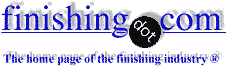
-----
Type 2-1/2 & Room Temperature Hardcoat Anodizing

TUTORIAL & FAQs:
Readers who would like a quick intro to aluminum anodizing and its terminology, including "Type II", "Type III" and the slang term "type 2-1/2 anodizing" may wish to review our 1-1/2 page "Introduction to Anodizing of Aluminum" to make understanding this thread easier.
Q. How do you know when the additive (glycolic acid) is used up? Is there a method for determining this?
Thanks
- Austin,Texas
November 23, 2021
Tip: This forum was established to build camaraderie among enthusiasts through sharing tips, opinions, pics & personality.
The curator & some readers who publicly share their info will be less likely to engage with those who don't.
A. If your hard coat additive is the popular 2% Glycolic Acid with 2% Glycerin, YES, titration procedure is available, but cannot post it here. Your additive supplier should furnish a way to control the additive.
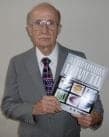
Robert H Probert
Robert H Probert Technical Services

Garner, North Carolina
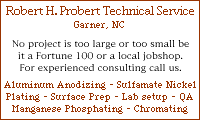
November 25, 2021
December 24, 2021
A. Hi Jane Jane.
Typically you'd send your anodizing additive supplier a specimen on a schedule determined by your bath volume/ throughput. Also type 2-1/2 around here (fishing reels, yes our nadcap shop has some fun) is more like 45-55 °F. Room temperature (70 °F) is straight TyII per spec requirements. So look at your process as much as your additives. I can't recall offhand what my anti-burn additive lists as the active but it smells like dry erase markers and costs about $850 us for a 5 gallon pail... there's some vocs in there ... I assume you run heavy air sparging or other aggressive mixing in the tank?
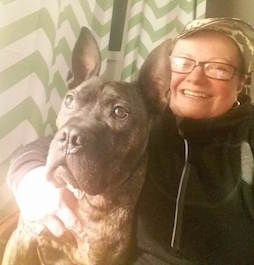
Rachel Mackintosh
lab rat - Greenfield, Vermont
⇩ Related postings, oldest first ⇩
1996
Q. This question is about Aluminum finishing. Can anyone provide more information on SANFORD HARDCOATING process? Is this a proven answer for hardcoating high Silicon alloy?
Thanks in advance.
Ganesh NatarajanTreatment &
Finishing of
Aluminium and
Its Alloys"
by Wernick, Pinner
& Sheasby
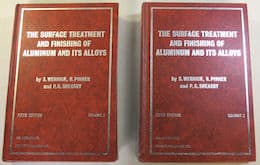
on eBay or Amazon
or AbeBooks
(affil link)
A. The 'Sanford Process' is a proprietary hardcoat process. Please contact the licensor for information because we don't discuss proprietaries/brands here ( huh? why?). Apologies.
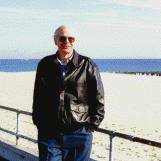
Ted Mooney, P.E.
Striving to live Aloha
finishing.com - Pine Beach, New Jersey
adv.
Luke Engineering has been hardcoating high silicon/copper aluminum die-castings for over twenty years with the unique process LUKONDC. Hardcoating thicknesses of up to 75 µm are possible, however, in production the "normal" thickness range is 20 to 50 µm.
We will be glad to hardcoat prototypes for evaluation, free of charge.
Luke Engineering & Mfg. Co. Inc.

Wadsworth, Ohio
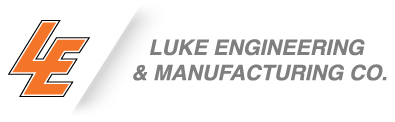
1996
Q. We are using [a proprietary process] and are having issues. Namely, we're failing Taber tests on 6061 with this process.
We *did* have temperature uniformity issues which are gone now.
Chemistry (sulfuric acid component) is okay. We don't have an analysis for the [brand name] additive, they so far been silent.
I'd like to fix our process, then pursue a process more transparent one.
