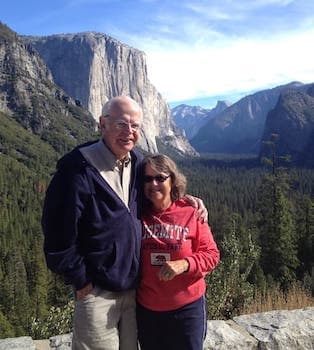
Curated with aloha by
Ted Mooney, P.E. RET
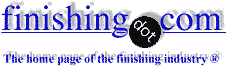
The authoritative public forum
for Metal Finishing 1989-2025
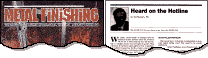
-----
Hard Chrome Plating of Cast Iron Q&A Problems & Solutions
Quickstart (no readers left behind):
'Hard Chrome' means a thick, wear-resistant plating of chrome, usually directly onto the substrate, rather than the very thin layer of chrome over nickel plating which is typical of decorative chrome plating applications. Readers may wish to review our "Chrome Plating Introduction & FAQS".
Cast iron is difficult to plate because of its inclusions of graphite.
Q. We are facing hard chrome defects in cast iron cylinders (Diameter 600 x 1800mm). The defect types are generally pits, porosity which is detected after dye penetration test also. We use 1.3 gm /litre sulphate and chromic as 250 gm/litre.
We do not preplate with nickel/copper, etc., and follow general cleaning practice with DM water/calcium carbonate.
Can anyone help or suggest to resolve?
QA ENGINEER - Ahmedabad India
April 14, 2025
⇩ Related postings, oldest first ⇩
Q. We are looking for a pretreatment method to hard chrome plate a roller made of chilled cast iron.
Any advise is highly appreciated.
Herbert Fröhlich1996
A. Hi, Herbert,
Chessin, Knill & Seyb report in the Feb. '83 issue of Plating & Surface Finishing: "Free graphite in cast iron and some high carbon steels does not create a problem for the plater unless the metal is subjected to excessive etching procedures that cause the graphite to accumulate on the surface of the work, making it very difficult to cover with a chromium deposit."
I would interpret this to mean that part of the solution is to be sure to minimize the etching step in pretreatment.
Good luck!
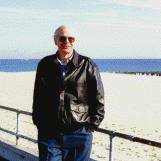
Ted Mooney, P.E.
Striving to live Aloha
finishing.com - Pine Beach, New Jersey
Q. We are hard chrome plating chilled cast iron calender rolls (65 HRC hardness, 3% carbon) size 700 mm dia. * 2000 mm long that are used in PVC (polyvinyl chloride) film industry.
We sandblast the roll, scrub by hand with pumice powder ⇦ this on eBay or Amazon [affil links] , chrome plate in conventional chromic acid at 4 ASI initial forward strike (no reverse etch) and step down to 2 ASI, at 73-75 °C, intermediate grind to 100 micron, re-chrome to 200 micron finished thickness. At times during grinding the deposit cracks, sometimes during service at 210 °C temperature the deposit cracks. We operate at higher temperature to produce a less hard & low stress deposit. Due to lack of floor space we do not have cleaning tanks, or oven for stress relieving. If absolutely essential we can incorporate an oven and one cleaning tank. What do you recommend? Cast Iron dryers 1220 mm dia. * 2000 mm long, used in paper industry has pin holes which are not to be covered by chromium deposit. Which is the best option: acid copper/cyanide copper/dull nickel or any other undercoat/thermal spray/inserting steel pins in cast iron surface pin holes, from technical and commercial point of view?
Shaunak Shah- India
1998
by Weiner & Walmsley
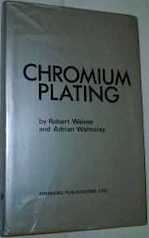
on AbeBooks
(rarely)
or eBay
(sometimes)
or Amazon
(sometimes)
(affil links)
A. I believe that steel plugs and nickel under-plate is the correct approach.
The eminently readable booklet, "Defects in Hard Chromium Deposits", by Chessin, Knill, and Seyb says that copper is suitable on ferrous substrates not subjected to severe pressure or stress. Nickel is recommended for other applications. The nickel bath should be brightener-free. Details on repair methods of the basis metal are also given.
