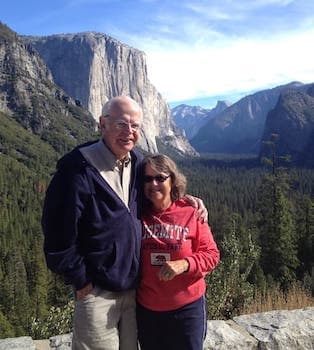
Curated with aloha by
Ted Mooney, P.E. RET
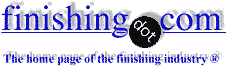
The authoritative public forum
for Metal Finishing 1989-2025
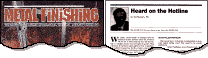
-----
How to Chromate ADC12, 380, Castings, and Secondary Alloys

Quickstart (no readers left behind):
Aluminum is often 'chromate conversion coated' as a corrosion resistant final finish or as a pretreatment for painting or powder coating. The process actually involves many steps, usually including alkaline cleaning, etching, deox/desmut, the chromate conversion step per se, and water rinses between each step.
MIL-C-5541 / MIL-DTL-5541 / MIL PRF-5541 is the most commonly cited spec. "Alodine" and "Iridite" are proprietary trade names from two suppliers of the process chemistry. "Chem film" is a slang term for the process often used in the USA.
Q. We had powder coated ADC12 High pressure die cast aluminium. We have done Alodine pre-coat; and after that pure polyester coating of 60 microns. But it is failing to sustain 336 hrs of salt spray test. Can anyone suggest alternate method for corrosion resistance to ADC-12?
Pravin Bhimanavaru- Pune, India
January 30, 2023
A. Hi Pravin. I think that if aluminum is properly chromate conversion coated and properly painted/powder coated, it should last that 336 hours.
I suggest that you investigate whether the chromate conversion coating process is being done really right. You may need to replace the contents of the tank, or adjust your de-smutting process as discussed in this thread. What do the parts look like after they have been chromate conversion coated but haven't yet been painted?
Salt spray testing is for helping you keep your process on track. Using it to guide you towards a replacement process would likely be a mistake; but if you want alternate process recommendations, please tell us about the component and its requirements. Thanks.
Luck & Regards,
Ted Mooney, P.E. RET
Striving to live Aloha
finishing.com - Pine Beach, New Jersey
Q. ADC 12 alloy processed with silicate, phosphate, caustic free degreasing then etching by HF/ HNO3 then trivalent chrome conversion coating.After each treatment two water rinses available.Dried parts powder coated. Finally while machining operation chip off issue noticed.Possible root causes and how to arrest the issue?
RAJA.RAMUElectro Chemist. - Chennai
December 7, 2024
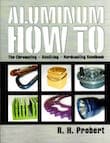
Aluminum How-To
"Chromating - Anodizing - Hardcoating"
by Robert Probert
Also available in Spanish
You'll love this book. Finishing.com has sold almost a thousand copies without a single return request :-)
A. Hi Raja,
It would be helpful to know whether you've successfully processed ADC12 in the past with this same process, and this is a new problem that suddenly arose, or whether you've never done ADC 12 before.
It's possible, of course, that the parts are abused at the machining step such that chipping is inevitable, but again I assume you've been doing things similarly for a while and have a good handle on that? Assuming that there is a process problem that is causing this issue, the first step I would suspect would be the chromating step ... so we appended your inquiry to a thread about chromating of ADC12 which should be helpful.
Have you spoken to your supplier about the suitability of their chemistry to ADC12? Have you followed parts through the process and observed issues such as the unexpected blackness which others report in this thread? Can you make up a fresh, small bucket of chromating solution to run test parts though (see Jason Johnston's comment)? Have you watched for water-break to make sure the parts are fully clean? Can you pre-scrub some test parts with a pumice
⇦ this on
eBay or
Amazon [affil links] solution before your standard process to insure that?
