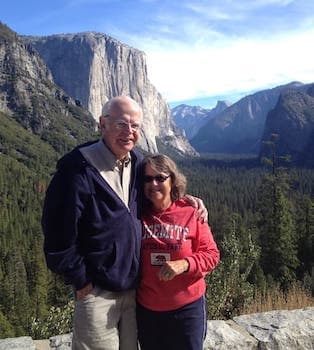
Curated with aloha by
Ted Mooney, P.E. RET
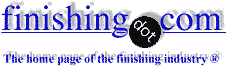
The authoritative public forum
for Metal Finishing 1989-2025
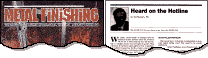
-----
Galvanizing vs. Dacromet
Q. Dear Sirs,
1. I am writing to ask you if galvanized auto parts are poisonous for either workers or people touching them? If yes, why?
2. Between galvanizing and Dacrotizing, which is more economical?
What percent in comparative choice?
Warmest regards,
supplying auto parts - Tehran, Iran
2003
A. Hi, Abdolhossein. Galvanized parts are certainly not poisonous. Feed bins and watering troughs for farm animals have been made of galvanized metal for decades. Similarly, galvanized roofs have long been used to collect rainwater for drinking where water supplies are limited. Although it's not considered best practice today, domestic water pipes were galvanized steel in some areas.
1. Galvanized coatings are basically zinc, which is an essential nutrient, not a toxin. However, galvanized coatings sometimes contain a small amount of lead, and galvanized components sometimes receive a final chromium quench which has some small amount of hexavalent chromium in it, and those are toxic materials.
2. The thicker the layer of deposited zinc, usually the more costly, and the more corrosion resistant. In general it proves most economical to apply thin layers of zinc by electroplating, mid thickness layers by dip-spin zinc flake coatings (Dacromet is the brand name of a proprietary coating of that nature) or mechanical plating/galvanizing, and thick layers by hot dip galvanizing. So hot dip galvanizing is substantially thicker and more corrosion resistant than dip-spin coatings. I think galvanizing more expensive but the dip-spin coatings do involve proprietary supplies, sometimes top coats, etc., so they are not cheap like zinc electroplating.
But many times the choice is not based solely on corrosion resistance and cost, but the specific needs of the component. For example thick hot-dip galvanized coatings can be a substantial problem for small and medium size fasteners because of their serious impact on thread dimensions. The fasteners may require specially cut threads, or skipping the galvanizing on the threads of nuts, etc.
Regards,
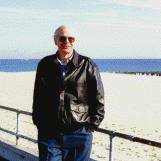
Ted Mooney, P.E.
Striving to live Aloha
finishing.com - Pine Beach, New Jersey
October 20, 2009
Q. I would like to know how the Dacronized finished steel compares to a galvanized steel in the salt environment, i.e., for deck boards along a pier or dock?
Jordan Loran- Annapolis, Maryland
A. Hi, Jordan. I'm pretty sure you mean Dacrotized. The corrosion protection of zinc-rich coatings comes primarily from the thickness of the zinc. Hot dip galvanized zinc coatings will almost always be substantially thicker than the competing technologies, and thus more corrosion resistant.
Regards,
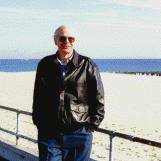
Ted Mooney, P.E.
Striving to live Aloha
finishing.com - Pine Beach, New Jersey
May 31, 2009
A. I would ask the makers of Dacral and Dacromet [Metal Coatings International].
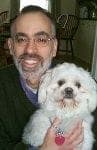

Tom Pullizzi
Falls Township, Pennsylvania
Q. I am a product tester for a company that makes wood products. I only test products that are non-wood though. Many of the products we receive are from overseas, and we have run across some products that are below par. For our purposes, Dacromet coating is preferred. Anyway, we have a company that suggested using galvanized metal, and spraying a "Dacromet" coating on top that they say doesn't need to be cured. Is it possible to use Dacro over galvanized metal? And if so, doesn't it have to be cured to perform correctly?
Dave Au- Brookings, South Dakota, USA
2005
A. Hi Dave. Yes, that does sound wrong to me. They may be talking about a solvent-based zinc-rich galvanizing touch-up paint rather than actual Dacromet.
I was about to suggest that hot-dip galvanizing by itself is the equal in corrosion resistance to any coating (75+ years proven, not conjectured life) so no worries ... but then I realized that the products they are claiming as "galvanized" may be just zinc electroplated rather than hot dip galvanized :-)
Be double careful. Good luck.
