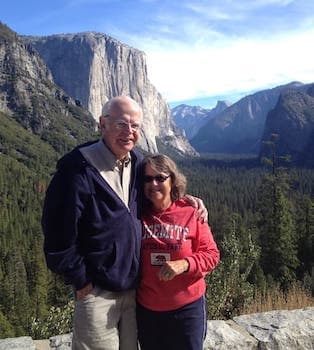
Curated with aloha by
Ted Mooney, P.E. RET
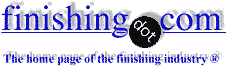
The authoritative public forum
for Metal Finishing 1989-2025
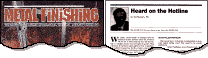
-----
Anodize, or Alodine or paint Aluminum Catamaran structure?
Q. I have 3 aluminum beams in a catamaran. They are a sailboat mast converted for use as beams.
They are big cylinders. About 10"x6" and 3/16" thick. 16' long
If we anodize, it will not get to the middle per the local vendor.
Alodine is needed in the inside.
But is painting or anodizing a better idea?
Thanks!
Builder - Inver Grove Heights, Minnesota, USA
September 30, 2018
September 2018
A. Hi Dan. Although it's possible to partially anodize and partially chromate conversion coat (Alodine), it's a bit complicated and reserved for applications where it's really needed. And anodizing the inside of a tube is hard (and difficult to prove). I think your best answer is to Alodine it both inside & out, and then paint everything you can reach.
You probably know this, but you never apply bottom paint (ablative copper) to aluminum.
Regards,
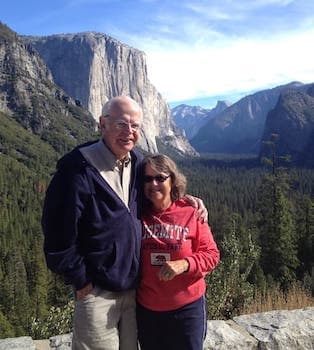
Ted Mooney, P.E. RET
Striving to live Aloha
finishing.com - Pine Beach, New Jersey
Q. Thanks Ted! The Alodine would be getting brushed on the inside with a sock on an 8.5 foot stick.
Will the Alodine apply evenly enough with a brush on the outside for a suitable paint finish?
And does the Alodine replace the etch step so I would go right to primer?
These same beams need fastenings. Bolts and rivets. The bolts and rivets could be a variety of items, but I am leaning towards anodized aluminum to reduce the galvanic corrosion in seawater. Most of the hardware in the boat is 316SS, but I am concerned the bolts might eat the beam. Can you advise or recommend fastenings? The exposure to saltwater is not high, but possible via the ends of the beam which are open to marine environment and breaking waves. The beam fastenings are mostly for locating and do not need the strength of 316. The rivets are also fine in aluminum, but they would not be anodized and people told me monel would be preferred. Thanks!
I am really grateful for the response Ted.
- Inver Grove Heights, Minnesota, USA
October 1, 2018
October 2018
by Stephen F. Pollard
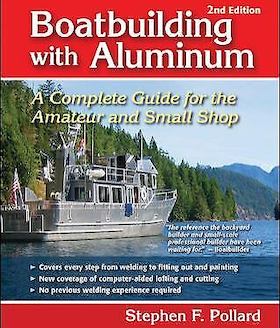
on eBay or
AbeBooks
or Amazon
(affil links)
A. Hi Dan. Since you were considering anodizing as an alternative, and you were talking about a local vendor doing it, I thought you were planning on immersing these tubes -- which is really the right way to do it. And I thought your vendor would take the tubes through the proper sequence which includes non-etch alkaline cleaning, de-smutting appropriate to the alloy, and Alodine (with rinsing between each stage).
I imagine manual cleaning, followed by manual brushing of Alumiprep 33 ⇦ this on eBay or Amazon [affil links] and Alodine 1201 ⇦ this on eBay or Amazon [affil links] can be done, but you should probably check with Henkel.
Yes, if strength is not needed, anodized aluminum fasteners could be used if you can find them. Aircraft specialty suppliers would have high strength aluminum coated steel fasteners, but I'm not aware of aluminum coated stainless or monel fasteners. Boats have their unique dangers, so having a marine surveyor review your plan might catch a weak area.
