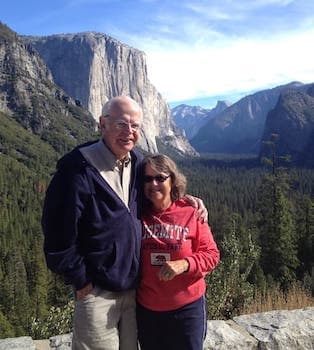
Curated with aloha by
Ted Mooney, P.E. RET
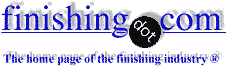
The authoritative public forum
for Metal Finishing 1989-2025
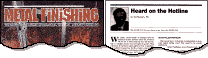
-----
Black oxide formula for Hot Blueing of Guns/Firearms
Q. I want to know the exact composition of the bluing salt used for the bluing of M.S. Also the chemical composition of chemical Degreaser (Alkaline). Also could you guide that some parts developed white powder at many areas after one day of bluing. Could you propose remedy for it?
Thank you,
Tayyab S [last name deleted for privacy by Editor]- Islamabad, Pakistan
2001
A. Hi, Tayyab. Black oxide solutions are essentially composed of sodium hydroxide, sodium nitrite, and sodium nitrate ⇦ this on Amazon [affil link] . Alkaline cleaners are largely sodium hydroxide, but also usually contain sodium silicates, sodium carbonate ⇦ this on eBay or Amazon] , sodium tetraborate, TSP, other sodium phosphates, soaps, and surfactants.
Most plating shops in the West buy proprietary alkaline degreaser processes and black oxide (bluing) processes from specialty suppliers, and the exact compositions of the proprietaries are held as trade secrets which people can't share.
We have an FAQ on Black Oxide and Cold Blackening to introduce the general technology. Beyond that, the Metal Finishing Guidebook goes into more depth about the general technology.
Regarding the white powder, please see thread 13097 "Black Oxide Problem". Good luck.
Regards,
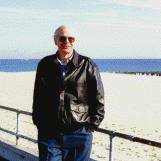
Ted Mooney, P.E.
Striving to live Aloha
finishing.com - Pine Beach, New Jersey
Q. What is the correct formula of hot caustic bluing for making up a bluing bath for refinishing guns, and can we regenerate the bath again and again , and how can we extend the life of the bath, as I am making the bath in the following manner:
caustic soda ⇦liquid caustic soda in bulk on
Amazon [affil link]
10 kg
sodium nitrate 10 kg
water 10 liters.
The bath forms red cast on the parts which is easily rubbed off but the bath lasts only an hour or so -- please advise.
firearms - Patiala, Punjab, India
2005
A. Hi Inderjeet,
Forget about your formula search and buy the correct ready-made product from any reputed company in your country.
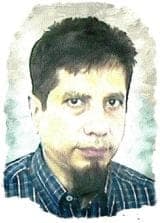
Khozem Vahaanwala
Saify Ind

Bengaluru, Karnataka, India
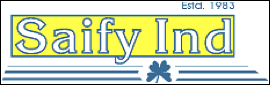
Multiple threads merged: please forgive chronology errors and repetition 🙂
Q. Hi, I am on the look out for bluing chemicals, details of chemical composition, process, suppliers and pricing details on polished steel parts. The process is hot bluing, on heat treated components.
Regards,
Rishabh Kapoor- Delhi, India
2002
Q. What is the formula for gun bluing hot caustic blueing for home-made. I want to blue my gun. It is old and has rust.
Thanks.
- Quito, Ecuador
2006
Q. Does anybody know the formula for the black oxide process? Concentration, chemicals used, procedure? Thanks.
Daniel Hernandezplating shop owner - Bucaramanga, Colombia
2007
A. Black oxide formula: 600 gm sodium hydroxide, 25 gm sodium nitrite, boiling solution, immersion 10-30 min, rinse well; it must be oiled, waxed or lacquered.
Use rubber gloves
⇦ this on
eBay or
Amazon [affil links] , protective clothing and goggles
⇦ this on
eBay or
Amazon [affil links] !