Regards,
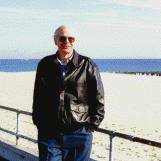
Ted Mooney, P.E.
Striving to live Aloha
finishing.com - Pine Beach, New Jersey
Q. WHAT IS THE NATURE OF COATING IN DIP SPIN COATING PROCESS? IS IT ZINC PHOSPHATE BASE PAINT? IS IT A REPLACEMENT FOR HOT DIP GALVANISING PROCESS ZINC COATING PHYSICALLY AND QUALITY WISE?
DR.DIPANKAR SENRESEARCH & DEVELOPMENT- PLATING SHOP - KOLKATA, India
October 7, 2010
A. Hi, Dipankar. Dip-spin is an application method rather than a type of coating, but I do think the method is used mostly for zinc-rich (and sometimes aluminum-bearing) compounds like Magni, Dacromet, Delta-tone, etc.
There are many ways to apply zinc as a coating, including electroplating, mechanical plating, sherardizing, flame spraying, hot dip galvanizing, spraying cold galvanizing compounds from a rattle can, and applying water-based zinc-rich coatings by dip-spin. The easiest way to look at it, which is somewhat of a simplification but not too far off the mark, is "zinc is zinc", i.e., the corrosion protection will be essentially proportional to the thickness of the coating. Each coating method suits different applications and thicknesses, with zinc electroplating used for the thinnest coatings, galvanizing used for the heaviest, and the others for thicknesses in between.
Good luck.
Regards,
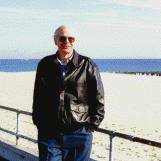
Ted Mooney, P.E.
Striving to live Aloha
finishing.com - Pine Beach, New Jersey
October 7, 2010
A. Dear Mr. Sen,
Cost wise zinc flake coating raw material is 15 to 20 times that of Hot Dip Zinc in India. Unless there are threaded parts we are talking about for which control on the dimensions or COF requirements compel the use of Zinc Flake - I don't see any significant improvement in corrosion resistance to merit a 20 times higher manufacturing cost.
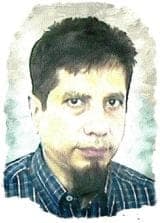
Khozem Vahaanwala
Saify Ind

Bengaluru, Karnataka, India
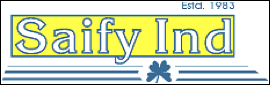
November 24, 2010
My trusted colleague KV has surprised me with that cost comparison. I had been under the impression that, due to the much heavier coating thickness, galvanizing was more expensive.
Regards,
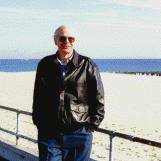
Ted Mooney, P.E.
Striving to live Aloha
finishing.com - Pine Beach, New Jersey
Q. I am looking at buying a boat trailer. One supplier is offering Dacromet Finish for the Axles and Springs. Normally this is galvanised.
Is there any benefit or weakness to the application?
private customer - Sydney, NSW, Australia
August 16, 2011
A. Hi, Joe. My personal opinion is that Dacromet can be a very good corrosion resisting finish, but is not quite the equal of hot dip galvanizing (How can we actually know since accelerated salt spray testing proves nothing for zinc-based coatings, and galvanizing can last 75+ years, whereas Dacromet hasn't been around for a fraction of that time?)
I certainly would not rule out a boat trailer with Dacromet axles and springs, but I certainly wouldn't consider it an advantage over hot-dipping. Happy boating.
Regards,
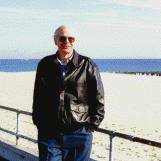
Ted Mooney, P.E.
Striving to live Aloha
finishing.com - Pine Beach, New Jersey
August 16, 2011
Q. What are the visual differences between spinal hot dip galvanizing and Dacromet coating?
Thanks.
- Tehran, Iran
June 2, 2013
A. Hi Hossein. Sorry, I don't know what you mean or intended to say with the word "spinal". Your question may be better handled by hands-on instruction, but you can see some photos on the Dacromet website. In general, Dacromet has a "paint-like" look to the finish whereas galvanizing often has the familiar mottled "frost on a window pane" look, and looks like metal rather than paint. Good luck.
Regards,
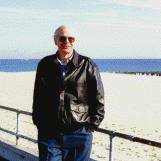
Ted Mooney, P.E.
