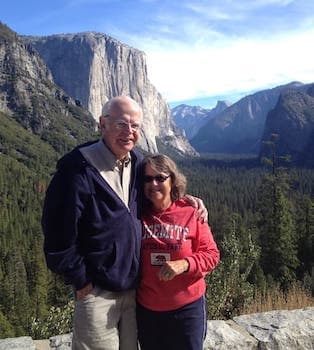
Curated with aloha by
Ted Mooney, P.E. RET
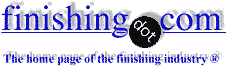
The authoritative public forum
for Metal Finishing 1989-2025
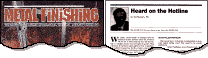

Jump to this related thread:
• Topic #2681 "How to remove Zinc contamination from Nickel plating bath"
• Topic #31166 "Allowable metallic contamination in nickel plating bath"
• Topic #41906 "Dummying" an electroplating bath?"
• or continue with -----
Problems in Nickel plating on Zinc Diecast Parts
Q. We plate a lot of Nickel Chrome on Mazak parts which go into locks, and wonder if there is any remedy to the problem of copper and zinc regularly dissolving in the Nickel Solution leading to black deposits in the LCD areas.
Why the chrome bath also produces burning on the HCD areas is another mystery to us. Our Supervisors swear that its on account of the same contaminants that are playing havoc in the Nickel Baths and decant both the Nickel and Chrome on a daily basis to remove any fallen Zinc parts but although this needs to be done , I would welcome any assistance to both these problems.
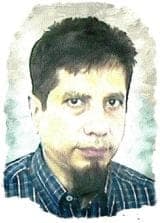
Khozem Vahaanwala
Saify Ind

Bengaluru, Karnataka, India
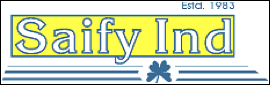
1999
A. Hi Khozem.
Yes the zinc and copper displays on the low current areas. Plate the bath with a dummy sheets and use a low current for copper 0,1-0,3 amp per dm2 and for zinc 0,2-0,5 amp per dm2. You must also inspect the bath if the part dropped from the rack. About the chrome solution, following reasons will make burning on the HCD areas. High temperature, Low CrO3, High ratio between CrO3 and sulphate acid, the current being turned on too fast.
Regard
Anders
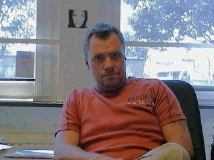
Anders Sundman
4th Generation Surface Engineering
Consultant - Arvika,
Sweden
A. Hi Khozem. Anders is correct that the Cu and Zn will deposit in the low areas and cause them to be dull. Getting the parts out that fall in the tank is imperative. They dissolve fast. A regular schedule of low current dummying will keep those metals below the level they start to interfere. We also send samples to a lab to have the levels checked. It only takes a few ppm of either metal in the bath before it starts to show. They do have additives that will complex these metals temporarily but they are just harder to remove later.
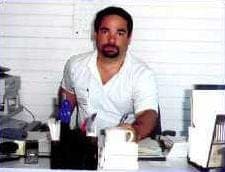
Jim Conner
Anoplex Software

Mabank, Texas USA
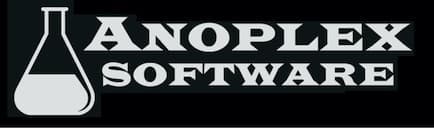
A. Hi Khozem,
I too agree with both Andrea & Jim, but we plate these contaminants out by adding GW Additive 42; though the deposit is a little dull but its not black. Also try keeping pH on the higher side. You can avoid decanting by just placing a mesh tray coated with PP at the bottom of the tank, this way you'll just have to raise the basket and take out the parts if any fall in the tank.
