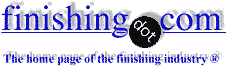
-----
Galvanic corrosion issues: aluminum and stainless steel
< Prev. page (You're on the last page of the thread)
Q. Could anyone please tell me what would be better for holding a PVC yard sign to an aluminum U channel stake, aluminum or stainless steel pop rivets, near the ocean?
David Graham- Florence, Oregon, USA
A. Hi David. I'd bet on the stainless rivets.
Regards,
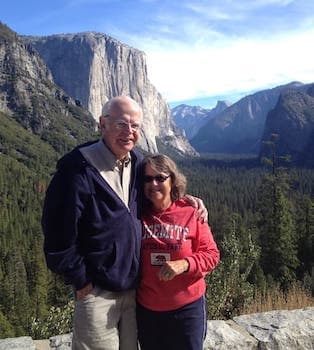
Ted Mooney, P.E. RET
Striving to live Aloha
finishing.com - Pine Beach, New Jersey
July 28, 2015
Q. Would a chrome steel ball bearing press-fit onto an aluminum rod present a galvanic problem? Neither material would be exposed to lubricants, and both would be in a "clean room."
N Kope- Newark, Delaware, USA
October 27, 2016
Q. What will be problems occur when stainless steel is coated with inorganic zinc silicate primer?
eydin mohammedAramco - Saudi arabia
November 4, 2016
A. Hi Eydin. I haven't heard of it, but I don't think it would cause any problems.
Regards,
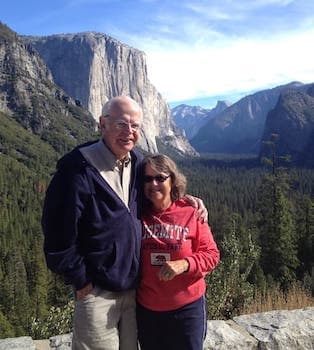
Ted Mooney, P.E. RET
Striving to live Aloha
finishing.com - Pine Beach, New Jersey
A. If you can get adequate adhesion inorganic zinc coatings will give excellent performance.
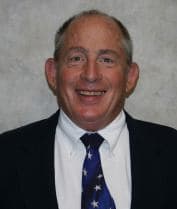
Tom Rochester
CTO - Jackson, Michigan, USA
Plating Systems & Technologies, Inc.

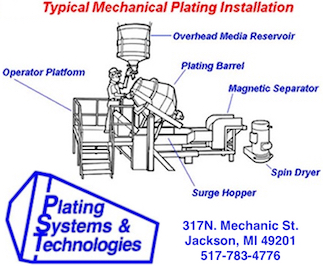
Q. My company is working on an outdoor application to be installed in a rural environment (faraway form the seaside). It consists of a large stainless steel (AISI 304) trapezoidal screw that goes inserted in a diecast aluminium (A380) fixture. One part is threaded to the other (and remains fixed thru the life of the application).
We are concerned about the effects of galvanic corrosion on this to parts, specially because the aluminium part is relatively smaller than the stainless screw.
Aesthetics is not an issue, but cost and ensuring structural resistance of the parts are.
As said, the part application will be installed outdoors, unprotected from rain. The desired life is 25 years.
We do not have a lot of experience with aluminium finishes, but making some online research we have found that anodizing could help reduce/avoid the galvanic problem. But have also read that anodizing is not easy with die cast aluminum.
The finishing we are thinking to use is: Mil-A-8625, Type II, (0.8 mil min), Class I. Sealed.
Do you think this finish will work? Do you know any better approach to solve this problem?
Thanks
product designer - Reus, Tarragona, Spain
November 14, 2017
A. Hi Raul. I think this is a poor idea for a few reasons. Not only can it be difficult to anodize aluminum die castings, but it can be very hard to anodize threads -- some people feel it should not even be attempted. But if the thread area is well sealed with some kind of thread sealant, so there is no non-anodized aluminum exposed to moisture or the atmosphere, it might be okay.