- Loves Park, Illinois
August 24, 2011
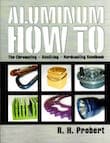
Aluminum How-To
"Chromating - Anodizing - Hardcoating"
by Robert Probert
Also available in Spanish
You'll love this book. Finishing.com has sold almost a thousand copies without a single return request :-)
A. Hi, Joe.
I visited that supplier so long ago that I barely remember it, but to my knowledge the process is "Type 2-1/2" anodizing -- a simulated hard anodizing that does not require the electrolyte to be 28° F, but about halfway from there to ambient temperature. We don't discuss brands here ( huh? why?), but as you can see from the previous postings, there are additional brands of proprietary alternatives.
All proprietary processes will lack some degree of transparency or they wouldn't be proprietary of course, but if you want a transparent process you can operate at 28° F. and do real type 3 anodizing, or you can refer to Wernick, Pinner & Sheasby or Probert's "Aluminum How-To" for generic info on glycolic acid, glycerine, and similar additives. Good luck!
Regards,
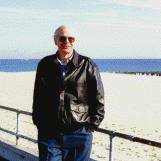
Ted Mooney, P.E.
Striving to live Aloha
finishing.com - Pine Beach, New Jersey
Q. I know that some anodizers raise their bath temperature to around 50 °F for hard anodize to achieve thicker coatings. Can you tell me what properties are effected within the anodized coat by this process? Also what role can additives to the anodize bath play in achieving thicker coats? How do they work?
Garry Pickettaerospace - Los Angeles, California
1998
1998
A. I'm not sure whether you have the direction of the temperature change wrong, Garry, or I'm just misunderstanding you. In anodizing, what happens is that the electricity forms the coating, and the sulfuric acid simultaneously dissolves some of it. The hotter the acid, the faster the dissolution--which is why hard coat anodizing is done at much lower temperatures than conventional anodizing, so that the equilibrium point is at a thicker coating.
Purportedly, additives allow hard coat anodizing to be done in the 50 °F range you mention, rather than the usual 28-32 °F. While there are additives that work, the industry has also seen some snake oil, so I'd be slow to even swear that they all work, let alone try to explain how they work. I believe that most are based on oxalic and/or glycolic acid, and an expired patent search with those terms may tell you more. Hopefully, a supplier of these additives will reference a study on the subject; I will cheerfully read it because I haven't stumbled upon any explanations myself yet.
Readers may also be interested in letter 41283, "Is oxalic anodizing equal to hardcoat anodizing?".
Regards,
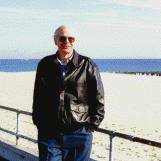
Ted Mooney, P.E.
Striving to live Aloha
finishing.com - Pine Beach, New Jersey
1998
A. Garry,
Several companies sell additives to achieve "hard coat" equivalents. Some or most or all of them can duplicate some of the characteristics of hard coat but not all of them.
I have not heard anyone give a good reason for how or why they work.
They allow you to run a higher voltage and current density at a given temperature without burning.
The folks at Henkel in Atlanta can probably give you some of the information you are looking for.
Metalast in Nevada appear to come closer to true hard coat and at a very high speed. Their process is proprietary and you must buy in and pay royalties. It is unaffordable unless you are going to do a lot of hard coat or thick coat and then it is fast enough to be a profitable purchase.
They will not tell you what their additive is and have said on one occasion that they do not truly know why it works as well as it does.
Jim
James Watts- Navarre, Florida
A. Many commercial anodizers are lowering their bath temperature and calling it hardcoat. Except in special circumstances, very few traditional cold tank (25-40 °F) hardcoaters are raising their bath temperatures. This hot tank (50-65 °F) hardcoating is more appropriately referred to as pseudo or Type II 1/2 hardcoating.
All things being equal, higher bath temperatures result in softer, more porous anodic coatings. This larger pore structure can allow for greater terminal thicknesses. Other anodizer controlled variables such as; bath additives, acid concentration, dissolved aluminum, current density, electrical waveform, cathode design, agitation, and racking also have a significant effect on hardcoat quality. Bath additives, typically organic acids, raise the solution conductivity without increasing the acid attack on the anodic coating.
This can help mitigate problems from other less than ideal process parameters and opens the window for acceptable coatings under a wider range of conditions. However, acceptable is not necessarily the same as equivalent.
