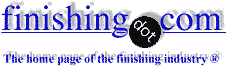
-----
Black Oxide process problems
Q. We use a blackening solution that runs at 126 °C. Our clientele is becoming more and more optics orientated and for obvious reasons the parts need to be dust and residue free (our processed parts seem to have a lot of dust on them once dried).
Normally we would rinse with water, dry, oil, clean in soapy solution, rinse and wipe clean. This seems quite a lengthy and vigorous process and is not good for very small components. Does anybody know of a process that is efficient at removing the dust without having to wipe individual parts please?
Finishing Manager - Cambridge, England
July 27, 2022
A. Hi Alex. This may not be totally responsive to your question, but is at least tangential ...
I had a friend/plater who worked with me on several consulting projects a couple of decades back and then went to work at a shop and eventually opened a shop himself. Wherever we/he worked, he seemed fond of trying to implement the concept of casual semi-cleanroom environments. While electronic grade cleanrooms are very expensive with their downdraft floor-sweeping ventilation, HEPA filtration, and rigid protocols, simply reducing dirt and dust even by as much as an order of magnitude usually isn't really all that hard. It just requires asking yourself where all that dust & dirt is coming from, looking around, and addressing targets which look both simple and cheap to address :-)
Luck & Regards,
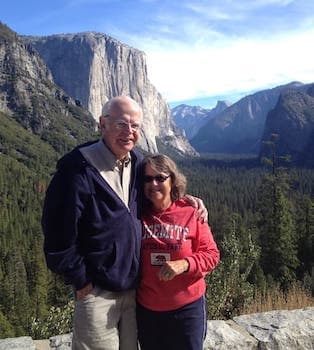
Ted Mooney, P.E. RET
Striving to live Aloha
finishing.com - Pine Beach, New Jersey
August 26, 2022
Q. Hello -
Having some issues with cold blackening of 304 SS.
We are experienced metal finishers and fabricators with steel and bronze, but less familiar with proper procedures of blackened stainless.
We are using Birchwood Casey SSB and have a fairly thorough process figured out.
However, some parts over time (3-5 months) seem to develop a 'bluish' hue (under the lacquer). This seems to be accelerated (but not exclusively) by direct sun (UV) exposure.
Other parts don't seem to change.
Some of the material we are starting with is 1/8" 2B finish, also a lot of 1/4" CMP.
Any help or insight would be much appreciated.
RFQ: We would be happy to hire a qualified consultant if this is something they have experienced before or are familiar with.
We are desperately trying to understand what is happening.
Thanks is advance,
Sam
- Northampton, Massachusetts
privately respond to this RFQ
Ed. note: As always, gentle readers: technical replies in public and commercial replies in private please (huh? why?)
A. Hi Sam. Although it was on a hot black line, not a cold blackening line, and for steel not stainless, I have seen mirror polished parts come out jewel blue while rougher parts come out dark black from the same processing line at the same time. If the fading to blue seems otherwise random, you might consider whether the parts which turn blue are more highly polished.
Luck & Regards,
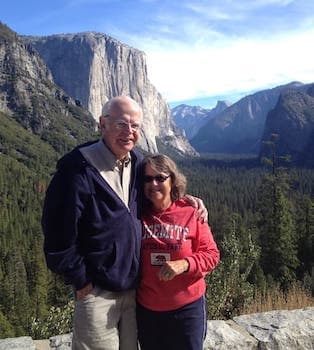
Ted Mooney, P.E. RET
Striving to live Aloha
finishing.com - Pine Beach, New Jersey
⇩ Related postings, oldest first ⇩
Q. We have a customer that has their parts black oxided by an outside source. The parts come back to their plant after black oxiding and are then dipped in a mineral spirits based rust preventive (after removal of the oil applied by the black oxider). The parts are then packaged in boxes with VCI paper for storage/shipment.
The problem is that the many of the parts have a visible white residue after being in storage. We suspect that the problem is due to incomplete rinsing of the caustic solution from the black oxider. Is this likely and if so how can this be verified?
Curtis Seichter- Oak Park, Michigan
2002
A. The caustic black oxide solution is not actually corrosive to steel as far as I know, and I suppose as you do that the white stuff is improperly rinsed caustic. Corrosion products would typically be red rust.
The black oxide & oil parts should exhibit some resistance to corrosion, so to me the question is why remove the oil?
