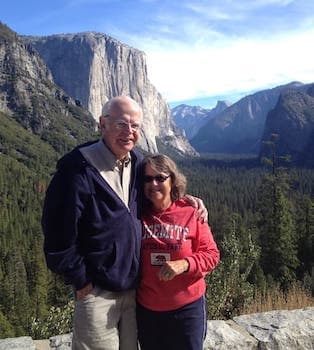
Curated with aloha by
Ted Mooney, P.E. RET
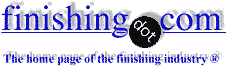
The authoritative public forum
for Metal Finishing 1989-2025
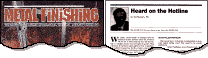
-----
Hard anodizing effecting roundness of my thin wall component
I am currently manufacturing a close tolerance part for an optical application, the roundness callout on the blueprint is .0004" TIR and the dimensional callout is ±.0002".The component is thin wall (.040 in places)
Prior to anodizing I am checking the part dimensions with a Sunnen gauge and a Brown and Sharp CMM and the parts check within the stated tolerances, however after hard anodizing to .001" per surface the roundness goes out to almost .001" TIR and my only option to correct this is to I/D grind this dimension to bring the part back into print.
My question is can anything be done to avoid this from occurring and is it possible that the heat or electrical voltage that is effecting the roundness of the component during the anodizing process.
Please help!
I have already lost 300 components due to this problem!
Metal Machinist - Long Beach, CA, U.S.A
2007
![]() |
If these parts are being racked on the OD/ID, its very possible that may be the cause of your problem. Parts must be firmly racked in the anodizing process in order to maintain good electrical contact, and the pressure on the parts may be distorting them. You might want to check with your coater to see if there's any other way he could rack these parts. ![]() Marc Green anodizer - Boise, Idaho 2007 The first thing that comes to my mind is the pattern of the gas evolution. Because of the tilt on the rack,if the gas goes up one side it will limit the time that the acid and current gets to that side. Give us a picture of the part as racked and maybe we can see what is happening. Is it a disk, tube, of what? ![]() Robert H Probert Robert H Probert Technical Services ![]() Garner, North Carolina ![]() 2007 |
2007
It is possible that residual stresses are being relived during the hardcoat processing. Possible mechanisms are a heat cycle during etch and/or seal, a chill cycle during hardcoat, and a reduction in wall cross section from aluminum consumed by etching and/or hardcoating formation. A normal hardcoat alone will consume 0.002" of wall material. On a 0.040" thick piece that is a 5% reduction. Uneven wall thicknesses with thin sections could lead to distortions.
There are cryogenic treatments which help stabilize the part. They are performed after the rough machining but before the final cut.
Luke Engineering & Mfg. Co. Inc.

Wadsworth, Ohio
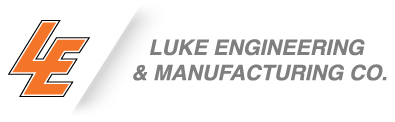
Q, A, or Comment on THIS thread -or- Start a NEW Thread