Striving to live Aloha
finishing.com - Pine Beach, New Jersey
June 3, 2013
Q. Hi,
I am trying to find some authoritative documentation that indicates the rust proofing qualities of Dacrotizing. Does anyone know of any environmental test reports, please?
Ideally I'd like something that makes a direct comparison between Dacrotizing and HD Galvanized.
Until I am convinced that Dactotizing is at least as good as HD [hot dip] Galvanizing I can't recommend it to my customer.
Cheers,
Ian.
- Southampton, Hampshire, UK
June 12, 2013
A. Hi Ian. Dacromet is a proprietary product, not a generic process. Therefore, I think you should contact the manufacturer of the product for case studies, test results, white papers, etc.
I think it is an excellent product, and automobile manufacturers around the world do as well. It's widely used on underbody components I understand.
In fact, though, there is nothing that can be said with 100% surety to be "at least as good as HD galvanizing" for the simple reason that we have structures in existence that were galvanized 75+ years ago. No accelerated test is truly representative, so how can any manufacturer of any coating at all claim performance at least as good as galvanizing unless it was available and applied more than 75 years ago :-)
Regards,
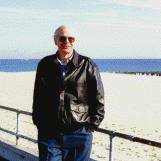
Ted Mooney, P.E.
Striving to live Aloha
finishing.com - Pine Beach, New Jersey
June 12, 2013
Thank you Ted, very wise words.
I have been in contact with NOF Metal Coatings, who have forwarded some information.
Like any coating, the suitability is dependent on the product and environment in which it is to be used. Whilst I don't doubt that it's a good product, we won't be using it on this occasion.
Regards,
Ian.
- Southampton, Hampshire, UK
June 14, 2013
Q. Sir,
Still many types of coating layers are developed in many countries and industries. My question is regarding Screw coating.
Which coating is best for real world test and 1000-hour salt spray test.
Below type of coating.
1. Zinc Flake, 2. Hot Dip Galvanizing, 3. Electroplating, 4. Mechanical coating.
Please suggest best coating for screw.
- Ahmedabad, Gujarat, India
August 12, 2016
A. Hi Harshit. If one coating were best there would not be those four options. There is a lot more to it than just corrosion resistance or salt spray hours: there's appearance, threads not being clogged with drips, freedom from zinc whiskers, hydrogen embrittlement issues, durability against mechanical damage, consistent torquing, etc. Even when you restrict it to "screws", are the screws small enough that bridging of the coating is a big problem? If so, 3 or 4 would be better than 1 or 2. Are the screws very hard, in which case only 1 & 4 would probably be acceptable while 2 & 3 probably wouldn't. Are they in critical components where zinc whiskers might be a problem: if so. 3 is out, and 4 might be. A 1000-hour salt spray test of zinc coatings can be a bad joke, as it can probably destroy a heavy hot dip galvanized finish which would survive a century in the real world.
The best answer is often the old saw "zinc is zinc", which emphasizes the importance of the thickness of the coating over the application method. Electroplating is usually thinnest and hot dip galvanizing the thickest, with mechanical plating/galvanizing and zinc flake in between.
Regards,
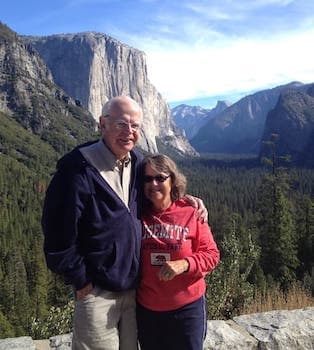
Ted Mooney, P.E. RET
Striving to live Aloha
finishing.com - Pine Beach, New Jersey
A. I have read all the opinions passed by my esteemed colleagues. All are concerned with the corrosion part of the comparative study between H.D.G. process and Dacromet coating process, their coating thickness, etc.
However, one important factor is missing in the above discussion which is of course applicable to high tensile bolts of higher property class [10.9 and above].
Here, H.D.G. is strongly not recommended due to the problem of hydrogen embrittlement manifested through cold cracking of bolts at much lower value of the load than the designed capacity and is very much uncertain to predict.
Technical Director (Structural Engineering Consultant) - Kolkata, West Bengal, India
May 14, 2017
Q. Hello,
We have specified A490 DacRomet coated bolts for a structural tube framing system in Jersey City. They were used in flange type splices of tubular sections as well as gusset plate connections. One and a half years after installation the bolts are rusting. Is there any records of these types of coated bolts loosing their protection due to installation and/or manipulation (scratching of the coating)? Is the coating that fragile?