This paper was presented during SUR/FIN 81. I understand that Atotech has an office in India, perhaps a copy of this paper is available from them.
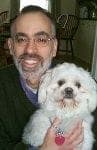

Tom Pullizzi
Falls Township, Pennsylvania
A. Hi, Shaunak. Also, in answer to your question about an oven, my response is 'yes, it is absolutely essential'. Any hard chrome plating shop that does items subject to hydrogen embrittlement needs an oven to bake the items for hydrogen relief. Good luck.
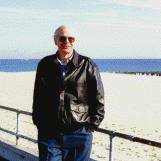
Ted Mooney, P.E.
Striving to live Aloha
finishing.com - Pine Beach, New Jersey
by Robert K. Guffie
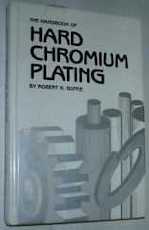
on AbeBooks
(rarely)
or eBay
(rarely)
or Amazon
(affil links)
Q. Dear Sir
We thank you very much for your prompt response.
90% of the steels we chrome plate have a tensile strength way below 1000 Newton/mm2, In most of these jobs chrome plating is carried out for wear resistance, hence there is no problem if stress relieving is omitted. However with chilled cast iron, when the roll is heated during service to 200 °C or due to localised heat generation during grinding, hydrogen entrapped in the chrome plating may be responsible for cracking? Manufacturer of calender rolls caution that roll heating or cooling must be carried out at a rate not exceeding 0.5 to 1 °C per minute. Is this heating cycle adequate for carrying out stress relieving or chromium plating?
These calender rolls have 3% carbon, the end application dictates that the plating deposit must have good adhesion, no pin holes, good corrosion resistance, because there is no tensile load on the roll or no abrasive material coming in contact with the roll, high wear resistance of the chromium plating is not required.
Reverse etching is very good for finish ground jobs of low carbon steels because it cleans the job and being low carbon not much of the carbon comes to the surface and a good adhering deposit results. However with high carbon steels sand blasting accompanied with good cleaning may be a better technique to produce a good adherent deposit? What temperature, ASI, time, sequence do you suggest to produce a low stress chrome deposit? In case during intermediate grinding we notice pin holes, is there any solution to micro drill the hard chromium and plug. Any other solution?
Thanking you
Yours faithfully
- India
A. Sir,
On soft steel, the thicker the deposit, the more stress it will have relative to the bond strength. When you heat it, the chrome expands faster than the steel and cracks or peels.
Hydrogen embrittlement is a cracking of the substrate normally along grain boundaries and has nothing to do with the initial cracking of the chrome. After the chrome cracks, the crack will propagate into the base metal because of hydrogen embrittlement.
James Watts- Navarre, Florida
A. Plating a 1/1000 inch thick deposit of nickel is such an elegant solution to so many problems; pinholes, corrosion protection, adhesion, that it really doesn't pay to try to do without it.
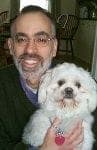

Tom Pullizzi
Falls Township, Pennsylvania
Q. SIR,
I AM A MANUFACTURER OF CHILLED CAST IRON ROLLS. I HAVE COME ACROSS A LOT OF PEOPLE WHO HAVE UNSUCCESSFULLY TRIED TO PLATE CHILLED CAST IRON ROLLS. IF YOU FIND A FOOLPROOF SOLUTION, DO LET ME KNOW.
REGARDS,
VIKRANT SINGH GILLNew Delhi, India
1999
A. Hi, Vikrant.
I don't think anyone has foolproof solutions, but after heeding the advice of Chessin, Knill and Seyb, consider Tom's & Scott's postings which present a good case for specifying an under-layer of nickel plating. Good luck.
