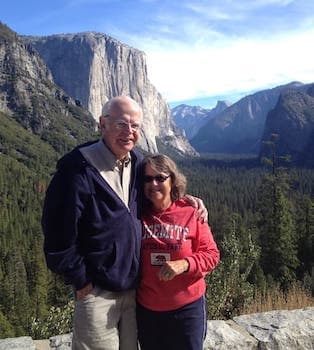
Curated with aloha by
Ted Mooney, P.E. RET
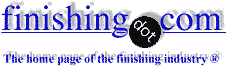
The authoritative public forum
for Metal Finishing 1989-2025
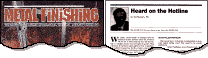
-----
Is oxalic anodizing equal to hardcoat anodizing?
Q. Our company has been evaluating anodizing in oxalic acid for a while. The outcome has been most satisfying this far and we produce a
45 µm coating in 60 min on a 5005 alloy.
Before we can market this method we need to know if its ok to call this method hard anodizing. If we compare a coating produced in oxalic acid and one produced in a standard hard anodizing setup, how good is the oxalic produced coating?
Of course I know that the above questions are dependent of how we preform the anodizing.
aluminum parts - Eksjö, Sweden
2006
A. Your final sentence is your own response. It does not depend on using a certain acid, but rather the conditions (which you didn't mention) which give your final coating its desired attributes. Hard anodizing is generally over 0.001" (25 microns) thick and up to 0.004" or more. It is done at lower temperature and higher acid concentration.
Guillermo MarrufoMonterrey, NL, Mexico
2006
Q. If we compare a "standard" sulfuric acid hard anodizing setup and a "standard" oxalic anodizing setup. Are the coatings produced in oxalic acid comparable with hard anodizing produced in sulfuric acid?
When I type "standard" I mean commonly used.
- Eksjö, Sweden
2006
A. Our industry does not have a clear definition of "hardcoat". Oxalic anodizing IS harder than sulfuric but few people know this. Why don't you call it "harder hardcoat". Indeed our USA Military specification does not address hardness as hardness, they only address abrasion resistance and thickness.
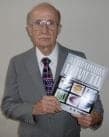
Robert H Probert
Robert H Probert Technical Services

Garner, North Carolina
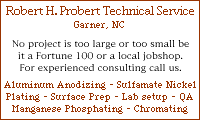
2006
A. I didn't know about the Mil-Std, but I fully agree with Mr. Probert. Hardness itself is a very complex value to measure. More so for porous materials such as anodic coatings. I would think that the more compact the structure, the more resistant to penetration. With this point in mind, the best thing you could do is to measure the abrasion resistance of your own coatings and compare them to your competition.
Guillermo MarrufoMonterrey, NL, Mexico
2006
A. To sell the service, verify compliance with abrasion resistance and other hard anodize requirements. See MIL-A-8625 / MIL-PRF-8625
[⇦ this spec on DLA]F (Type III coatings), BS 5599, DEF STAN 03-26 (cancelled) or ISO 10074. If using the Eloxal GX process, I expect coatings harder than conventional sulfuric anodize (typical: 15% Sulfuric acid @ 20°C, 12 amps/sq ft) but softer than hard anodize (typical: 18% Sulfuric acid @ 0°C, 24-36 amps/sq ft)). Lowering the temperature should improve abrasion resistance. Alert customers of the light bronze to gold color imparted by oxalic acid anodizing.
Please inform us of any test results.
- Goleta, California

Rest in peace, Ken. Thank you for your hard work which the finishing world, and we at finishing.com, continue to benefit from.
2006
Thanks for your answers. I will contact a company who will be able to help me run the tests and get back when I have the results.
- Eksjö, Sweden
2006
March 15, 2013
Q. Dear All,
Can anybody advise regarding surface corrosion after wet test of oxalic hard anodizing?
I run anodizing on Aluminum 6061 series, and thickness requirement is 23 microns.
Control temperature in anodizing is 19 to 22 °C, and cycle time of 74 minutes, sealed with hot seal up to 95 °C.
We don't have difficulty of reaching the thickness but after the wet test the surface is corroded.
Question
1. Is controlling of temperature 19 to 22 degrees in the oxalic anodizing causing the aluminum coating to be very hard and become brittle or crack and result in wet test surface corrosion?
2. How to determine that the coating is hard or soft coating? Is there any measurement? Can anybody advise for simulation test for this issue?
3. Is it related also to the type of jig used and current flow performance?
4. Is the sealing performance not good?
Production supervisor - Batam Riua, Indonesia
Q, A, or Comment on THIS thread -or- Start a NEW Thread