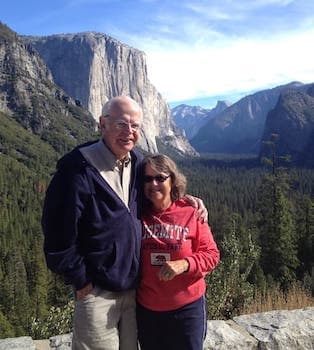
Curated with aloha by
Ted Mooney, P.E. RET
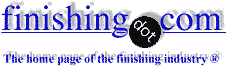
The authoritative public forum
for Metal Finishing 1989-2025
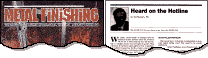
-----
Anodizing On Cast Aluminum (ADC12)
Q. Hi, I got feedback from a supplier that he cannot make a hard anodize (type 3) to cast aluminum part (ADC12), I am wondering what is the difference in the process between type 2 to type 3 and why he cannot make it.
Additionally why the thickness of the anodize type 2 is only 10 MICRON can he make it thicker?
I want another opinion before I contact him.
Thanks
design engineer - Israel, Ashdod
March 15, 2022
A. Hi Ofir. A vendor declining to quote is not the same thing as saying that something can't be done :-)
It is difficult to anodize ADC12 because of all of the non-aluminum content in it; and the thicker you want it, the more difficult and the less aesthetic. But it can be done and probably even to a thickness of 0.002" (50µm) although 0.001" (25 µm) is more practical.
Luck & Regards,
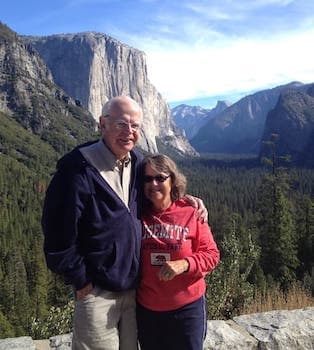
Ted Mooney, P.E. RET
Striving to live Aloha
finishing.com - Pine Beach, New Jersey
March 2022
⇩ Related postings, oldest first ⇩
2000
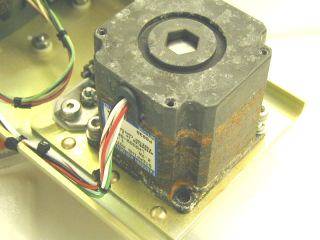
Q. Problems with black anodizing of aluminum die castings
1. We have two types of aluminum casting materials that we try to black anodize. The first is A380 which is cast in the U.S.; the other is ADC-12 which is cast in the far east. We have run into some problems with humidity testing the motors (casting material ADC-12 in photo) are placed in a chamber for 10 days @ 100% humidity and at the end of the test the castings exhibit white blotches. Can you explain what is happening? See photo of problem.
2. What would be your recommendation for corrosion protection for A380 and ADC-12 if Black Anodize will not work because of the high silicon content in the material?
Rick Henderson, Chief Designermotors- Dover, New Hampshire USA
A. We don't think the anodic film is thick enough? Please check the thickness.
Max Faeth- Los Angeles, California, USA
2000
A. YOU MAY SWITCH TO ALUMINUM ALLOY A413 LOW COPPER ALLOY AND HAVE BETTER BASE METAL RESISTANCE.
JEROME GRAESER- SULLIVAN, Missouri
2003
Multiple threads merged: please forgive chronology errors and repetition 🙂
Q. Dear All,
Can anyone tell me whether the ADC12 grade casted part can be anodized?
Regards,
Innotech - Penang, Malaysia
2006
Treatment &
Finishing of
Aluminium and
Its Alloys"
by Wernick, Pinner
& Sheasby
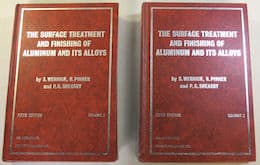
(note: this book is two volumes)
on eBay or
AbeBooks
or Amazon
(affil links)
A. Yes, although the anodize appearance is only fair.
ADC 12 per Japan JIS5032 composition: Cu 1.5-3.5, Si 9.6-12.0, Mg 0.3 max, Zn 1.0 max, Fe 0.9 max, Mn 0.5 max, Sn 0.3 max, Al remainder.
Primarily used for pressure die casting. Similar to LM2 per BS 1490, Aluminum Association 384.0, ISO AlSi10Cu2Fe, and AC 46100 per EN 1706.
- Goleta, California

Rest in peace, Ken. Thank you for your hard work which the finishing world, and we at finishing.com, continue to benefit from.
Q. Dear,
After anodizing parts made of LM 2 material, some of them have black patches on some machined surfaces.
What is the reason of these black and very hard patches?
How to prevent it?
- Belgium
2007
A. Hi --
Generally aluminum alloys containing silicon will have a black, powdery, coal-dust-coated appearance after anodizing.