Nippinder Singh-New Delhi-India
A. What Mr. Singh has mentioned is a particular proprietary additive to be used. Most suppliers of nickel brightener chemistry have both general use formulations and those specifically for zinc alloys. The brightener chemistry in the zinc alloy formulations generally has lower leveling than the other. However, in the general brightener category most all manufacturers have a purifier (or similar product) to help overcome the effects of metallic contamination. This will enable consistent plating and reduce the need for low current electrolysis (dummying).
Gene Packmanprocess supplier - Great Neck, New York
A. Dear Khozem ...all the above suggestions are very good. We run the pH at 4.2-4.5 and check at least hourly. Makes for smaller additions to adjust the pH. The temperature we found of the nickel in this application was 138-142 °F. Decorative chrome should be 108-115 °F -- I try to keep it 108-110 °F.
Bill Hemptech svc. w/ chemical supplier - Grand Rapids, Michigan
A. Dear Khozem
We also experience the same chemical burning on our Mazak 3 die castings we have tried many different ways to plate this very difficult material but however thick we lay down the copper the acid nickel still gets through and attacks the Mazak leaving the black marks. Jig plating is a solution but the cost is prohibitive compared to barrel plating. We are investigating other finishes than nickel but so far have had no success but we will let you know if we find one
We also experience discolouration of the bright zinc , we believe that this is due to contamination of either zinc or magnesium in the nickel bath this can only be removed by electro cleaning the bath which then goes back to a bright nickel finish.
If we could find a reliable UK plater we would be over the moon.
But we haven't found one yet
We wish you good luck in you solution to the problem
Best Regards
Stuart Sharples- Corby Northamptonshire U.K.
Thanks everyone for the advice. Mr Stuart, despite all the common difficulties, we still consider ourselves as reliable platers! As labour is cheaper in India, we are yet Jigging and not Barrel plating. Ball pen tips made of Mazak are also being successfully Barrel plated only with one hour of heavy copper undercoat using a potassium cyanide based copper plating.
Regards,
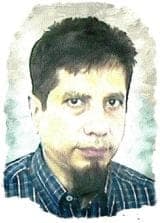
Khozem Vahaanwala
Saify Ind

Bengaluru, Karnataka, India
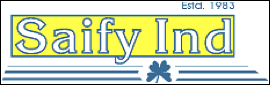
A. Plating of Mazak will always end up with zinc and copper impurities in the nickel solution. It is true that there are commercial additives (usually named purifiers) that give a temporary relief as they create a complex with the zinc metal in the nickel solution. It turns the black low current density into dull nickel. But remember, these additives are temporary and help for a day or two only. Dummy plating is necessary every few days when plating Mazak. Try to add hydrogen peroxide prior to the dummy plating. Regarding the chrome solution, well, the copper and zinc can cause throwing power problems but NOT burning at high current densities. If you have burning problems, check the parameters mentioned by Anders like, chrome/sulphate ratio, temperature, current density, contacts, etc.


Sara Michaeli
Tel-Aviv-Yafo, Israel
Q. Dear Sara M,
When we dummy the bath we generally reduce the pH to about 3 before dummying although we have never tried adding Hydrogen Peroxide. How much do you recommend ?
Thanks in advance,
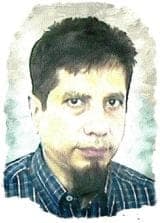
Khozem Vahaanwala
Saify Ind

Bengaluru, Karnataka, India
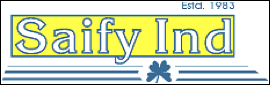
Q. Hi I am looking for an answer to a question that puzzles me. When plating a zinc/strike coated aluminum part in a nickel bath... What happens to the zinc when the nickel bath attacks it? Does it eventually pollute the nickel bath? Thank you Tom T& S; Wood products
Tom Haltmeyer- Peoria Arizona, USA
2000
A. Tom.
I hope you use pre-contact.You should use filtration with a cationic system like nickel purifier (Atotech). Best regards
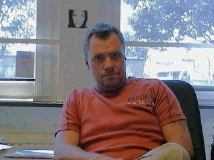
Anders Sundman
4th Generation Surface Engineering
Consultant - Arvika,
Sweden
Q. Dear sir,
We're having lot of problems when doing zinc base die casts for copper and nickel plating; main defect is zinc metal will be started reaction in acid copper solution and in the nickel bath also, showing only black and dull plating surface, please give me your technical assistance.
