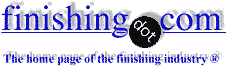
-----
Home anodizing-Truths from the experts?
< Prev. page (You're on the last page of the thread)
Q. Hi all new to this but done a bit of research and come to a dead end there's nothing on what I want to achieve regarding anodising --
I want to anodise and dye dirt bike rims and hubs and nipples
I know the consequences regarding cast hubs but what I do want to know are the following
Can any sheet lead be used as a cathode or is it specialist (I have a roll of 1 mm roofing lead lying around)
Will any car battery do (e.g., 12 V 45 Amp)? Do I need a regulator or anything else?
Would appreciate any advise thanks.
Hobby - England
May 8, 2016
A. 12 V is not high enough. You need 15 - 18 V.
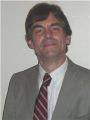
Dave Wichern
Consultant - The Bronx, New York
May 16, 2016
Q. Sorry I have 2x 12 V batteries, so 24 V
Another question: I have mixed 4 liters of 32% battery acid
⇦ on
eBay
or
Amazon [affil links]
to 20 liters distilled water is this correct?
Cheers, tony
- United kingdom
May 21, 2016
A. Hi Tony. It's much too weak. You are looking for 15% by weight, which means that a 1:1 mix of 32% battery acid and distilled water would be quite close.
Regards,
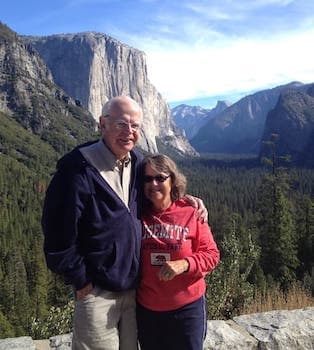
Ted Mooney, P.E. RET
Striving to live Aloha
finishing.com - Pine Beach, New Jersey
Q. Where does all of the conflicting information end? Over the past week or two I think I have read and watched every YouTube video on the subject of Anodizing Aluminum. I have seen everything from a Redneck Brit with a 5 gallon bucket and aluminum foil with a battery charger to some guy talking about the finish on an Ipod. I have tried and failed at coloring Anodized Aluminum of the 6061 and 7075 variety.
I tried the battery charger method using a unit capable of producing up to 60 amps. I'm not sure if the equipment is the issue or not, so I just ordered a bench top power supply from eBay that is adjustable from 0-30 Volts and 0-10 Amps. I just need someone to tell me how to use it.
Here is what I have; in a tub I have mixed 6 Quarts of Sulfuric Acid from an Auto parts store with 1 gallon of distilled water (water first, not the other way around). 2 aluminum sheets 1/4 inch thick 11 inches long and 6 inches wide, hooked to the negative lead. 1 bubble agitator and a cooling system to keep the acid between 70-75 °F. 1 exhaust hood to ventilate fumes outside. Titanium rod threaded into my work piece.
If I have a piece of 6061 that is 3 inches in circumference and 6 inches long (capped off) and I only want to "color" the outside, this should be about 18 square inches. How long should it be left in the tank and at what volts / amps do I set my power supply to? Also, the same questions with a piece that is 60 square inches of 6061.
Thank you in advance for the information.
- Eskridge, Kansas, USA
June 3, 2016
Treatment &
Finishing of
Aluminium and
Its Alloys"
by Wernick, Pinner
& Sheasby
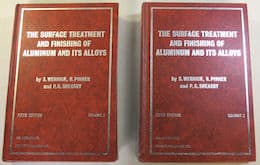
on eBay or Amazon
or AbeBooks
(affil link)
A. Hi David. Nothing wrong with youtube videos, I watch them all the time. But I see conflicting youtube info on the simplest stuff like replacing washers on shower faucets, whereas anodizing is an industrial science with 1500-page textbooks, at least two trade associations / educational associations, annual conferences, and people who have devoted their entire careers to it. Obviously it's tough to condense such a subject into a quick video or a couple of paragraphs of text.
Nevertheless, a good amperage for standard anodizing (as opposed to low current density hobby anodizing) is about 12-18 ASF -- which means 2.25 Amps for your 18 square inch part and 7.5 Amps for your 60 square inch part. At the beginning of the cycle it will take little voltage to generate the 18 ASF; as the anodizing builds and the conductivity of the surface drops, the voltage will climb to 12-15 Volts if you hold 18 ASF.
