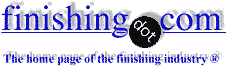
-----
Dip-spin zinc flake coatings with high corrosion resistance
Q. I am interested in learning more about Mil-C-87115A, "Coating, Immersion Zinc Flake/Chromate Dispersion". The specification reads like this is manna from heaven for those who would like to avoid conventional zinc plating, bakeout, and chromate conversion coating, but it does not say how the coating is applied. Does anyone have experience with this process? Is it commercially available? Is the process cost effective to set up?
Thanks,
Bob
R.D. Mikkolaaerospace - Oak Ridge, Tennessee
1996
----
Ed. note updated April 2016: Specification MIL-C-87115 [link is to free spec at Defense Logistics Agency, dla.mil] has been inactive since 1997
Other readers may wish to also see BS 7371-11 which is the British Standard for this kind of coating.
A. This sounds like a proprietary process that is sold by Metal Coatings in Chardon, OH. We are a licensee in Chicago. I will have one of our people look up this spec and let you know if this is the same spec/product.
Robert Giesel1996
RFQ: This product sounds like Dacrol (France) or Deltatone (Germany). Because they both offer a license arrangement that does not allow the product to be used within a radius of x miles from an existing user, it excludes us from using either.
We are looking for an alternative. Can you help please.
Peter S [last name deleted for privacy by Editor]protective finishes - Redditch, Worcestershire, England
1996
Ed. note: This RFQ is outdated, but technical replies are welcome, and readers are encouraged to post their own RFQs. But no public commercial suggestions please ( huh? why?).
A. Thanks Robert; hi Peter...
Although it is true that Dacrol/Deltatone are proprietary coatings that you can only license from the license holder, there are many additional suppliers of MIL-C-87115 [link is to free spec at Defense Logistics Agency, dla.mil] Zinc Flake Coatings.
The site's supporting advertisers will contact you privately about their offerings because a public discussion of one proprietary versus another proprietary invariably leads to spam and hostility, has often even led to phony testimonials ("satisfied customers" posting from the IP address of a supplier). So we don't include postings claiming that one brand is better than another, and any claims that "my fu-fu juice, but I can't tell you what it is, is better than their secret fufu juice" don't suit a technical discussion forum anyway :-)
Regards,
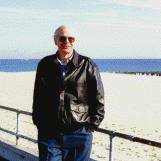
Ted Mooney, P.E.
Striving to live Aloha
finishing.com - Pine Beach, New Jersey
RFQ: Dear Sir,
We apply zinc flake organic coatings at 2 addresses in UK and are always looking for new and improved products, can you let me have more detail, i.e., coverage rates, costs, performance.
Richard D [last name deleted for privacy by Editor]- West Midlands, UK
1998
Ed. note: This RFQ is outdated, but technical replies are welcome, and readers are encouraged to post their own RFQs. But no public commercial suggestions please ( huh? why?).
A. Dear Sir:
Zinc flake/chromate dispersions can be applied by several different methods; dip/spin, dip/drain, or spray. The application method will be determined by the part configuration, appearance requirements, and cost constraints.
You are correct with your assumption that this coating is a great alternative to zinc plating. These coatings typically provide greater corrosion resistance, but are applied somewhat thicker. Many of the automotive companies are choosing to use this type of product in place of plating on fasteners and other areas where high corrosion protection is required.
As mentioned in previous responses, this product is typically applied by a licensed applicator but a sound infrastructure exists to meet most application requirements.
Edward KonecznyBirmingham, Michigan
1998
----
Ed. note: Thanks Edward!
RFQ: WE HAVE 5/8-11 HVY HEX NUTS THAT NEED TO BE ZINC PLATED TO MIL-C-87115 CLASS 2 OR ASTM F1135
[withdrawn] GRADE 7.
PLEASE CONTACT US FOR WEIGHT AND QUANTITY.
THANKS, JIM
JIM D [last name deleted for privacy by Editor]fastener company - DALLAS, TEXAS , US
2003
Ed. note: This RFQ is outdated, but technical replies are welcome, and readers are encouraged to post their own RFQs. But no public commercial suggestions please ( huh? why?).
Multiple threads merged: please forgive chronology errors and repetition 🙂
Need zinc flake coatings with good UV resistance
Q. We are looking for a special type of coat which has a corrosion resistance of 700-800 hours and a coating thickness of 8-10 microns (like Delta-Magni and Dacromet applications). We already have a coating line for Delta Magni but this type of coating offers poor UV protection performance. So we are in search of a different type of coating which has the same application technique as Delta-Magni and Dacromet but has a high UV performance.
Thank you in advance.