Thanks and best regards,
UPALI
ELECTROPLATER - Alawwa, Colombo, Sri Lanka
November 22, 2011
A. Hi, Upali. You are not attempting to plate acid copper directly on zinc diecastings, are you? That won't work; you must start with cyanide copper plating (or copper pyrophosphate). Good luck.
Regards,
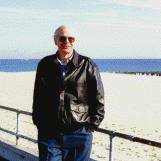
Ted Mooney, P.E.
Striving to live Aloha
finishing.com - Pine Beach, New Jersey
Q. Dear Mr. Ted,
Thanks for your kind response for my problem, sir. Already we did cyanide copper for zinc diecast and then did acid copper but in acid copper and nickel bath those alloys will be further dissolved. Please give your kind technical assistant to overcome this defect.
Thanks and best regards,
UPALI-SRI LANKA
- ALAWWA, SRI LANKA
December 25, 2011
A. Hi, Upali.
You must achieve 100 percent pore-free copper layer in the cyanide copper. The process cannot work if any zinc is exposed in the acid copper tank. And then you probably should also enter the acid copper tank with a live lead so the copper (and zinc) does not dissolve in the acid copper tank. Good luck.
Regards,
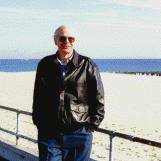
Ted Mooney, P.E.
Striving to live Aloha
finishing.com - Pine Beach, New Jersey
Q. Dear All,
We are basically zinc diecasters in India. We have started manufacturing zinc handles for faucets; Mazak 3 material.
We need to plate it copper, nickel and bright chrome; it is to be pass 96 hours NSS test. Please suggest what process/chemicals to be used.
As of now we will be starting manual plant for plating, can anybody suggest what are the benefits for automatic electroplating plant for zinc faucet handles?
Await your quick reply,
Thanks.
- Jamnagar, Gujarat, India
February 14, 2013
A. Hi Kushal. We appended your inquiry to a thread which covers some of the issues of copper, nickel, chrome plating of Mazak. If you read between the lines, you should align yourself with a process supply house who will sell you those chemicals, and give you the operating parameters, and help you troubleshoot the issues. The principal advantage of automation is labor savings. Manually carrying racks of work from one tank to the next can be a drudge. Good luck.
Regards,
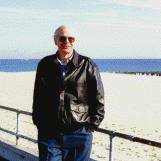
Ted Mooney, P.E.
Striving to live Aloha
finishing.com - Pine Beach, New Jersey
Q. We are working on process of copper nickel plating on Mazak, i.e., zinc diecasting. Plating is done in barrel, but after nickel plating black spots, blisters (bubbles) are seen kindly suggest solution on this problem. Can you also state process rejection percent in zinc diecasting plating process.
Ashok Theteplating - Nashik , Maharashtra, India
April 14, 2013
A. Hi Ashok. Barrel plating of zinc diecastings isn't easy, as you have read on this thread. Blisters can be due to a number of causes, but the first suspect when plating diecastings is parts with porosity or cold shuts.
I can't give you a typical reject rate from diecasting, especially since continuous improvement should be constantly reducing it. But I can tell you that you will not satisfactorily plate parts which have porosity or cold shuts, so there's your starting point on what portion of your diecastings are rejects.
Regards,
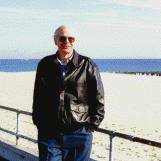
Ted Mooney, P.E.