Regards,
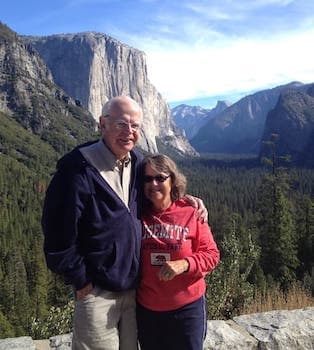
Ted Mooney, P.E. RET
Striving to live Aloha
finishing.com - Pine Beach, New Jersey
October 3, 2018
Hi Dan! I'm a catamaran sailor myself and can give you a couple observations about the construction of the classic Hobie Cats. The rails are anodized Al and the fittings and fasteners are a combination of Al and stainless (I'll go home and check to see what is used where). My boats are 1971 and 1984 models, and regularly see salt water. I sail with a club out of Naragansett Bay RI and a couple of us have pretty old and busted boats! Save for some discoloration on the stainless components, there has not been an issue with corrosion enough to cause strength concerns or binding of the travellers as they slide along the rails. If you can find high strength Al rivets as Ted suggested, that is great. But you should not have to worry much about things like padeyes and rails that are in direct contact with the anodized surface, if you choose to go that route.
Also as Ted said, Alodine only works when the surface is correctly prepped- Squeaky clean and devoid of any existing oxidation.
An Alodine-paint combination, or, even better, a 2-stage epoxy meant for use in UV exposed applications, would provide very good protection, and this is commonly done on components meant to be used in challenging environments.
I'd personally Alodine the inside of the tubes and then seal them off watertight for flotation reasons.
One thing I'll add here is that if you haven't thought about your rudder pins and brackets yet, my strong suggestion is to have them hardcoat anodized, because of the constant abrasion metal-on-metal and metal-on-sand. And have a couple extra sets made for spares ... Inspect and clean regularly and swap out as soon as you notice grooves forming. We had a guy get blown out on his H16 to Falmouth (lowest tip of Cape Cod) a couple years ago after snapping a pin and not being able to tack! He was lucky, because the next point of land is Cape Verde or the Canaries :)
Here's a link to a tech sheet for the brush-on version of the chromate coating we use at work, that should give you some idea of what to expect: http://www.galladechem.com/specs/macdermid/78660.pdf Iridite (Macdermid-Enthone) and Alodine (Henkel) are simply different proprietary product lines formulated to meet the same specs. Be aware that a product designed for immersion application may not work correctly as a brush-on, and vicw versa, so make sure to get the brush-on version of whichever one you go with. And I can't stress enough that the deoxidizer (in this case, Isoprep) is crucial to the chromate reaction occurring correctly.
Happy sailing!
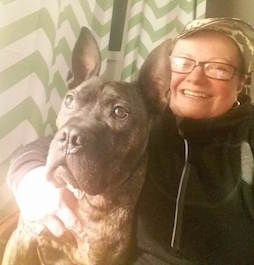
Rachel Mackintosh
lab rat - Greenfield, Vermont
Thank you Ted and Rachel, I spoke with a pro today and he suggested Alodine and powdercoating within 72 hours and would not guarantee the inside.
The parts will have penetrations, so capping the ends might result in trapped saltwater or environments trying to exit some threaded area. Not good, so we will leave open.
This is a powercat and these are removable beams. No sail rigs.
The insides do not need to be pretty, so perhaps the powdercoating people could paint the insides for me after chromate conversion.
Thanks to all. I really like this forum. It is a bit hard to use, but worked!
- Inver Grove Heights, Minnesota, USA
October 4, 2018
![]() |
Hi Dan. The interface can perhaps be improved if you explain what you feel makes it hard to use. Thanks. (Dan has also posted thread 27167 on this subject) Regards, ![]() Ted Mooney, P.E. RET Striving to live Aloha finishing.com - Pine Beach, New Jersey October 2018 |
December 27, 2018
Q. I want to follow up. Ted aptly pointed out I double posted a bit.
I am looking for a consultant. This is a demountable powercat; not a sailboat. The demounting is where the intersecting of ss and aluminum will occur. The cat beams are large 6061 mast sections from sparcraft. There are three in the boat. A 10', a 14' and a 16' section. The 16' section is the complex one.
The powder coating people told me powdercoating chromate converted aluminum is a guaranteed way to invite trouble, bybthe way... but this is not too large a concern. I was advised to chromate convert and then paint.
The complexity arises in the connections.
There are rivets to the beam and stainless strapping welded to large stainless angle irons that will drive potential I fear and galvanics.
The trouble is the strapping to support the angles by the beam must be strong and aluminum is not. So the strapping must be 316 or something that won't fatigue easy and break like conventional aluminum. For this reason and strength reasons, I have already purchased the 316 angles. The strapping will get welded to the angle and then the disastrous bit. We rivet the strapping to the beam. If we use an aluminum rivet; it may fail at sea and while simultaneous failure of say 9 rivets is unlikely; failure is certain. If we use a stainless rivet; the holes will eventually fail which may be safer and more manageable, but it might be quicker than desired.
