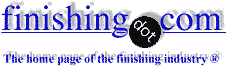
-----
Parkerizing formula, process and Q&A's
Current Q&A:
⇦ Tip: Readers want to learn from your situation;
so some readers skip abstract questions.
Q. I want test method for checking a Star washer on which parkerizing is done.
Dighe SwapnilEmployee - Pune, India
December 17, 2021
A. Hi cousin Dighe. The problem with such questions is that people must reply "what do you want to test about the parkerizing, and what values from those tests should indicate passing vs. failing?" :-)
But the resolution to the problem is actually simple: you need to parkerize/phosphatize in accordance with some particular specification. Then the specification will tell you what you need to test, and how, and what constitutes compliance. So look through some star washer and/or phosphatizing specifications and pick one. You could look at MIL-DTL-16232 [from DLA] as a starting point because access is free.
Luck & Regards,
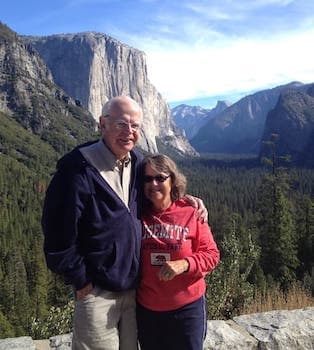
Ted Mooney, P.E. RET
Striving to live Aloha
finishing.com - Pine Beach, New Jersey
December 2021
Mn phosphating formula for couplings for pipes and treads
⇦ Tip: Readers want to learn from your situation;
so some readers skip abstract questions.
Q. I need new composition with formulas - for Zn phosphating of Thread on couplings and ends of pipes with thread for oil drilling.
Could you help me with composition and activator.
- thickness of coating 6-15 mkm.
- mass of coating - 10-25 grm2.
I need activator too.
- New jersey
May 20, 2022
A. Hi Vadim. We added your question to a thread which already has a lot of information about formulation of Mn Phosphatizing processes. Thread 31345 also addresses this topic. Thread 14221 offers good info on activation chemistry.
You are certainly welcome to precede down this path if you wish. But just in case you didn't know, virtually no one formulates their own phosphatizing and activation solutions these days; rather, they buy proprietary processes from suppliers to the industry.
But what is your current formulation and what problems is it causing that you feel an improve formulation will resolve?
Luck & Regards,
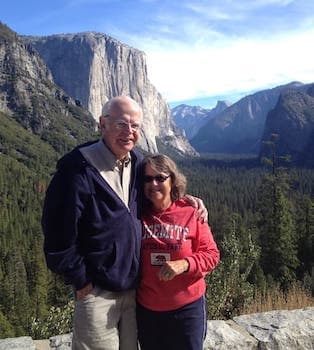
Ted Mooney, P.E. RET
Striving to live Aloha
finishing.com - Pine Beach, New Jersey
May 2022
⇩ Related postings, oldest first ⇩
Q. I need a detailed description on a Parkerizing or phosphatizing process as it is used as a finish for handguns (companies like colt or Springfield offer a Parkerized finish on some of their pistols). the finish should be slightly rough and the color should be a medium gray. the description should include the pretreatment (sandblast, acid treatment, degreasing, ?), the process itself (chemicals, solvent, concentration, temperature, time, ...) and the treatment afterwards (sealing, chromatizing, maybe coloring,?).
Thank you, all.
Lois KleeweinGraz. Univ. of Tech'y - Graz, Austria
1998
1998
A. "Parkerizing" is the trade name for a phosphating process by Parker. They are now Parker+Amchem whose parent company is Germany based Henkel.
I'm not sure that it is a phosphating process. It could be a Gun "bluing" process.This is a controlled oxide formation process. There are various companies offering these products. They should be able to provide you with the information you are looking for, and would process some samples for you as well.
Good luck
Dan ZinmanQ. I was trying to find information re "chromatizing" or "chromitizing" that was common in the 1940's and 50's and your letter showed up in my Internet search re "chromatizing". If you know anything at all about this post metal finishing process I'd be interested in any details.
In the meantime, I used to do industrial hard chrome plating and installed a black chrome tank to blacken optical components. Before I knew it, the Los Angeles Police Dept. were all bringing their guns (broken down) for me to blacken. The process worked great and nobody ever complained. Most processes I had seen were more of a browning process than a blackening. The black chrome I used came from Dupont, but I think that they have gone out of the that business.