[I believe it is the silicon itself that is the culprit tho the chemistry I am not entirely certain of. I'll ask a materials professor at Lehigh about this.]
380 or 356 for instance anodize into a very dark, powdery appearance. the anodize itself can still be to speck for what it is -- an electrically induced oxidization of aluminum -- that would otherwise take decades or even centuries to achieve at standard temp, pressure, atmosphere.
Conversely, aluminum alloys high (>95%)in combined aluminum and/or magnesium content anodize very nicely and truly can result in a 'clear anodize' (for instance, the 5xx series cast as well as the6xxx series, bar stock. other families also can fit the bill as well if you check the chemistries).
- Bethlehem, Pennsylvania, USA
February 7, 2008
Multiple threads merged: please forgive chronology errors and repetition 🙂
How to anodize ADC12 material with blue color?
Q. I am a Chinese, I work in a trading company, I am dealing a project which all part are make of ADC12(a type die casting aluminium), and the customer ask us to anodize the part with blue color, but our supplier, a metal stamping factory , told me their supplier can't anodize the ADC12 with blue color, and then I am trying to ask other anodization supplier around our city, but some factory said they can use electrophoresis to make the blue color on the part, and some factory said they can anodize the ADC12 with blue color, and most of factories said they can't do it, are there anybody can tell me if ADC12 part can be anodized with blue color? Why? Thanks!
David Tangproduct designer - ZhuHai, GuangDong, China
2007
A. Blue anodizing any aluminum can be done, however, if you're looking to achieve a cosmetic, aesthetic looking blue, it's not easy if at all with aluminum die castings that contain appreciable silicon, such as ADC12. The resulting anodic coating will be blotchy, dark in silicon-rich areas(often the outer non-machined skin), and likely to be powdery in areas. If you're looking to get a "MagLite" type blue, it won't happen with ADC12! Good luck and I hope this helps.... get a sample done by the house that says they can do it and make sure your customer will accept it!
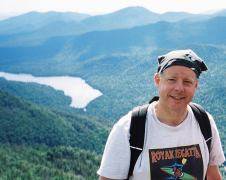
Milt Stevenson, Jr.
Syracuse, New York
2007
Q. Hi there,
I have some small (114 mm x 55 x 55) die cast aluminium boxes that I would like to anodise blue. Do you think this type of material will be suitable for anodising? In not what would you suggest.
Thanks in advance
Ben
product designer - Glasgow, United Kingdom
March 31, 2010
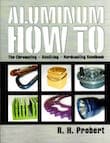
Aluminum How-To
"Chromating - Anodizing - Hardcoating"
by Robert Probert
Also available in Spanish
You'll love this book. Finishing.com has sold almost a thousand copies without a single return request :-)
March 2010
Hi, Ben. As you see, we appended your inquiry to a thread that may answer it for you. Good luck.
Regards,
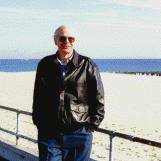
Ted Mooney, P.E.
Striving to live Aloha
finishing.com - Pine Beach, New Jersey
Multiple threads merged: please forgive chronology errors and repetition 🙂
Grade of Aluminum suitable for Pressure die casting and Anodising
Q. I'm looking for a Grade(s) of Aluminum that can be manufactured through Pressure die casting Process and that can be Anodised.
Kester Sujay SureshSenior Engineer in a Watch Manufacturing Industry - Hosur, Krishnagiri District, Tamil Nadu, India
July 24, 2008
A. Hi
I am not expert in Aluminum Die casting, but I have been doing anodizing on ADC 6(5xxx)- Magnesium Alloy, cast parts.
ADC 12, cast parts also we have tried, but it is a Silicon alloy not suitable for anodizing, finish as well as the SST results are problematic there.
I also know that producing casting on ADC 6 is a difficult task.
Good luck...
- Chennai, India
July 29, 2008
What finish can you put on Cast Aluminum products?
Q. I am creating a new kitchen appliance that will go in an oven.
Most of the parts will be made of cast AL ADC12.
I am trying to find a surface treatment that will work up to 500 °F. What would you recommend? My supplier says you cannot anodize cast AL, and I don't know about teflon coatings at this temperature?
engineer - Alpine, Utah
June 8, 2016
A. Die-castings can be anodized or hardcoated. However, they have an uneven appearance which may make them unsuitable for cosmetic applications.
Chris Jurey, Past-President IHAALuke Engineering & Mfg. Co. Inc.

Wadsworth, Ohio
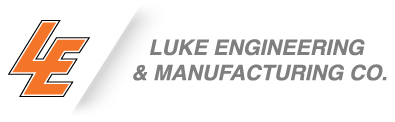
June 15, 2016
A. There are a lot of people who regularly check out this site that can help you, but you probably have to explain what you hope to achieve by coating the aluminum.