Striving to live Aloha
finishing.com - Pine Beach, New Jersey
Copper plating peels off from zinc die-castings
Q. We are doing copper-nickel plating on zinc diecasting material. We are getting peel-off problem after copper plating.
Please tell us about how to remove Cu & Zn contaminants from nickel solution, what should be pH of nickel plating, how long dummy should be placed in solution, and what should be the temperature and other parameters.
Kindly suggest on this problem. Await for your reply.
Thanks & regards
Plating - Nashik, Maharashtra, India
September 16, 2013
A. Hi Ashok. We have numerous threads on line here that answer each of your questions and I can refer you to them if you wish; or, if you'd like a more tutorial approach, we can point you to plating books that have good chapters on nickel plating. But before sending you off on possibly the wrong track: two comments.
1. Suggestions regarding nickel plating parameters should generally be under the direction of your nickel plating process supplier.
2. Copper and Zinc contamination, and minor variations in nickel plating pH and temperature, are unlikely (in my experience and opinion) to manifest themselves as a "peel-off problem". If you are sure that the acid copper is fully adherent, and the nickel will not adhere to it, I think I'd suspect something wrong with the copper plating additives. Other readers may be better informed about this than me, so I welcome additional comments.
Regards,
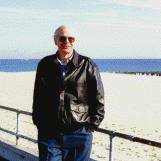
Ted Mooney, P.E.
Striving to live Aloha
finishing.com - Pine Beach, New Jersey
A. Good day Ashok.
There is some info at letter 51199 regarding peeling on acid copper. Remember to try an acid etch/electrocleaner after acid copper, to remove brightener films (organics) which can cause peeling of nickel. What is the condition of your nickel?
Is the bath overloaded with excess brightener? Are you ensuring there is no current interruption during nickel plating? This can also cause peeling.
Hope this helps.
Regards,
Eric Bogner.
- Whitby, Ontario, Canada.
A. Hi.
For zinc die-casting material, here's some important pointers.
1. Ensure the soak cleaner and anodic electrocleaner are proprietary chemicals specially for zinc die-casting.
2. 1% sulfuric acid ( 10~20 sec ) pickling before cyanide copper plating.
3. Ensure a minimum of 5 microns copper thickness. ( current density at 3 A/dm2 for 15~20 minutes ). I prefer a CuCN at 60 g/l, Free cyanide at 12 g/l.
4. Followed by nickel/chrome.
Be warned, blister free plating on zinc die-casting also dependent on the porosity of the die-casting itself. Check the condition of material during incoming. Good Luck.
- Penang, Malaysia
A. What is your plating cycle?
Ted assumed you have a problem with acidic copper but I am not sure you even use acidic copper following the cyanide copper.
Anyhow, you have to make sure that the hot soak cleaner and the electrolytic cleaner have low hydroxide concentration.
Acidic activation - that is the key for the process - do you have fluorides there? Do you recharge this solution often?


Sara Michaeli
Tel-Aviv-Yafo, Israel
Q. Dear Sir,
1. We have observed peel off problem on zinc diecasting mazak material after 2-3 days from the day of plating, peel off is observed in 1 percent, on performing file test and hammer test we have not found peel off problem on same piece.
2. Also suggest process for removing zinc and copper impurities from nickel solution and cyanide copper solution
3. Also suggest what material should be used to make low pH of nickel solution.
Thanks & Best Regards
Plating - Nashik, Maharashtra, India
February 26, 2014
Hi again, Ashok.
1. Five people previously offered their suggestions regarding your first problem. Maybe you missed those responses. Can you start by commenting on those suggestions please? Thanks!
2. If you do not see sufficient info earlier in this thread about zinc and copper contamination to satisfy your needs, please search the site with the term "zinc contamination nickel plating" and "copper contamination nickel plating" to find several discussions on each subject. I apologize for assigning you that extra work, and I don't wish to be evasive, but we are finding that these threads are more coherent and useful as a reference for other readers, and get much better search engine coverage when they stay narrowly focused. Apologies.