Chris Jurey, Past-President IHAALuke Engineering & Mfg. Co. Inc.

Wadsworth, Ohio
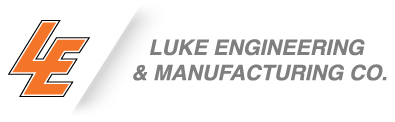
1998
1998
A. The above comments have said it pretty well. Let me add that the anodic coating consists of a hexagonal cellular structure and within each cell is a pore. The density of the coating is the size and number of the cells and pores within a given area. This can often be indirectly measured by using coating weights and the number of cycles on a Taber Abrasion tester, prior to breakthrough. The pore size and cellular structure are determined by electronic field effects. The pore size depends linearly upon the anodic voltage and upon the electrolyte pH. The number of cells is due to the current density, as is the rate of growth. As the anodic coating grows it is also dissolving. At a point when the rate of growth equals the rate of dissolution the part is dimensionally shrinking.
Hardcoat anodizing allows a higher current density to be applied without the parts burning (increases the rate of growth/cell density), and slows down the rate of dissolution (temperature = time in chemical reactions) thus allowing thicker coatings which are more dense.
Anodizing additives work by reducing the rate of dissolution and at the same time allowing higher current densities, thus still causing a dense/thick coating. Additives work by affecting the pH and conductivity of the anodizing electrolyte at the surface of the part.
Personally, I have seen 6-8 mil thick coatings per surface, produced on conveyor rollers, at a temperature of 68-72 °F using an electrolyte additive, and high current densities. This same tank chemistry also produced 60 °F coatings which passed Taber abrasion testing and coating weights per MIL-A-8625 / MIL-PRF-8625 [⇦ this spec on DLA]. It might well be argued that those coatings were not as dense as cold temperature produced hardcoat, however I do not know of any studies comparing the density of cold produced hardcoat versus additive produced hard coat.
An excellent study of the field effects during anodizing which relates anodizing parameters to oxide growth is:
Theoretical Modeling of Porous Oxide Growth on Aluminum published 1992 in J. Phys. D: Appl. Phys. 25 pages 1258-1263.
Ward Barcafer, CEFaerospace - Wichita, Kansas
Multiple threads merged: please forgive chronology errors and repetition 🙂
Room Temp Hard Anodizing
Q. We want to convert our conventional 30 degree Hardcoat anodize line to a mid, or room temperature process. Although we understand that there are some expensive proprietary licensed processes available, we wonder if this is the only way to get there. Are there some relatively simple baths that are commonly used that will operate in the 50 degree + range. All advice will be appreciated.
Thanks
Pete Faxon- Oxnard, California
1998
A. There are a number of non-licensed hardcoat additives on the market. These additives, when added to the anodize tank will help retard the tendency toward burning. They will also allow a moderate increase in processing temperature. Care should be taken to follow the manufacturer's recommendations.
Charlie Grubbs- Alpharetta, Georgia
1998
![]() ![]() |
Q. I am interested in room temperature anodizing process. ![]() Yongsoo Jeong - Changwon, Kyungnam, Korea 1998 Q. I would be deeply grateful if information is provided on Hard Anodizing at room temperature. Prem Sagar- Bangalore, INDIA 1999 Q. I want technical information about hard anodizing at room temp.can you give it Thanks lots, Laljikpatolia- Gujrat, India 2001 Q. I'm also interested in following up the already many time asked questions about how anodize aluminum for hardening at room temperature. - San Juan, Argentina August 15, 2009 |
Hardcoat Anodize Additives - ANODAL EE & Others
Q. Looking for pro & con info from anybody using the Anodal EE Hardcoat additive from Sandoz aka Clariant.
Are you happy with it? Any problems with it?
Any pro & con info from anyone using any other Hardcoat Anodize additives would also be appreciated.
David A. Kraft- Long Island City, New York
1998
----
Ed. note-- Readers: Please offer your opinions of proprietaries vs. generic additives, and express any general thoughts you wish ... but we can't compare one proprietary to another in this forum, or praise or slam any brand or source on this no-registration site (why?).
