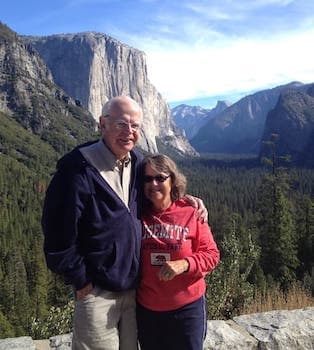
Curated with aloha by
Ted Mooney, P.E. RET
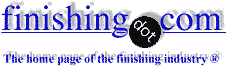
The authoritative public forum
for Metal Finishing 1989-2025
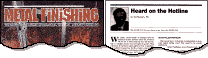
-----
MIL-DTL-5541 Class 1A vs. Class 3

Quickstart (no readers left behind):
Aluminum is often 'chromate conversion coated' as a corrosion resistant final finish or as a pretreatment for painting or powder coating. The process actually involves many steps, usually including alkaline cleaning, etching, deox/desmut, the chromate conversion step per se, and water rinses between each step.
MIL-C-5541 / MIL-DTL-5541 / MIL PRF-5541 is the most commonly cited spec. "Alodine" and "Iridite" are proprietary trade names from two suppliers of the process chemistry. "Chem film" is a slang term for the process often used in the USA.
Q. When customer does not specify the class (1A or 3) is there a rule that says that I should revert to one or the other if not specified?
Tammy Pennington- West Carrollton, Ohio
September 20, 2022
A. Tammy,
Buried down in 6.5 (of revision F) is: "If the coating class is not specified, class 1A is recommended."
Note that "recommended" does not mean a requirement, and the entire section 6 is marked non-mandatory.
Unlike the very clear "If no material type is specified type I shall be used" in 3.1, the choice of class if none is specified seems to be ultimately up to you.
Of course, you could also ask the customer if they have a preference and neglected to mark it on the drawing or purchase order.
Ray Kremer
Stellar Solutions, Inc.
McHenry, Illinois
⇦ Tip: Readers want to learn from Your Situation 🙂
many readers skip abstract questions.
Q. I need to to know and understand exact chemical composition of
MIL-DTL-5541
[⇦ this spec on DLA]
Type I Class 1A
MIL-DTL-5541
Type I Class 3
MIL-DTL-5541
Type II Class 1A
MIL-DTL-5541
Type II Class 3
Could you please help me to provide chemical composition ?
- Pune & Maharashtra / India
August 11, 2023
A. Hi, Pratik, please introduce yourself. It is very difficult to know how to answer such a question when we don't know whether you are a plating shop employee, a PhD researcher, a development manager for a major chemical company, someone who is doing an environmental cleanup, etc. -- but I'll try to respond anyway :-)
Apologies, but nobody is going to be able to do that for you :-(
The problem is that you cannot comply with the MIL-DTL-5541
[⇦ this spec on DLA] conversion coating spec except by using a particular mix of chemicals that is on the qualified products list (QPL-81706
[⇦ this spec on DLA]) and there are no generic mixes of chemicals that comply, only trade secret formulations like Alodine and Iridite -- and nobody can/will reveal those closely-held trade secrets to you.
However, if you simply want to do chromate conversion coating without complying with any specifications, the Type I formulations are long-established and there are a number of typical formulations, but some of the older ones contained cyanides and other problematic materials.
If you are a major chemical manufacturer and which to develop a line of chromate conversion chemistry and get it qualified, it's a big job but do-able. But if you are a plating shop you can't do MIL-DTL-5541 unless you buy proprietary chromate conversion chemistry.
Luck & Regards,
Ted Mooney, P.E. RET
Striving to live Aloha
finishing.com - Pine Beach, New Jersey
A. Not sure if this is helpful but my understanding is Type 1 is formulated with hexavalent chromium and Type 2 is trivalent.
Chris Jurey, Past-President IHAALuke Engineering & Mfg. Co. Inc.

Wadsworth, Ohio
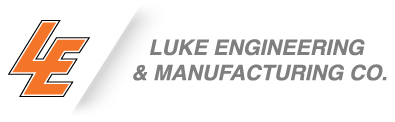
August 30, 2023
⇩ Related postings, oldest first ⇩
Q. I have a piece of equipment that is coated to MIL-C-5541 class 1A. I have a customer that desires it to be coated to MIL-C-5541 class 3.
If he provides no specific conductivity requirements, could the class 1A coating potentially satisfy the class 3 rating? How can this be shown?
