon steel parts, the carbon migration initiated by pickling and plating can be baked prior to plating, the pickling step removes the carbon from the surface, and resolves blistering issues in the same way as your baking removes entrapped air.
But the customer won't agree; you see it's a commercial issue here: if he does, then he has to pay you for the extra step and also pay for the plated parts that form blisters; by denying the problem exists, he can continue to pick holes in your process, and dump the liability of process rejects onto you.
Welcome to the ways of the world.
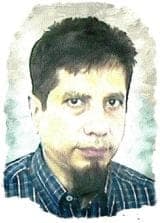
Khozem Vahaanwala
Saify Ind

Bengaluru, Karnataka, India
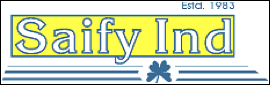
September 28, 2009
Insightful response, KV!
Regards,
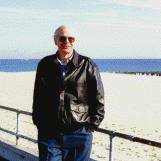
Ted Mooney, P.E.
Striving to live Aloha
finishing.com - Pine Beach, New Jersey
Q. Dear Sir,
We are facing a big problem in zinc die-cast parts (pitting, porosity and bubbles after nickel chrome plating)
Our process is given below:-
Polishing :
Buffing
Cleaning
Electroplating;
Soak cleaning
Cathodic cleaning
water rinsing
Acid dip
water rinsing
Strike copper (cyanide base)
Bright copper (cyanide base)
water rinsing
3% sulfuric dip
water rinsing two times
Bright nickel
water rinsing two times
Buffing before chrome plating
after buffing
soak cleaning
water rinsing
acid dip
water rinsing
chrome plating
neutralizer
water rinsing two times
hot water rinsing
end
Hoping for the best .
Thanks,
automotive parts - Karachi, Pakistan
February 12, 2014
A. Hi Amir. Although I am unfamiliar with buffing parts between nickel plating and chrome plating, I have no reason to believe it is unworkable. So I see nothing wrong offhand with your plating cycle. But it brings back the question of what is the condition of the die-castings? Is there good inspection of them before you attempt to plate them? If they have visible cold shuts or porosity they are not reliably plateable. Good luck.
Regards,
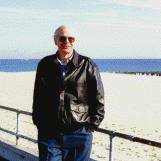
Ted Mooney, P.E.
Striving to live Aloha
finishing.com - Pine Beach, New Jersey
A. Hi.
I would spend some time at incoming store to check on the zinc die casting material. Bet you will find those porosity and bubble problem in the material itself. Yes, the bubbles will look like plating blisters...
For me, after showing these defects to the customer, that the casting itself is not defect free, we have now come to an understanding and certain % defect and limit samples are accepted. Hope it works out the same for you. Good Luck.
cheah
- Penang , Malaysia
A. I have little experience in zamak plating compared to those who often post answers here.
There is one possible cause that is worthwhile to be analyzed --
1) Zamak is very sensitive to acids (Zinc, Aluminum, Magnesium and Kupfer[copper])
2) Porosity can carry solutions from one tank to another
If you combine both factors you have that if you have for example:
- Too strong acid dip -> You will create small pits in the substrate that carry solution from (for example) Alkaline cleaner or alkaline copper to watts nickel bath.
-Cyanide copper layer too low (due to little time, unbalanced bath chemistry, etc.) this will allow acid baths to corrode substrate creating small pits on it.
The problems with pits is that they carry solution and after the nickel plate they create a lack of adhesion (Blisters)
The same happens when the substrate is corroded or defective or for example with very old parts which are very difficult to be plated because you must remove all the pits that can hide solution inside.
By the way you can try if it is the case to use hot water rinses alternating with cold water rinses, this is going to help solution entrapped to leave the pits.
But now in this point this is becoming too complicated, I suggest check rinses (5% sulfuric acid) please readers tell me if I am wrong, check bath chemistry of copper, and also check the parts before entering to the plating line for corrosion.
I have little knowledge about zamak plating but when corroded zinc diecast is somewhat difficult to plate for me, I used to grind and polish it very well again before plating.