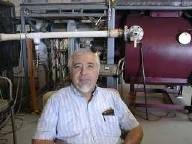
Jim Treglio - scwineryreview.com
PVD Consultant & Wine Lover
San Diego, California
June 9, 2016
A. Stating the alloy will help get a more specific response to your question, but Aluminum castings CAN be hardcoat anodized if what you're looking for is a FUNCTIONAL rather than decorative coating. We do some parts at our shop that are hardcoated and dyed castings; the dye doesn't really 'take' attractively the way it does on wrought alloys, but if your goal is corrosion and abrasion resistance it's an option.
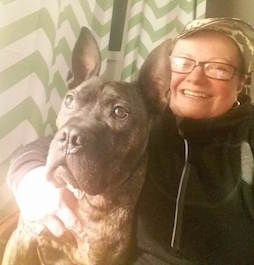
Rachel Mackintosh
lab rat - Greenfield, Vermont
June 17, 2016
![]() |
Q. This product is a kitchen appliance so appearance is everything. I was aware of the splotchy finish on hard anodize so I was looking for a solution that would be uniform. This is why I was considering teflon. - Alpine, Utah USA June 20, 2016 September 2016 A. Hi. I have ceramic coated cast iron cookware ("Le Creuset") that we're very happy with. I believe they are sprayed on at very high temperature. Although aluminum has more temperature sensitivity than cast iron, just reading some ads it seems that the same colorful ceramic coatings can be applied to aluminum cookware, and presumably your product. Good luck. Regards, ![]() Ted Mooney, P.E. RET Striving to live Aloha finishing.com - Pine Beach, New Jersey |
Q. ADC12 Aluminum contains 9.6 to 12.0 % of Silicon & 1.5 to 3.5% of copper. When you go in any chemical bath it turns dark. How do I make surface brighter before anodizing.
Kanak Patel- Paterson, New Jersey, USA
October 27, 2016
White spot 24 hours after anodizing adc12 aluminum
by Runge & Kaufman
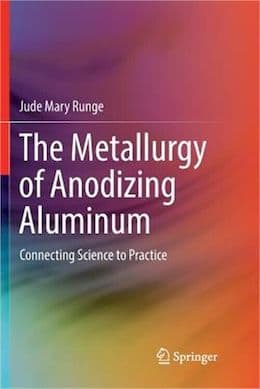
on AbeBooks
or eBay or
Amazon
(affil links)
Q. Hello,
I have aluminum ADC 12 alloy, I want to non-stick coat.
Now I have formula for desmutting ADC 12, before I use OKUNO ADD 320
My formula: 25% HF + 75% HNO3
My steps:
NaOH 20% --> Rinse --> HNO3 50% --> Rinse --> OKUNO ADD 320 (Now I use my formula) --> Rinse --> Anodizing --> Rinse --> Dry --> Non-stick coating
After using my formula and OKUNO ADD 320, the same brightness
I have tested it after anodizing:
Immersion Water (Not RO), Micron Siemen : 366
After 24 hour
Okuno ADD 320 : Have some white spots
My formula: Have a lots of white spots
Why my formula has more spots than OKUNO ADD 320 ?
Thanks for answer.
Engineer - Viet Nam
A. Hi Huy. Step one in eliminating white spots seems to be to continue to use a proprietary product, because you have proven its effectiveness. In asking why a proprietary product works better than your home made acid mixture, you might as well ask how to improve the taste of a homemade wine so it's as good as Vang Dalat :-)
... because readers don't know what is in Okuno Top ADD 320 and, if they did, we could not legally post it on the internet anyway.
But step two is to look into other causes of white spots, and Robert Probert's article on the subject is a good starting point. Good luck!
Regards,
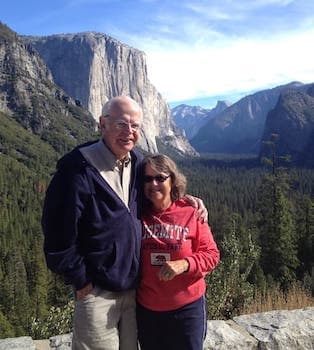
Ted Mooney, P.E. RET
Striving to live Aloha
finishing.com - Pine Beach, New Jersey
March 2017
Thank you very much !
Engineer - Viet Nam
March 19, 2017
Q. Currently I have a project to have clear anodize on ADC12 casting part. However, there is a lot of yellow stain/patches which my customer cannot accept. May I know is there any way to eliminate the yellow stain/patches?
Thank you.
- Bayan Lepas, Malaysia
June 19, 2019
Q, A, or Comment on THIS thread -or- Start a NEW Thread