A photo of the part might be helpful because it's difficult to suggest what should be done instead when we don't understand the implications of any such suggestions. And if the owner removes the screw and reinserts it without careful resealing, or the sealant deteriorates from the sun over the years, it sounds like you would get severe galvanic corrosion in the thread area.
Regards,
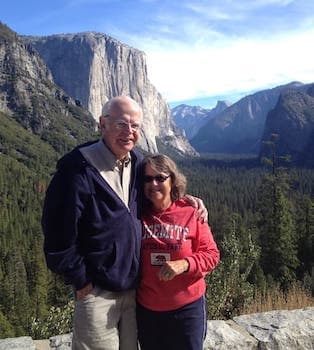
Ted Mooney, P.E. RET
Striving to live Aloha
finishing.com - Pine Beach, New Jersey
Q. Thank you for your answer Ted.
As I understand, you are suggesting to anodize the full part (without paying special attention to thread anodizing) and protect isolate the thread with thread sealant.
I include some pictures of our 3D model and of some prototypes we manufactured, so readers can get a better understanding of our application.
Our manufacturer suggest to use a Chromate passivation Cr3 (Clear) as a finish. Do you think that may work properly if combined with the thread sealant?
Raul Obis
- Reus, Tarragona, Spain
A. Hi again Raul. Thanks for the pictures.
If you are still talking about anodizing the outside of the aluminum item, but also adding chromating of the thread area, I imagine that chromates could be of at least some small value. But if you are now talking about chromating the exterior in place of anodizing it, I personally do not think that will be a satisfactory answer.
Regards,
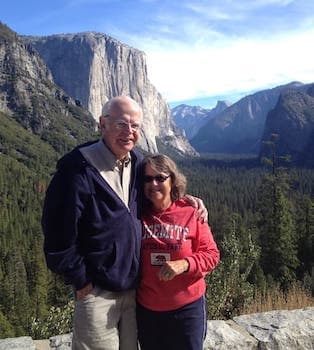
Ted Mooney, P.E. RET
Striving to live Aloha
finishing.com - Pine Beach, New Jersey
Galvanic corrosion potential with aluminum tank, stainless nipple and brass fill assembly
Q. I had a custom fiberglass boat built with an aluminum gas tank. The builder installed a 6" stainless steel nipple into the aluminum tank and a brass filler cap assembly atop the stainless nipple. The boat is used primarily in a salt water environment. After reading your forum, I am concerned! Your thoughts?
Mike WilsonNew boat owner/Inshore fishing guide - Silverhill, Alabama USA
January 2, 2018
A. Hi Mike. I don't know exactly what "installed" means in terms of direct metal to metal connections. I've seen numerous anodized aluminum railings installed on hotel and condominium balconies with stainless steel screws, and a lot of aluminum fins directly on copper heating coils without memorable issues, but there's also a lot of difference between the conductivity of rainwater and saltwater. A direct metal to metal contact in a saltwater environment does sound to me like it could lead to pitting and corrosion issues. But again, if the metals aren't actually contacting each other, you cannot have galvanic corrosion.
Regards,
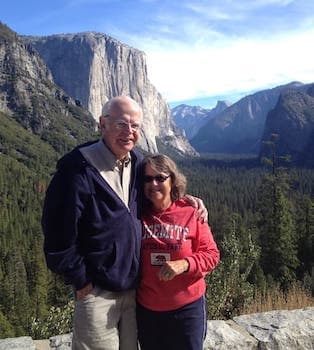
Ted Mooney, P.E. RET
Striving to live Aloha
finishing.com - Pine Beach, New Jersey
Thank you for your response. The "installed" gas tank assembly is direct metal to metal connections. The brass fill cap and flange is threaded to a 6" long x 2" diameter male stainless steel nipple which is threaded into the aluminum gas tank. Although somewhat protected in a fiberglass enclosure, with only the brass fill cap and flange directly exposed to the elements, it is used exclusively in a saltwater marine environment and the enclosure is vented. Thank you again.