I hope this helps.
I will gladly receive any corrections, recommendations and feedback to learn more about this subject.
- Bucaramanga Santander Colombia
A. Also the acid attack of the zamak substrate alters the surface and produces the lack of adhesion.
Daniel Hernandez Guerra- Bucaramanga Santander Colombia
Zinc die castings: Can time between finishing and chrome plating cause plating problems?
Q. I manage a metal finishing job shop. Among other metals, we polish and buff zinc die castings that then go to another vendor for copper, nickel chrome plating. Are there any problems caused by the amount of time that the parts sit after finishing and before they can be plated? Parts are wrapped in toweling and stored in cardboard (in the plating shop)while waiting to be plated. Thank you.
Chuck StairsMetal finishing shop - Rockford, Illinois, USA
October 28, 2015
by Safranek & Brooman
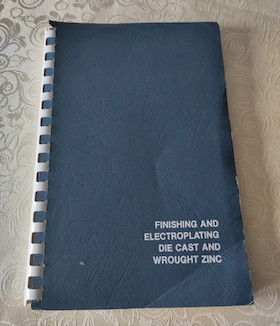
on eBay or Amazon
or AbeBooks
(affil link)
A. Hi Chuck. I doubt that the metal itself "ages" in any significant way under these condition, but Safranek & Brooman .
make the point that buffing compounds are always difficult to remove but get even more so with age. For this reason they suggest considering vibratory finishing in lieu of your buffing if that is workable for your situation. Good luck.
Regards,
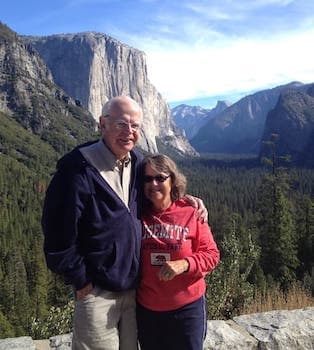
Ted Mooney, P.E. RET
Striving to live Aloha
finishing.com - Pine Beach, New Jersey
Q. Hello , I am doing Nickel Chrome plating on Zinc die cast parts. Since last one month I am facing passive problem on parts what I am plating. This problem is just like burning on edges but the difference is this is very smooth not hard like burning.
Can anyone suggest me any idea?
bathroom products - Bhiwadi, Alwar, Rajasthan, India
July 12, 2016
A. Hi Parmod. Unfortunately, even when the readers have a clear description and understanding of the problem, it can be tough to help solve the problem. But I doubt that anyone can offer much based on this verbal description :-(
It happens only on the high current density edges and corners where burning could occur, but it is "very smooth"? Why is it objectionable then -- is it the wrong color? What do you mean by "passive problem" -- is something not adhering? Please send photos of the defect, your process cycle, and a few paragraphs of detail about the defect and I think someone will be able to help.
Regards,
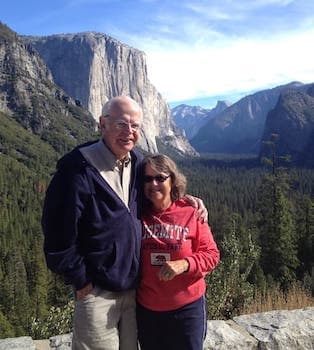
Ted Mooney, P.E. RET
Striving to live Aloha
finishing.com - Pine Beach, New Jersey
Pitting in Chrome Plating of Zamak 3 Die Castings
Q. The company that I work for has had a pitting issue that has been going on for sometime and we can not seem to get to the bottom of it. We are a company that produces Zamak 3 castings and buffs and plates all in house. We produce chrome castings that have mostly A surfaces and more than 1 on a part.
All of our parts seem to have the same pitting problem to the point that I would call it a speckling affect that sometimes feels rough. We have been through multiple tests sometimes more than once. We have looked at the castings themselves and yes there are times that we can see porosity in the parts and there are times that we can't see anything under the microscope.