Baco Enterprises - Bronx, New York
August 21, 2017
A. Hi Elliot!
Were these bolts you mention tested in salt spray chamber prior to be installed? There are many causes for poor adherence and/or poor corrosion resistance in water (as Dacromet) and solvent based coatings.
The bolts should be tested, and if they were, I would say the manipulation did harm the coating as you say. I don't know how the parts were installed, so I can't say more...
If you give us more data, we may help you jump to some kind of conclusion.
Regards,
TEL - N FERRARIS - Cañuelas, Buenos Aires, Argentina
August 23, 2017
August 23, 2017
Q. I email some photos showing the application:
Baco Enterprises - Bronx, New York
A. Hi Elliot!
I would say that the coating was damaged when the bolts were installed. Organic coatings like Dacromet don't have the self repair capacity of a hot dip galvanized bolt, and when a bolt is damaged, corrosion may get through.
For this usage, I (and many others may say the same) recommend hot dip galvanization bolts and nuts. Lab results may say differently, but in practice damage in the bolts thread is almost impossible to avoid.
Best of lucks!
TEL - N FERRARIS - Cañuelas, Buenos Aires, Argentina
August 29, 2017
A. This is a problem of spin coating ... it will be thinner on the edges and you have the rusting on the edges. Use Hot dip Galvanised fasteners only.
Vishal AgarwalINDANA STEEL PVT.LTD - kolkata,Westbengal, India
October 29, 2017
Q. Hi All,
How is Dacromet/Magni 565 compared to HDG in terms of protection Hours/Cost?
Thank you!
- Memphis, Tennessee, US
November 7, 2017
A. Hi Mathew. Re. "Hours?": the problem is that salt spray hours are not at all a valid way to categorize a coating like galvanizing. Over the years the zinc reacts with carbon dioxide in the atmosphere, forming tough glassy corrosion products which seal the remaining raw zinc away from the environment and slow corrosion to a crawl. Under the right conditions, galvanizing can last 75 years, even 100 years or more. But in a salt spray chamber, sacrificial coatings like galvanizing dissolve rather rapidly and fare poorly. Zinc rich dip-spin coatings can be a fine finish, but they are no match for hot dip galvanizing for longevity, and even if someone claims that they are, how are they going to produce a 100 year old example to prove their premise?
As for cost, our learned friend Khozem said that in India in 2010 dip-spin was significantly more expensive than galvanizing; despite his hundreds of knowledgable responses in this forum, I don't think that is true in America in 2017. Further, abstract comparisons can't take us very far anyway; we need to know the type of parts and application before much can be said. Good luck.
Regards,
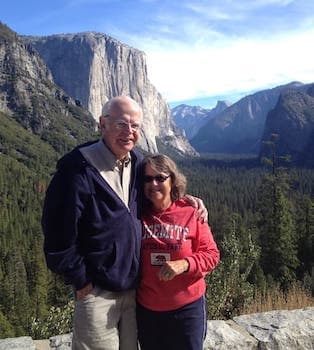
Ted Mooney, P.E. RET
Striving to live Aloha
finishing.com - Pine Beach, New Jersey
November 2017
Q. Hi,
We want to commission the manufacturing of litter bins that will be used outdoors at a UK environment with an expected life 15 years. It was suggested to hot dip galvanized the sheet metal and then powder coat but I am worried about been able to obtain a nice and smooth finish which would have been the case if we are to use zintech. What do you suggest?
Kyprianou Group - Larnaca, Cyprus
December 6, 2017
A. Hi Kyriacos. I don't know what "zintech" is, and Google didn't help, but I'm guessing it's a trade name for zinc-rich dip-spin coatings. So we appended your inquiry to a thread on that subject. Dip spin coatings followed by powder coating are probably adequate for 15-year life even in a tough environment. But they are probably not the equal of hot-dip galvanizing. Good luck.
Regards,
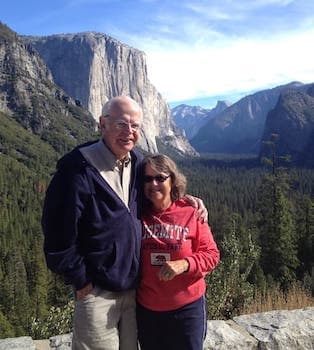
Ted Mooney, P.E. RET
Striving to live Aloha
finishing.com - Pine Beach, New Jersey
December 2017
Testing of hot-dip galvanized steel coils
Q. Hello Ted,
Thanks for the last advice.
