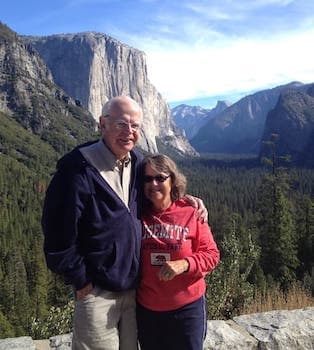
Curated with aloha by
Ted Mooney, P.E. RET
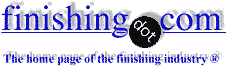
The authoritative public forum
for Metal Finishing 1989-2025
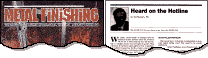
-----
MIL-C-5541 / MIL-DTL-5541 Class 1a vs. Class 3 Chromate Conversion Coatings
Quickstart (no readers left behind):
Aluminum is often 'chromate conversion coated' as a corrosion resistant final finish or as a pretreatment for painting or powder coating. The process actually involves many steps, usually including alkaline cleaning, etching, deox/desmut, the chromate conversion step per se, and water rinses between each step.
MIL-C-5541 / MIL-DTL-5541 / MIL PRF-5541 is the most commonly cited spec. "Alodine" and "Iridite" are proprietary trade names from two suppliers of the process chemistry. "Chem film" is a slang term for the process often used in the USA.
Q. MIL-C-5541-E, Class 1a (gold finish) vs. Class 3 (clear finish)
What is the difference between Gold Iridite and Clear Iridite in terms of process. Is there any favorable impact on cost if we require our vendor to do Clear Finish?
John Chuelectronics - Melville, New York
2000
Ed. note: Iridite is a Macdermid/Enthone trademark for their line of MIL-DTL-5541 Chromate Conversion Coating processes for aluminum.
A. Yellow chromate is thicker than clear and has more chromate in it so protects the metal considerably longer. Since most people want better protection, most shops do not offer clear. Some will legally bleach a yellow which is another step. Some will give it a very short tank time which will normally provide a substandard product.
Cost wise, you will probably be better off with yellow.
James Watts- Navarre, Florida
A. Class 1 or 1A yellow is usually called out for corrosion protection or as a pretreatment for paint adhesion, Class 3 is usually called out for electrical conductivity purposes. In actual practice many folks use the same processes for classes 1 or 3. However, many folks will bleach yellow to meet a clear call-out which results in substandard corrosion resistance, and won't meet salt spray specification requirements. There are good products out there for clear chromate which will meet salt spray requirements even for 2000 series. There should not be a cost impact between the two classes as long as the shop is set up to run both as the number of tanks, processing times and chemical costs are essentially the same. In terms of passing salt spray for clear, there are many letters at this site about this and most people in the business know the parameters required, some of which involve the salt spray coupons themselves.
Ward Barcafer, CEFaerospace - Wichita, Kansas
A. John,
The cost for either process is the same for my business, however, the end use of the product would probably dictate which to specify. The conductivity of 1A vs. 3, as Ward mentioned, is often the biggest reason to specify Class 3 (gold or clear). Some customers want the Clear Chromate finish only because they prefer the way it looks, without any regard or need for corrosion protection or relative conductivity. As James mentioned, Class 1A will give the product more protection longer and that may be the most favorable impact to cost.
Lamar Jackson- Fort Walton Beach, Florida
Ed. note: The postings above refer to hexavalent chrome coatings, and predate the world's big shift to RoHS-compatible trivalent chromium conversion coatings. With the new proprietary trivalent coatings and topcoats, it may no longer be true that yellow coatings are thicker or offer greater protection; these days the coatings are uncolored, but if there is any color it's probably just dye.
Q. Will clear Iridite process cause poor peel strength to a metal part? If Yes, Why and How significant different is it compared to a raw metal (no Iridite coating )?
Eric De Forzea- Malaysia
2001
A. Hi Eric. "Peel strength" of what -- paint or powder coating on the component? As long as the chromate conversion coating is done right, paint will stick better to it than to raw aluminum, and you will have better corrosion resistance too.