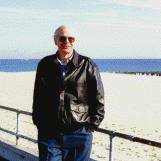
Ted Mooney, P.E.
Striving to live Aloha
finishing.com - Pine Beach, New Jersey
2002
P.S. March 28, 2009: Rod Henrickson's answer below is much better than mine was.
A. First, it may be whatever is being utilized to remove the soluble oil from the black oxide, leaving a residual film before mineral spirits is applied. Second, why not have the black oxider apply this material instead of removing the oil?
Bill Hemptech svc. w/ chemical supplier - Grand Rapids, Michigan
A. Curtis, you could confirm the source of the white residue by carefully scraping some of it off the parts and analyzing it. If the residue is sodium or potassium salts, it is likely that it came from the black oxide process.
Another possibility is it may be from the rust preventative oil applied over the black oxide. Many rust preventative oils contain calcium based materials. If you are using solvent to remove the oil, the calcium based materials will be left on the surface of the parts. Without the other ingredients that were present in the original oil, the calcium materials migrate to the surface and form the white residue.
A third possible source is from your cleaning step. In the above scenario, I have assume you are using solvent to clean the original oil off the parts. If you are using an aqueous cleaner, the white residue could be salts from the cleaner.
From the outside looking in, you may be able to solve the residue problem and simplify your process by getting the shop that applies the black oxide to apply the oil you use to the parts instead of the oil they currently use. That would safe you the cleaning and reoil steps. Hopefully, I have given you some things to think about.
Roy NussTrevose, Pennsylvania, USA
A. Very simple answer to your question. I have the same problem when I am bluing firearms and it is close to quitting time. Like cockroaches, bluing salts literally find their way into every nook & cranny. Dang stuff is insidious and will hide in the darndest places and wait until the customer has picked up his part or gun and will then wait another three weeks before quietly creeping out over the metal surface. When the guy brings it back in he is generally freaking out as he has already found that no amount of oil will stop it.
Whose fault is it? Well it's the fault of the guy that blued the parts. All parts that are caustic blued MUST be boiled out for at least a half hour after they come out of the bluing solution. If the parts have nooks and crannies the solution will hide there. If the parts have been sand blasted the danged stuff will hide in the bottoms of the tiny craters the sand blasting creates. Forget oil! Bluing salts are made from sodium nitrate
⇦ on
Amazon [affil link]
or ammonium nitrate if you can stand the smell and sodium hydroxide. None of these chemicals are oil soluble. Bluing salts will crawl out of a hole and walk over an oiled surface like a baby crawling across the living room rug.
Crawling salts are simple to spot. They can appear as a light snow on the surface or an ugly white mould spot that just keeps growing. It can also take on a light bluish tinge if the chemicals happen to be new. The only way to avoid it is to boil the parts in fresh water for thirty minutes after bluing and then oil or wax everything down. Waxing is the best that I have found. Keep a separate hot water tank and toss a cup of any paste floor wax in it. The wax will melt and float on top. Dip the part in and out several times and then rinse with cold water and dry. The wax will fill the nooks and crannies. After this apply some light gun oil. Don't worry about the part rusting in the boil out tank. As long as it is under water it won't rust in the thirty minutes it is in there. When you take it out of the tank then you can start to worry as rust will form in less than 15 minutes. Go straight from the boil out tank to the wax tank or get oil on it right away.
Some people add water soluble oil to their boil out tanks. Does that really help? Well, I have tried 101 different hangover cures and short of getting drunk again they never seemed to work either. I suppose if you believe water soluble oil helps, far be it from me to tell you anything different. Rod

Rod Henrickson
- Edmonton Alberta Canada
March 28, 2009
Q. Hello Rod, would this process (post process boiling and waxing) be the same for the black oxide process, and if so what wax do you recommend as I am having a hard time finding a water soluble floor wax? Thank you for your time.
John Taylor- Evansville, Indiana
September 6, 2022
A. Hi John. Rod's posting was from 13 years ago so I don't know if he'll return to answer you, but suppliers to the metal finishing industry like Heatbath (DuBois) offer waxes designed/formulated for this specific purpose.