![]() |
Q. HI THERE, I AM JUST ENQUIRING ABOUT THE PRODUCT ANODAL EE. I HAVE USED IT BEFORE AND WOULD LIKE TO USE IT AGAIN BUT I AM HAVING TROUBLE GETTING INFO AND ALSO GETTING THE PRODUCT ITSELF. ANY HELP WOULD BE GREATLY APPRECIATED. ROBERT GIMENEZANODISING SHOP 1999 Q. Hi owner of a anodizing shop - Eksjö, Sweden May 20, 2008 |
Multiple threads merged: please forgive chronology errors and repetition 🙂
Hardcoat anodizing at room temp
1998Q. I have communicated with you before I think in one of the finishing chat rooms. I am a subscriber to metal finishing and follow your Q&A's quite closely.
I am very interested in the hardcoating process that is done at room temp (50-70 °F). What are the organic additives needed and their amounts g\L in a sulfuric acid solution? Is this a proprietary product and what will be my current density and voltage needs. Several of our customers have all said "think big" because of the large items they are currently having hardcoated. Can you provide me with some guidance or point me in the right direction? Any suggestions or pointers?
I thank you in advance.
Kenny Bryant1998
A. Anodizing additive packages are available from a number of metal finishing chemical suppliers as are proprietary anodizing "systems" which include bath chemistries. The literature details a number of beneficial organic additives which may be less expensive to purchase. There is no such thing as an industry standard, most anodizers have their own favorite.
Many refer to hot tank hardcoating as pseudo or Type II 1/2 hardcoating. It may meet the minimum requirements for hardcoating under certain conditions but may not be equivalent to traditional cold tank processing. In general, with all factors being equal, colder is harder.
Chris Jurey, Past-President IHAALuke Engineering & Mfg. Co. Inc.

Wadsworth, Ohio
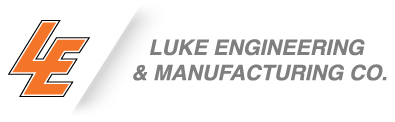
A. I agree with Chris. There is no substitute for low temperature hardcoat anodizing. Certain additives can enhance the process, but CONTROL and AGITATION are equally, if not more important!
There is little "magic" in proper hardcoating. It is a matter of sticking to the basics.
Charlie Grubbs- Alpharetta, Georgia
1998
How to speed up the hard anodizing process
Q. As far as I know, hard anodizing needs to be done at low temperatures and takes a long time to achieve higher thickness. Is there any possibility to speed up the process through whatever kind of chemical pretreatment of the workpiece and get colored film?
Yang, NingResearcher - Chutung, Hsinchu, Taiwan
2004
A. Hello Ning. The anodizing reaction consists of two competing reactions: building up of the oxide through electricity, and destruction of the oxide by acid attack. So running this process at low temperatures, where the acid is less active, speeds up the process rather than slowing it down.
There are numerous additives and patented or trade secret processes for hard anodizing and "type 2-1/2" (higher temperature pseudo-hardcoat anodizing). Chris gave us the general hint that they increase conductivity without increasing acid attack. But the people who have developed these generally wish to license the technology (or sell the additive) rather than telling you what it is and how to make it. Contact suppliers like Clariant, Metalast, N>Tec, or U.S. Specialty Color, or do a Google search.
Although hard anodizing has a grayish cast compared to thinner anodizing, it can be dyed to various colors. Dyes need to be sealed, and this sealing process softens the hard anodized coating somewhat, so hardcoat is not usually dyed, but it is not truly rare for parts to be hard coated or type 2-1/2 anodized and then dyed. For example, some ammunition is hardcoated but must be dyed to distinguish live from dummy rounds.
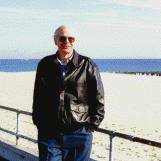
Ted Mooney, P.E.
Striving to live Aloha
finishing.com - Pine Beach, New Jersey
2004
Hi Ted,
Thanks for the detailed explanation.
Yang, Ning [returning]- Hsinchu, Taiwan
2004
Anodizing additives, room temp. anodizing
RFQ: I would be grateful for more about hard and decorative anodizing baths, the additives, and some of equipment for room temperature.