Regards,
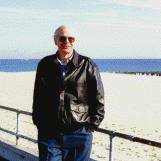
Ted Mooney, P.E.
Striving to live Aloha
finishing.com - Pine Beach, New Jersey
Q. I am having a problem with a hard chrome plating application. As a hard chrome job shop, we normally plate plastic injection molds and assembly machines. We have started plating cast iron rolls for a new customer and are unable to eliminate small voids or pits in the plating after a post grinding process. We feel the pits are from the porosity of the cast iron and not the bath chemistry. As I stated before, the part is a cast iron roll 7.500" dia. X 6.00" tall with a 6.200" i.d. (the grade of the cast iron is unknown). The O.D. is to be ground undersize, then hard chrome plated and reground to the finish dimension. The total thickness of the chrome after final grinding is approx. 0.004" p/s. I would normally burnish a part like this to close up the pores in the steel, but there are holes on the O.D. that would prevent the burnishing tool from working properly
Should iron castings that require a #16 micro inch finish be plated with another material, possibly a sulfamate nickel, then hard chrome plated?
Any suggestions would be appreciated.
Jeff
Jeff Hanaway- Pennsylvania
2000
A. Jeff we use chrome plated roll in our business of making coated paper. The nickel under coating is a good way to seal the cast iron surface from corrosion because chrome is porous. You might want to try nickel plating the cast iron first, about .001" per side, then chrome plate.
Scott M. RichardsonCoated Paper - Westbrook, Maine
2004
Q. Dear sir:
We are working on coating the cast iron engine cylinder with the hard chrome and now we would like to know if there is a way that we can measure the adhesion of the coating. Thank you for your attention & your prompt response will be highly appreciated.
Sincerely yours,
hassan eivazy- Iran, Tehran
2001
A. Hi, Hassan. There are a number of different adhesion tests, but the "modified Ollard test" is probably the "referee" method because you do an actual tensile pull test of the adhesion -- please see thread 18002 for diagrams and explanations. Good luck.
Regards,
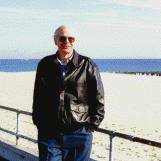
Ted Mooney, P.E.
Striving to live Aloha
finishing.com - Pine Beach, New Jersey
Hard Chrome Plating on Cast Irons containing Graphite
Q. We are facing a problem while Hard Chrome Plating on Cast Irons containing Graphite, the chrome simply does not adhere, even after 3.25 Amp/square inch. We are considering Grit Blasting or undercoat plating?
Neil Paarekh- Mumbai, Maharashtra, India
2001
A. Neil,
We had similar problems plating chrome onto graphite cast iron, specifically meehanite gray cast iron. The problem was resolved by grit blasting as you mentioned, then going into the chrome tank "live", with both anode and cathode connected, and current on at about 6 volts. (We use welding cable as temporary jumpers when going into tank live.) You will need to "strike" with about 6-8 amps/sq. in., then process at approx. 3 amps/sq. in. Another important factor is to process as soon as possible after grit blast (before the metal oxidizes too much).
Ralph Peltier- Providence, Rhode Island
Q. We do hard chrome plating for automobile industries. We are facing problem of plating peel-off on cast iron . We have attended to all types of pretreatment before plating. Any suggestions.
Regards,
Harish Krishna- Bangalore, India
2002
A. Dear Mr Krishna,
1)What kind of cast iron are you talking about?
2)When you say "all types of pretreatment" you don't specify.
You'd better describe exactly what you have tried so far.
Regards,
Christos Sigalas- Athens, Greece
A. Krishna,
Can you explain what type of chrome solution you use. If you use a Sargent's chrome solution try to bake the part at 200 °C, degrease for 2-3 hours before plating. That is to remove the hydrogen from the part. All casting materials have some hydrogen from the beginning.