Luck & Regards,
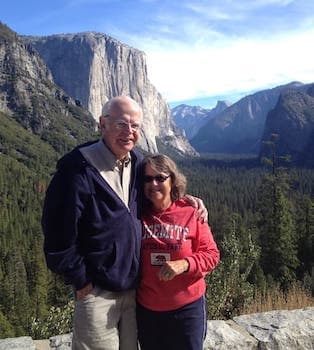
Ted Mooney, P.E. RET
Striving to live Aloha
finishing.com - Pine Beach, New Jersey
Q. I have the same problem, why I should remove the black oxide is because of coating purpose. I think, the black oxide that we receive from customer is to protect their fastener from corrosion while it is on board for export. That why we receive a black oxide fasteners and I have to remove it for coating purpose. The problem is what is the suitable chemical to remove the black oxide and what is black oxide content?
John Gerry- Japan
2006
Q. I am facing a similar problem in my work as well.
I need to remove the oil from the black oxide for secondary work to be done on the metal.
Hence, I would like to know if the "de-oiled" metal, with just the black oxide coating, is sufficient for rust prevention under normal indoor environment?
Also, what is the most suitable method of removing the oil from the black oxide? and what solvent should I use?
Hope to get a reply soon! Thank you!
Procurement - Singapore
June 2, 2008
A. Hi, Jay. In my estimation it will not work. I have been to firearms factories where they remove the oil from blued (black oxided) guns for certain rework, and often suffer flash rusting within a few hours. It is only my opinion but I believe the idea of an oil and wax-free black oxide finish is doomed to failure.
Regards,
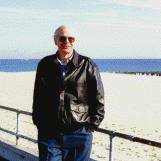
Ted Mooney, P.E.
Striving to live Aloha
finishing.com - Pine Beach, New Jersey
June 2, 2008
A. Dear Friends:
To Remove any black oxide coating, as they applied oil on them, you should first degrease the parts in "Hot Degreasing" materials or use some solvent base degreasing material, then after rinsing, dip the parts in HCl base mild acid solution (20% for e.g.) plus corrosion inhibitors at room temp. And then you can see that all the black coating will be vanished in a second. But if the coating did not change, then the parts have been blackened by Cold Black Oxide material, (Selenium salts base)and the only safe way to remove the coating is mechanical rubbing or blasting (sand or glass). To prevent rusting before the second process you can use anti-oxidants in your last rinsing process at the rate of 3-5% (check with the producer).
Good Luck
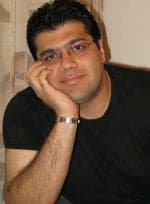
Alireza Reyhan
- Istanbul, Turkey
January 10, 2013
Q. I have a large piece of equipment, the support structure of which was treated with black oxide. During shipment the packaging was damaged and the structure was exposed to several hours of rain, which has caused the structure to slowly bleed a white liquid (I am assuming a caustic salt solution). As this has been going on for several weeks, we are considering disassembling the structure, stripping the finish, and painting it. Since this method is highly disruptive to schedule and surrounding equipment, is there a more practical way to treat and stop the leaching of the affected parts without stripping the finish and disassembling the structure?
Liza Oleynik- LaGrange, Georgia, USA
January 29, 2013
A. Hi Liza. We appended your question to a similar earlier thread where Rod Henrickson has offered his knowledgable answer. However, black oxide is not corrosion resistant (although the oil or wax might have been sufficient if it hadn't got wet). Once it has been in the rain for several hours, I don't think you'll get it back to right, and your plan of dissembling and painting it is probably the most practical approach.
Regards,
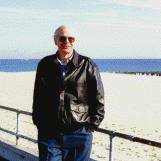
Ted Mooney, P.E.
Striving to live Aloha
finishing.com - Pine Beach, New Jersey
January 31, 2013
A. Dear Liza:
Sometimes the oils used as topcoat are water soluble and the color is kind of milky color. I did not see you parts but Sodium or Potash residue is colorless and can`t be seen as white liquid. Anyway I suggest you to repair the blackening in a simple way: First cover all the part with plastics and tape. Just leave the damaged places. Check for Cold Black Oxide Chemicals in your area and then degrease the part (By the offered products by companies), remove the damaged blackening by 15-20% HydroChloric acid (HCl) by spray, then rinse well and then go for Blackening instruction. Please bear in mind that you should wear safety gloves, goggles and mask. Use the blackening material in spray form through the revealed area, then wash and dry it. After finishing the process use protective oil on it and leave it for 1 or 2 days for better results.