Hope it helps and good luck!
600 gm NaOH, 25 gm nitrite and 1 lit water!
Goran Budija- Cerovski vrh Croatia
2007
Thanks,
It works. Thank you very much
plating shop owner - Bucaramanga, Colombia
2007
Why don't gun shops know hot gun bluing?
Q. Dear sirs:
I have been to many "gun" sites and could not find a formula for "hot" gun blueing. I have found your recipe to be very interesting. Why couldn't I find it elsewhere?
Eric P [last name deleted for privacy by Editor]- Philadelphia, Pennsylvania
2001
A. Hi, Eric. I'm not sure, but possibly two reasons: first, many of our readers are professionals so they frequently reference and quote the metal finishing textbooks whereas your average gun enthusiast probably wouldn't; second, hot bluing is a dangerous operation that should probably only be practiced in a proper industrial setting, not in a back room of a retail store. Best of luck.
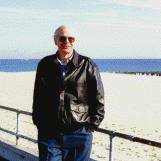
Ted Mooney, P.E.
Striving to live Aloha
finishing.com - Pine Beach, New Jersey
A. Eric,
You can try "gunsmith supplies" search and probably find instructions and bluing compounds. The modern bluing solutions are very good and it probably wouldn't be worth trying to make your own. As was said, hot bluing is not a back room project. The solution I use is a caustic soda ⇦liquid caustic soda in bulk on Amazon [affil link] solution heated to 300 °F. It will eat thru leather, wool, skin, etc., and will cause chemical and heat burns. The fumes will deteriorate any metal in the area, so a very good ventilation system is required. Personal protection is a high priority.
Good luck,
Ed Kay- St. Louis, Missouri
A. Hi Eric,
I have an old engineering book "Dictionary of Metals and Alloys" 1939, which describes the HOT BLUEING process very well and safely and I have used it with good success.
Thoroughly clean the articles in ammonium sulfide, and hydrochloric acid for a "few" minutes" will lightly etch the surface and create a light rusted effect which will improve the depth and darkness of the finished result.
Coslettising bath of a heaped desert spoon of phosphate of iron to a liter of water which needs a few drops of phosphoric acid to dissolve into solution ... boil the articles for 1/2 an hour or more ... longer produces deeper penetration to a small extent ... leave to dry overnight and oil.
Granodising is an electrolytic process using a solution of zinc phosphate acidified with phosphoric acid and passing a light current from the negative cathode (the article) to a carbon anode. Articles acquire a dense black coating which is highly resistant to oxidising ... can be applied to zinc, cadmium, iron steel, stainless steels and copper/brasses etc
Carver - New Zealand
June 5, 2008
Why is bluing too dull to match rest of gun?
Q. Hello, I have a pre war model-70 Winchester. I just had the floor plate, trigger guard & screws blued. however they are too dull to match the rest of the gun. Can these parts be polished by me to bring out more luster to match the rest of the gun? thanks,
Bruce M Hissomretired - Star Junction, Pennsylvania
2007
A. Hi Bruce. The coating is too thin to polish. The bluing can be waxed or oiled to bring out a bit more luster, but I suspect what really needs to be done is to polish the bare metal and re-blue it. The exact same black oxiding compound that generates a jewel-like navy blue on a highly polished part produces a matte black on a rough part :-)
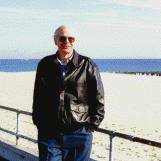
Ted Mooney, P.E.
Striving to live Aloha
finishing.com - Pine Beach, New Jersey
Inconsistent results: Bluing doesn't work on all parts
Q. I have tried my hand at Hot Caustic Blueing. I have a couple of problems I need assistance with. I have several parts that did not blue. Several that did. One that looks like it has freckles on parts of it. I thought all parts were the same type of steel. They all draw to a magnet. My frame did not blue at all. My slide blued to a good color but has freckles at edges. They were in caustic bath at same time. Some of my small parts also blued and some didn't. They to were also in caustic bath at same time. Any Ideas? Thanks Skip
Skip KalmarHobbyist, maybe One day gun smith - Heath Ohio
December 11, 2009
A. Hi Skip,
Since it didn't look like you ever received a response, I thought I'd throw in my 2 cents.