Malcolm Fieldplating shop - Palos Verdes Estates, California
1998
1998
A. For my opinion your process is heavy coating Zinc Phosphating and then you have to oil the gun.
The Process Sequence is :
- Alkaline Cleaning
- Rinse
- Oxide removal with Inhibited HCL
- Rinse
- Grain Refining
- Heavy Zinc Phosphate
- Rinse
- Chromate Sealing
- Rinse
- Oiling
For my opinion you have to release hydrogen by entering the gun into oven at 200° C for 3 hr before oiling.
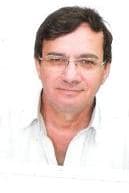
Yehuda Blau
YB Plating Engineering and Quality - Haifa Israel
A. Parkerizing or Phosphating is a very well known process in the firearm industry. Parkerizing has been used by the U.S. military since the early 1900's. The Patents for Parkerizing are or were (my references are rather outdated) held by the Parker Rust Proof Company, Detroit, Michigan.
The basic formula consists of;
Phosphoric Acid
iron filings [affil links]or Manganese Dioxide
Distilled Water
Parts may be sand or bead blasted before finishing but good results may also be produced on highly polished parts. The Parkerizing process should only be used on on exterior surfaces to protect close tolerance parts. Parts are neutralized immediately after removal from Parkerizing solution by boiling in plain water.
Brian Northgunsmithing
1998
! Hello all! Just a note to anyone interested in the history of The Parker Process. Clark W. Parker was my great-great grandfather, the one who invented the Parker Process. I was surfing through the net and found this site. Sincerely,
Sharon A. Walker-Ciafone- great-great-granddaughter of Clark W. Parker
1999
Hi Sharon. Happy to meet you. We wish you as much success in your endeavors as your great-great-grandfather :-)
Regards,
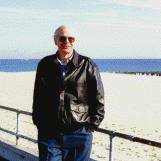
Ted Mooney, P.E.
Striving to live Aloha
finishing.com - Pine Beach, New Jersey
1999
Q. Respected Sir,
We are having a industry in India which is doing Mechanical work shop activity from past five years. Now we are interested to start cold zinc phosphating process for hydraulic cylinder tubes. We understand that we have to follow the following process..
- 1.Cleaning with Kerosene
- 2.Cleaning with Sawdust
- 3.Cleaning with water
- 4.Degreasing
- 5.Cleaning with water
- 6.Pickling with HCL
- 7.Neutralizing
- 8.Cleaning with water
- 9.Zinc Phosphating
- 10.Cleaning with water
- 11.Passivation
- 12.Oiling and sealing
We need to know the chemicals and its compositions used in degreasing, pickling, neutralizing, zinc phosphating, passivation. Kindly send us the details for cold zinc phosphating process.
Yours faithfully, Sudheer
P. Sudheer Babu- Hyderabad, Andhra Pradesh, India
Q. I would like to know the advantages and disadvantages to use the phosphate without Nickel in the followings metal:
Cold rolled and galvanized.
When it is not used a Nickel as chemical component of phosphate which component is used in stay of Nickel?
Please tell us which are the tree component used in thee chemical composition of the phosphate.
Thanks, Best Regards
Franklin Esteban- Venezuela
1999
Q. I am a self-employed engineer making detergents, black phenyle & white pine oil emulsion. I am trying to diversify into some industrial product and since I live in an industrial town, phosphatizing seems to be the first option. Will some helpful soul who has made his money help me make mine and bless you eternally? Please tell me how to make a zinc phosphating solution and the afterwards used chemical solutions.
GOD HELPS THOSE WHO HELP OTHERS. THANK YOU,
REGARDS
Raminder Singh Kohli- India
1999
----
Ed. note: Hi, Raminder. That means God will help you if you help with thread 18029, where lots of people are seeking help with black phenyle and white pine oil emulsions, which are your areas of expertise. Thanks.
A. Look at Metal Finishing, (1979, May) Vol 77, No. 5, page 99. Phosphating of Steel Using trisodium phosphate ⇦ on eBay or Amazon [affil links] , or see Rajagopalan et al., Central Electrochemical Research Institute, Karaikudi, India. Good Luck!
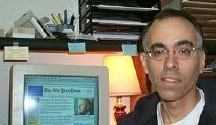

Tom Pullizzi
Falls Township, Pennsylvania
1999
Q. I have a (personal interest only) in the formula for Parkerizing or phosphatizing steel !. Does anyone know temperatures, time, and mixing ratios ? Everyone seems to know the basic formula . But do you have exact formulas ? Please respond and post. Thank You , Ken ...
