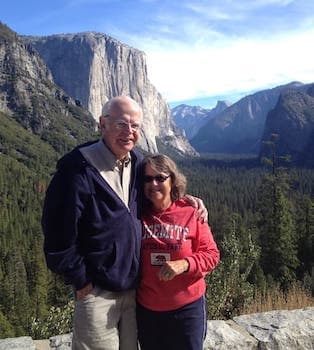
Curated with aloha by
Ted Mooney, P.E. RET
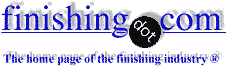
The authoritative public forum
for Metal Finishing 1989-2025
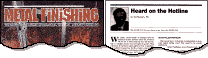
-----
Frosted, etched, or burnt passivated parts - Type 303 stainless steel

this text gets replaced with bannerText
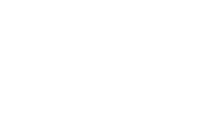
Q. What would cause 303 stainless steel to "burn" to this extent during the passivate process? The spec call-out was Passivate per AMS2700, Method 1, Type 2.
Q. The parts were a bright and shiny machined finish when sent for processing.
Roger Fluet- Hillside, New Jersey
April 10, 2024
A. Hi Roger,
Unfortunately, passivation of 303 stainless is often troublesome because of its sulfur content; we have many other threads on the issue, including most notably thread 17774 and thread 20840.
Perhaps the most common shortcomings leading to this problem are use of the wrong solution (you need to use solutions with dichromate content), inadequate cleaning (which can contaminate the passivating solution, and create organic acids), and excessive chlorides.
The easiest correction is probably to switch to citric acid passivation; but if that is not possible, make sure you are actually using a proper nitric-dichromate solution (see Lee Gearhart's posting), then analyze against very high chloride concentration, and try extreme cleaning such as at least an hour in a hot alkaline soak clean bath (and electrocleaning if possible).
Luck & Regards,
Ted Mooney, P.E. RET
Striving to live Aloha
finishing.com - Pine Beach, New Jersey
A. Roger,
To be honest those do look more like a 400 series that wasn't heat treated before passivation. If it is 303, the sulfur distribution in the alloy must be fairly bad, on the order of inclusions.
Type 2 is the allegedly correct nitric recipe to use, although citric acid would be easier going. With the citric you would definitely want to pretreat in alkaline to remove sulfur from the surface, doing so with the nitric bath wouldn't be a bad idea either.
Any rotten egg odor around your passivation bath shows you have a sulfur problem, although with a nitric bath's terrible fumes I'm not sure how you would notice.
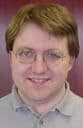
Ray Kremer
Stellar Solutions, Inc.