I'm using Sulfuric acid (150 g/l) added with oxalic acid (2 g/l) for decorative anodizing at temperature 10 °C to 500 HV hard (clear hard), and room temperature (30 °C) for decorative products and using Lead cathodes.
ALUMETAL - Blumenau, Santa Catarina, Brazil
2005
Ed. note: This RFQ is outdated, but technical replies are welcome, and readers are encouraged to post their own RFQs. But no public commercial suggestions please ( huh? why?).
How to verify between hard anodize and normal anodize?
Q. I would like to know how to verify accurately whether an anodized part is anodized or hard anodized?
Ronald YeohPrecision Machining - Singapore
2005
2005
A. The question isn't quite a valid one, Ronald; you wouldn't take a pile of parts and sort them, claiming these are hard, and those are conventional. Rather, each part meets certain specs or it doesn't. In broad generalities though, hard anodized parts would probably have a coating of 2 thousandths of an inch, and would be unsealed whereas conventional parts would have a thickness of well under a thousandth of an inch and would pass a seal test. But there are also "Type 2-1/2" coatings that may be halfway in between. Please try to describe the actual situation because we can probably quickly offer an answer to your particular situation but it can take a book to answer generalized questions covering all possible variations and their almost endless "ifs, ands & buts" :-)
Thanks.
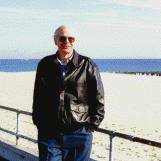
Ted Mooney, P.E.
Striving to live Aloha
finishing.com - Pine Beach, New Jersey
Q. Dear Ted,
Thanks for your kind response. My professional knowledge in anodizing is pretty limited which explained the manner of the question posed. My current situation is that I need to verify that the plater is really doing hard matte anodizing on the parts instead of normal anodizing. I tried testing the first batches by running a round edge tool lightly across the surface and a line could be seen where the tool moves across. Am I right in concluding that this should not happen with hard matte anodizing? As such, I am seeking for a better/accurate methods to verify the parts.
Precision Machining - Singapore
2005
2005
A. The principal and easiest distinction between hard anodizing and conventional anodizing is probably the thickness; unless otherwise agreed, hardcoating must be .002" thick according to MIL-A-8625 / MIL-PRF-8625 [⇦ this spec on DLA]. When you review that spec, you'll see that it also references a hardness test that hard anodizing is expected to pass.
But a hint is: if the parts still look like aluminum, they almost surely aren't hard anodized; if they are black although not dyed, they probably were hard anodized; some alloys turn dark gray when hard anodized, but some alloys turn dark gray even from a conventional anodize and black from hard anodizing so it's more difficult to tell.
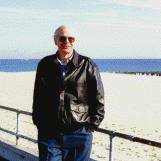
Ted Mooney, P.E.
Striving to live Aloha
finishing.com - Pine Beach, New Jersey
2005
A. While I'm hesitant to offer the following, because as Ted said - it is very dependent upon your exact circumstance, there is a substantial weight and thickness difference between a MIL-A-8625 type II (conventional) and a MIL-A-8625 type III (hard) anodize coating.
Type II has to have at least 1000 mg/sq foot coating weight (approx. 4 micrometers under normal conditions) and pass certain tests for corrosion resistance. Type III has to be a minimum of .002 inches thick (50.8 micrometers) unless specified otherwise, with a coating weight of 4320 mg/sq foot per 0.001 inch.
So - if the parts were done to spec (rather than just "hard anodize"), and if they pass all other testing requirements, you could sort them by checking the anodize thickness.
What is your exact situation?
Compton, California, USA
⇦ Tip: Readers want to learn from your situation;
so some readers skip abstract questions.
Q. Hi,
Is the any difference BTW hard anodize to conventional anodize in term of resistance?
I know hard anodize is very high resistance. What about conventional anodize?
Thanks,
- Haifa, Israel
March 17, 2016
March 2016
A. Hi Shaul. Yes there's a difference. Hard anodizing is thicker and therefore offers more electrical, wear, and corrosion resistance. This is reflected by the hard anodized coatings requiring higher voltage rectifiers to achieve them. But again, if you would please describe your actual situation, we can avoid these generalized answers which always have exceptions and which are often misleading. Good luck.