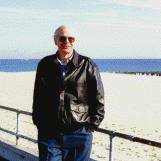
Ted Mooney, P.E.
Striving to live Aloha
finishing.com - Pine Beach, New Jersey
2002
Q. What is the difference between MIL-C-5541 & MIL-C-5541E? Is the implication of Class 1A and Class 3 the same? This process is chromating, but come across some time call it Alodine or Iridite, what is the difference?
William Wong- Singapore
2002
A. Hi William. The letter after MIL-C-5541 is simply the revision letter. Alodine is Henkel's trade name for their line of chromate conversion coating; Iridite is Enthone-MacDermid's
Ted Mooney, P.E.
Striving to live Aloha
finishing.com - Pine Beach, New Jersey
Q. Which process is better protection on parts? Is there a significant cost difference?
Thanks,
Plating of metal work - Chapel Hill, North Carolina
2006
A. Neither and no, Nick. They are brand names (actually trade names for a whole series of processes) from two different suppliers. It's like asking if Ford products are better than Chevy products. Some people prefer one brand over the other and claim it performs better, but after 50 years in this business my own conclusion is that whichever brand has the more helpful local serviceperson at the time is the brand that works better :-)
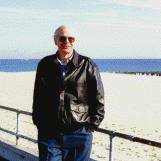
Ted Mooney, P.E.
Striving to live Aloha
finishing.com - Pine Beach, New Jersey
Multiple threads merged: please forgive chronology errors and repetition 🙂
Difference between Class I and Class III Iriditing
Q. I would like to know the difference between Class I and Class III Iriditing. Is Class III gold? Thanks for any help
Rita Flygarhobbyist - Rockville, Maryland, USA
2006
A. Class 3 is lighter in color BUT more importantly, less electrically resistant (i.e. MORE CONDUCTIVE). Heavier chromates (i.e. darker), Class 1A, are more resistant to both corrosion and electrical passage.
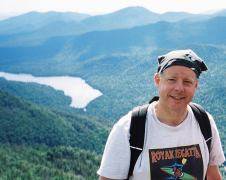
Milt Stevenson, Jr.
Syracuse, New York
Q. My experience is this process is not very good, the Iridite does not adhere to the base very well; it could be removed by rubber. Is there some method to improve this?
Seaman Fang- Shanghai, China
May 13, 2009
A. Hi, Seaman. Raw aluminum is not simply dipped into a tank full of Iridite; immersion is this tank follows after a cleaning, etching, and desmutting pretreatment sequence. Are you operating the process in full compliance with the technical data sheets from Macdermid? What alloy of aluminum are you treating, and what is the pretreatment sequence? But yes, an eraser can remove most of the coating -- it is not abrasion resistant.
Regards,
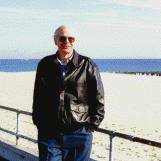
Ted Mooney, P.E.
Striving to live Aloha
finishing.com - Pine Beach, New Jersey
Q. Is there contact resistivity differences between Iridite type III yellow and Iridite type III clear in K band?
I assume the resistivity is extremely low for either type; is there some reference material with actual measurements of surface resistivity?

Paul Volk
- Palo Alto, California USA
February 21, 2014
Q. Need Suggestions:
I am new to the chemical processing side of things, and have a few questions if somebody can help answering:
- Talking about immersion time req'd for Class 1A and Class 3 ALODINE (using Alodine 1200s): is there a table/chart we can use that talks about immersion time against concentration of Alodine in the tank?
- Referring to MIL-DTL-5541F, if parts comply with ALODINE class 3, do they technically comply with Class 1A as well ? (considering both Classes need to comply with Corrosion Resistance but Class 3 also need to comply with Electrical Conductivity, so basically Class 3 is better than Class 1A?, and if I fine tune my immersion time for Class 3, no matter what is called on the PO I can use the same numbers for both classes 1A and 3?
- Pickering, Ontario, Canada
October 23, 2017
Q. I was really hoping someone would answer Nav D's question. Mine is similar. We have a part that requires MIL-DTL-5541 Class 1A and Class 3, Type 1 Clear in different locations on the part - the Class 3 is definitely for electrical conductivity where there are covers on our unit. Our normal outside process shop has to perform 2 masking steps in order meet this requirement.