McHenry, Illinois
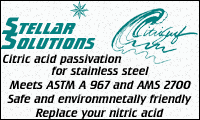
⇩ Related postings, oldest first ⇩
Q. What would cause a frosted appearance after passivating 303 stainless steel? Could it be from pre cleaning or the passivate process?
Mario Rodriguez- Phoenix, Arizona
2002
A. Frosted appearance comes from etching away microscopic stuff, leaving a rougher surface which reflects light at many angles. Since you're working with 303, which has lots of sulfides to aid machinability, I'd suppose that the sulfides on the surface are being etched away by the either the pre-cleaning or the passivation. Either one could do it.
If you can stand the frosted look, put up with it because removal of those sulfides is really important for corrosion resistance.
Mike Mcguire- Pittsburgh, Pennsylvania, USA
? You do not give enough information for me to give you a definitive answer but based on the information you have provided it seems you are getting etching of the part. This could be caused by passivating with oil left on the surface after inadequate cleaning. If you send more information about the process you are using I can possibly make more suggestions.
Good luck.
John Holroyd- Elkhorn, Wisconsin
Q. The process I'm using is AMSQQP35 [canceled] type II. According to that spec, the frosted condition is cause for rejection. Parts had some oiled before process, I cleaned them as usual and passivated type II. Can a weak solution cause that condition?
Mario Rodriguez [returning]- Phoenix, Arizona
A. Sorry about the delay in responding but I have been traveling.
It seems probable that your problem is caused by residual oil left on the part after cleaning. The cleaning process has to be extremely thorough if you are to properly passivate the parts. Etching is often caused by traces of oil reacting with the acid and forming an organic acid which will etch the parts very effectively. In fact this is a technique used by metallurgists to etch difficult metals.
First check to make sure that you have not got your passivation bath contaminated with oil and that it is at the proper strength for the procedure. If it is contaminated then change it.
Next I would suggest that you remove all the oil from the surface of your parts by wiping with paper towels, then wipe the parts with lacquer thinner ⇦ this on eBay or Amazon [affil links] Warning! flammable! and paper towels using frequent changes of paper towels to be sure that you are not recontaminating the surface.
After the lacquer thinning the part should be soaked in a heated and agitated bath of caustic soda ⇦liquid caustic soda in bulk on Amazon [affil link] for at least half an hour. Finally rinse the part without touching the surface in any way and transfer the part to the passivating solution. If the part still etches I will be very surprised but I do not expect you will have any further problems. Please let me know how you go on with this.
Good Luck,
John Holroyd- Elkhorn, Wisconsin
A. Mario:
Yes, a weak solution can cause a definite problem. The nitric acid used in AMSQQP35 [canceled] is a reducing acid in dilute solutions. I agree with the others that it is critical to clean the surface of residual sulfur and oils to get a good passive layer on 303. This can be done well with a 5% NaOH solution or a high pH alkaline cleaner. citric acid proprietary formulations may be better for you if it is allowed by your customer. It is not allowed by AMSQQP35 [canceled], although many aerospace companies have tested and approved it. It is allowed by AMS2700. This can give you an improvement in performance without the danger of frosting the surface.
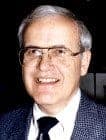

Lee Kremer
Stellar Solutions, Inc.

McHenry, Illinois
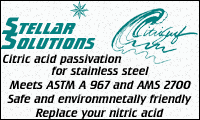
Multiple threads merged: please forgive chronology errors and repetition 🙂
Rework of etched 303 stainless
Q. We have an in-house passivation shop. We passivate 303 material that sometimes etches. In one batch of about 10 parts, we could get 3-8 etch and the others do not. What could cause this situation? Once this situation occurs, what options do we have for salvaging the parts? The etching isn't deep into the base, it mostly just puts a frost on the part. Sometimes we scrap the parts, sometimes we blast them and re-passivate, what is the best practice?
Debra BurmChemical Process shop - Phelps, New York
2005
Ed. note: Please start with our FAQ on this subject, Debra. Some people assert that the formation of aggressive organic acids from tiny amounts of oil is the cause of this common sporadic problem, and that ludicrously long cleaning times before passivation will solve it.
A. Random etching of 303 is a common problem. Most likely what you're working with is 303Se. Can the mfgr. change to another alloy? - 304, for example will give no problems.
We are at the point of not bidding on passivation of 303. It's just too risky, and impossible (for us anyway) to predict which parts will etch and which will not.
I've seen reports which claim that the problem can be solved by extended soak cleaning on hot alkaline cleaner (several hours) before passivation. Maybe worth a try.
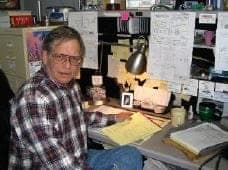
Jeffrey Holmes, CEF
Spartanburg, South Carolina
A. 303, 303S and 303Se are all major problems in passivation with nitric acid formulations unless you know how to handle them. Organics on the surface are always a problem with nitric acid, but the high sulfur in these grades is what causes the problems. Pretreating with HOT NaOH solutions or cleaners with a pH greater than 12 (with possible sequestering agents) will eliminate the problem.
You can also eliminate the problem by using good citric acid products that are on the market, with the precleaning in high pH solutions.
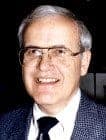

Lee Kremer
Stellar Solutions, Inc.