- Silverhill, Alabama USA
Q. I have a "salt water" pool (1/12th ocean salinity).
My second ($1000) pump is about to fail due to what I think is galvanic corrosion.
I'm wondering if there is any type of "sacrificial anode" I can attach that would prevent the issue?
The pump unit is fiber reinforced plastic.
The electric motor has a bell shaped aluminum casting that is bolted to the plastic pump with stainless steel (through) bolts and nuts. I don't think the bolts directly touch the pool water, but undoubtedly get some stray water on them.
The corrosion is such that the aluminum flange the bolt goes through entirely gets eaten away. It starts under the paint (no apparent primer or anodizing under paint). The paint flakes off and reveals just white dust left behind where the aluminum used to be...
Is there a sacrificial anode I could use?
Are there "sleeved washers" I could get to put under the bolt heads?
- San Diego, California, USA
February 14, 2018
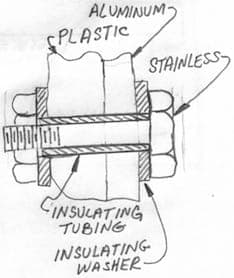
Hi Rick. Due to the low salt content, zinc sacrificial anodes might not work, but magnesium ones ought to. I think they're available from boat stores, or you could get one from a water heater. But, unless tightly connected to the aluminum, and wet, it won't work.
Yes, you can insulate thru-bolts. It requires a micarta or fiberglass washer under the bolt head or nut, between the stainless and aluminum, and a micarta or fiberglass tube which just fits inside the washers and is just a hair shorter than the tightened joint. It's a pretty common arrangement. Aluminum hardware, if you can find it, or nylon hardware if it's strong enough is another solution. Good luck.
Regards,
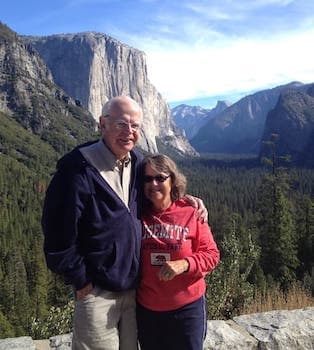
Ted Mooney, P.E. RET
Striving to live Aloha
finishing.com - Pine Beach, New Jersey
Fasteners to repair aluminum boat
Q. I have an old 1962 18' riveted aluminium boat that I am rebuilding. The bottom inside of the boat has a lot of galvanic corrosion. I believe it is built with 1/8" 5056 aluminium. I am planning on cutting 3" strips of 5056 1/8" aluminium and attaching them to the outer skin of the whole bottom of the boat. I would coat the inside of the strip with 3M 5200 adhesive sealant, then fasten to the boat....I need to find very strong shear and tensile fasteners so I can pull the strips of aluminum to the curves of the boat tightly. I am looking for a fastener that will not cause galvanic corrosion with the 5056 aluminium boat, and that one person can install. The best I could come up with is 3/16" closed blind rivets made with 1100 aluminium, they would work but have a very low tensile and shear strength. The same thing made of 5056 or 6061 with an aluminium mandrel would be much stronger but I can only find those with a steel or stainless mandrel. ( I am not sure how concerned I should be about the galvanic corrosion, as they will be exposed to mainly fresh water but at times salt). Maybe the alum/ stainless or steel mandrel rivets would work if filled with the 3m 5200 or a marine epoxy putty like jb_weld_marine?
Maybe I should be looking at something other than a closed rivet? Or maybe there is another type of rivet or fastener that you can suggest that one man can install, is sealed, strong, and won't corrode?
I am looking for about 2000 fasteners for this project, the way I have it thought out now. Any ideas about a better way to do the repair and/ or the best fastener you can come up with would be very much appreciated.
- Whitehorse Yukon Canada
May 27, 2018
A. Outboard motor castings with numerous stainless screws corrode very badly, of course. Generally disassembly includes small fasteners snapping or breaking off, probably due to stress corrosion together with galvanic phenomena - then a wirefeed and an old nut come into play to get the remaining threaded part out of the aluminum casting.