Regards,
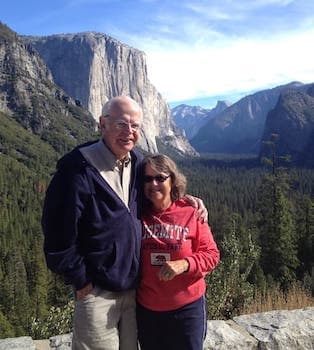
Ted Mooney, P.E. RET
Striving to live Aloha
finishing.com - Pine Beach, New Jersey
March 22, 2016
A. Hi Shaul,
I delayed replying to see if you would describe, as suggested by Ted, the actual situation. It can be so much easier to offer advice if the real problem is known.
I am uneasy about measuring resistivity. Firstly, how are you going make repeatable measurements? It is quite easy to to measure the resistance of say, aluminium wire. But a very thin, high resistance anodic film on a highly conductive base is a very different matter. You would need to get a repeatable surface area of contact. In reality the surface undulations would make the intimate contact, required for getting a flow of current, highly variable. Secondly, moisture in anodic pores or surface defects could substantially reduce the apparent resistance.
Voltage breakdown, to measure film thickness, might be more helpful. ISO anodizing standards include such tests.
It does not follow that hard anodized films are thicker than convention ones though they usually are. It is perfectly possible to have 25 µm in both. This is a instance where knowledge of the actual situation would be so useful. (Sorry, I couldn't resist turning the knife).
Ultimately hard anodizing is defined by hardness and not thickness. An abrasion test with a suitable abrasive medium might separate the sheep from the goats.
Your comments please.
Harry
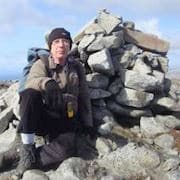
Harry Parkes
- Birmingham, UK
Q. Can we use oxalic acid and sulfuric acid together for best oxidation layer? Temperature is 19 °C to 22 °C, and ratio of solution is 17% to 18%. If anybody knows about the anodizing method, please inform me, thanks to all.
naveed muhammadps plate engineer - Faisalabad Pakistan
December 11, 2015
December 2015
Hi Naveed. As you know, there's no "best" except in response to a specific list of requirements. If oxalic acid and sulfuric acid together were "best", everyone would be using them ... whereas I suspect that there are many more anodizers using straight sulfuric acid (Type II anodizing) than such mixes.
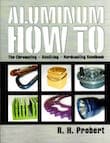
Aluminum How-To
"Chromating - Anodizing - Hardcoating"
by Robert Probert
Also available in Spanish
You'll love this book. Finishing.com has sold almost a thousand copies without a single return request :-)
What alloy(s) do you plan to process, and what thickness of anodizing are you seeking? Thanks!
Glycolic acid is also sometimes used as a hardcoat additive, and Robert Probert's "Aluminum How-To" offers some info and formulations. You can perhaps also find more by searching the site for "glycolic anodize" and "oxalic anodize". Good luck.
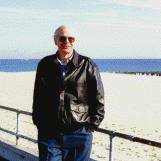
Ted Mooney, P.E.
Striving to live Aloha
finishing.com - Pine Beach, New Jersey
Q. Are anodizing additives indeed useful for reducing time, energy consumption and refrigeration requirements? Is there any user of these chemicals?
alaattin tuna- TURKEY,sakarya
January 20, 2016
A. Hi Alaattin. We combined a bunch of threads on that subject here, and then appended your inquiry to it. I think you'll find your answers on this page now.
Additives don't reduce required anodizing time -- the 720 rule still holds. They allow higher temperature pseudo hard anodizing, so refrigeration may be simpler, but they don't reduce energy requirements by much, because any heat the rectifier puts in, the cooling system still has to take out. Good luck!