Luck & Regards,
Ted Mooney, P.E. RET
Striving to live Aloha
finishing.com - Pine Beach, New Jersey
⇩ Related postings, oldest first ⇩
Q. I have a problem with chromate conversion coating on 380 aluminum: I have a very trace amount of copper on the surface of parts when the they are put into use down the road. Anyone have any ideas? I am using a thin coating of chromate. Replating of copper? Corrosion of the alloy's copper?
Joe Hankeengineer - San Jose, California
1996
A. 380 has a lot of copper in it, about 3.5 percent, so I'd certainly assume that the copper is coming from the alloy, and immersion depositing. At this point there is probably dissolved copper in the chromating bath. Whatever you are doing in terms of rinsing after cleaning / etching /desmutting probably needs improvement; but I don't know if that alone can fix the problem, or if the longevity of your chromating solution will be limited by its picking up copper this way.
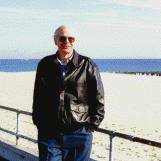
Ted Mooney, P.E.
Striving to live Aloha
finishing.com - Pine Beach, New Jersey
A. My experience has shown that chromating solutions for use with aluminum alloys have to be discarded quite frequently. It usually comes concentrated and takes little to make up. Some good hand scrubbing, caustic etch, rinse, Preposit® 748, rinse and then chromate. This works great for me.
Hope this helps.
JASON JOHNSTON- OTTAWA, ONTARIO, CANADA
2000
Q. I am looking for some information regarding Alodine 1000 and 1500. First the name and contact information for the manufacturer in the US.
Second, looking for information regarding the best method of measuring the thickness of Alodine on Aluminum die castings.
Lastly, any information regarding non-chromate chemical conversion processes for aluminum die castings (A380, 413.2, ADC 12, GD-AlSi9Cu3, GD-AlSil2(Cu)).
Thank you,
Kevin Yuskis- Richmond, Virginia USA
2000
A. Alodine is a trademark of Henkel Surface Technologies. Find them on the web or ask your local plating process distributor if they handle Henkel. This site is free but made possible by supporting advertisers, and we can't bill them the cost of maintaining contact info for their competitors :-)
I don't have a good answer for question #2, sorry, but I do have an excuse: This is a conversion process not a coating process, so it's usually measured by weight rather than thickness. But it is very thin (millionths of an inch, not thousandths).
Regarding substitutes, see www.jgpp.com/jtr-hugh.htm ⇩ for a list of the most promising, and to learn the sad news that, when independently tested, no chromate substitute really holds up yet despite all the hype and the desperate search.
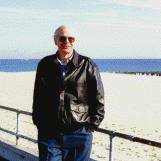
Ted Mooney, P.E.
Striving to live Aloha
finishing.com - Pine Beach, New Jersey
Update Nov. 2006: The jgpp.comdomain is still functional but the referenced page link is now broken. Progress has been made on this subject though, and there is now a MIL-DTL-5541
[⇦ this spec on DLA] approved hex-free substitute called TCP (trivalent conversion process) licensed by the navy to CST-Surtec, Henkel, Luster-On, and Metalast.
Update Feb. 2020: www.jgpp.com is now broken and leads to a site in French about house building, but there are probably additional TCP licensees by now.
Q. I need yellow Alodize (chromate conversion) technical data for die casting aluminium (ADC12), which shall meet MIL-DTL-5541 [⇦ this spec on DLA], CLASS III.
Peter Hongstudent - Nanhai, Guangdong, China
2004
A. Hi Peter. To my knowledge there is no product called "Alodize" but a technical dictionary claims --
So I think this thread covers your topic. Good luck.
Regards,
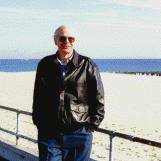
Ted Mooney, P.E.
Striving to live Aloha
finishing.com - Pine Beach, New Jersey
Q. We have been told that Alodine® can only be used with the so-called "pure" grades or primary aluminum alloys, and that it will not work with the secondary alloys, such as, 360, 380, etc., that are found in the pressure die casting industry. Is this true? I would appreciate hearing from anyone who can share their experiences of Alodining secondary aluminum alloys.