Sincerely,
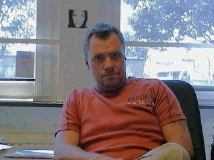
Anders Sundman
4th Generation Surface Engineering
Consultant - Arvika,
Sweden
2002
Q. HARD CHROME PLATING ON CAST IRON
WE ARE FACING PEELING PROBLEM ON PLATING CAST IRON. WE HAVE ATTENDED TO sulfurIC ACID ETCHING, POLISHING, HOT WATER WASH, caustic soda ⇦liquid caustic soda in bulk on Amazon [affil link] CATHODIC CLEANING, AND COLD WATER PRESSURE WASH. THE CAST IRON IS A ALLOY CASTING OF SILICON, MANGANESE AND CARBON. WE ARE USING CHROMIC ACID SULPHATE BATH. THE JOB IS VERY BIG AND CONNECTING CATHODE AND ANODE ARE THROUGH CABLES AND THIS TAKES ABOUT 30 MIN. COULD THIS BE ONE OF THE REASONS? KINDLY SUGGEST A PROPER PROCEDURE. WE KNOW THAT THE JOB SHOULD BE CLEAN AND FREE FROM OXIDE SCALES BUT PRACTICALLY THERE COULD BE AN HUMAN ERROR.
REGARDS,
Harish Krishna [returning]- Bangalore, India
2002
Hard chrome coating on cast iron cylinder
Q. Dear all,
We have made hard chrome coating on Cast iron compressor cylinder bore, but the coating gets peeled off in some portions after honing using Diamond stick.
What could be the solution to prevent this peel off while machining?
We are in the critical process of our design. please help me.
I would appreciate if you will consider my situation and you give some solution to this issue.
With regards,
compressor manufacturer - Coimbatore
2006
A. The highest probability is poor preprocess steps. It could be either the cleaning or the activation steps.
James Watts- Navarre, Florida
Q. Does anyone have a simple reliable way of pretreating nitrided cast iron prior to chrome plating.
Norman Evanshard chrome plating - Springfield, Ohio
2006
A. A thorough cleaning (solvent and electro), light sand blast and immediate plating in a mixed catalyst or fluoride bath sounds to me like the easiest method. But you'll have better answers if you tell us what are you talking about. Shape, size, quantity, finish or smoothness required. Also, if you have tried something w/o success.
Guillermo MarrufoMonterrey, NL, Mexico
Hard chrome plating s g cast iron
Q. I would like to know what pre treatments are required before plating sg cast iron i.e., if we have to etch anodically or cathodically in sulfuric acid and the concentration of acid.
thank you,
plating shop owner - Chennai, Tamil Nadu, India
2006
A. Cast iron you have only to prepare mechanically, i.e. by high speed polish, and then put it in the chrome bath under plating current, no reverse current allowed.
Arik Linnoble metals - Tel Aviv, Israel
Peeling and pitting of hard chrome plating on SG iron casting
Q. We are facing problem during hard chrome plating on SG IRON Casting. peeling off and pin holes is the major problem.
Pre plating Dia. 69.85/69.80mm
After hard chrome Dia. 70.1/70.15mm
Finish dia. 69.97/69.95mm
kindly give your opinion
Product designer - Pune, Maharashtra, INDIA
May 13, 2008
A. I am not surprised that you are having a problem. You might try a vacuum impregnation pre-plate or a copper that is buffed under plate. Chrome absolutely will not fill the voids-holes-pores. It may plate over them, but the plate may peel because of trapped liquids in the porous metal.
You may have to switch to a thermal deposition process of an appropriate alloy for the end use of your part. You may have to use plasma spray or one of the high velocity processes. This will require a bit of home work.
- Navarre, Florida
Q. Sirs,
Does that mean that hard chrome plating on SG IRON is very difficult to achieve (100% defect-free)?