We are now looking to buy galvanized coils from China and more particularly dx51D (1.0226) z100 with zero spangle. Quantity around 100 tons.
My question is how and what tests do we need to carry out prior to delivery on the coils so that we know that we are buying something of good quality or how do you verify that the supplier is of good standing?
Kyprianou Group - Larnaca, Cyprus
February 13, 2018
Ed. note: This RFQ is outdated, but technical replies are welcome, and readers are encouraged to post their own RFQs. But no public commercial suggestions please ( huh? why?).
A. Hi Kyriacos. Your February 6 RFQ for 150 tons of this stuff as posted on www.steelnumber.com popped right up as the first hit on Google, so the world knows you're looking for it. I would say that the first step is securing the standards for DX51D steel and for Z100 galvanizing so you are absolutely clear about exactly what you are specifying.
Sorry, I don't know enough about inspection of galvanized steel to recognize good quality, nor advise what tests should be run to monitor for it. Hopefully another reader can offer general hints or direct you to a published or web article which addresses the subject. This public forum can often answer quick and limited questions, but when a posted question is broad enough to resemble a consulting assignment, the answer is sometimes: "Please consider retaining a finishing consultant"; I recognize that 100 to 150 tons of galvanized steel can't justify a large consulting expenditure so start with getting the specs. Best of luck.
Regards,
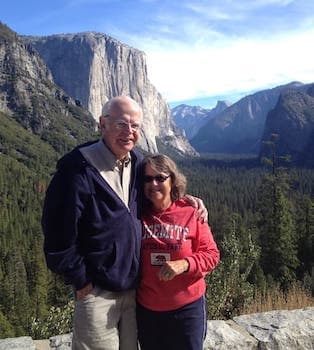
Ted Mooney, P.E. RET
Striving to live Aloha
finishing.com - Pine Beach, New Jersey
February 2018
Switch fastener from zinc flake to "galvanic zinc coating"
Q. Hello, we have a sensor application in the wheel suspension of the car. The sensor is fastened by using a class 8.8 screw with zinc flake coating (currently). The fastening screw is inserted into a stainless steel sleeve (X5CrNi18-10; USA: 304, 304N) that is an overmolded component of the sensor. The sensor is fastened to the appropriate part in the suspension which is from AlSi7Mg0.3 alloy. Our customer wants to change the coating of the fastening screw from zinc flake coating to galvanic zinc coating. My question is, is this change feasible from point of view of galvanic corrosion? Or are these two coatings equivalent in this aspect? Is there anything else why this change might not be feasible or not proposed? It is obviously an outdoor environment with high humidity and presence of salt.
Zoltan Szabo- Veszprem, Hungary
February 28, 2018
----
Ed. note: We don't know whether 'galvanic zinc' means zinc electroplating or hot-dip galvanizing, Zoltan. Please clarify.
By 'galvanic zinc' I mean zinc electroplating. Thanks for pointing that out.
- Veszprem, Hungary
March 5, 2018
A. Hi Zoltan. Zinc electroplating, or even zinc alloy plating, is not the equal of zinc flake coating in corrosion resistance, and it will require baking for hydrogen de-embrittlement. If it's a small screw, perhaps stainless steel would be better.
Regards,
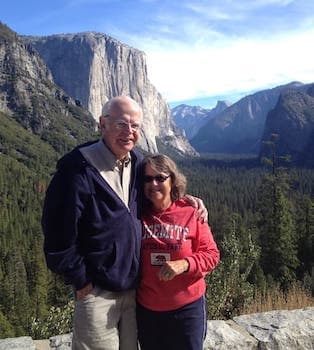
Ted Mooney, P.E. RET
Striving to live Aloha
finishing.com - Pine Beach, New Jersey
March 2018
A. Normally in situations such as this the coating specification is set by the automobile manufacturer.
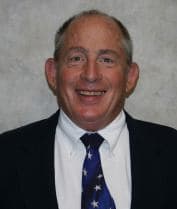
Tom Rochester
CTO - Jackson, Michigan, USA
Plating Systems & Technologies, Inc.

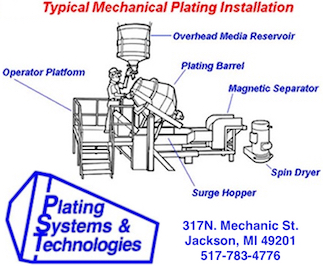
March 4, 2018
Q, A, or Comment on THIS thread -or- Start a NEW Thread