Don Wineman- Asheville, North Carolina
A. Don, perhaps whoever told you this is not familiar with the diecasting business. We probably Alodine 90-95% of the aluminum castings we run and that would include A380, A360, ADC12, 413.2, etc. Now if you had mentioned anodize, your source of information would be correct.
Kevin Yuskis- Richmond, Virginia
A. Alodine and other chromates and also anodizing may be applied to the casting alloys you listed. Only the surface preparation is different. In the case of the cast alloys the quality of the finish (either chromate or anodize) is a function of how much non-aluminum alloying ingredients we can remove from the surface, and different preparation for different alloys. Many job shops are only set-up for wrought alloys and when they try to process the casting alloys thru the same deoxidizer they leave alloying ingredients on the surface; then since we can only anodize aluminum, the presence of the silicon, copper, etc, interferes with the cosmetic appearance and the protection of the chromate or anodize oxide.
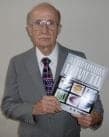
Robert H Probert
Robert H Probert Technical Services

Garner, North Carolina
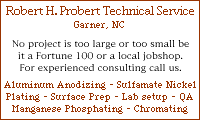
Q. Hello,
We tried to do clear chromate per MIL-DTL-5541
[⇦ this spec on DLA] on ADC-12 aluminum alloy casting.
We followed the same process as we do for extruded aluminum. The parts look blackish and we also see lot of big stains on the surface.
Can somebody help me what change in process is required to get a good finish? I heard that others had success and get good quality surface finish.
Thanks in advance.
- Randolph, Massachusetts, USA
March 15, 2013
A. Hi Pritam. We appended your inquiry to an existing thread which answers it. Diecastings contain silicon, copper, and other materials which will cause these problems if not removed from the surface with proper pretreatment chemistry. The etch, and especially the desmut process that you are using, are probably not adequate for castings. Please talk to your supplier about new chemistry for these steps. Good luck.
Regards,
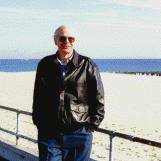
Ted Mooney, P.E.
Striving to live Aloha
finishing.com - Pine Beach, New Jersey
Q. There are so many Alodine types available like Alodine 1000, 1200, 1201, etc. I just want to know which type is suitable for ADC-12 diecasting. Can anyone tell me?
ABHISHEK JAINManagement - ALIGARH, UTTARPRADESH & INDIA
March 31, 2013
A. Hi Abhishek. Alodine is Henkel's trade name for their line of chromate conversion coating chemistry.
Yes, it is confusing because there are many types depending on whether you need a light coating with good electrical conductivity vs. a heavier more corrosion resistant coating where conductivity doesn't matter; whether you intend to apply it by spray or immersion dip; whether you want to buy it as a liquid or a powder, whether rinsing is do-able or you need drying in place, whether this is primarily a touch-up operation where you want a single-part concentrate for simplicity vs. a system where you can add replenishment chemicals to maintain a balanced system at lower cost; and whether you can use a hexavalent process or need to use trivalent. Hopefully you can understand why people cannot answer your question without more info. Please tell Henkel about your needs, and they will tell you which of their products to use. If they won't, another supplier will be happy to tell you which of their processes to use.
Good luck and Regards,
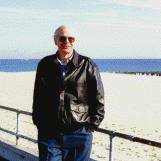
Ted Mooney, P.E.
Striving to live Aloha
finishing.com - Pine Beach, New Jersey
Black shade after chromating on ADC 12
Q. Hi friends,
We have an issue of black shade on ADC12 DIECAST PARTS after chromating Alodine 1200.
The diecast parts have black shade.
The diecast parts are machined and glass bead blasted before chromating.
We have been observing that black shades remain after chromating.
Can anyone post your views in this regard?