- Pune, Maharashtra, India
A. I am not sure of what you are calling SG iron. From your stated problem, I assumed that it is a cast iron which on anything but an investment casting is going to have pits and voids, even when turned (machined).
If it is, you probably are going to have to copper plate it and re=machine the copper.
Chrome has one of the worst ability to plate into a pit or void.
- Navarre, Florida
Ed. note: SG probably means 'spherical graphite', i.e., malleable iron.
Peel Off and Pin hole problem on SG Iron Hard Chrome Plated surface after Grinding
Q. Dear Sir,
referring to subject matter,
We are facing continuous problem of Peel Off of plating (Plating thickness is 450 to 500 micron) & finish size required is 200 micron diametrically on S G Iron product. Also there used to be heavy taper & the length is 149 mm.
Please guide whether the problem lies with the Pre-plating processes or actual plating process.
Regards,
Vijay
Customer - MUMBA I.MAHARASHTRA, INDIA
December 8, 2008
A. 500 micron (0.020") is too much for hard chromium, more so on a difficult to plate substrate like SG cast iron. Nevertheless, you say nothing about your plating cycle, so, how can we possibly know what is wrong?
Guillermo MarrufoMonterrey, NL, Mexico
Q. We have problems with hard chromium plating on cast iron parts. Please describe surface preparation and plating condition (current density, temp.) for hard chromium plating on these parts. Can we use metallic inter layer coating like nickel electroplating before hard chrome plating?
Ali zagharplating shop - Cabol, Afghanistan
July 23, 2009
RFQ: Seeking hard chrome plating and finishing for hydraulic piston/rod made of ductile iron
One-piece piston/rod considered to be cast of ductile iron in order to save production cost. The part weight is about 10kg, dimensions: Ø225x35mm (piston) and Ø100x55mm (rod). Chrome required to provide proper finish for seals application and corrosion protection for exposed portion of the rod.
QTY=100 for initial order.
MFGR - Delta, British Columbia, Canada
September 18, 2009
Ed. note: This RFQ is outdated, but technical replies are welcome, and readers are encouraged to post their own RFQs. But no public commercial suggestions please ( huh? why?).
Does HEEF hard chrome plating work on cast iron?
Q. Dear Sir,
We successfully do hard chrome plating on liners made from cast iron. We directly do hard chrome plating on these liners using chromic acid. We do not do any undercoat such as woods nickel or copper plating before doing hard chrome and directly plate the cast iron liners for hard chrome plating. We do reverse etch in the plating bath itself.
Now my question if can we plate these cast iron liners directly using HEEF (of Atotech) successfully or not, as people say that HEEF does not work on cast iron items. Will it work if we do reverse etch in a separate tank and than plate using HEEF?
plating shop - India
August 29, 2008
A. Personally I wouldn't plate chromium directly on to cast iron - the cast iron may be too porous and this will cause all sorts of problems. I would recommend you use a high throwing power copper and then nickel and chromium. However, you may (and should) talk with Atotech first!
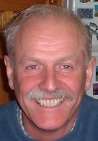
Trevor Crichton
R&D practical scientist
Chesham, Bucks, UK
Q. Dear Sir,
Thank you for your response.
I know that there is a general practice to undercoat cast iron and then do hard chrome plating over it which increases the cost of plating considerably. However as written above we successfully plate the Cast iron Liners directly with hard chrome plating. We have being doing this process since more than 15 years and have no problem, such as peel off or lack of better adhesion. Also what is important is we plate on diesel engine liners which are subjected to high pressure and temp.
We wanted to use the HEEF bath for better plating and for cost saving of energy as in India it is expensive. We had contacted the Regional sales manger of atotech but we was also not able give us any satisfactory answer to us. They said that we will have to go by trial and error method, which is no satisfactory answer.
Also does the carbon content of the cast iron which will later so into the HEEF plating bath will disturb the bath or not? If yes want are the levels of which it can withstand the contamination?
Thanking you and awaiting for your reply.