Good Luck
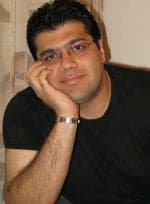
Alireza Reyhan
- Istanbul, Turkey
April 1, 2014
Q. Hi, we are blackening low carbon steel parts. We are observing white dots on the blackened parts. Before blackening, these parts are rem barreled. The white dots seem to be fine spots where blackening has not happened. Mild steel fixtures are used to hold the parts in the blackening line. Any insights would be helpful. Thanks in advance.
Sri Ram- Chennai, TN, India
September 19, 2013
Q. Hi,
I'm new to black oxide. We had some test parts hot black oxided for a rust endurance test where we place the parts on the lawn just outside our office. Just before leaving it there I spotted a small tree with small oranges/limes on it. I squeezed out some juice on the parts and then left them in the sun. I few hours later I went out with some other test part and found the the lime juice had completely removed the black color from the first parts where the juice was present.
Is this normal?
- Guangzhou, China
October 11, 2013
A. Hi Peter. It sounds normal to me. Black oxide is simply a form of iron oxide rust, and I'd expect mild acids like fruit juices to easily dissolve iron oxide. The waxes or oils on the black oxide might provide a tiny bit of temporary rust resistance, but apparently not enough to resist the fruit juice in this case.
Regards,
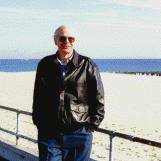
Ted Mooney, P.E.
Striving to live Aloha
finishing.com - Pine Beach, New Jersey
October 14, 2013
Q. We do chemical blackening process and we have the following problems:
1. White deposit at some places.
2. Formation of red patches here and there.
3. Blackening is followed by oiling or not?.
4. Blackening is being done for surface protection why should we apply oil?
- Chennai, Tamilnadu, India
February 26, 2015
A. Hi cousin Murali. Although I'm no expert in black oxide, such questions are so perennial that I've seen them repeatedly :-)
1. The white deposit is most likely failure to boil out, as Rod explains above.
2. The red patches are perhaps due to controlling temperature by heat addition instead of concentration. The tank must be BOTH at a rolling boil AND at the right temperature; that is accomplished by holding the concentration as Rod explains on some other threads. Search for his name, "red" and "black oxide" to find those threads.
3. Yes, oiling or waxing is required.
4. Black oxide is one form of "rust" in a desirable color and form. If not protected from the elements by oil or wax it will convert to the undesirable color and form.
Good luck.
Regards,
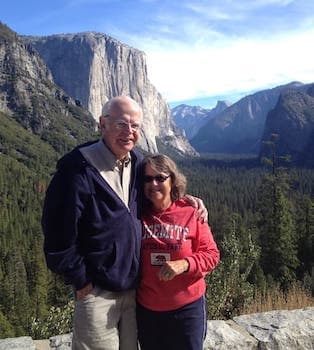
Ted Mooney, P.E. RET
Striving to live Aloha
finishing.com - Pine Beach, New Jersey
February 2015
Q. Can you please help? This is my time to do hot bluing. My boss wants me to use their old facility (the boiler and the chiller) for my gun bluing operation. It is advisable or not to use the two facilities?
ave juezantechnician - abu dhabi,UAE
April 14, 2015

A. Seriously, nobody can say whether some unknown facility is appropriately designed and in good enough condition for such an operation. But what would you use a chiller for in a hot bluing operation?
Regards,
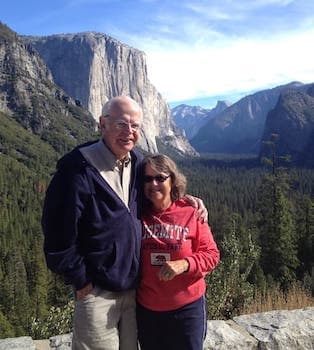
Ted Mooney, P.E. RET
Striving to live Aloha
finishing.com - Pine Beach, New Jersey
Q. Hi Ted,
Thanks for replying in my question.
If it was up to me I would not use their old facility, but what can I do? Our management wants to see if their facilities are still working good. Is there no bad effect in my bluing solution if I will use the chiller and the boiler? Because they want me to try to use it, but I'm afraid it might kill my bluing solution easily. I will use Oxynate 7 by Brownells.