We are bringing on a new outside process shop to increase throughput and they are saying that they can perform the chem film process in one step (by controlling the timing) and meet both Class 1A and Class 3 without having to mask.
That there is some "sweet-spot" where both can be met if you get the timing right. Has anyone heard of this before or had good results with this. Seems too good to be true and I could really use some feedback on if this actually will meet the requirements for both chem film classes.
electronics - Mesa, Arizona, USA
August 29, 2018
![]() |
A. Hi Angela (and Nav, if you're still listening), Aerospace - Yeovil, Somerset, UK A. Angela, - Lexington, Massachusetts |
Thank you so much Brian and Kurt for your quick responses. This has been an eye opening journey the more I am learning about the chem film process. And it is so nice to have other people who 'have been there' provide feedback. It is very appreciated!
Inter-Coastal Electronics, Inc. - Mesa, Arizona USA
Q. Hello,
Does anyone know of any "touch up" pens that are compatible with or contain Clear Chem Film per MIL-C-5541, CL3?
My company recently converted from "Gold" CL1 to CL3 and on several occasions need to perform such touch ups to reduce the amount of scrap we otherwise would have.
Thank you in advance!
ZMicro - San Diego, California
October 3, 2018
A. Just make your gold chromate up weaker, if powder, down to about 0.2 oz/gal, raise the pH , use a cotton swab.
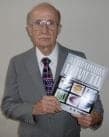
Robert H Probert
Robert H Probert Technical Services

Garner, North Carolina
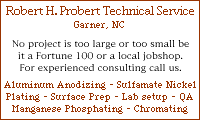
Q. Hi all
Would appreciate some help on the following:
As part of my manufacturing process I am required by my client to do the following finish:
1. Clear chromate conversion MIL-C-5541 Class 3
2. External wet painting (primer + paint)
The parts are Aluminium 6061-T6, used as covers in a regular environment (i.e. not a humid environment, no salt spray, no electrical conductivity, etc).
What would be the reason for the conversion / coating if the parts are painted anyway (for anti corrosion + finishing effects)?
Thanks!
- Israel
August 14, 2019
A. Hi Doron.
The chromate conversion coating does at least 3 things: improves corrosion resistance, improves adhesion, and provides protection in the event of a scratch, pinhole, or porosity in the paint. Aluminum which is painted without pretreatment is generally not a satisfactory finish.
Regards,
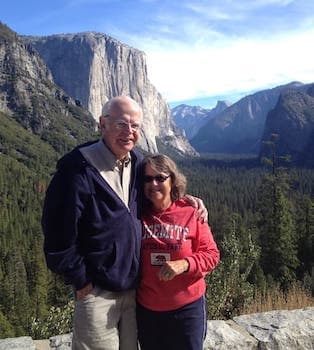
Ted Mooney, P.E. RET
Striving to live Aloha
finishing.com - Pine Beach, New Jersey
Thanks for your answer, it was definitely helpful.
- Israel
A. Ted's answer is technically correct but the simple answer is because it is what your client required you to do.
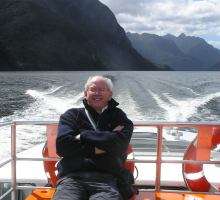
Geoff Smith
Hampshire, England
A. Ted is absolutely correct ! But you mentioned "primer". There is one internationally known corporation that specifies "acid wash primer" on top of the chromate. Be sure you did not mean acid wash primer, because it strips off the chromate.
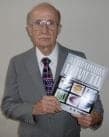
Robert H Probert
Robert H Probert Technical Services

Garner, North Carolina
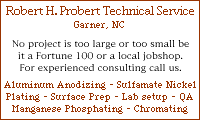
----
Ed. note: We have tried to consolidate onto this page a good number of threads about Class 1A vs. Class III chromate conversion coating, but it is such a perennial issue that, even still, this is only one of several threads on the subject :-)
Please see also thread 27034, "MIL-C-5541 Class 1A vs. Class 3" or search the site.
Q, A, or Comment on THIS thread -or- Start a NEW Thread