- India
A. Hi,
HEEF 25 is not a good solution to use on casting iron, because the etching structure will be wrong to get right structure for chrome deposit and that also can be a bad adhesion between chrome and material. But if you etch in Sergeant solution as a first step an transport it to HEEF it will work. As Trevor says copper plate it first, maybe also a nickel layer will show you the best results.
Regards
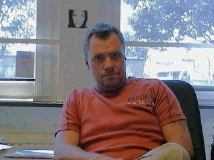
Anders Sundman
4th Generation Surface Engineering
Consultant - Arvika,
Sweden
A. Since your primary concern is the cost of energy, why don't you use trivalent chromium -you get double the metal for the same rupee. However, you may not get the same successful engineering layer that hexavalent chromium will give you, but maybe that won't be as important as the operating costs
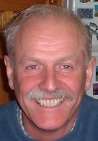
Trevor Crichton
R&D practical scientist
Chesham, Bucks, UK
Q. Dear Sir,
I give my regards to Mr.Anders Sundman and Mr.Trevor Crichton for replying to my inquiry.
I will like to point out that we do hard chrome plating of the liners which are subject to high temp and pressure therefore we cannot shift to trivalent chrome plating as we need the engineering benefits of hexavalent chrome plating, such as hardness and etc.
Also Sir if I first etch in Sergeant solution and transfer it to HEEF bath as said by you will than also I will have to do a undercoat of nickel or copper?
Also I am using Sergeant solution for plating is there any ways such as additives etc, available for better plating and cost saving that can be added in my plating solution.
Thanking you,
- India
Q. Please suggest what are the essentials to do for hard chrome plating over the Gray cast iron cylinder, and how can I seal the minute pin holes. How can we we ensure that it's sealed?
Ebrahim Ebrahimreading the book - Chennai, Tamilnadu, India
October 21, 2010
Q. Possibility of safely making hard chrome plate on cast iron rolls of 400mm.
Quality: ASTM Gr.45-12 (normalized and tempered)- 3,5%C; 2,6%Si...0, 3-0, 4%Mg
Influence of free graphite?
engineer, metalurgist - Celje, Slovenia
December 21, 2011
Q. We are about to hard chrome plate cast iron cylinder liners of diesel engines. We successfully plate case hardened shafts and plate,
but we need to know the best surface preparations for hard chrome plating cast iron.
The anode positioning specifications for 4" in. dia. cylinder is also a problem.
Any kind hearted help would be greatly helpful.
- Dhaka, Bangladesh.
July 18, 2012
Q. Dear Sir,
I am working on the design of an 'Impression cylinder' of offset printing press. The problem before me is the Peeling Off of Hard chrome coating on the Cylinder.
Till now the usual coating method that we follow for similar situation is Electroplating of hard chrome. The substrate is G3 cast iron of nearly 190 mm dia. and 1030 mm length. Can you please suggest an alternate Coating method for me? Either a new coating material or a different method for chrome?
- KANNNUR,KERALA STATE, India
January 27, 2013
Tip: This forum was established to build camaraderie among enthusiasts through sharing tips, opinions, pics & personality.
The curator & some readers who publicly share their info will be less likely to engage with those who don't.
A. Hi Nirmal. We've appended your inquiry to an interesting discussion which I think will answer it for you. If not, please try to phrase your question in terms of the answers already given (like "we tried ... and it didn't work", or "we cannot nickel plate because ...", etc.). Thanks!
Regards,
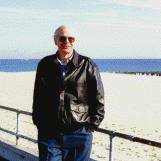
Ted Mooney, P.E.
Striving to live Aloha
finishing.com - Pine Beach, New Jersey
Q. We are facing issues with hard chrome plating on Sg ductile iron casting part with 80 micron plating thickness, issue types are pin holes, porosity. Please suggest.
- Ahmedabad, India
January 18, 2020

Q, A, or Comment on THIS thread -or- Start a NEW Thread