Elif K[last name deleted for privacy by Editor]
A. Search the literature and patents after you have an answer from the suppliers of this type of coating.
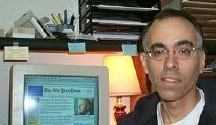

Tom Pullizzi
Falls Township, Pennsylvania
A. Hi, Elif. If you are restricted to applying the coatings via your existing dip-spin coating line then I think Tom Pullizzi is right that you must talk to the vendors you mentioned, and their competitors, about addressing the UV problem. A great list of suppliers of zinc-rich dip-spin coatings has been prepared by Tom Rochester and can be reviewed at dipspincoatings.com^see Ed. note. It includes The Magni Group and Metal Coatings International (Dacromet) which you mentioned, but also Doerken, Sermagard, Zintek and others. Visit Mr. Rochester's page on the subject for contact info; surely one or all of those companies will be highly conversant in the UV issue.
But there certainly are other coatings like galvanizing, mechanical plating, alloy zinc electroplating, and sherardizing / thermal diffusion which may meet your corrosion resistance requirements while having no sensitivity to UV radiation problems because they are inorganic.
Maybe a very thin UV-resistant e-coat clear coating on top of your dip spin coating will solve your problem?
It's fine to want the coating to be thin, but for a first order approximation the corrosion resistance of zinc-bearing coatings is directly proportional to their thickness. The main reason dip-spin coatings tend to be more corrosion resistant than zinc plating is simply that they tend to be thicker. 8-10 microns (.00032 to .0004 inches) is thicker than the typical .00015 to .0002" of commercial zinc plating, but electroplating to 8 or even 25 microns is not a challenge. Good luck!
The following threads may be a helpful start for an evaluation of zinc flake dip-spin vs. those alternate coatings --
24405, "Hot-dip Galvanizing vs. Zinc-rich Dip-spin Coatings"
35049. "JS500 vs. Dacromet"
38226, "Zinc Plating vs. Zinc Flake Dip-Spin Coating"
Luck and Regards,
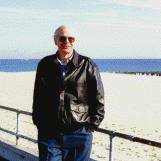
Ted Mooney, P.E.
Striving to live Aloha
finishing.com - Pine Beach, New Jersey
----
Ed. note Aril 2016: The dipspincoatings.com domain is no longer maintained, but you can contact Tom Rochester [of Plating Systems & Technology, a finishing.com supporting advertiser] directly for a new address for that list.
March 29, 2014
A. Dear Sirs
I also think that the UV resistance problem needs to be understood through the failure mode. Supporting images?
Yeah, otherwise dip-spin coating followed by an e-coat of UV resistant clear should be helpful.
Help me about "Dacrotizing"
Q. Please send me full information about Dacrotizing process, notes, problems...
Thanks,
Reza Rafiey2005
2005
A. DACROTIZING® is a process whereby the aqueous dispersion is applied by cold immersion or spray and is therefore free of any risk of hydrogen embrittlement. The coating thus produced is passivated throughout the film and provides high performance corrosion protection.
CHARACTERISTICS:
The corrosion resistance of DACROMET® 500 depends upon the thickness of the coating and is due to the combination of several mechanisms:
- a barrier effect due to the tile-like structure of the film,
- controlled sacrificial protection of the zinc in relation to the metal substrate,
- the film passivation which reduces the speed at which the zinc and aluminium are consumed.
COATING THICKNESS:
Two coating weights are commonly used to meet the automobile industry's requirements:
Grade A : coating weight > 24 g/m", average thickness 5 to 7
µm
Grade B: coating weight > 36 g/m", average thickness 8 to 10
µm
Greater coating weights may be applied to increase the duration of the corrosion protection.
PROPERTIES:
1/ No hydrogen embrittlement
When surface preparation is done according to recommended techniques, the non-electrolytic application of the film does not induce hydrogen embrittlement. DACROMET® 500 is therefore especially indicated for protecting security parts.
2/ Corrosion resistance
DACROMET® 500 meets all automobile manufacturer specifications for the corrosion protection of mechanical parts. It is also very well suited for numerous other applications such as building, civil engineering, railway equipment.
2.1/ Salt spray test (ISO 9227)
> 600 hours (Grade A ) without red rust.
> 1000 hours (Grade B ) without red rust.
No white rust (zinc corrosion) before 250 hours.
2.2/ Salt spray test after 8 hour thermal shock at 260°C:
ditto
2.3/ Cyclical corrosion tests: 3C test
test method: RENAULT D17 1686 > 10 cycles without red rust.
2.4/ Bimetallic corrosion resistance
DACROMET® 500 behaves very well in contact with aluminium and performs as well as other zinc-based coatings in contact with copper, stainless steel or magnesium.
3/ Resistance to automotive fluids
standardised test fuel, diesel fuel, motor oil, organic solvents, cooling fluid, brake fluid: no coating alteration (VDA 621-412).
Immersion in brake fluid for 24 hours at 80°C: no coating alteration.
4/ Ductility
Sufficient for elastic deformations of springs, clips.
5/ Electrical conductivity
DACROMET® 500 is conductive. It allows for use of electrodeposited paints.
6/ Heat resistance
DACROMET® 500 is cured at 300°C, thus providing excellent heat resistance.
7/ Paintability
DACROMET® 500 may be covered by most organic coatings and in particular, those applied by electrodeposition.