3. If your nickel bath is Watt's bright nickel, sulfuric acid pre-diluted with DI water is used to lower the pH; again we have several threads about pH control of nickel plating baths. Good luck.
Regards,
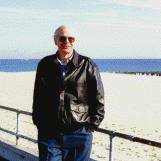
Ted Mooney, P.E.
Striving to live Aloha
finishing.com - Pine Beach, New Jersey
Q. We are using die casted MAZAK-5 material part duly NI-plated. Let me explain the total process:
We are taking die casted piece from the die. The material is MAZAK-5 (ZAMAK). After that we are doing grinding on four walls of the piece. After that we are doing Electroless Nickel on the whole surface .
Now we have got various problems like plating peel-off in a few areas, plating not proper, etc.
Surprisingly this problem is observed for 10-15 pieces out of 50 or 4-5 cases out of 50. So this way total lot is not rejected.
Now these rejected castings we have to scrap. We are totally confused. We have tried the plating with approximately 5-6 good suppliers but same problem. We cannot control all the parameters of plating so we would like to know what precaution can we take at our end before we do plating so as to minimize rejection. Or is there any other way of finishing?
ANAND PATHAK- PUNE, MAHARASHTRA, INDIA
October 25, 2013
A. Hi Anand. It is uncommon to grind diecast parts before plating because only the skin of the casting is non-porous, and if you break through the skin and reveal porosity, the parts will not plate properly. An alternative, although not cheap, may be to vacuum impregnate the castings.
Personally, I would suggest one of two courses of action:
1. - send trial lots of parts to competent plating shops to see whether the parts are reliably plateable, or
2. - retain a good plating consultant to figure out what you are doing wrong.
If you have tried 5 different suppliers, you have already wasted far more money already than either of these alternatives would have cost you. Best of luck.
Regards,
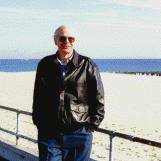
Ted Mooney, P.E.
Striving to live Aloha
finishing.com - Pine Beach, New Jersey
A. Hi Anand.
I don't see a cyanide copper before the EN. ASTM B252 Standard guide for Preparation of Zinc Alloy Die Casting for Electroplating recommends a cyanide copper plating of at least 5 micron thickness before any other subsequent plating.
- Penang, Malaysia
Q. We do plating on mazak components. For surface preparation operations for all components buffing process is carried. After buffing components, our surface is looking clean & even but after plating components surface contains porosity, pit marks which are not getting identified in visual inspection and under magnifying glass.
What should we do to eliminate this defect?
- Mumbai, India
October 14, 2014
by Safranek & Brooman
on AbeBooks
or Amazon
(affil links)
A. Hello Deepak,
Could you please elaborate on your complete plating process, such as what types of Cu plating you are using on the Zamac? On Zamac there is normally a Cn Cu strike and Cu plate. You don't mention this. Thanks.
Process Engineer - Phoenix, Arizona USA
A. HELLO FRIENDS,
I SUGGEST KCN BASED ROCHELLE COPPER CONTAINING 24 GRAMS/LIT OF COPPER METAL, 8 TO 10 GRAMS/LIT OF KCN AND 35 TO 50 GRAMS/LIT OF SODIUM POTASSIUM TARTRATE
⇦ this on
eBay
or
Amazon [affil links]
PRIOR TO ACID COPPER.
- RAJKOT, GUJARAT, INDIA
November 3, 2014
Nickel+Chrome on die-castings - too much Cu, not enough Ni?
Q. I am an engineer, but I'm not a plating guy. We have some Zamak (zinc-alloy) die cast parts used for BBQ knobs and handles. Our supplier in China has been making these for a while. In certain coastal areas, the parts are corroding/pitting in as little as 6 months due to the ocean air environment. Our drawing has always called out ASTM B456, but we never gave them a Service Condition. However, reading the spec shows we would probably go with an SC3 condition which, per table 3 would mean 5µm of copper and 20µm of nickel, then a flash of chrome.