Stainless used in guns is 400 series and magnetic. It will not blue in ordinary salts. There are salts available for stainless. Some alloys work and some don't.
It's always advisable to try to blue a matte finish vs. a polished finish. Polishing stainless is almost always a guaranteed failure.
Speckles on edges are indicative of poor cleaning. When the part goes into the solution, if there is any floating oil, the part will pick them up and it acts like a mask and the salts won't penetrate it.
Hardened parts, castings, will leave a red to purple tint and again, the courser the finish, such as matte, will offer a greater chance of a darker blue.
Hope this helps!
precision bluing - Greene, New York, USA
December 2, 2010
Q. Please give me a proper hot procedure. I am using ms tank.
gosai jaydipheat engineering works - Surat, Gujarat, India
April 20, 2014
A. Hi Gosai. Many plating texts will offer this general information. For example, The Metal Finishing Guidebook suggests:
8 lb. caustic soda ⇦liquid caustic soda in bulk on
Amazon [affil link]
,
1-1/2 oz. sodium nitrite, and
1-1/2 oz sodium dichromate
... to 1 gal. of water, operated at a boiling point of about 295 °F. Goran has offered a rather similar formulation.
But personally, I believe Khozem and others have offered better advice, i.e., to go to a reputable supplier of blackening salts who will supply proper salts with quality control, a technical data sheet on how to use them, a technical service person who will know what they are looking at and how to troubleshoot any issues, and an experienced lab when trouble develops. Professionals with decades of experience in this, like Khozem, feel that they are better off buying the product than trying to formulate it themselves, so people with less experience should probably heed their advice :-)
As you read these pages you'll find that the potential troubles abound, and if you don't know from long experience whether the problem is in the bath formulation, or the operation, or defects in the substrates, or improper cleaning, or wrong expectations, or whatever, it can be very difficult to function efficiently. Using proprietary solutions can cut the problem down to size. Best of luck.
Regards,
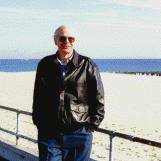
Ted Mooney, P.E.
Striving to live Aloha
finishing.com - Pine Beach, New Jersey
Q. We are doing Hot Black Oxidising on High Tensile Fasteners. We use Caustic, Sodium Nitrate and Sodium Nitrite in the ratio of 80:10:10. Can anybody guide what are the characteristics or the function of each chemical in this?
Regards
Chintan
- Bhavnagar, Gujarat, India
June 1, 2014
Q. Same chemicals were used by me but the coat is very thin and easily removable by scratching with steel wool.
Durai vignesh- Chennai. Tamilnadu .india
April 23, 2017
A. Hi Durai. Yes, the coating is almost unmeasurably thin and that is what I would expect. But at least use 0000 #0000 steel wool ⇦ this on eBay or Amazon [affil links] if you are trying to minimize the removal. Good luck.
Regards,
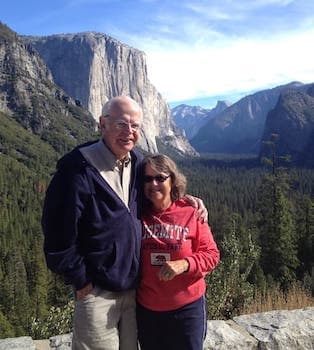
Ted Mooney, P.E. RET
Striving to live Aloha
finishing.com - Pine Beach, New Jersey
A. Durai -
Black oxide is not very hard, and it is not very thick.
Steel wool will remove it.
The answer is: steel wool and black oxide are not compatible. Ever.
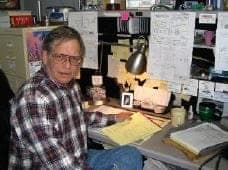
Jeffrey Holmes, CEF
Spartanburg, South Carolina
Q. Respected sir, what should I do in order to reduce the intensity of concentration of drained water used for black oxide process?