But to the prevention of trouble so that next time there will be a nondestructive disassembly:
Clean hole. Coat screw with nickel or zinc anti-seize
⇦ on
eBay
or
Amazon [affil links] and fit it several times into hole, blow residue but do not wash out the hole. Reapply the anti-seize and add a small amount of Loctite … red is fine. Works well. Similarly works fine on motorcycles.
I sometimes use RTV or a heavy coating of aluminum spray paint on threads, sometimes with Loctite … it depends.
Me? Retired millwright. The paint trick, with blue or red LT helps on rebellious gaskets and mating surfaces too.
- red bluff California usa
Minimizing galvanic corrosion between 6061 and 316
RFQ: The application is marine.
We are using an aluminum sailboat mast section as a catamaran beam.
The beam supports a deck by connecting a 316ss angle via stainless strapping to the beam with rivets.
The concern is if we use 316 strapping and 316 angle and say a 316 rivet that the corrosion will land in the beam.
We intend to chromate convert and paint the beam. The inside of the beam may also get periodic Alodine treatments.
The same beam also has some other connections planned with some thru bolts of 316 to support a box or locker. The bolts can be nutted with 316 epoxied to the inside of the beam.
I would like to hire a consultant on this project for advising the metal connections.
The issue is further complicated because I need to setup the system and tear it down for finishing.
So, while the designer suggested rivets, they are a bit too permanent.
Without advice, I would probably use some smaller aluminum rivets and drill them out.
If anyone is interested in consulting, please provide a contact number. Thanks.
Owner - Inver Grove Heights, Minnesota, USA
December 25, 2018
Ed. note: This RFQ is outdated, but technical replies are welcome, and readers are encouraged to post their own RFQs. But no public commercial suggestions please ( huh? why?).
A. There is a product available for avoiding corrosion between dissimilar metals-in my case aluminium and stainless steel (marine environment) It is (was?) commonly used in the aircraft industry for aluminium rivets. It is cadmium sulphate? based, so google it and handle with care as it is reputedly possibly carcinogenic. I have successfully used this for many years on my yacht, and know of many here (Australia) that use it. I buy it at a marine chandler. It comes in a tube, is bright yellow, sloppy gel-like and hardens. It will allow easy removal of s/s bolts from aluminium many years later, even those threaded one into the other.
frank centa- Karrinyup western australia
----
Ed. note: please see also Dan's earlier question 60863. Generic solutions are welcome! Apologies, but we must reject testimonials to proprietary products and their secret ingredients (huh? why?). We thank you for your effort to help, but suggesting specific brands & sources has proven to not work on this 'no registration' site.
Q. I wish to use 316 stainless flashing under an aluminum skylight frame, in a wet marine environment. Water will collect at two sides of the skylight, due to its placement on an outside corner. The existing galvanized flashing is totally destroyed, and the skylight frame looks like it has been affected.
I considered the damage was caused by galvanic action. However, I understand the skylight is anodized. If that is a long term fix, then was the damage not caused by galvanic action? Can I use stainless under the new skylight? If there is a problem can I use a insulating tape such as Heskins H3453 or 3M 51? ⇨
Ballough Construction - Playa Del Rey California USA
June 30, 2019
A. Hi William. Yes, insulating tape is a perfect idea for preventing galvanic corrosion if the aluminum and steel will not be connected by screws or any other metal to metal connection.
I would agree that stainless steel flashing will be better than galvanized. Good luck.
Regards,
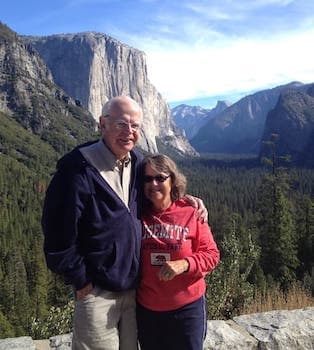
Ted Mooney, P.E. RET
Striving to live Aloha
finishing.com - Pine Beach, New Jersey
Q. Can anybody comment on using stainless steel fender trim on a aluminum body pickup around the wheels using stainless steel screws to fasten together. These would be subject to rain and salt and ice in the winter.