If he provides a conductivity requirement, how can I establish that the current coating does/does-not meet his class 3 requirement?
Thanks,
Matt Landelavionics system engineer - Amherst, New Hampshire, United States
2003
A. Class 3 requires low electrical resistance. Only a thin coating or a bleached coating will meet the requirements. There is a standard ASTM test for contact resistance. It consists of a ball contact with a specific pressure. Note. In my opinion, the test is not very good: if the coating is broken by the pressure the conductivity is good. Therefore if the test surface is slightly rough or very rough the test will pass for almost any chromate coating. However, you must comply with the test by having a qualified laboratory perform the test and certify the results.
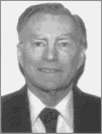
Don Baudrand
Consultant - Poulsbo, Washington
(Don is co-author of "Plating on Plastics" [on Amazon or AbeBooks affil links]
and "Plating ABS Plastics" [on Amazon or eBay or AbeBooks affil links])
Treatment &
Finishing of
Aluminium and
Its Alloys"
by Wernick, Pinner
& Sheasby
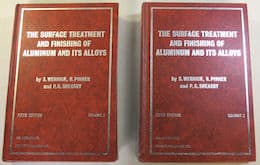
(note: this book is two volumes)
on eBay or
AbeBooks
or Amazon
(affil links)
A. Electrical Contact Resistance testing for MIL-C-5541E Class 3 is only required if specified. The procuring activity is responsible for specifying the test method, frequency of testing, and required resistance values. If this testing is not specified, the only requirement on the applicator is to use materials listed on QPL-81706 [⇦ this spec on DLA] for Class 3 and to perform the other required testing, i.e., Appearance, Corrosion Resistance, and Paint Adhesion. Many QPL materials are approved for both Class 1a and 3.
Chris Jurey, Past-President IHAALuke Engineering & Mfg. Co. Inc.

Wadsworth, Ohio
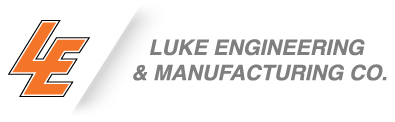
![]() |
Q. Hello, everybody! I really need your help because I meet a trouble now. I know nothing about chromate treatment so I don't know how to do my product finish. The specification of chromate treatment is MIL-C-5541. If anybody has this file, please give me a copy or tell me where can I download it. Thanks! WEI GAO- Ningbo, Zhejiang, China 2004 A. Try this site for downloading [US] military and federal standards:
- Wilmington, Massachusetts ---- |
Multiple threads merged: please forgive chronology errors and repetition 🙂
Q. Problem: MIL-C-5541 Class 1A vs Class 3. A certain customer has requested (i.e. engineering, specifications, etc.) that their aircraft parts be Chem-Filmed with two different processes and results. One side of the part is to be processed per "MIL-C-5541, Class 1A," then primed. Masking. No problem. The opposite side is to be processed per "MIL-C-5541, Class 1A, Clear Coating" with no primer applied. Possibly an aircraft appearance item. I am no expert in this field, but according to MIL-C-5541/AMSC5541, there is no "Clear Coating" that can be applied to the requirements of Class 1A. As far as I can ascertain, "Clear Coating" can only be applied per Class 3. Unless someone knows something I missed, basically all Class 1A approved chemicals will exhibit color after application. My thinking may be, possible engineering error?
I have a motto that I have kept and lived by for almost 25 years. "Do Right By The Airplane" I can use some input and guidance with this issue.
Thank You,
Brad Huddlestonaerospace quality assurance engineer - Wichita, Kansas, USA
2004
A. We both share the same view that this could be an engineering spec. error. However, I note that there is a grey area in the MIL spec class I esp. in the color. It specifies a range of color. And one of the most common chemicals available for this class, i.e., Alodine 1200S could be used to produce a clear coating also.
Asyong [last name deleted for privacy by Editor]- Toronto, Ontario, Canada
A. If you are talking about "bleaching" with hot water, forget it. Color-wise, it may look good, but to the protective requirements of MIL-C-5541, it will more than likely fail.
When it comes to aircraft up to 5 miles above this ground, I do not like taking chances or cutting corners. There are Class 3 compatibles out there. Alodine 1100 and 1500 I believe.
Talk Later, Regards.
Brad Huddleston [returning]- Haysville, Kansas, USA
2004
A. You are correct. Class 1A is less electrically conductive than class 3 and has a gold color. Class 3 also may have a very light gold tint as they are both processed the same with immersion time in our Alchrome II bath being the only difference. We run into this error quite often and the disturbing thing is that most times the customer cannot answer as to which class they actually require.
