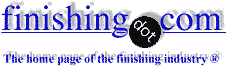
-----
Home shop phosphating, chrome conversion and plating
2003
Q. Well after 6 months of searching books, the web and asking everyone I could think of, I am more confused than ever. I realize what I need is a good book (Home Metal Finishing for Dummies) but everything I find either has no real "how to" information or is so deep I just don't understand.
A little history first. I am consultant by trade (electrical controls). I started off as a machinist then went back to school and graduated from a three-year college as a mechanical engineering technologist. Machining is still my first love. I have a small lathe and mill. This entire search started because I wanted to turn my finished parts black but not just with paint. I didn't want to send parts out to get finished. I want something I can do myself in my small shop. I don't have to meet any type of specifications. Most of the materials I use are plain carbon steel (4130 is about as exotic as I get).
So I first looked into "bluing" metal (I remembered many guns are a dark blue or black color). I soon found out that gun "bluing" was simply giving an oxide coating (using high temperature salt baths). It gave no real protection from corrosion. I did find a "cold blue" solution (buff, wipe on, wipe off and buff) at a local gun shop. It made small parts look good.
So I started reading about "Parkerizing". Seemed great. But now the confusion started. In the Finishing.com letter 722 it states "Iron (gray), Zinc (green) and Manganese (black)" Zinc is used for a paint base, Manganese for an oiled finish and Iron for either paint or oil. This letter even has a "home brew" formula Using Manganese Dioxide.
Question 1: Is this information correct? In some letters zinc is called gray, in others green. Can I paint over Manganese phosphate?
Question 2: Is there also a "home brew" formula for zinc and / or iron phosphating solution?
Question 3: Earlier in the same letter they talk about process steps alkaline cleaning, oxide removal, .. passivation and / or chromate sealing). What chemicals do I need to do these steps? How do I do these steps?
Question 4: This seems to be an ongoing discussion even on this board! Is these such a thing as a green colored phosphating. I have a friend who wants me to build him a "dummy" gun (welded closed barrel, welded in barrel-- just a fake to hang on the wall). He wants me to match the original finish. I saw one message suggesting the green color was from years of being packed in Cosmoline. I believe this is not the case since he left a new (reproduction) bayonet with me. The finish looks to be phosphating (it is a dull OD green color). How can I get this color (OD green)? Is it something in the passivation process (I've been reading about "olive drab chromate conversion" but this would need zinc plating first). I don't really know what the finish (chromate) would look like.
Question 5: If I want to paint over the parkerized finish do I just skip the oiling?
Section #2 Chromate conversion what does this finish look like? Could this be the green finish many talk about on gun parts?
This forum has a demonstration of zinc plating in the FAQ section. Will this work for larger parts--say 12 x 4 plates?
Does anyone have a "home brew" formula for a "olive drab chromate" conversion coating? Passivation?
Finally, on a recent tour of a gun manufacturing plant, I watched barrels being "hard chrome plated". If plating zinc is relatively easy, can I hard plate chrome to surfaces? Again, home brew formula?
It seems the more I read the more questions I come up with. Like I said at the beginning, I am just want to "tinker". Any information or suggestions on where to find all this information would be greatly appreciated.
Thanks!
Michael C [last name deleted for privacy by Editor]- Lexington, South Carolina, USA
A. Hello, Michael. Yes, there is a lot to learn. And as you've proven to yourself rather conclusively, while the internet is a good place to get a specific answer from an expert on a very narrow question, or general guidance about where to look for stuff, it's a poor place for structured learning because it possesses no structure itself :-)
On the internet, not only is the bad advice homogenized with the good but, as you complain of, the answers bounce from shallow & repetitive to opaque because it can't be based on what you've learned so far like books and school courses are. But I think you should narrow your efforts down to one specific finish because trying to learn iron phosphating, zinc phosphating, manganese phosphating, black oxiding, room temperature blueing, chromate conversion coating, passivation, chrome plating, and zinc plating might be the work of years.