- COIMBATORE, TAMILNADU, INDIA
October 15, 2013
A. The issue is with your precleaning. Each of those alloys have either high Copper or Silicon, which when etched with a caustic solution will form a smut of black powder. You will need to use a more aggressive deoxidizer after caustic etch, one formulated to remove those elements. There are proprietary deoxidizers on the market, your Chromate supplier can help, or you could try a Nitric Acid/ Nitric-Sodium Bi-Fluoride Etch.
Paul Slater- Cedar Rapids, Iowa, USA
Surface treatment problem on ADC 12 pressure die casting -- insufficient salt spray hours
Q. Hi,
I am looking for a process/chemical to be used on ADC 12 castings to achieve minimum 160 hrs. salt spray life. I have tried different process/s but results are not satisfactory. Maybe because of some lubricant being used (graphite based but shifted to water based during casting process). We have used Surtec chemicals but results are not satisfactory. Will shot blasting with Stainless steel balls help improving salt spray life? Please suggest a process to achieve 160 hrs. minimum salt spray life.
- Faridabad, Haryana, India
March 11, 2015
A. Hi Varun. We added your inquiry to this thread since your interest may be in chromate conversion coating. You say you've tried different processes and you've tried Surtec brand chemicals, but it's not really clear to me what those processes were.
What cleaning regimen did you use to remove the graphite? And did you try chromate conversion coating after that cleaning? Was the chromate the final surface, or did you paint or powder coat it? How many hours of salt spray are you obtaining? Is your desmut step removing all the copper & silicon, or is the surface black? Thanks.
Regards,
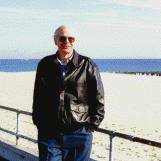
Ted Mooney, P.E.
Striving to live Aloha
finishing.com - Pine Beach, New Jersey
Q. Hi,
ADC 12 parts after nitric acid treatment gets blackish in colour. Is it the graphite based lubricant present in pores during casting process or is it due to presence of high copper? Will short blasting with SS shots before treatment will solve this problem?
Need salt spray of minimum 160 hours with trivalent based chromating. Please suggest a process. No coating is allowed -- only chromate passivation.
varun soni [returning]- Faridabad, Haryana, India
A. Hi Varun. You inquired whether the problem is the graphite based lubricant not being cleaned properly but when we asked what cleaning regimen you are trying you haven't answered, just asked the question again. Please scrub some test parts with a pumice solution and a scrub brush before doing whatever you are doing for cleaning.
You said you've tried many processes, but when we asked for details, you just asked again whether the problem is graphite, or could it be copper. It can certainly be copper, copper needs to be removed by demutting ... what are you doing/using for desmut? Thanks.
Luck & Regards,
Ted Mooney, P.E. RET
Striving to live Aloha
finishing.com - Pine Beach, New Jersey
![]() |
![]() Sir I want the procedure of how to get the silicon and carbon percentage. tukaram buddemaking aluminium alloys - aurangabad india maharastra March 17, 2015 |
Alodine 5200 on ADC12 extreme discoloration problem
Q. We have manufactured large Die Cast ADC12 chassis and steel shot blasted them, 30% HCL and Alodine 5200 post treatment that cosmetically well but not RoHs friendly. Now we are doing smaller modules and we glass bead and decrease and then treat with Alodine 5200 but the color has dissimilar wave patterns in it, like the flow of the material and is very ugly. These need to cosmetically look good but not perfect. We tries acid washes pre-treatments but still the same effect. We need some treatment that is RoHs and does not effect the thermal or electrical properties... also not expensive. Any suggestions?
Stuart RingwaldEngineer - Houston, Texas, USA
June 23, 2017
Ed. note: This RFQ is outdated, but technical replies are welcome, and readers are encouraged to post their own RFQs. But no public commercial suggestions please ( huh? why?).
A. The problem with ADC12 is the high copper and silicon content, which don't chromate and can form a smut during etching or acid pretreatment. Clear chromate or anodize will not be cosmetic on copper containing castings.