Dr. Kenneth Boydmarine engineering - Valley Center, California
1999
A. As previously mentioned, Parkerize is a Trade name which may consist of either Iron (Gray) Zinc (Green) or Manganese (Black) phosphate finishes. They have evolved through the year. There are other companies which make similar type products and some better than the Parker Brands.
To be applied properly, they need to be sent to a professional who has the equipment to maintain the temperatures, and the bath consistencies. To achieve maximum corrosion protection, other processes need to be applied to the phosphate finishes and the metals baked. Forget about Parkerize, it is an old obsolete method of corrosion protection, no mater what method is used.
A lot of gun smiths Parkerize guns but are not using the industrial methods of application and will not hold up. After the phosphate coatings, you need to apply another dry film lubricant and corrosion barrier coating. The results is a flat black durable finish which is more corrosion resistant than Stainless Steel. Phosphate finishing is only the first step of a good gun finish.
Ollie Dawgunsmith - Gulf Shores, Alabama
1999
Q. dear readers
I require the information about the metal pretreatment systems; I am starting a new job. Is there anybody who can give me information about the ratios /concentrations of various chemicals used in alkaline cleaners, pickling solutions and zinc phosphating. I also need information about time and temperature that is required for the process. I will be much thankful to you. God bless you.
syed iqbal saleemchemist - Pakistan
2000
! Brian North's response has most of the essential chemicals listed for the phosphatizing (sometimes called "Parkerizing") process that's commonly applied to steel tools and firearms. Yehuda Blau's message of Aug. --- lists the correct processing steps for certain phosphatizing processes.
I have several phosphatizing and black oxide finishing formulae that I've used in the past with good results. All my information was culled from various gunsmithing and arsenal documents I've acquired over the last 30 years; most of the information is at least 50 years old but the basic principles have remained unchanged to this day.
Parkerizing itself is indeed an obsolete process but general-use phosphate coatings on steel are alive and well. The oil-retention characteristics, abrasion and corrosion resistance of a properly applied phosphate finish is most impressive. Unoiled, phosphated steel makes a great substrate for the application paint and lacquer.
The results you'll get are strongly dependent upon the purity of the chemicals that you use, your processing tank materials and the consistency of your processing steps. It should also be noted that the color and durability of phosphate finishes are strongly tied to the alloying elements and the heat treatment conditions of the steels you'll be processing. Many of the higher-alloy steels (such as chromoly 41xx steels) emerge from the process with a greenish-to-blackish finish. The original Parkerizing process applied to US military small arms usually resulted in something close to an olive drab color after it was oiled. That may have been partially due to the composition of the steels used in older firearms; until mid-WWII, gun alloys were rarely more exotic than plain carbon or low-order nickel steels.
Anyway, I'll be happy to share (for free, no less!) what information I have with anyone who's interested.
Geoff Schecht- Austin, Texas
2000
I would like to contact Geoff Schecht with regard to his offer. We shoot and restore old Military Firearms. Any help you can give me with formulas and processes would be greatly appreciated. Regards
Mike Mc Mahon- Deakin ACT, Australia
2000
I recently purchased an old military surplus handgun that needs to be refinished. I wish to Parkerize the gun and have gathered a lot of useful info on this site. However, If Mr. Geoff Schecht would contact me to share his info it would be VERY helpful for a beginner to Parkerizing.
Jeffrey Polek- Big Rapids, Michigan
2000
----
Ed. note: Hi Geoff; Mike; Jeffrey.
We appreciate people's willingness to share! ... but it just doesn't work when people take a public forum private. Party B wants to contact A, then C wants to contact A, then B wants to contact C for whatever he has learned from trying to apply it -- and readers D & E are cut adrift, kicked out of the loop they were following, and the site's advertisers are left asking why sponsor a site that arranges private hook-ups they're cut out of :-)
We have all the room in the world to post any questions anyone wants to ask, and to make available any information anyone is willing to share. There are good reasons to keep it public!
Q. Is Parkerizing a small area on a gun practical?
I have a Parkerized Remington '03 in unissued condition except for a 1" rust patch on the barrel where something corrosive evidently got on the gun. I haven't done anything with the repair yet, but suspect the metal is pitted.
Would it hurt to clean it up with naval jelly ⇦ on eBay or Amazon [affil links] to get a better look at it?
Larry Caldwell- Myrtle Creek, Oregon
2000
A I build guns for a living . I also Parkerize on a daily basis. I use a mixture of 1 gallon technical grade Phosphoric acid to 8 ounces manganese dioxide . The Phosphoric acid is mixed with 9 gallons water in a stainless trough and brought to a rolling boil.