You can read about chrome plating in our FAQ "Introduction to Chrome Plating", and black oxiding in our Black Oxide FAQ.
The demonstration of zinc plating in our FAQ section is, as it states a couple of times, only intended to help students learn about the science of Faraday's Law, etc.; it is not an adherent or useful plating. Trying to do practical plating from this would be like trying to drive off in the clay model of an automobile they built for a wind-tunnel test.
The single best introductory text for your purposes (and used copies are available very cheap) is probably the Metal Finishing Guidebook. Good luck, and get back to us with specific questions on one of these technologies. Good luck!
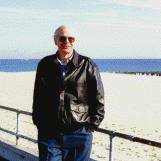
Ted Mooney, P.E.
Striving to live Aloha
finishing.com - Pine Beach, New Jersey
A. Hi Michael,
Phosphating is not easily accomplished in a garage or a bathtub. There are thousands of phosphating formulations used in industry today and they are not the result of tinkering by hobbyists.
I would not recommend that anyone mess about with these types of treatments if they do not have the requisite chemical training. All aspects of the metal pretreatment process utilize chemical baths that are corrosive. Phosphating is not something to be done at home by the unskilled.
George Gorecki- Naperville, Illinois
2003
A. Hi Michael,
I don't intend to answer your questions, but to let you know that there are numerous web sites on the subject, if you patiently search for them. Quite a few give formulae for making up and using phosphating chemicals. Try the web page
1919a4.com/cgi-bin/Forum1/HTML/000359.html for a discussion forum on "Parkerizing my 1919a4". Also look up "Culver's Shooting Page" for an article called "Kitchen Stove Parkerizing" by Dick Culver. Another good site is "Gunplumber's Guide to Home Gunsmithing: Parkerizing Overview (revised 02-18-03)", refer Arizona Response Systems.
As for safety, the main safety concern is the phosphoric acid. If you purchase it at higher strengths (e.g., typically 85%), wear eye protection goggles
⇦ on
eBay or
Amazon [affil links] and rubber gloves
⇦ on
eBay or
Amazon [affil links] , and rinse any spills with copious amounts of water. When diluting, remember to always add the acid to the water, never the other way around. You can of course buy the acid in much more dilute forms than 85%, and I would recommend this. The phosphoric acid used in the actual phosphating process is very dilute. When heating the solution, avoid burning yourself, and use in a well ventilated area.
Give it a go, Michael! I've had a lot of fun experimenting, with some very good results on my firearms. Don't be put off by unnecessarily dire warning from people who may have a vested interest in the industry, and don't like to see we private individuals having a go ourselves. As far as surface coatings on metals goes, phosphating is about as safe a process as it gets. Many cooking procedures in the kitchen are at least as hazardous!
- Auckland, New Zealand
2006
Ed. note, Feb. '08: Another problem with the internet is its impermanence. We've struck through Richard's link as it unfortunately no longer works.
Grey green phosphate finish question
April 4, 2015Q. There have many inquiries on this site about the replication of olive drab to slate green phosphate finishes for WW2 firearms. The common misconception is that it is a grey zinc phosphate finish that has turned green after being stored with cosmoline. I have several different German model 98k rifles, one Coded BCD45 (Gustloff) and another SVWMB (Mauser). Both of these firms are noted for their impossible to duplicate slate grey green phosphate finishes. Many examples exist of mint guns with no cosmoline residue that exhibit this finish. It almost appears that the oxidation is what turns green. I have heard it suggested that a colored oil was used.
I have included photos of one such rifle. The Germans switched to this process in the last months of the war so the materials involved would have been inexpensive and available. This is an untapped goldmine for an enterprising chemist. I'm sure many people would consider this finish as an upgrade on their modern day firearms. Hopefully someone can answer this riddle.
Richard WalterHobbyist - Margate, Florida USA
Q, A, or Comment on THIS thread -or- Start a NEW Thread