The 720 Rule will tell you how long to anodize for depending on the thickness you want. It takes 720 Amp-minutes / square foot (or 90 Amp-minutes for an 18 square inch part) to build 0.001" thick anodizing. If you anodize at 12 ASF, that's 60 minutes; at 18 ASF, that's 40 minutes. But 0.001" is pretty thick ... you probably want half of that.
Your acid is probably okay for casual use. How do you know you are not getting any anodizing, or that the material isn't already anodized? And what is happening? What do you see? How much current is flowing? Do you see gas bubbles on the anode and cathodes?
Regards,
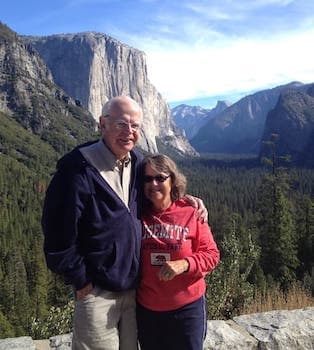
Ted Mooney, P.E. RET
Striving to live Aloha
finishing.com - Pine Beach, New Jersey
June 2016
June 5, 2016
A. Ted's advice is sound, David. One of the things he stated is very important, and that is are you sure the part isn't already anodized (some very thin coatings can be hard to see). A simple continuity test with an ohmmeter can confirm. Touch one lead to your Ti rod, and the other to your part, and see if you have continuity. If not, your piece is coated with something, and that coating needs to come off. You can also use a continuity test to see if you're being successful in your attempts to anodize.
Your power supply sounds adequate for the parts you're trying to coat. If you coat per Ted's advice, in approx 20-25 minutes, you'll have grown approx .0005" of coating, which should be fine for what you're trying to accomplish. Set you're voltage at 30, and your amperage at 0. Turn the unit on, and slowly (around 2 minutes) increase your amperage to the appropriate amount for the work you're trying to coat, in this case, 7.5 amps.
The other thing I noted was your acid concentration. You should be around 15%-20% of acid to water. The way you described your set up, (1 gal of water to 1.5 gal of concentrated acid)is way too strong.
You also mentioned "coloring". That's another step done after the initial oxide is grown. I think home anodizers have had success with RIT dye. And finally, there is a sealing step done, which can be accomplished in your home with boiling water (distilled).
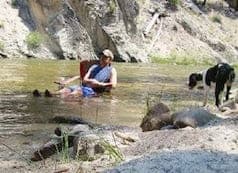
Marc Green
anodizer - Boise, Idaho
June 8, 2016
Q. I now have everything ready for the tubs to the electrolyte mix.
Coated my tub in lead.
2 x 45 Amp 12 V batteries.
I'm going to try and oxidise an 18 inch motorcycle rim
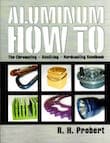
Aluminum How-To
"Chromating - Anodizing - Hardcoating"
by Robert Probert
Also available in Spanish
You'll love this book. Finishing.com has sold almost a thousand copies without a single return request :-)
Are there any books out there that anyone can recommend? Im after anodising and dying items of this size.
Cheers tony
- United kingdom
----
Ed. note: We have a vested interest, but we suggest Robert Probert's "Aluminum How-To" .
DIY Anodizing problems
March 10, 2018Q. Hi all!
First of all this is a wonderful site and community and has been a tremendous help already.
I just have some more specific problems that I haven't been able to find answers to.
I am trying to colour anodize a set of wheel spacers, about 200 mm in diameter and 25 mm thickness.
The alloy doesn't seem to be the best for anodizing, as when I put the spacers in the NaOH solution, they come out almost completely black. To remove this, I dip them in 58% HNO3. This removes the blackness instantaneously, but then some pitting or uneven patchiness can be seen.
I then have made an anodizing bath where I've made a solution of NaHSO4 (the pH is around 2), I have a polished stainless steel flat bar running across the bath and as a cathode I've bent a sheet of aluminum into an L-shape, which covers about 75% of one side and the the bottom of the tank.
I then used aluminum mig-welding wire to tie the spacers and hang them from the stainless bar so that they are completely submerged in a vertical position.
I used an old truck battery charger
⇦ on
eBay or
Amazon [affil links]
running at 24V, positive clamped to the stainless bar and negative to the L-shaped sheet of aluminum. When I switched it on, a lot of fizzing ensued and the ammmeter on the charger showed a current of about 20-23A.