Yes Ted, my boss wants me to use the chiller in my bluing operation; my question is it is ok to use that one?
ave juezan [returning]technician - abu dhabi,UAE
April 14, 2015
A. Hi again. I think we are having trouble understanding each other. A chiller is used to make a process tank colder. What are you planning to do with the chiller in a hot black oxide process?
Regards,
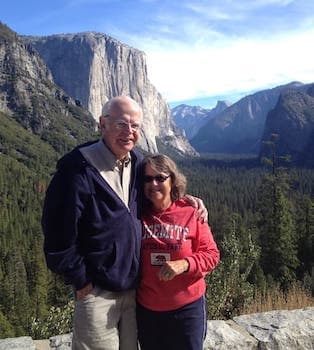
Ted Mooney, P.E. RET
Striving to live Aloha
finishing.com - Pine Beach, New Jersey
April 2015
Q. Hello. Anyone can explain to me what is GUNKOTE?
Thanks
- dubai, uae
May 2, 2015
July 2015
Hi Kabz. Where did you hear about that word and in what context please? My guess might be KG Gun-Kote offered by Brownells. It's an epoxy low friction bake-on coating available in a number of colors. Good luck.
Regards,
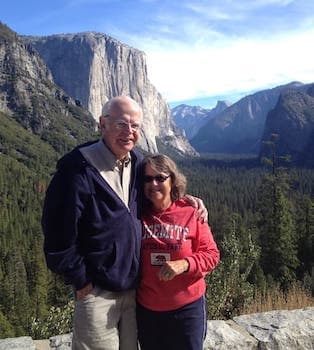
Ted Mooney, P.E. RET
Striving to live Aloha
finishing.com - Pine Beach, New Jersey
Q. We are experiencing what appears to be a white crystalline growth on a few parts that we have had black oxided. The severity varies from part to part, and 2 of 10 showed no signs of this strange "growth". After cleaning the material off the part it has come back. It almost looks like salt. Any ideas on what it is and how to combat this issue?
Nathan Pekoc- Sugar Grove, Illinois USA
July 23, 2015
A. Hi Nathan. Look to Rod Henrickson's explanation earlier in this thread. It surely seems that failure to "boil out" is the cause of that growth. Good luck.
Regards,
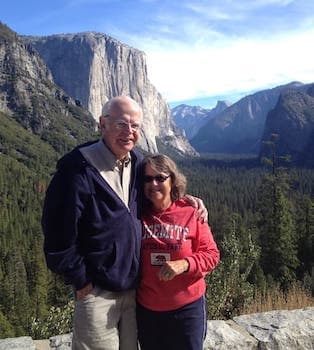
Ted Mooney, P.E. RET
Striving to live Aloha
finishing.com - Pine Beach, New Jersey
July 2015
A. White "growth" after bluing are the salts crystallizing and bleeding out of the hidden places. We control this by placing hot parts directly into very hot water into which we add a very small amount of vinegar ⇦in bulk on eBay or Amazon [affil links] The vinegar will naturalize the base or caustic soda ⇦liquid caustic soda in bulk on Amazon [affil link] . Let it remain for 10 plus minutes then place in oil or WD-40 ⇦ on eBay or Amazon [affil links] and let it rest until cool. Leave overnight to cure.
Robert LeggGunsmith - jacksonville, Texas
February 3, 2016
Coating - Steel Cylinder w/ 12 small Blind Holes
Q. I am looking for a black oxide type of coating on a steel 12L14 machined part. The part is 1.25" in diameter with 6x 8-32 UNC-2B blind threaded holes per face. We have tried several attempts at applying a black oxide coating to these parts only to find out that in 2-4 weeks of humid northeast US weather, we get salt bleed in most if not all holes. I am wondering if you experts out there can tell me if I would have better luck with a Manganese or Zinc based phosphate coating on these parts. We need the rust prevention but without the salt bleed in the blind holes. Our current vendor has tried a hot oil dip, agitation, and blowing out the holes after the oxidation process, all with varying results.
Any help would be appreciated.
Tim
Operations - Middletown, Connecticut USA
October 25, 2018
A. Hi Tim. I appended your inquiry to this thread because I thought Rod Henrickson's posting was so applicable and informative. Please have your shop try the full half-hour boil-out that Rod suggests; Robert Legg's suggestion of a little vinegar might help (I don't know).