We have also went to the point where we have drawn/etched a circle around pitted areas of the part, so we could confirm that it was a casting issue. We lost! The pits that you could not see by eye, but under a scope that we engraved around covered fine and other areas of the parts that we did not see anything in had the pitted deposits. We then started looking at the prepping before plating, so we tried to do a color buff and not a cut buff operation, this also did not help the results. We have tried multiple things in plating as well. Better cleaning (we added a Vapor Degreasing operation), better filtering, software to monitor most of our plating adds and trends. We did notice a couple of weeks ago that if we orientated parts on the rack different the defect would move. We often have troubles with the surfaces that are coming out of the baths first and or the part facing the anode.
At this time I am looking at our plating line, but we are still looking at die cast tooling and process, the buffing process, and the cleaning process.
I will say that when I look at the raw parts under the scope I might see a couple of pits, but this is covering almost the entire surface and it is on every part, not just a couple.
Here is our process.
Die Cast - Zamak 3
Buff - combo buff with sisal and color mixed together with a color cut Tripoli.
Vapor Degrease - Enthron Aero
Soak Cleaner - 2 minutes
Electro Clean - 30 sec.
Acid Tank - 30 seconds
Electro Cleaner - 30 seconds
Acid Tank - 30 sec.
Copper Cyanide 4.5 volts 10 min.
Triple Rinse In and Out
Semi Bright Nickel - 7 volts at 45 minutes
Bright Nickel Tank - 7 volts 25 min
Particle Nickel - 6 volts 3 minutes
Triple Rinse in and out
Chrome Tank - 1800 amps 3 min.
We were seeing this defect before we added the Vapor Degreasing operation.
I know I did not cover everything, but I can answer more questions later.
Any Thoughts on what to try next?
Employee - New Hampton, Iowa
December 12, 2016
A. Hi Jeremy. Are the pits semi-hemispherical and bright when examined at low power magnification such as with a jeweler's loupe? If so, these are "gas pits" / "hydrogen pits". Widespread pitting which does not seem related to defects in the casting may be such gas pitting. Although a number of things can cause it, including poor buffing, the first step is to check the wetters and agitation in your nickel bath because any hydrogen bubbles that adhere too long will cause these pits.
Regards,
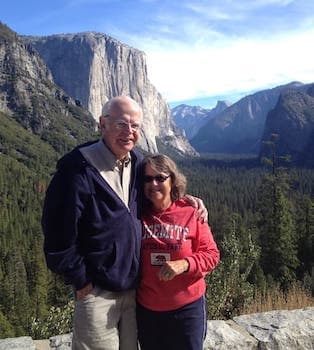
Ted Mooney, P.E. RET
Striving to live Aloha
finishing.com - Pine Beach, New Jersey
Q. Yes. Under an eye loop they look semi-hemispherical and shiny. Some appear to have a raised look and some appear to have a indent look. Is that typical?
On a side note, do you know or is there a rule of thumb on how big of a defect the plating process can cover? This is something that we get asked all the time and we have never been able to answer.
- New Hampton, Iowa
December 13, 2016
A. Hi again. The shiny semi-hemispherical pits are definitely "gas pits" (formed by a small bubble of hydrogen adhering to the surface as the plating builds around it). Again there can be a few causes, but the first thing to check is the surface tension in the nickel plating tanks. We have several threads on that: search the site for "surface tension nickel" or "pitting nickel".
I'm not sure about the bright hemispherical bumps, but they sound more like nodularity than roughness. Are the nickel plating baths commercial proprietary processes where you can get technical data sheets and analysis of the additives from the supplier?
Although modern nickel plating baths can level and bring reflectivity to a roughly polished steel surface, I'm not sure that that translates in any way to diecastings. To my limited knowledge of plating of diecastings, any visible porosity or cold shut will cause a plating defect.