The problems then were:
-the wires, which suspended the parts, kept snapping, regardless of how many strands I made (started with single wire and by the end folded it 3 times to get 8 strands)
-when I finally took the parts out and rinsed them, the were uneven, slightly rainbow-coloured and they didn't really want to take in any dye, only very barely.
What should I be doing differently?
I've read from several sources that the cathode shouldn't be on the bottom, but why? Is this my issue?
I want to redo the parts, so I am thinking of removing the anodizing in the NaOH solution, then sanding and buffing them, then clean and then retry the anodizing.
Thank you!
Hobbyist, Mechanical Engineer - Tallinn, Estonia
March 2018
A. Hi Riido. Starting from the top of your posting --
Professionals use inhibited chemistry for cleaning, not straight NaOH. Try cleaning the parts by scrubbing with powdered pumice and rinsing first, then dipping into your NaOH for just a couple of seconds, using it strictly as a minimal etch, not a cleaner.
I'm personally not familiar with anodizing in sodium bisulphate and would suggest 10% by volume / 15% by weight sulfuric acid instead. You can probably add battery acid about 1 part to 1 part water for this.
I'd try one part at a time instead of all four until you've learned a bit more. I figure they'll draw about 10 Amps each.
Ideally you should have anodes on both sides rather than one side and the bottom, but I don't think that's one of your major problems.
24V is way too much starting voltage; or you need to limited amps; a battery charger isn't very appropriate for anodizing.
Your aluminum mig welding wire isn't cutting it for carrying the amperage. Maybe take some of that excess aluminum anode sheet and try to "wire" up one spacer with it.
The rainbow coloration probably indicates that you have an anodizing layer of partial wavelength thickness, probably about 1/10 to 1/20 of what you need. Good luck.
Regards,
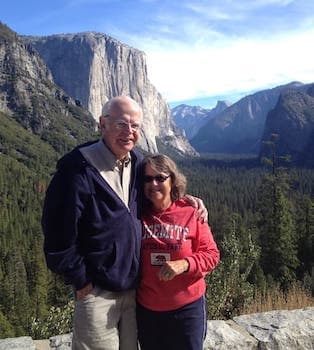
Ted Mooney, P.E. RET
Striving to live Aloha
finishing.com - Pine Beach, New Jersey
Q. Hi, Ted!
Thank you!
What would the appropriate voltage be? The other option for me would be a car battery charger, which charges at around 14.7V.
Is there any good tip on how to attach the anode wire/aluminum strip to the spacer?
Best regards,
Riido
- Tallinn, Estonia
March 13, 2018
A. Hi again. Battery chargers are not great power sources for plating or anodizing. One problem is that raw aluminum is highly conductive (you're even using aluminum wire to carry power to your spacers) but anodized aluminum is highly insulating / very high electrical resistance. Since A = V/R, too much current can flow in the beginning, causing burning, and too little in the end, so the coating never gets thick enough. Ideally you either start with low voltage and ramp it up slowly, or you anodize at constant current. But if you determine the maximum current the charger can put out, and compare it to the 10 Amps per spacer which I estimated, maybe you can get by.
Whether you can practically bend your anode material to make a good connection, I don't really know. But what you could do is go to an electrical store or building supply store and buy the right kind and gauge of aluminum wire. In the USA aluminum wiring is used on service entrances to circuit breaker boxes (but not in house wiring). If it's the same in Estonia, maybe you can find 10-gauge aluminum wire instead of your MIG welding wire. Of course, 8-ga or 6-ga could be used if you can't find 10-gauge. I don't know how you'll avoid "rack marks" where the wire attaches to the spacer, because you need a solid, fixed, connection because otherwise the wire and the spacer will anodize at the connection point and you'll lose contact.
Regards,
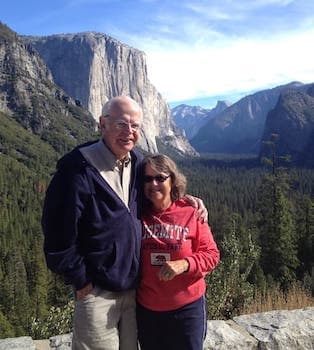
Ted Mooney, P.E. RET
Striving to live Aloha
finishing.com - Pine Beach, New Jersey
March 2018
Rectifier problem in small scale anodizing
Q. Hey guys just finished setting up my anodizing setup, 200 L tanks. I'm having issues with my anodize tank when I turn the rectifier on. I set it to 20 volts. As soon as I submerge the anode, volts drop to almost nothing, amps do come up but from what I can gather volts should also stay up? I tried a small scale setup in a 10 L bucket and same deal. The clip from the positive side bubbles but the aluminium piece doesn't. Any ideas? It's just a 5 amp 30 v rectifier off eBay . I'm using lead as anode and 10% sulfuric acid, DI mix.