Good Luck.
Tim Knoxmetal finishing shop - Springfield, Vermont, USA
A. The easiest answer is to leach the color from the side that is not painted. Use hot water. Iridite 14-2 "clear" is qualified as class III when leached. It will pass salt spray requirements of the spec. Yellow Alodine may not pass SS, and it is not qualified class III whether leached or not.
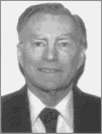
Don Baudrand
Consultant - Poulsbo, Washington
(Don is co-author of "Plating on Plastics" [on Amazon or AbeBooks affil links]
and "Plating ABS Plastics" [on Amazon or eBay or AbeBooks affil links])
A. In my opinion Alodine 600 is applicable for type 3 coating.
Rajeev [last name deleted for privacy by Editor]- Bangalore, INDIA
November 14, 2012
Ed. note: To the maximum extent possible, gentle readers, please talk technical issues, not brand or sourcing issues (why?). Statements which might imply that MacDermid products are 'better' than Henkel products or vice-versa have quickly led to a race to the bottom :-)
Multiple threads merged: please forgive chronology errors and repetition 🙂
Q. My company has been doing class 3 conversion coatings per MIL-C-5541 for years. We send our coupons out for testing to the 168 hours salt spray per the standard. We also perform the wet tape testing per the standard. Does this also qualify us to do class 1A finishing?
We have been subcontracting class 1A finishes, but reading the standard, I see no difference other than the conductivity for which there is no testing mandated.
If we do the required test to qualify us to do class 3 finishes, does this qualify us to do class 1A? What's the difference?
metal products - Cedar Rapids, Iowa USA
2006
![]() |
A. If you use one of the products listed on the QPL for both Class 1a and 3, the testing for Class 3 will also meet all of the requirements for Class 1a. Chris Jurey, Past-President IHAALuke Engineering & Mfg. Co. Inc. ![]() Wadsworth, Ohio ![]() A. Yes and no in varying degrees. Nobody understands that spec! If you "pass" salt spray with Class 3 you surely will pass with 1A, but that does not necessarily "qualify". So you should do panels both ways. Some people think the difference is yellow versus clear because that is the practical interpretation; however, there is nothing in Class three about "clear". ![]() Robert H Probert Robert H Probert Technical Services ![]() Garner, North Carolina ![]() |
A. There are several differences between a Class 1A and a Class 3 coatings, to include salt spray testing requirements.
4.3.3 Option 2 states:
The specimen panels shall be 2023-T3 aluminum alloy panels per QQ-A-250/4 for class 1A coatings and 6061-T6 aluminum alloy panels per QQ-A-250/11 for class 3 coatings. If desired, 2024-T3 panels may be used in lieu of 6061-T6 panels for testing class 3 coatings (see 6.8).
Section 6.8 states that due to high copper content, 2024-T3 is more susceptible to salt spray failure than 6061-T6.
So why would you want to use 2024 in the first place if it has a greater chance of failure?
Another thing to consider is coating weight. If parts are being run to class 3, (i.e. minimal coating weight), 2024 will have 2-3 times the amount of coating weight as compared to 6061 or even 5052. To verify this I recently ran three sets of five panels each of 2024-T3, 5052-H32 and 6061-T6. In this case I ran parts to class 1A using Alodine 1200S. All parts were run on the same rack at the same time. The average coating weight of each of the three sets was: 2024-T3 - 1.99 g/m^2; 5052-H32 - 1.10 g/m^2 and 6061-T6 - 0.54 g/m^2. (According to ASTM B449 these all meet the requirements of a maximum corrosion resistant class 1A coating.)
The ASTM B449 definition of a class 3 low electrical resistance coating is a coating mass <0.1 g/m^2. 2024 is hard enough to get to pass when doing class 1A let alone class 3 and if you meet the definition as presented above, I don't know that you will get a class 3 coating to pass using 2024.
However, this may all be a moot discussion with the advent of trivalent based coatings which provide both class 1A and class 3 properties at the same time.
Indianapolis, Indiana
A. I do think it is the specification MIL-DTL-5541 itself leading to so much confusion. If it defines class 3 is the low conductivity concerned only, when no low conductivity required, you should come to class 1A, then nobody will be confused.