8/ Throwing power
The application on parts by cold immersion allows for the total covering of the internal surfaces.
9/ Coefficient of friction on nuts and screws
test method RENAULT 01-50-005 µ average between 0,12 and 0,18
APPLICATION FIELD
When choosing the coating process best suited for a given application, DACROMET® 500 may be used in all industrial areas, for all types of metallic parts.
HOMOLOGATIONS
DACROMET® 500 is specified and used by numerous automobile manufacturers, and many other companies.
APPLICATION
Several application techniques are used industrially by DACROMET® Licensees according to particularly ecological methods specified by DACRAL:
- dip-spin in bulk: the parts are cleaned, immersed in baskets into the DACROMET® 500 bath, spun to eliminate excess material, then dried and cured at 300 °C. The operation is performed at least twice to obtain the desired level of protection.
- dip-drain-spin on racks: the parts are attached to racks. The procedure is the same as for bulk applications.
- Dip-drain: for parts too large to be spun.
- Pneumatic or electrostatic spray or high-speed bell: DACROMET® 500 lends itself particularly well to these application techniques.
DACROMET® is an inorganic coating composed of zinc and aluminum flakes in a binding matrix of chrome oxides. The corrosion resistance performances of DACROMET® are particularly high at low thicknesses (from 5 to 10 µm). DACROMET® is the technological reference in the field of automotive threaded fasteners parts.
The following are the methods used in DACROTIZING® and DACROSEALING® :
1-Dip-Spin Processing
2-Dip-Drain Spin Processing
3-Spray Processing
Hi Hadi. Thanks!
... but Reza also asked for the "problems". So, while sales lit is helpful to part of his question, it isn't the full answer :-)
Another problem is that while company lawyers typically are happy to see glowing testimonials printed on the net, they sometimes make threats if even slightly uncomplimentary postings are not taken down. And then too, there are whole services like reputation.com which promise to rig the search engines so the glowing compliments rise to the top, and uncomplimentary ones are lost in the haystack. So online postings mentioning specific proprietaries tend to be overly favorable rather than neutral.
For these reasons and others, we discourage Q & A's which mention specific proprietaries, and we ask the readers to mentally substitute "zinc-rich and zinc&aluminum-rich dip-spin coatings" for any brand names mentioned. Thanks again for the highly detailed and useful posting!
Regards,
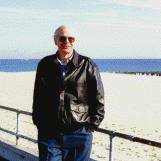
Ted Mooney, P.E.
Striving to live Aloha
finishing.com - Pine Beach, New Jersey
Zinc aluminum flake coating
Q. I would like to see available research work on Zn-Al Flake coatings on steel with respect to corrosion behaviour and their applications.
Bindu H goyal2005
A. We appended your inquiry to a thread on the subject, but perhaps a company that offers the service commercially, like Saify Ind [a finishing.com supporting advertiser], can send you something.
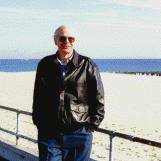
Ted Mooney, P.E.
Striving to live Aloha
finishing.com - Pine Beach, New Jersey
2005
RFQ: We are in process of quoting an assembly where the customer has called out a Zinc Flake coating followed by specific locations requiring an additional 1K-PUR anti chip coating at .5 mm thickness. EAU is 160K.
Stamping/assembly to occur in the southern corridor - Kentucky area.
Thanks
Stamping/Assembly - Bowling Green, Kentucky, USA
September 8, 2009
Ed. note: This RFQ is outdated, but technical replies are welcome, and readers are encouraged to post their own RFQs. But no public commercial suggestions please ( huh? why?).
Compatibility of zinc flake coatings with aluminum
Q. Is this process applied on self drilling screws compatible with aluminium, and does not cause corrosion in aluminium like stainless steel does.
Perry PhippsAugust 9, 2010
A. Hi Perry. Zinc-rich coatings, especially if they also include aluminum, and especially if they are chromated (which is the usual casr) will be reasonably compatible with aluminum.
![]() | But you seem to be implying that stainless steel is highly incompatible with aluminum and is causing galvanic problems, and I don't necessarily accept that premise. Might it be that the self-drilling fasteners destroy the anodizing in that area and the resulting non-anodized area won't hold up regardless of fastener material? You might install a few "extra" self tapping fasteners, back them out and discard them, or insert plastic screws and see whether there is a corrosion problem. Good luck. |
Regards,
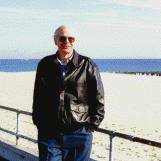
Ted Mooney, P.E.
Striving to live Aloha
finishing.com - Pine Beach, New Jersey
December 26, 2014
A. Hi,
Our company is specialized in metal finishing techniques and have developed Zinc aluminum flake coating chemicals, and we are using same chemicals regularly.
Regards,
adv.
Need a metal finishing line staffed & operated just for you with worldclass supply chain management? Saify Ind [Bangalore]
Q, A, or Comment on THIS thread -or- Start a NEW Thread