Any help would be great!
- australia nsw
April 4, 2019
April 2019
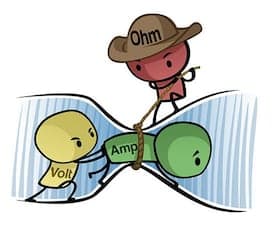
(courtesy of www.build-electronic-circuits.com)
A. Hi Mitchell. You've got a smart rectifier there, which is doing what it's supposed to, lowering the voltage to maintain constant amps so you don't burn the parts when you first start and resistance is close to zero. Although you setting it to 20 volts instead of about 12 volts seems quite a bit too high. What alloy are you anodizing?
The electricity is splitting H2O into hydrogen at the cathode and oxygen at the anode, so you should expect twice as much gassing at the cathode or more. You didn't mention the size of the parts, but if you are trying to anodize at 12 - 18 ASF, then a 5 A rectifier can only anodize a total surface area of about 5/18 to 5/12 of a square foot (counting both sides), say a single piece 5" x 5", so a 200 L tank sounds pretty big.
Regards,
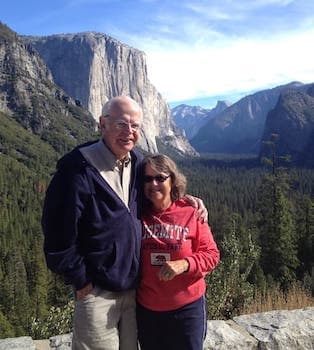
Ted Mooney, P.E. RET
Striving to live Aloha
finishing.com - Pine Beach, New Jersey
A. Mitchell,
Use amps to anodize, not volts. Go with Ted's advice of 15 - 18 ASF. Acid concentration, aluminum content, anode to cathode distance affect resistance which in turn has an effect on voltage for a given current. Set your voltage knob to Max, and control the current to achieve the desired current (density).
Your terminology suggests you may have the polarity reversed. The lead slab is the cathode and the aluminum part is the anode. Positive terminal goes to the anode.
- Green Mountain Falls, Colorado
April 6, 2019
A. Hi Willie. Thanks for catching what I obviously should have caught, that the anode (the aluminum workpiece) should be connected to the positive lead :-)
Regards,
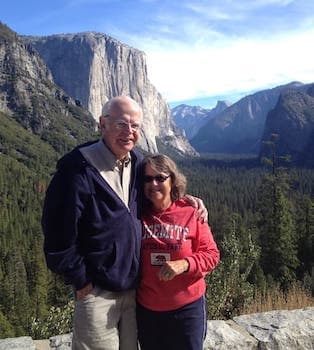
Ted Mooney, P.E. RET
Striving to live Aloha
finishing.com - Pine Beach, New Jersey
April 2019
Q. Hi guys my name is Mark, from Calgary, AB. I wanted to know what the proper method for anodizing 020 aluminum sheets is. All the information I have found so far, relates to aluminum that is much thicker.
Mark Masterson- Calgary, AB Canada
March 18, 2019
A. Hi Mark. Have you successfully anodized thicker materials? Trying to run before you walk might be a mistake :-)
Thin sheets can warp if the anodizing is thick -- topic 44542 addresses a problem with warpage of 0.040 thin wall tubing, and topic 50143 talks about warping of thin sheets. To do any anodizing you must get current to the work and, yes, with thin sheets careful design of multiple contact points will be very necessary; in his October 2, 2018 posting on the latter thread Robert Probert suggests a method of study. Best of luck.
Regards,
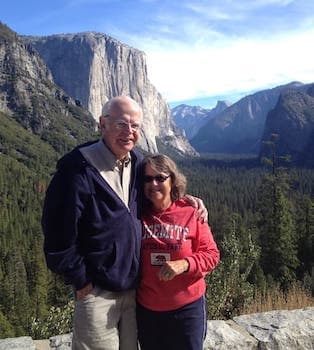
Ted Mooney, P.E. RET
Striving to live Aloha
finishing.com - Pine Beach, New Jersey
April 2019

Q, A, or Comment on THIS thread -or- Start a NEW Thread