Daniel Ning- SH, China
January 24, 2011
Multiple threads merged: please forgive chronology errors and repetition 🙂
Q. When coated on aluminium, do we call Mil C 5541 Class 3 "clear chromate" or "clear anodising"?
Jimmy kohEngineer - Minneapolis, Minnesota
October 5, 2011
A. Hi, Jimmy.
We call it chromate conversion coating; some people call it chem-film. Anodizing is a very different process.
Regards,
Ted Mooney, P.E.
Striving to live Aloha
finishing.com - Pine Beach, New Jersey
Q. Hi. I have a question. The company I work for wanted to know if a class 1 can be used as a substitute for class 3?
malinda culley- ozark, Alabama
July 27, 2015
A. Hi Malinda. Essentially, "no". The situation is that you can't comply with MIL-DTL-5541 without processing per its instructions and using the qualified products. Good luck.
Regards,
Ted Mooney, P.E. RET
Striving to live Aloha
finishing.com - Pine Beach, New Jersey
A. Mooney is legally correct, but I have many clients who do a short dip in type 1a, call it type 3, and pass salt spray,
Robert H Probert
Robert H Probert Technical Services
Garner, North Carolina
Indeed Robert is correct too. If you are processing parts and have no obligation to conform to MIL-DTL-5541
[⇦ this spec on DLA], a satisfactory coating may well be applied via a short dip in a Class 1A solution -- and you might refer to "class 1a" and "class 3" as slang or shorthand to refer to the general type of finish you want to apply.
... much as you might "xerox" a copy of the spec on a Brother copier and "scotch tape" it together with generic cellophane tape rather than the 3M product :-)
Regards,
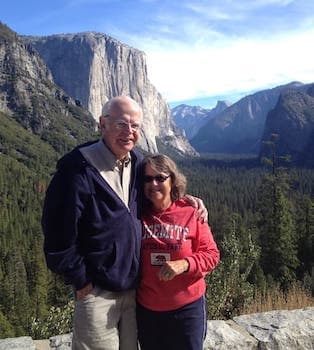
Ted Mooney, P.E. RET
Striving to live Aloha
finishing.com - Pine Beach, New Jersey
Q. What is the difference between MIL-DTL-5541 [⇦ this spec on DLA] class 1a and MIL-DTL-5541 class 3?
Rene RamirezInspection - Santa Ana California USA
August 13, 2015
A. Hi Rene. From the front page of the spec.:
But you have to download the spec.; I don't think you can inspect without it. Good luck.
Regards,
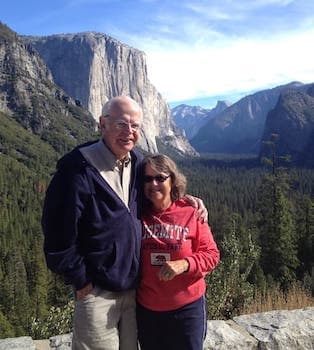
Ted Mooney, P.E. RET
Striving to live Aloha
finishing.com - Pine Beach, New Jersey
Inspection parameters for compliance to Mil-DTL-5541
Q. When attempting to comply with Mil-DTL-5541 section 3.7, how do you proceed if the customer fails to provide resistance limits for a Class 3 coating?
With regard to section 4.3.1, how do you proceed if the customer fails to establish AQL's?
I get the impression that people assign finish requirements without understanding them enough to satisfy the amount of information required to fully comply.
Any such thing as industry standards or defaults for these points?
Manufacturer - Frederick, Maryland USA
July 5, 2016
Hi Ed. We appended you inquiry to a thread where Chris Jurey seems to have already answered your first question.
Regards,
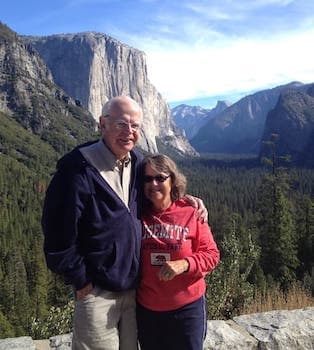
Ted Mooney, P.E. RET
Striving to live Aloha
finishing.com - Pine Beach, New Jersey
A. Ed,
Looking at the F revision here. It seems pretty clear to me.
3.7 points to 6.4, which states the PO needs to say "If electrical resistance testing if required for class 3 coatings" and what parameters to use when that testing is being required.
I would presume that if the PO doesn't mention it at all, that counts as not requiring the test.
4.3.1 gives a default sampling plan of ASQ-Z1.4, inspection level II, unless the PO states differently. This is backed up by a similar statement in 6.4.