The Manganese Dioxide is then slowly mixed in the solution and boiled for 10 minutes. When the parts are ready to Parkerize after blasting with coarse ground glass I reheat the solution to 190 °F and immerse the part in the solution until foaming stops.
Then I remove the part from the solution, rinse with cold water, oil with a mixture of 1 gallon WD-40 ⇦ on eBay or Amazon [affil links] and 1 quart chainsaw oil, dry and re-oil. I have built over 300 guns this year alone using this method. The finished guns are near black and retain oil very well.
Mike Prewitt- Kent Washington
2000
A. After reading all the comments above, I took to the kitchen.
My wife has not left me yet over the experiment but I don't think I will get away with a big project. I attempted to coat a steal punch. I did not do too good a job of cleaning the punch so the finish is a bit splotchy.
I used 2 cups of tap water, one cup of white vinegar ⇦in bulk on eBay or Amazon [affil links] , and one heaping table spoon of epsom salt. The water and vinegar was brought to a boil. Then I added the epsom salt. After boiling this for a about 10 minutes, I added my somewhat clean tool steel punch. After simmering this stew for 20 minutes, I removed the punch and rinsed in lots of hot water. Dried the punch and applied lots of oil.
The darn thing looks fairly good. I think with a Parkerizing kit anyone should be able to follow the direction and do a good job. Good luck to all of us who dream of Parkerizing that old piece of junk .22 or .410.
Gary D Antley- Groveton, Texas
2001
Q. I used to do the Parking for a local gunshop. I did more projects than one can imagine. I however do not know the chems used in the process.
I performed 2 basic styles of parking. One was to do a standard military style, which had a nice med to dark grey finish. The other method was to replicate the natural aging and that greenish color, created by years of Cosmoline.
I used 2 tanks, the primary tank had the flame. I kept an operating temp of 200 deg F. the secondary tank got its heat by sitting next to the primary tank. Temp about 160 or so. I would use a fine glass media to blast the entire surface clean. Next would drop it in the primary tank. Normal time was 45 seconds to 1 and a half minutes. Sometimes longer depending on the metal condition. I would then remove it from the solution then drop it into the secondary tank. This would give the greenish tint. I then would apply a specialty lube, could use CLP, and allow to air dry. Done that is all. Done parking in about 15 minutes from time start blasting to putting on cooling rack. Primary Tank, the chemical was a pale light green color, and was mixed 9 cups to the rest plain tap water. The greening agent, was a deep orange color, and only needed a quick dip, or a long soak depending on the amount of greenness.
If anyone knows what those 2 chems were please let me know.
Merlin [last name deleted for privacy by Editor]- South Carolina, USA
2001
2001
A. Found this after my own search for Parkerizing finishes.
Kitchen Stove Parkerizing By Dick Culver
NOTE: I originally gave this formula to an interested individual when we were posting on the Ohio site, but it was lost in the transfer. I publish it again here with the disclaimer that I don't wanna be responsible for anyone ruining a $1000 part or becoming a vegetable from inhaling the fumes from some noxious brew. I've done it on numerous occasions with no ill effect (some will differ in their opinion of my mental state of course) but if you choose to play around with chemical formulas, you are strictly on your own!
INSTRUCTIONS FOR "HOME-BREW" PARKERIZING:
You need a number of things to do a "home-brew" "Parker-job", but only 4 ingredients.
1. Phosphoric Acid (the active ingredient in naval jelly ⇦ on eBay or Amazon [affil links] ) usually procured at a chemical supply house.
2. Powdered Manganese Dioxide (a very dense and heavy dark gray to black powder) also available at any chemical supply house.
3. Distilled water (I've used tap water, but the distilled stuff gives more consistent results).
4. A biscuit of 00 steel wool ⇦ on eBay or Amazon [affil links] (don't use soap pads or Brillo pads!)
I used to do this on the kitchen stove (I wasn't married in those days) in a one gallon Pyrex beaker (these little beasts are expensive, so be careful with them). Metal pots don't work as well (if at all) I understand, but then I never used anything else but Pyrex.
Proceed as follows:
1. Use one whiskey jigger (yeah, this is really scientific, right?) of phosphoric acid added to the water. Remember your high school chemistry, ALWAYS add the acid to the water, and it is best done by pouring it down a glass rod!
2. Use one whiskey jigger of the (powdered) Manganese Dioxide in the solution.
3. Bring the solution to an extremely slooowwww rolling boil.
4. Now add your biscuit of steel wool.
I used wooden sticks placed across the top of the beaker and suspended the parts in the solution using steel or iron "machinists wire or some such. DON'T use painted coat hangers or any wire with grease on it! You can usually get this stuff from a machine shop or from Brownells [ Brownells home page (affil link) ] .