In an ideal world; we would use a rivet that insulates the stainless from the aluminum. The designer suggested monel rivets, but I don't know if that is good.
An added difficulty is rivets are less than ideal here. I will need to spot them and drill them out or use a small bolt and rivet into the threaded hole to build things prior to finishes. The section is about 0.150 thick. So we considered just threading the section for setup. Any physical bolt would be nearly impossible to attach as they are inside the section 5-8 feet in. However, a nut could be epoxied if you could ever locate it... I will probably use say a #8 ss machine screw for setup...
Again, would prefer to pay for consulting; I could send pictures, etc.
Owner - Inver Grove Heights, Minnesota/USA
Ed. note: This RFQ is outdated, but technical replies are welcome, and readers are encouraged to post their own RFQs. But no public commercial suggestions please ( huh? why?).
Q. I have an 5086 Aluminum sailboat which has a swing keel which disassembles like a hinge with a stainless steel pin. After 30 years part of the hinge has corroded. For the replacement parts (they could fit in a 5 gallon bucket), I am wondering if type III anodizing is best solution for area of contact with stainless.
Second part of question is can I paint rest of part with epoxy primer and then anti-fouling paint. Would I need to rough up the anodizing?
How does anodizing accept paint?
For extra protection, the joint between aluminum and stainless would be coated with Duralac or similar.
DIY SAILOR - SEABROOK, Texas, USA
February 2, 2019
A. Hi Greg. Type III anodizing is extremely abrasion resistant and highly insulating, so I think it would be perfect for the hinge pin slot. There are some observations on this site that acetone cleaning worked well for paint adhesion on Type III (as long as acetone cleaning is compatible with the selected paint).
If all of the aluminum parts are flawlessly anodized, it m-i-g-h-t be okay to use ablative paint on aluminum, but few things are as destructive to aluminum as copper (the active ingredient in anti-fouling paint) because of the huge electromotive potential difference.
Regards,
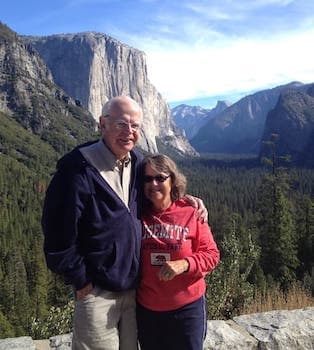
Ted Mooney, P.E. RET
Striving to live Aloha
finishing.com - Pine Beach, New Jersey
February 2019
Q. This is looking like the best option! The anti-fouling would never have copper in it for Aluminum boat, there are alternatives. A primer or barrier coat would be applied first. As far as adhesion, would I want to seal the anodizing or leave it open pours? I realize the pores are small and even dying is difficult.
As far as "flawlessly anodized", this has had marine paints on it for 30 years, what is best way to specifically target the paint which is embedded in corrosion crevices and pits. Research points to nitric/phosphoric acid mix, but there is no mention of removing paints. I am Dremmeling out the corrosion and welding back the metal, but....
One last question: 5086 is difficult to get in the size I need, if 6061 was used and anodized (Type III), it could be a viable alternative for under water use? Any comment appreciated!
Researching acetone cleaning now.
Thanks, great site!
DIY SAILOR - Seabrook, Texas, USA
February 5, 2019
A. Hi again. Glad there are non copper anti-fouling paints for aluminum; the only ones I knew of, way back when, were tributyl tin (an environmental disaster which was banned).
If you search the site for "paint hardcoat" or "paint type III" you can see the original comments on that subject rather than my transcription.
Aircraft Stripper is really noxious stuff, but it specifically for removing paint from aluminum and other soft metals.
Although 5086 is known for its corrosion resistance and good strength, once you hardcoat 6061 it seems like it should be a fine material for corrosion resistance. Reportedly, 5086 is the material of choice for yachting but 6061 is often used on smaller skiffs and such.
Regards,
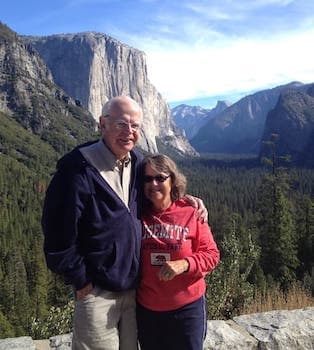
Ted Mooney, P.E. RET
Striving to live Aloha
finishing.com - Pine Beach, New Jersey
February 2019
Q, A, or Comment on THIS thread -or- Start a NEW Thread