Please return their favor by letting us know what happens :-)
Regards,
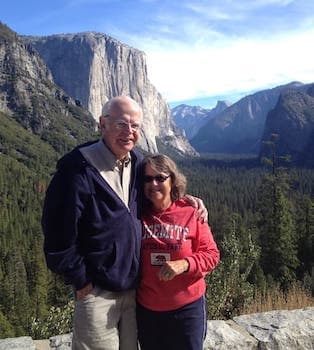
Ted Mooney, P.E. RET
Striving to live Aloha
finishing.com - Pine Beach, New Jersey
October 2018
Basket contact marks in black oxiding
Q. My name is Julie Gardner and I co-own Oklahoma Superior Plating with my husband Tim. We have begun a new line in black oxide and it is small line. We are coating 4340 Steel. Our finished product is coming out with a mixture of acceptable parts that have a finish free of defects to parts that exhibit contact spots from our baskets. These can even happen in the same basket of parts. These results are sporadic. We are keeping a close watch on the temps as this is a high heat line. Any help would be greatly appreciated.
Julie GardnerOklahoma Superior Plating - Duncan, Oklahoma, United States
August 8, 2019
A. Hi Julie. At the risk of being Captain Obvious, I think you need to either jiggle the baskets or re-think the basket design. I would not attempt any temperature or concentration change for those basket marks.
Regards,
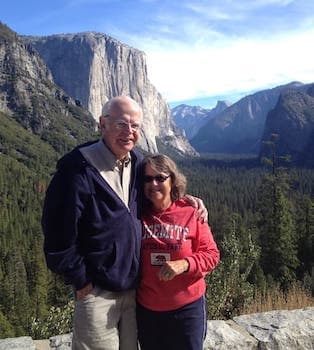
Ted Mooney, P.E. RET
Striving to live Aloha
finishing.com - Pine Beach, New Jersey
October 2019
Thank you so much Sir. We did just that! It has definitely corrected the problem. Again, thank you so much for your feedback!
Oklahoma Superior Plating - Duncan, Oklahoma USA
October 15, 2019
A. Black Oxide works best when it is free to move around and under a part unobstructed. You can prop up the parts to allow for this in the basket or simply put a surface on the bottom such as rebar as a base material to prevent the flat contact by the parts to the basket. Make a birds nest of rebar on the bottom of the baskets and you should be fine.
J Lee PowellAnodizing and Black Oxide Supplier - Edinburgh, Indiana
December 27, 2019
Q. Hello all,
My name is Marc and I am in the metal finishing business, specified in zinc phosphate and black oxide. But lately I have been having some problems with a customer. After black oxiding their parts, and use oil as a protective coating to prevent rust, the parts seem to have some white residue showing on them, it looks like a cloud. This usually happens within 12 to 48h of the part being done, Sometimes even longer. Now, I assume that it is salt from the black oxide tank, which my boss disagree. But I have tried several things such as going into a cleaner/degreaser, hot water before putting oil on them. But it doesn't seem to help much. Is there anyone out there experiencing the same issue, and if yes, is there anything that can be done to solve the issue. Thank you for!
- Waterbury, Connecticut, USA
April 6, 2020
A. Hi Marc. We added your question to a thread where it looks to me like gunsmith Rod Henrickson answered it. But feel free to expound if his answer doesn't suffice.
Regards,
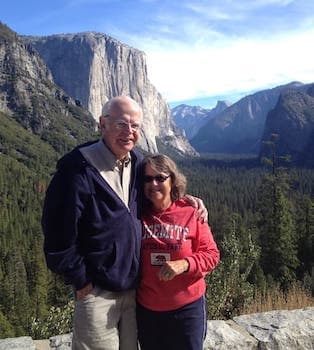
Ted Mooney, P.E. RET
Striving to live Aloha
finishing.com - Pine Beach, New Jersey
April 2020
Q. Hello Ted, I did notice his answer, but the problem is that the customer doesn't like the idea of wax on their parts, they simply want black oxide and oil.
Marc Roseau- Waterbury Connecticut USA
April 6, 2020
A. Hi again. Wax vs. oil didn't strike me as the heart of Rod's suggestion; to me it seemed the half-hour boil-out was the heart of the matter.