Which method should I adopt for blackening (hot or cold)?
Suggest some best chemicals for blackening process amongst daily used chemicals.
- Maharashtra, India
September 12, 2017
A. Hi Shital. With regard to effluent treatment from the black oxide finishing line, neutralization with acid followed by clarification is the normal course. But here in the USA, waste water treatment is not something done casually with internet advice, but is addressed by retaining experienced professional engineers.
What exactly do you want to apply black oxide to and why? Certainly hot black oxide is the superior finish, but many components are done with the selenium-based cold blackening.
Inderjit, Goran, and myself have already suggested formulations for the hot black oxide process, whereas Khozem and others have urged you to buy a proven formulation rather than trying to get by with commodity chemicals. Good luck.
Regards,
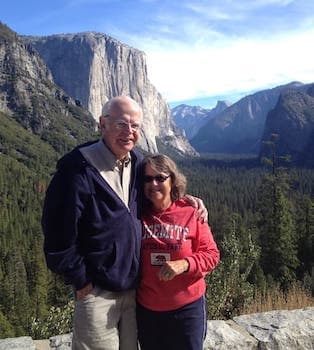
Ted Mooney, P.E. RET
Striving to live Aloha
finishing.com - Pine Beach, New Jersey
Black oxide came out brown
Q. Thanks all for the useful information, I followed the process of blueing (600 gm Sodium hydroxide + 25 gm sodium nitrate + 1 L water)
The first batch turned to black color BUT the second one turned to brown color !!
I do not know the reason ... please advise.
Screw manufacturer - Cairo, Egypt.
November 5, 2018
A. Hi Mohamed. I'd credit it to beginner's luck with the first batch I guess :-)
Seriously, a guess is that some of the water evaporated, rendering a more concentrated solution which boils at too high a temperature, giving a mix of red and black. But some folks have spent their entire careers learning to do consistent blueing/black oxiding. You would need to tell them the type of metal, the operating temperature, and a lot else ... and even then I doubt that anyone will promise a robust and consistent black without experience and a proprietary process.
You haven't introduced yourself, so we must warn you that although this forum can often help answer specific questions, it cannot serve as basic training. Hot black oxide processes are very dangerous; eruptions have killed a number of people. I hope you fully understand how to add water safely, and that your operators are wearing head-to-toe protective gear. Good luck!
Regards,
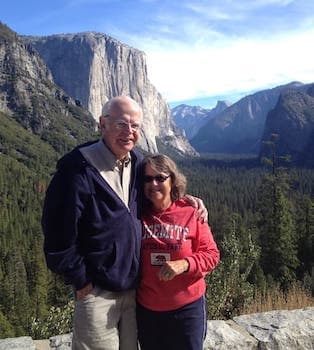
Ted Mooney, P.E. RET
Striving to live Aloha
finishing.com - Pine Beach, New Jersey
Black Oxide coating for steel
Q. How to formulate a Black Oxide solution for golf clubs
A T Leerestorer - Singapore
January 28, 2019
Q. In hot bluing method, how to preserve the strong alkali solution after use? And can the solution be reused for bluing again? I personally tried hot bluing process it gives satisfying results but after some days I tried the same solution from previous bluing but this time it did nothing. One more thing Can you please tell me the exact ratio of ingredients?
Dark Light- Lahore, Pakistan
April 24, 2019
A. Hi Dark. What formulation did you use that gave satisfying results initially? Hot bluing is better suited to regular use than to occasional use because it is dangerous, expensive, and difficult to heat it up to process a single part. I don't think anyone bottles it up for next time; rather, they always leave it in the tank.
We appended your inquiry to a thread where several knowledgable people suggested buying a formulation rather than trying to mix it yourself if possible; but several formulas are printed on the page if need be. Good luck.