McHenry, Illinois
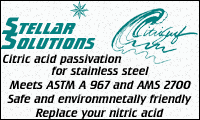
A. Don't use type II. Use type VIII. We switched and our etching problems went away.
The table in the back of QQ-P-35C (canceled) [link is to free spec at Defense Logistics Agency, dla.mil] was a SUGGESTION ONLY, folks.

Lee Gearhart
metallurgist - E. Aurora, New York
Multiple threads merged: please forgive chronology errors and repetition 🙂
Q. ISSUES PASSIVATING 303 SST. PROBLEMS WITH ETCHING OF PARTS USING THE AMSQQP35 [canceled] procedure.
GREG BEGUHLSUPERVISOR - MINNEAPOLIS Minnesota USA
February 4, 2011
Post cleaning passivated 303 stainless steel
Q. I have some 303 stainless steel parts that will be heated to 365 °C after passivation. The parts will discolor from the heat. Is there any way to clean the discoloration after the heating process? Does this temperature affect the passivation?
Mark Stevens- Worcester, Massachusetts November 7, 2012
A. Mark,
Is there are reason behind this heating?
The common methods to remove a discoloration like that are pickling, electropolishing, or mechanical removal such as sandblasting or tumbling.
I don't have a full set of phase diagrams handy but based on what a quick google search pulled up, I doubt a heat of 365 °C will do much to migrate any significant amount of iron to the surface. However, if you do any of the above to remove the discoloration, you may want to passivate again.
I would just move the passivation stage to the end of the manufacturing processes, which is where it belongs anyway.
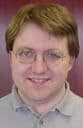
Ray Kremer
Stellar Solutions, Inc.

McHenry, Illinois
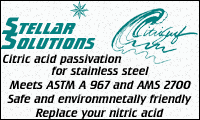
A. Ray: The heating comes from the curing of high temperature epoxy. This curing is the next to the final step in the assembly of the product so the passivated parts are already on the assembly and in close proximity of the parts being heated. Close enough that the parts discolor. Additionally we have to be careful of the cleaning of the discolored parts as this is a medical device and the mating parts around the passivated parts are silicone.
Mark Stevensre- Worcester, Massachusetts, USA
A. Mark,
It is possible to do mild passivation methods, color removing. Or if it does not work, slight electropolishing in acid-free electrolyte may work, since such electrolyte does not impact silicon. We have already done some cleaning of the SS-ceramics assembly after heat treatment.
adv.
Contact me for testing arrangement.
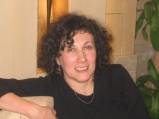
Anna Berkovich
Russamer Lab

Pittsburgh, Pennsylvania
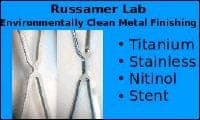
January 10, 2013
Q. Hi, we are having issues with frosting on 321 stainless after passivating to ASTM A380 . Could this be similar to the problems with passivation of 303 stainless?
Grant HartmanNortech Systems - Blue Earth, Minnesota
September 18, 2019
A. Grant,
321 isn't a high sulfur grade like 303. The notable alloy addition for 321 is titanium, which I wouldn't expect to cause issues. If your parts are getting etched, you may be using incorrect nitric acid bath parameters. I would suggest testing out a citric acid passivation method to see if that solves your problem.
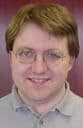
Ray Kremer
Stellar Solutions, Inc.

McHenry, Illinois
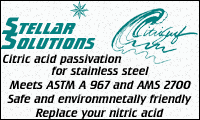
Thanks, I will see if our customer is open to citric acid passivation. The main reason why I was asking is the inconsistency in the finish. Using the same lot of stainless and within the parts passivated at the same time we are seeing 50% with no issues and 50% with differing levels of discoloration to frosted.
- Blue Earth, Minnesota
Q, A, or Comment on THIS thread -or- Start a NEW Thread