The parts should be totally immersed in the solution, being careful that anywhere the wire touches the part won't show on the finished part (usually easy to do ñ like in the firing pin hole of a bolt). The part(s) to be Parkerized should be totally "de-greased" and sand or bead blasted prior to finishing (depending on the texture you desire on the finished part). Once you have bead blasted the part, you should handle the part with gloves (never greasy hands) and store them wrapped in clean paper towels awaiting the Parker Bath. Any grease on the parts or wire will cause what can only be politely called a variation in color (the parts come out streaked and spotted like a "paint horse").
I usually let the part remain in the solution for a total of 20 minutes (less MAY work, but I was told 20 minutes so that's what I used and it worked marvelously). When you withdraw the part, immediately rinse it in hot running water to get the solution off of it. Use extremely hot water, and the part will dry itself. Let it dry (and get cool enough to touch) on some clean paper towels, spray on some lubricant and voila you are done!
Rumor control said that if you immersed the freshly rinsed and still hot part in Cosmoline.
it would give the sometimes sought after "gray-green" tint to it. I have never tried it. Cosmoline is still available from Brownells [
Brownells home page (affil link) ]
if you are adventurous!
The original formula called for iron filings vs. steel wool, but since I didn't have any floating around, and didn't want to file on the cast iron stove, I found that the steel wool worked just fine. What you get is a chemical reaction that causes an iron phosphate to form on the metal (steel phosphate I suppose, using steel wool). I have found that the resultant finish is just as durable as the Arsenal finishes and has exactly the same appearance! ñ an attractive dark gray, almost black. Some say that adding more manganese dioxide causes a darker finish, but I've never tried it, as I was happy with what I got!
We often used this technique when finishing .45s built on early Essex frames that needed a lot of fitting, thus often requiring the removal of offending metal. I used to checker the front straps (also violating the finish in a rather spectacular fashion) and the resultant finish worked great and showed little or no wear even with extensive use ñ much like the official GI finish. I'm still using a wadcutter gun I performed the magic on back in the '70s and it still looks new.
A couple of cautions:
1. Always be careful of any sort of acid, even such an innocuous acid as phosphoric. I certainly would never deliberately inhale the fumes (although there is no great odor to the process that I could tell, but then I smoke cigars). I started doing this back in the early to mid '70s and still have no "twitch" that I can directly attribute to Parkerizing on the kitchen stove. Just use common sense, WEAR GLOVES AND EYE PROTECTION ANYTIME YOU ARE PLAYING AROUND WITH BOILING SOLUTIONS (with or without acids being involved).
2. Be very careful not to cause any splashes with the boiling solution (of course the same can be said of boiling corn).
3. Prepare your area and your parts before hand, don't try to do this on the spur of the moment.
4. Send your wife to see "Gone With the Wind" or "Titanic" or some other movie that whiles away a number of hours. If you ever want to do this again, make sure the kitchen is spiffy when she returns! In Gloria's case, she would be attaching the parts, but then I'm just lucky in that respect...
5. Once you have allowed the solution to cool, you are DONE! Reheating it don't cut it, It simply doesn't work (I've tried it on several occasions). Have everything that you want to Parkerize ready to go when you fire up the solution. You can keep Parkerizing as long as the solution is hot, but allowing it to get cold kills it ñ you've gotta brew up a new solution and start from scratch.
6. Do not name me in any divorce proceedings!
Good luck!
Bill Reid- Kuna, Idaho
Q. Hi. I need to Parkerize the internal wall of a 1000-L gas cylinder (about 10 square meter surface area inside)... could somebody shed me some light on how I can compute roughly how much Parkerizing solution (11% v/v) is needed to have a decent coating? Thank you!
Anne Vargas- Singapore
January 13, 2013
We do firearm parkerizing in our shop. The formula we have found that works well:
1 cup phosphoric acid per gallon of water.
You will need several stainless steel tanks, one big enough to fit the firearm in until submerged. Another for a strong soap and water rinse.
Heat water and phosphoric acid until a gentle boil. Submerge the firearm, parts, etc., and leave until no more bubbling (releasing hydrogen, I believe). When bubbling stops, rinse parts, etc., in a very strong, mostly soap and water solution and submerge. Then rinse with clean water and blow dry. The harder the metal, the lighter grey the finish will be.
Hope that helps!
Gunsmith - Spring, Texas
July 14, 2021
Q, A, or Comment on THIS thread -or- Start a NEW Thread