Regards,
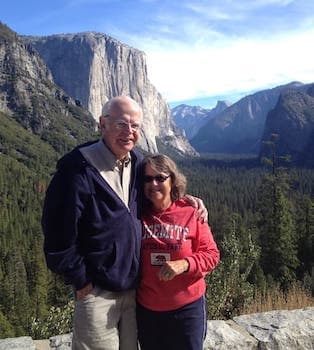
Ted Mooney, P.E. RET
Striving to live Aloha
finishing.com - Pine Beach, New Jersey
A. HOT BLUING TIP- For the DIY person hobbyist, who can afford to wait a view hours, one can operate a caustic hot blue bath at much lower temperature than the typical 285 to 300 °F - and gain a significant safety factor. Because the blueing process is a chemical temperature dependent reaction, if you lower the temp to around 220F and place the blackening salts bath in an oven overnight, very good results are obtained. In practice the objects are placed in a glass tray inside of an oven baking bag - to minimize evaporation. At this lower temperature the sodium hydroxide will not etch the glass significantly, or the water evaporate. It is well known that hot concentrated NaOH etches glass containers. Furthermore the cooled blackening salts can be stored in closed glass containers indefinitely - for occasional use.
Jerry Quigg- Chandler,AZ -USA
May 12, 2019
Great posting, Jerry. I'm happy to be corrected.
Regards,
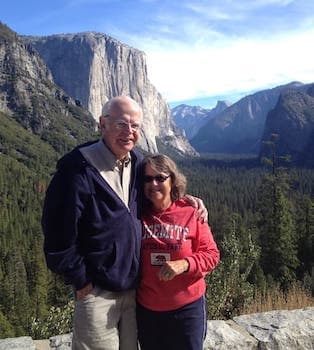
Ted Mooney, P.E. RET
Striving to live Aloha
finishing.com - Pine Beach, New Jersey
Black oxide process works on some ferrous materials but not all
Q. My bluing tank works well but sometimes some ferrous material are very stubborn to respond to the bath despite that these materials are well degreased and very well cleaned with gasoline. Can you please help me.
Ibraham hasani- Jeddah, saudi Arabia
May 24, 2019
A. Hi Ibraham. It's really best when you know exactly what ferrous metal you are processing so you can start applying your prior experience towards tweaking the operation to best accommodate it. If it's stainless, for example, your standard black oxide process is unlikely to oxidize it.
In topic 55621, gunsmith Rod Henrickson explains how some steels, especially high nickel steels, resist black oxide.
Gasoline is too dangerous for use inside, and that step should be abandoned! You should alkaline clean, rinse, acid pickle, rinse, black oxide, rinse, and boil out. Good luck.
Regards,
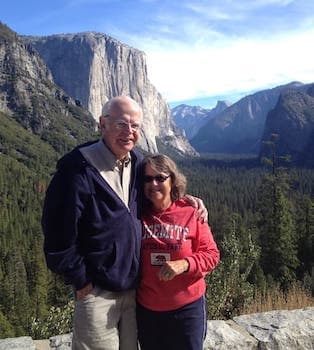
Ted Mooney, P.E. RET
Striving to live Aloha
finishing.com - Pine Beach, New Jersey
Q. Thanks for your flash response to my problem. I have already blued 2 ak magazines. I went through the same steps of pretreatment above. Both magazines are twins, they belong to the same manufacturer. One magazine was blued very well but the other is very ashy despite the fact that both magazines went through the same treatment. This drives me crazy.
Ibraham hasani [returning]- Jeddah, saudi Arabia
A. Hi again. It is often said that 90% of metal finishing problems are due to poor cleaning. Although that's probably an exaggeration, when you have identical parts processed identically at the same time, and one is good while the other is not, it certainly becomes a possibility that the cleaning process is marginal and was just good enough for the one part but not robust enough for the other. Double check your cleaning.