Regards,
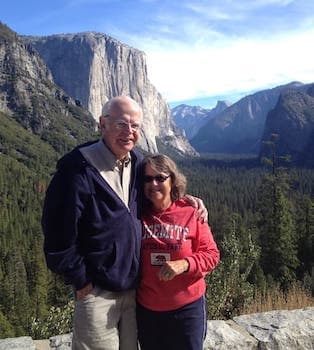
Ted Mooney, P.E. RET
Striving to live Aloha
finishing.com - Pine Beach, New Jersey
January 2016
Q. Hi guys , what is the proprietary additive that is in the acid solution when hard anodising?
Brian WardmanRestorer - Sydney Australia
April 28, 2019
April 2019
A. Hi Brian. What's the secret formula for Coca-Cola and Big Mac's special sauce? :-)
The formulas wouldn't be proprietary if they weren't trade secrets, but as an introduction you can look up "MAE (multipurpose anodizing electrolyte) Process" to learn that it (and probably they) involve glycolic acid and/or glycerin and/or oxalic acid. We appended your inquiry to a long thread with lots of info and reference sources.
Good luck.
Regards,
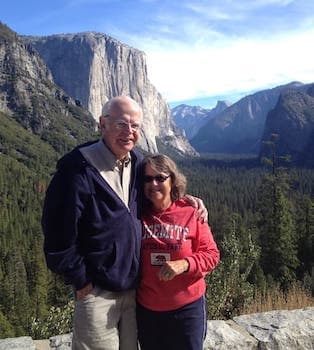
Ted Mooney, P.E. RET
Striving to live Aloha
finishing.com - Pine Beach, New Jersey
May 31, 2021
Q. Hi Finishing.com,
We are a fairly large surface treatment factory in Sweden. Among many different services we offer Anodizing. Our Passivation/Anodizing-line consists of three tanks of H2SO4-solution where we perform Anodizing 5-25 µm. The tanks have cooling to avoid overheating.
We've received a very interesting RFQ but the specification is 35 µm on 6060 alloy. We are unable to reach this thickness with our current parameters. And my question is if there is an easy fix to obtain this thickness. As far as I've understood and read on this forum there are quite a few differences between hard anodizing and "normal" anodizing.
Questions:
1. The spec on drawing just relates to thickness of anodizing. Which makes me believe that potential differences in crystal structures is not the main issue. Do you agree with this?
2. Would simply setting cooling down to i.e. 10 °C make 35 µm possible if enough time in the anodizing bath?
3. Do I have to mix in oxalic acid or is this just a method of controlling temperature or expanding the "process window"?
4. Any other suggestions on how to easy convert one of our tanks to be able to achieve 35 µm?
Best,
Eric
- Sweden Gothenburg
May 31, 2021
A. 35 microns is, to us, 0.0014 inch thick. After you pass about 0.0008 you need more voltage to overcome the resistance.
Depending on the alloy you can get 0.001" with about 24 volts (but not on the 2000 alloys). Come back and tell us your top available voltage. If you've got about 30 volts you can get 0.0014" without an additive and without cooling so low. The colder requires more voltage and since you do not need the small pore or abrasion resistance, you may stay up around 72 °F (22 °C). Oxalic, glycolic, and glycerin additives will not help you get thickness, those additives only make the pore smaller which you do not need. Again, all you need is enough voltage to overcome the resistance at 0.001" so it will go on to 0.0014".
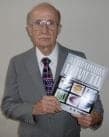
Robert H Probert
Robert H Probert Technical Services

Garner, North Carolina
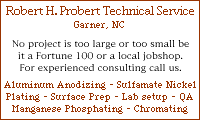
June 8, 2021
A. Eric,
adv.
Contact me directly about suggested additives to produce up to 100 microns of hard anodized aluminum coating without going into deep cooling.
Also the newly developed technology of micro-arc aluminum anodizing produces up to 55 microns extremely hard coating.
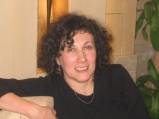
Anna Berkovich
Russamer Lab

Pittsburgh, Pennsylvania
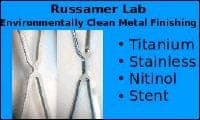
Thank you for your replies! Our rectifier goes up to 24V/3000A so we took your advice and just went for it. Managed to get 34 µm first try and will make another run later this week.
- Sweden Gothenburg
June 9, 2021
----
Ed. note: Readers may also be interested in Topic 1148, "Hardcoat vs. regular anodize of aluminum"
Q, A, or Comment on THIS thread -or- Start a NEW Thread