Regards,
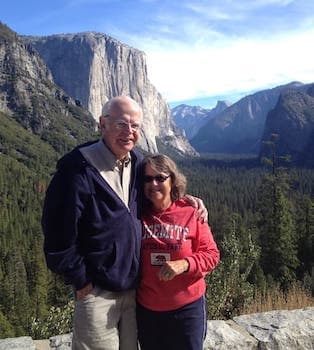
Ted Mooney, P.E. RET
Striving to live Aloha
finishing.com - Pine Beach, New Jersey
April 2020
⇦ Tip: Readers want to learn from your situation;
so some readers skip abstract questions.
Q. We blackened mild steel, observed grey finish with maintaining all correct parameters of MIL-DTL-13924 [⇦ this spec on DLA].
chathush Vekatesh- Bangalore Karnataka
January 11, 2021
Hi Chatrush. Hopefully you'll get some immediate feedback from someone who has obtained a gray finish, but questions really should be longer than the answer you are seeking -- so it wouldn't hurt to flesh out the inquiry a bit with a few paragraphs about: concentration, temperature, salt boil-out done or not done, whether it's a problem that popped up after years of satisfactory operation or whether you are just starting and have never successfully blackened, whether it affects every piece you are blackening or only a few, etc.
I hate to nitpick, but the actual case is that you did not maintain all the correct parameters or the work would have come out correctly :-)
... there is obviously one or more important parameters that are either not being monitored, or where you interpretation of their correct values is in error, or where you have been given incorrect information regarding those values. One of those parameters may, of course, be the material composition or surface characteristics of the component you are trying to black oxide.
Luck & Regards,
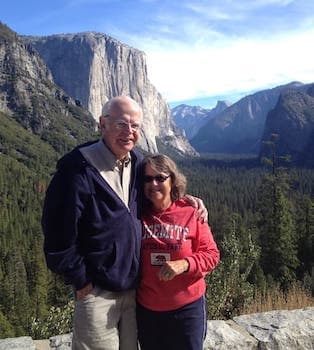
Ted Mooney, P.E. RET
Striving to live Aloha
finishing.com - Pine Beach, New Jersey
January 2021
⇦ Tip: Readers want to learn from your situation;
so some readers skip abstract questions.
Q. How do you use wax coating at end process -- or how do I use the waxing in a hot black oxide process. Thanks for the help.
Elias Damian- Phoenix Arizona
February 8, 2021
A. Hi Elias. Are you a production plating and metal finishing shop or a gunsmith?
Usually a production processing line for black oxide will not be a single black oxide tank, but will be a whole series of tanks, including cleaners and rinses; the last tank in the process will often contain a water soluble wax purchased from your metal finishing process supplier. Sorry, I don't know the actual chemistry of them.
A gunsmith is usually more or less a bespoke manufacturer who offers a tailored service to the buyer, and he might well do manual waxing or oiling after the black oxide process.
Luck & Regards,
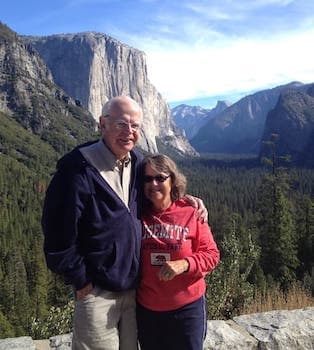
Ted Mooney, P.E. RET
Striving to live Aloha
finishing.com - Pine Beach, New Jersey
February 2021
⇦ Tip: Readers want to learn from your situation;
so some readers skip abstract questions.
Q. Does anyone know if something during the black oxide process can cause the steel surface to crack. I am using Dual Phase steel tubes.
Armando Arredondoemployee - Mexico
November 13, 2021
A. Hi Armando. May we assume that you are in fact encountering a surface cracking problem? Please tell us when it was noted, how prevalent the problem was, etc.
I spent 20 minutes or so on google unsuccessfully looking for an answer to the abstract question of whether black oxide ever can cause cracking of dual phase steel, but I did read that it dual phase steel should not be carbonitrided.
Luck & Regards,
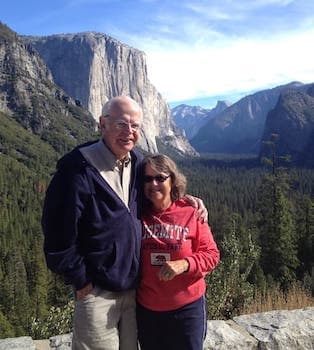
Ted Mooney, P.E. RET
Striving to live Aloha
finishing.com - Pine Beach, New Jersey
November 2021
Q, A, or Comment on THIS thread -or- Start a NEW Thread