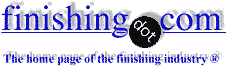
-----
Aluminum Sheetmetal Warping after Anodizing
Q. Hi, I'm a manufacturing engineer for a family run CNC machine shop in Brea, CA. We're having trouble conforming to specifications on this troublesome part, and my local anodizer sent me here to see if any of you could help.
My company has manufactured some parts for a customer from 1/16" thick 6061-T6 plate. The customer requires Type III anodize and a flatness tolerance of .010" The parts range in size from 9" x 11" to 14" x 18". There are a few small (.070") holes along one edge, but other than that they are featureless. We CNC milled the periphery on a vacuum chuck, deburred, finished with an oscillating sander and Scotchbrite 7447 pads and mechanically straightened them to within .005" - .008" flatness. After returning from Type III hard anodize a significant percentage of parts were up to, and some over, .020" flatness. We've been unsuccessful in mechanically straightening most of them. The hard anodize seems to be making the parts spring back, much more so than they did before processing.
I'm looking for help or suggestions on this. Is there a way to get the hard anodize to "relax"? I'm thinking the harder skin is putting some stress on the thin substrate. Would a thermal treatment help, maybe heating, then sandwiching between flat heavy plates to cool? Vibratory stress-relief? Cryo treatment? We're grasping at straws trying to get these parts flat enough for our customer. I realize this might be as much metallurgy related as it is finishing, but perhaps somebody out there has had some experience with what we've encountered here?
Thanks in advance for any help anyone can provide.
CNC Machine Shop - Brea, California, USA
September 29, 2008
A. Your material is a bit thin for the size of the plate to hold 0.010. If you are near the limit before anodizing, it does not seem unusual that it could regain some of the original deflection or memory. A stress relieve cycle would help before it is sent to the anodizer. You could boil them in DI water for a few minutes, cool to room temp and recheck for flatness.
I know that in stainless steel that the removal of the highly stressed outer layer of metal would cause thin material to warp severely. I used to flatten parts that were machined and grit blasted by selective grit blasting.
- Navarre, Florida
October 1, 2008
![]() |
A. My guess ( give it 90% confidence rating! ) is that the parts were compression racked from one side to the opposite and in doing so, in order to assure good electrical contact and prevent burning (especially important on thin 0.062" thin parts), bowed the parts. Once they are hardcoated in the bowed state, they'll likely return to that same bowed state unless something dramatic happens to redistribute the stress - perhaps heat and pressure (but I'd give that ~ 10% confidence). The only sure thing is to strip them, then re-flatten them and have them re-hardcoated. It sounds to me that this might not be possible given that this will likely shrink your part and open holes by 0.001". Hate to be the bearer of bad news but this is reality as I see it. ![]() Milt Stevenson, Jr. Syracuse, New York October 1, 2008 A. Neil - Colorado Springs, Colorado October 2, 2008 A. Getting the current spread evenly on a thin sheet is very difficult. Have your anodizer ramp up slowly over 15 minutes to no more than 24 amps per square foot (later try only 20 ASF), have him make contact in several places - at least 4, preferably 6 or 8. Using an eddy current thickness tester, check the thickness corner to center, if not uniform, then lower the current to 20 ASF and raise the temp from 32 °F to 45 °FF. ![]() Robert H Probert Robert H Probert Technical Services ![]() Garner, North Carolina ![]() October 2, 2008 |
A. 6061 aluminum contains silicon and copper, and small amounts of other alloying constituents. If the etching of the aluminum prior to anodizing is too severe, some of the these constituents are removed. The purpose of the alloy metals is to strengthen and harden the aluminum. Copper and possibly other materials are usually removed using nitric acid, and/or tri-acids. Aluminum is removed in caustic solutions. The removal of these alloying constituents will change the hardness and strength of the item. I suggest that you use a very minimum etching prior to anodizing.
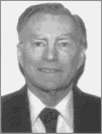
Don Baudrand
Consultant - Poulsbo, Washington
(Don is co-author of "Plating on Plastics" [on Amazon or AbeBooks affil links]
and "Plating ABS Plastics" [on Amazon or eBay or AbeBooks affil links])
October 4, 2008
Gentlemen,
Thank you all very much for your thoughtful replies. I might be out of luck with my current parts, but will take your recommendations to my anodizer for future runs.
Best Regards!
CNC Machine Shop - Brea, California, USA
October 7, 2008
Q. We are doing sheet metal fabrication of aluminium AA5052 H32 sheets. After punching & bending process, the aluminium sheet metal part goes to chromating & powder coating process. After chromating, while curing the part in water dry off oven at 130 °C, the parts get slight bow. After powder coating, while curing at 200 °C, the parts get more bow. We checked the chemical & mechanical properties of aluminium sheet material. We even checked the part by processing chromating & powder coating process from another source. Still we could not sort out what went wrong?
Mahendra KumarNash Industries (I) Pvt Ltd - Bangalore,Karnataka, India
March 24, 2018
A. Hi Mahendra. I would suggest putting a bare unprocessed part in your dry-off oven and then in your curing oven and observing whether there is bowing. If there is not, then Don Baudrand's advice seems applicable.
If you succeed in solving that problem, I would suggest re-evaluating the temperature of your dry-off oven as it seems to be hot enough to destroy the chromate protection. Good luck.
Regards,
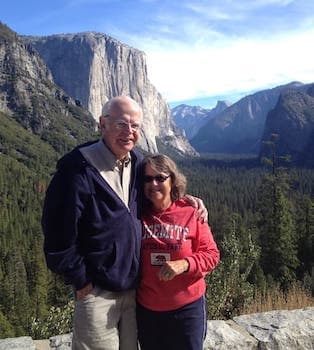
Ted Mooney, P.E. RET
Striving to live Aloha
finishing.com - Pine Beach, New Jersey
March 2018
Q, A, or Comment on THIS thread -or- Start a NEW Thread