Dennis Myers- Joplin, Missouri usa
September 2, 2019
A. An article appeared in the September 2019 issue of Products Finishing that readers of these questions may find useful: https://www.pfonline.com/articles/fixing-corrosion-between-anodized-aluminum-and-steel
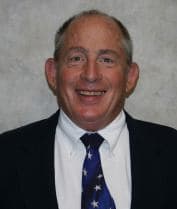
Tom Rochester
CTO - Jackson, Michigan, USA
Plating Systems & Technologies, Inc.

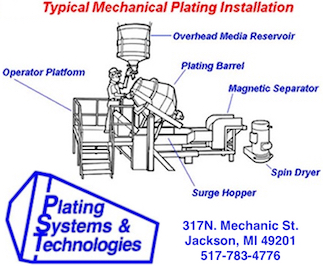
Ed. update 2024: The article which Tom references is now considered "Premium Content" and requires registration with that site :-(
Will finishing.com be the last fully open site on the internet? In other news, spam now exceeds requested or welcomed e-mail worldwide.
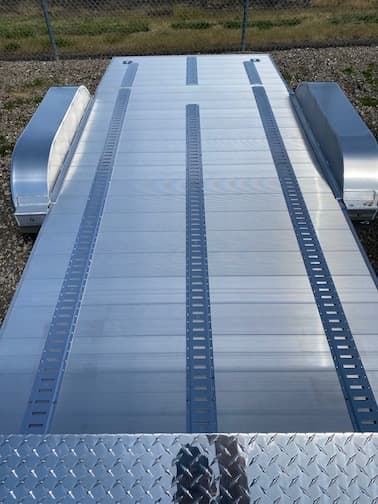
Q. Hello. I have an all aluminum car hauler and it has two situations I need input on.
1: along the Aluminum deck there are E-Track Tie down rails made of aluminum, fastened to the Deck using stainless self-drilling screws.
2. On the main drain near the hitch there are steel brackets part of the hitch assembly, and a steel coupler assembly.
The trailer is not in a salt-water environment but is stored and used outside in the Pacific Northwest rain.
Since the aluminum is massive and is hundreds of times more volume than the stainless screws, or single bracket on the frame - is this a terrible set up?
- Portland, Oregon, USA
July 2, 2020
A. Hi John, it's probably okay. But another thing to think about is how conductive any wetness is. If it's rainwater, which is not far from distilled water in a non-industrial, non-salty environment, you're not very subject to galvanic corrosion; but if fertilizer is commonplace in the storage area, de-icing compounds, etc., are commonplace on the roads, then you are.
Luck & Regards,
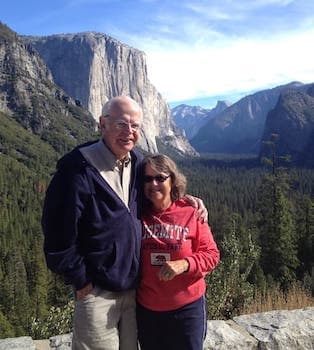
Ted Mooney, P.E. RET
Striving to live Aloha
finishing.com - Pine Beach, New Jersey
Hi there
I just bought a solid Aluminum ball mount and a stainless steel ball. Will I have galvanic corrosion issues here? I contacted the manufacturer of the solid aluminum ball mount manufacturer, and they had no idea what I was taking about...
Can I put some type of isolator between the ball and nuts fastening the ball on the aluminum mount?
Perry decuir- Los Angeles, California
July 8, 2020
A. Hi Perry. Both galvanic corrosion and quicksand are real, but it's possible to worry too much about them as well :-)
I'm having a hard time understanding the value of an aluminum ball mount though ... and if galvanic corrosion should be worried about, what about where the ball mount inserts into the receiver? And what about the hitch pin connecting the ball mount to the receiver? These would seem to have a far more corrosive effect on the ball mount than the ball will.