Appearance can be improved by using a fluoride based etch with nitric and HF or ammonium bifluoride to remove the copper and silicon, but cosmetic can still be an issue as the composition is different everywhere in the casting due to cooling rate. Avoid alkaline etching, this will only remove aluminum and concentrate the impurities.
I have also found better results switching to A360 grade casting material that does not contain copper.
- Rochester New York
Cosmetic Surface Finish for ADC12
Q. Hi, I am a R&D engineer in the medical device field. I recently got some parts from Malaysia that are die cast with ADC12 or A383. They sent the finished parts with Clear Chromate surface finish but the look is very "unfinished". This is a customer-facing part and is the housing for some motors with an arm and roller that pinch silicone tubing.
Earlier generation was machined parts so the finish was glossy silver and clean.
What will be a good surface finish for my ADC12 parts that can withstand tubing pinches with motors and not have any damage?
Also the customer will be cleaning this part with various cleaning solutions, so the finish needs to not get damaged over time because of cleaning.
Thank you for any help in advance.
Medical Device Company Employee - SAN JOSE, California, USA
February 21, 2020
A. Hi Sourabhi. We added your question to a thread about chromating of ADC12, which (as you will see) contains some hints about improving the appearance. But I'm a bit confused about why, aside from appearance, the chromating was okay on machined parts but not on castings. It certainly would not have had much abrasion resistance even on machined surfaces.
Yes, as an alternative, the component can be anodized for greater corrosion & abrasion resistance; topic 43432, "Anodizing On Cast Aluminum ADC12", covers this but (as you will read) you will still likely find the appearance unsatisfactory.
Another alternative is plating the castings -- see topic 33883, "Problems in Plating on ADC-12".
I don't want to be nationalistic or jingoistic because this is a WWW site for the whole world, but while buying a pair of imported sneakers is one thing, attempting to develop & control a process halfway around the world is another. "Walking the line" is fundamental to development processes, and developing this process with one of the capable shops in town would certainly be an easier approach :-)
Regards,
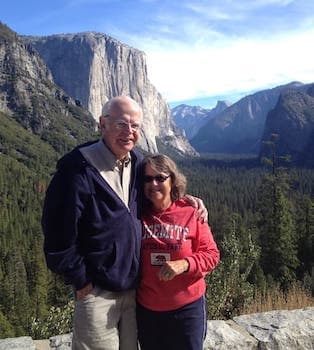
Ted Mooney, P.E. RET
Striving to live Aloha
finishing.com - Pine Beach, New Jersey
Thank you for your response. I should have mentioned previous generation parts were stainless steel machined vs. current die cast aluminum.
I agree with you on your reasoning about parts coming in from half way around the world but unfortunately that was not my decision to make. :)
Again, I appreciate the time you took to respond to this.
Best,
Medical Device Company Employee - SAN JOSE, California
Q. We are using ADC12 for Die Casting. After Shot blasting with SS 20% Chromium, Machining, Alkaline cleaning in Ultrasonic Bath, DM Rinse, DM Rinse, Vacuum Impregnation, Hot Bath Curing for 15 min, Acidic Brightening Again in Ultrasonic Bath, DM Rinse, DM Rinse, Drying. The product develops small black spots which are hard to remove even with scrub.
Please suggest best method to get proper cleaning and spot free casting. We don't want to Paint the surface.
We want to Clear Alodine the final product, but must get rid of these black spots.
- New Delhi, India
September 4, 2021
A. Hi J,
This is a very complicated need -- cosmetically acceptable clear chromate on an impregnated ADC12 casting.
I can't solve it, but remember that chromating is a conversion process, it's not a coating, and it is only capable of converting aluminum, not alloying ingredients and not impregnation materials.
Luck & Regards,
Ted Mooney, P.E. RET
Striving to live Aloha
finishing.com - Pine Beach, New Jersey
Q, A, or Comment on THIS thread -or- Start a NEW Thread