I sent 5 different parts to a lab for micro examination (per ASTM B487) of the plating thickness. All five parts showed NO copper at all, and the nickel thickness were all too low in the 3-13 µm range. The lack of copper seems to tie into the occasional pitting and poor surface appearance of brand new parts, and the low nickel seems to tie into the poor corrosion resistance we have seen.
So now the supplier wants to introduce a new plater. When asked about their plating thicknesses, they are saying the following:
Our die cast parts are plated three layers of copper. The plating thickness:
1st plating - Ground Copper
2nd plating - Alkali Copper
3rd plating - Coke Copper
Total Copper thickness 20µm
4th plating - Nickel thickness 4-6µm
There is no plating factory in Ningbo area can plate over 20µm thickness.
5th plating - Chrome thickness 0.1-.2µm
We will get a plating thickness tester next month for in-house inspection.
Salt spray corrosion test chamber (attached photo) for in-house inspection 72 hour test - Salt AR 500g, 95%, PH 7 per NSS ACSS
Temperature 35°±1° Temperature fluctuations <0.5° Temperature uniformity <2°
Saturated air barrel temperature 47°±1°
As I'm reading this, it looks like this guy wants to use 4X the amount of copper, and 1/4 the amount of nickel. I know both metals are expensive, but I'm not happy with what I'm seeing. Both appearance and corrosion resistance are important to me. If I can convince this guy to use the 20 µm of nickel he's saying is his maximum, is there an issue having too much copper?
Thanks for your help.
Engineer - Anaheim, California USA
February 12, 2018
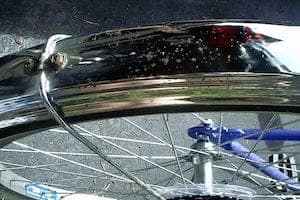
nickel-chrome bicycle fenders rotting within 3 months :-(
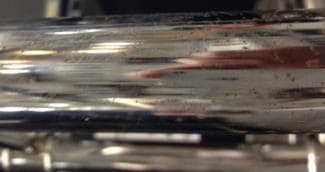
nickel-chrome bathroom accessories in big-box store, already rusted before sale :-(
A. Hi Hans. I'm not familiar with those 3 layers of copper plating; I suspect there are some translation difficulties. Usually the copper plating is done in two layers: cyanide copper plating (just enough for coverage), then bright acid copper plating to a total of 5-8 µm. If the copper plating is done right, 20µm shouldn't hurt anything, but as noted in the MFSA Quality Metal Finishing Guide, "copper cannot be substituted for any part of the nickel thickness specified".
4-6 µm would never be correct for any exposure; 20 µm would be for moderate exposure. And 0.1-0.2 µm of chrome is probably too thin as well.
China is capable of some of the highest quality metal finishing in the world, as witness such processes as the anodizing on the iPhone. But almost all of the copper-nickel-chrome plating from China these days is a scandal of trash! If you don't want your company to be identified with that absolute garbage quality, you'll have to work very hard indeed to get things done right. Your website says your stuff is all made in the USA; you might want to consider having the plating done locally.
You can probably specify 16 hours of CASS testing per ASTM B368 or Corrodkote per ASTM B380 rather than having to specify salt concentrations and temperatures, etc. Good luck!
Regards,
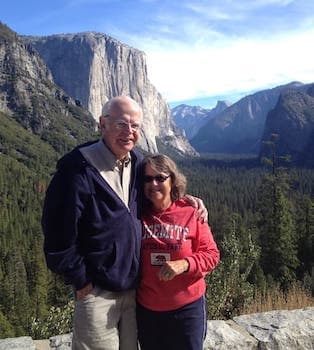
Ted Mooney, P.E. RET
Striving to live Aloha
finishing.com - Pine Beach, New Jersey
Q, A, or Comment on THIS thread -or- Start a NEW Thread