Regards,
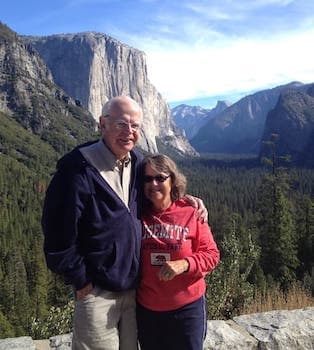
Ted Mooney, P.E. RET
Striving to live Aloha
finishing.com - Pine Beach, New Jersey
Ed. note: for further info on this subject, please also see letter 3778, "Problems in Nickel Chrome plating on Zinc Diecast Parts"
A. Hi Jeremy,
Letter 1000 mentions details regarding etching of zinc die-cast parts. Perhaps I missed it...is there an etch step in the existing process? According to my understanding, etching can help knock down micro-peaks formed during the casting process. As Ted pointed out, an improved buffing process may need to be investigated.
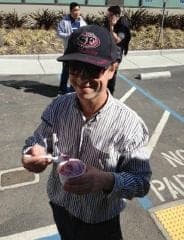
Blake Kneedler
Feather Hollow Eng. - Stockton, California
February 6, 2017
Q. Hi we are producing some zinc castings (Zn # 3) we do Ni Cr plating on them but have been struggling to get right finish. We see blisters, flow lines etc. The platers says that this is due to bad casting quality.
Can somebody throw some light on this. What all I need to ensure good plating quality Zinc castings.
Al and Zinc castings - Delhi, India
December 4, 2018
A. Hi VK. On a couple of assignments I acquired enough experience to be able to fairly reliably separate zinc diecastings and aluminum diecastings into "plateable" and "non-plateable", but there are many people with far greater experience & skill at it than I acquired in my short stints. In fact, William Safranek wrote whole chapters about inspection of diecastings before plating in several books :-)
But my experience was that porous surfaces (sometimes created by mechanical removal of swarf) are not plateable and "cold shuts" (tiny hairline cracks where the flow came together from two directions but was no longer hot enough to fuse) are not plateable.
Although you probably know much more about diecasting than I'll ever know, if you have a major contract, I think you should meet with your best plater and inspect a hundred diecastings or so and have him/her mark those that s/he thinks are and aren't plateable, then review the results after plating so you get a good feel for what is plateable and what isn't. On one of my jobs we powder coated the castings that we felt weren't good enough for plating but were too good for re-melting, further showing that there are degrees to "good" diecastings.
Regards,
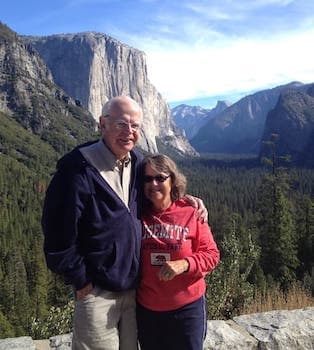
Ted Mooney, P.E. RET
Striving to live Aloha
finishing.com - Pine Beach, New Jersey
⇦ Tip: Readers want to learn from your situation;
so some readers skip abstract questions.
Q. How can I coat a die cast part with Hard Chrome?
Jesus Godinez- Tijuana Baja California
July 28, 2021
A. Hi cousin Jesus. After the die-casting has been mechanically treated sufficiently for plateability you will probably need to electroclean, acid activate, cyanide copper strike, possibly nickel plate, and then chrome plate. Please start with our "Introduction to Chrome Plating", but recognize that there are whole books about plating of die-castings, and whole books about hard chrome plating, so your posting is quite open-ended and cannot be fully answered.
But be sure of what you want the plating to do -- it can improve wear resistance, but it's unlikely to have any good effect otherwise, just as an egg shell or a sheet of glass is very limited in its ability to protect an egg from much :-)
Luck & Regards,
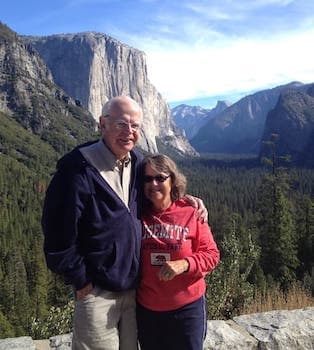
Ted Mooney, P.E. RET
Striving to live Aloha
finishing.com - Pine Beach, New Jersey
Q, A, or Comment on THIS thread -or- Start a NEW Thread