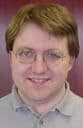
Ray Kremer
Stellar Solutions, Inc.

McHenry, Illinois
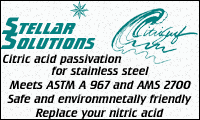
! I understand that Inspection Level II is the default and will determine the sample size but it does not address the AQL levels. The AQL levels determine that if in a sample size of say 15 pieces and you find 0 with critical faults, 3 with major faults and 3 with minor faults, the lot may or may not be considered good or bad.
Ed Peters [returning]- Frederick, Maryland USA
July 13, 2016
A. Ed,
I may be out of my depth now, but 4.3.1 Says: "Unless otherwise specified in the contract or order (see 6.4 and 6.18), the sampling plan and acceptance criteria shall be as specified in ASQ-Z1.4, inspection level II." I don't know what ASQ-Z1.4 says or doesn't say about acceptance criteria. 5541 seems to think it does.
The paragraph after says: "4.3.2 Visual lot examination. Samples selected in accordance with 4.3.1 shall be visually inspected for compliance with 3.5 and 3.9."
3.5 and 3.9 do not seem to define such things as critical faults, major faults, or minor faults. In the absence of such definitions I would tend to assume these are meant to be binary pass/fail inspections.
Beyond that, the first page of the standard gives contact info for "comments, suggestions, or questions on this document", so perhaps that could be your next step.
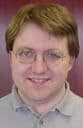
Ray Kremer
Stellar Solutions, Inc.

McHenry, Illinois
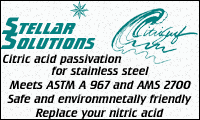
Q. Hello, I sent some parts for coating per: MIL-DTL-5541 TYPE 2, CLASS 3, must meet RoHS. What color is the coating supposed to be? I received yellow. is it OK?
koren tzAVCO - israel, YAVNE, HADAROM
August 29, 2017
A. Hi Koren. The color per se is not a problem unless you (or the ultimate customer if it's not you) specified colorless. See section 6.4e.
But something different than what you are used to is often a red flag that means it's time to double check what happened, and that the parts actually will comply with Class 3 :-)
Regards,
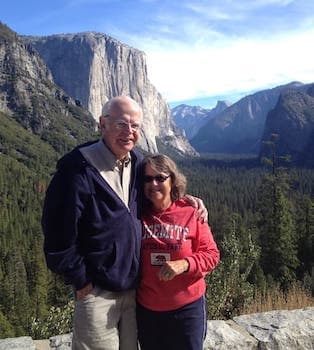
Ted Mooney, P.E. RET
Striving to live Aloha
finishing.com - Pine Beach, New Jersey
A. There is only one material on the MIL-DTL-5541 QPL for Type II and it is clear.
Joe Loughry- Anaheim California
July 3, 2021
Thanks for participating, Joe!
Although the QPL Database includes many different brands & application methods for acceptable Type II Class 3 coatings and, according to research studies such as "Cross comparison of TCP conversion coating performance on aluminum alloys during neutral salt-spray and thin-layer mist accelerated degradation testing" by Munson et al, there are variations in concentrations and performance -- it does seem that yes, they are all NAVAIR-developed and licensed "TCP", and I have also heard from QPL-approved vendors that they are inherently clear (or very very slightly brownish) and cannot be dyed.
So I think I have to accept Joe's point that if it's not clear, it seems either it's not RoHS-compliant or it's not MIL-DTL-5541 compliant :-(
Luck & Regards,
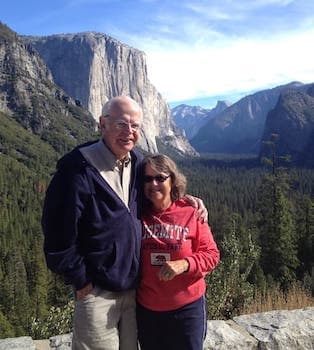
Ted Mooney, P.E. RET
Striving to live Aloha
finishing.com - Pine Beach, New Jersey
Ed. note: We've consolidated onto this page a number of threads about Class 1A vs. Class III chromate conversion coating, but it's a perennial issue; so even still, this is only one of several threads on the subject :-)
Please see also thread 4558, "MIL-C-5541 / MIL-DTL-5541 Class 1a vs. Class 3 Chromate Conversion Coatings" or search the site.
Q, A, or Comment on THIS thread -or- Start a NEW Thread