Regards,
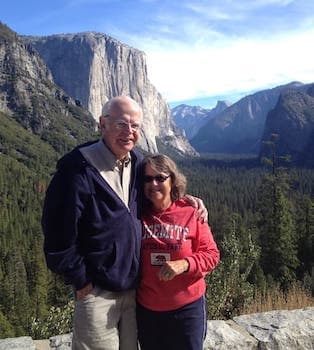
Ted Mooney, P.E. RET
Striving to live Aloha
finishing.com - Pine Beach, New Jersey
Q. Hi again. Due to the cleaning process I'm sure 100 percent that the work piece is fully cleaned and degreased. You have pointed out acid pickling. I think it is an important step. It also helps to activate the surfaces. But I'm ignorant about this particular step. Can you please explain this step in details. Best regards,
Ibraham hasani [returning]- Jeddah, saudi Arabia
A. Hi Ibraham. There are 101 ways to do everything in metal finishing, and some people do acid pickling, followed by a rinse, followed by 'activation', followed by a rinse before black oxide ... but the black oxide lines that I'm familiar with simply had a combination pickle/acid activate consisting of room temperature HCl at a concentration of maybe 15-20% and a rinse.
Regards,
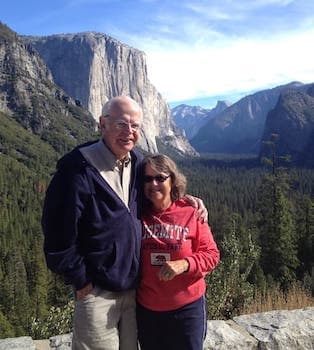
Ted Mooney, P.E. RET
Striving to live Aloha
finishing.com - Pine Beach, New Jersey
Q. Nice; I already have HCl. How long do you suggest for the work piece to be soaked in?
Ibraham hasani [returning]- Jeddah, saudi Arabia
A. Hi Ibraham. Such things vary, so all I can give you is the planning info that it probably will be between about 20 seconds and 90 seconds based on my recollection of what I've seen. Good luck.
Regards,
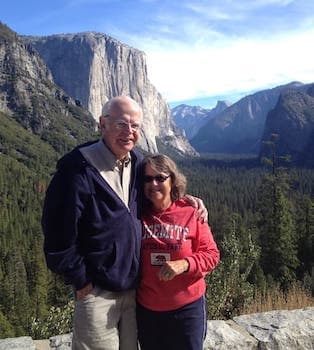
Ted Mooney, P.E. RET
Striving to live Aloha
finishing.com - Pine Beach, New Jersey
Thanks Ted you are my best friend and my hero as well!
- Jeddah, saudi Arabia
Let's see if it actually helps first :-)
Regards,
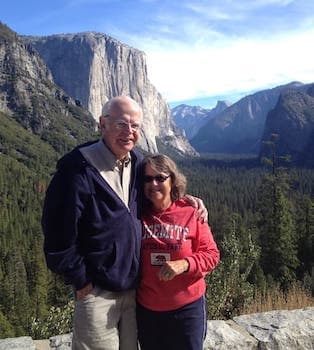
Ted Mooney, P.E. RET
Striving to live Aloha
finishing.com - Pine Beach, New Jersey
Q. Hi again I have dissolved a new bath using the same ratio before 600 mg sodium hydroxide and 30 gm sodium nitrite. All previous problems that I've been suffering were solved. I've reached very professional result. Here are rising questions
1- was the previous bath contaminated despite I was spending so much time cleaning work pieces?
2- is there any kind of maintenance that should be taken into consideration regarding the new bath?
3- is there a time life for the bath?
- Jeddah, saudi Arabia
June 7, 2019
A. How frequently are you desludging currently? There is actually quite a bit of maintenance required to keep a hot black oxide bath running optimally, but the bath should have a very long bath life if cared for.
Regular desludging based off your through-put and a proper desludging process to ensure you just take out the junk and not the oxidizers/rectifiers are key. As far as contamination, you are running a home brew so you don't have a built in recitifer to handle small metallic contamination. This will come from your alloys so its hard to comment on its potential effects. How is your rinsing now? Any soap or oil that you drag down the line can contaminate the bath, and any acid drag in will neutralize it and waste chemistry. Do you have any iridescence on your rinse tanks currently?