Luck & Regards,
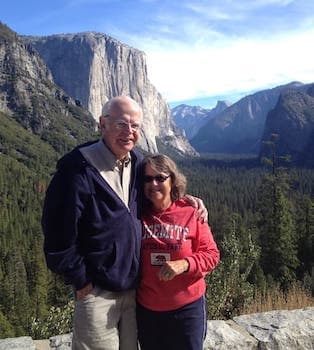
Ted Mooney, P.E. RET
Striving to live Aloha
finishing.com - Pine Beach, New Jersey
Q. Hi,
I'm designing an electrical enclosure for industrial-duty lab equipment that's planned to last for ~25 years.
The electrical panel is located inside of the equipment (not sealed, it's open front), but it's going to be humid in there. There's a heated water bath using DI water that's part of the process. It's somewhat located away from the electrical panel, but the entire interior of the machine shares that air. So, I expect that I'll see condensation on both interior and exterior of the panel, and should plan for the rare drip/leak of DI water onto the exterior of the box.
I'm only able to use powder coated steel, or trivalent chromate conversion treated aluminum as the enclosure box material. I'm currently leaning towards Type II, Class 3 conversion on 5052 aluminum.
The goal is to keep conductivity as high as possible for a few key grounding points, for the entire life of the machine.
For hardware, I'm leaning towards zinc plated steel. Much of that will be accomplished with PEM brand pressed-in nuts. Being zinc plated, the fabricator I'm working with wants to chromate the aluminum enclosure first, then press in the nuts afterwards. So, the chromate coating would be penetrated around the fastener.
Some of the of the ground paths (for electrical filtering, not safety) will be bonded to the aluminum enclosure through the fasteners.
I'm planning on directly bonding the safety related ground points together, which are tin-plated (aluminum or copper substrate) electrical terminals or electrical bus hardware.
Most of those connections will be a sandwich of:
zinc plated fastener stack -> chromate coated aluminum panel -> tin plated copper -> tin plated copper-> zinc plated fastener stack.
Will those combinations be OK for low electrical contact resistance increase and mechanical integrity over the 25 year planned life-span? My research on galvanic corrosion has led me in circles on this choice of materials.
Is there a better combination available, such as moving to stainless hardware, or another substrate material? Or, will I need to use a sacrificial anode of some type, dielectric or conductive greases, or the like?
For self clinching nuts, there's really only a choice of various stainless alloys, or zinc plated carbon steel. Aluminum is an option, but then mechanical issues like limited clamping force and thread durability come into play.
It's possible to avoid self-clenching sheet metal hardware and go for a through hole with screw or stud of some different material for more critical electrical bond joints.
Any advice would be greatly appreciated. Thanks!
- Woodbridge Virginia
September 15, 2020
A. Hi Jim. Except when the fasteners are prohibitively expensive I think stainless steel is much better than zinc plated, especially in contact with aluminum. But stainless is not a very good conductor.
Other than that, I think the plan is sound except that 25 years is a long time and it's hard to make broad general predictions about an installation lasting 25 years when my understanding of your situation is marginal :-)
Luck & Regards,
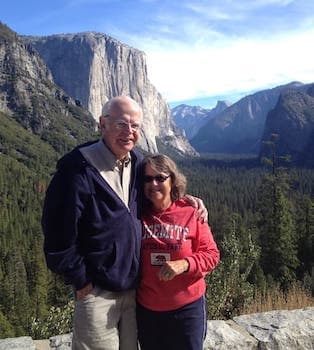
Ted Mooney, P.E. RET
Striving to live Aloha
finishing.com - Pine Beach, New Jersey
A. I would use a touch up pen to cover up any scratches on your aluminum, also if you can use titanium bolts and fasteners, it will last longer. Titanium although more noble than stainless, the kinetics are slower. Just a warning though: aluminum is very prone to galvanic corrosion.
Bob Hagerty- Patuxent River, Maryland
September 28, 2020
Q, A, or Comment on THIS thread -or- Start a NEW Thread