As far as your recent issues, how well can you control the temperature/heat distribution in your tank? I don't know how you're heating now or what your boil looks like but temperature stratification is a common black oxide issue. Did you process the parts at the same time or back to back? Can you control the temp within 2 degrees for the entire process time? The deep black color is achieved in a small temperature window and you can see varying appearance if you drift at all.
Do you have any pictures? "Ashy" isn't giving me a good idea of the issue you're seeing. Is it light in color, does it have some rub-off, or is it both?
- Agawam, Massachusetts USA
Q. We have been using a commercially available black oxide mix. Kind of expensive at $130 a bucket + $40 shipping. 1 bucket does about 4 tanks and works on stainless. Can only seem to get one batch of parts at a time from each tank. We mix 4 lbs of salts to 1 gallon of water and look for boiling at 240 °F. Our stuff seems to like 250-260 °F to turn parts black. We are doing rifle barrels and other misc. steel and stainless parts. The bucket we receive for $140 seems to be rebranded. I have to believe that I can find the same chemicals at a considerably lower price if I can find the manufacturer. Anyone suggest where to start searching?
Bob Dicerson- Southern California
October 26, 2019
A. Hi Bob.
We can't compare or source products in this forum (why?) but you might try EPI / Electrochemical Products Inc. [a finishing.com supporting advertiser] as they are a manufacturer rather than a re-packager, and they will have distributors who can probably supply you by the bucket if your needs are not great enough for minimum orders from a manufacturer. Good luck.
Regards,
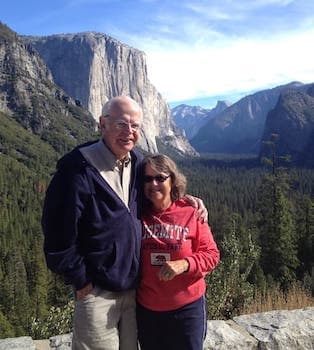
Ted Mooney, P.E. RET
Striving to live Aloha
finishing.com - Pine Beach, New Jersey
Tip: Readers want to learn from Your Situation 🙂
(little can be learned from abstract questions, so many readers skip them)
Q. How to obtain a peacock blue finish on the gun metal?
Saabi singh- Amritsar, Punjab, India
March 1, 2020
Q. Can you please suggest the ready made solution for blueing? We produce Iron Belt buckles with german silver over them and need to brown/blacken the Iron surface to give it a rust iron look.
Arif khanManufacturer - Kanpur UP
December 9, 2021
Ed. note: This RFQ is outdated, but technical replies are welcome, and readers are encouraged to post their own RFQs. But no public commercial suggestions please ( huh? why?).
A. Hi Arif. You can google for "black oxide" or "blackodize"; most general metal finishing suppliers and distributors will have such a process among their offerings. But just so you don't waste time moving in the wrong direction, you should know that black oxide/bluing attempts to give a uniform very dark coloring to iron (black if on a matte surface, deep jewel blue if on a highly polished surface). That doesn't sound like what you are trying to do with your "rust iron look". It sounds to me like you are looking for a "rust patina" -- if so, you might find topic 30522, "Clear coating to seal a rust patina finish on metal", helpful.
Luck & Regards,
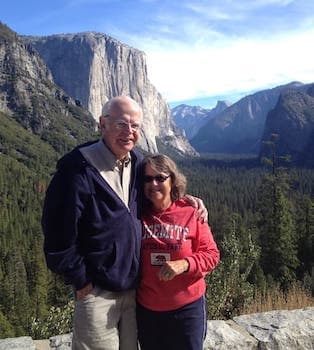
Ted Mooney, P.E. RET
Striving to live Aloha
finishing.com - Pine Beach, New Jersey
Tip: Readers want to learn from Your Situation 🙂
(little can be learned from abstract questions, so many readers skip them)
Q. How frequently do we have to change the bath for different salts in cold black oxide coating?
Madhven Rathodstudent - Mumbai, India
April 5, 2023
Q, A, or Comment on THIS thread -or- Start a NEW Thread