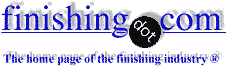
-----
Chrome Plating on Fiberglass
Current question and answers:
January 23, 2022Q. / RFQ: I have been asked by a client to make a head mask; for weight purposes, I was thinking of making a rubber mold, then using fiberglass and resin to make the full head mask.
1st picture shows the shiny gold finish which is sought, 2nd picture shows the full head mask which is wanted
I am trying to have it gold plated. I am having trouble finding companies, and it needs to be durable for the artist to wear on tour. I know how to electroform and plate metals as I am a metalsmith artist. I would like to find a company that could gold electroplate this mask. Is it possible to do this on a fiberglass and resin mask? I have used conductive paint but the companies I'm finding only do large quantities for other companies in the industry. One plating company said it had to be metal to plate on. I'm not sure I can electroform something so large. Is it possible to mix a copper powder and resin material? Would that be conductive for plating? If so what would be the ratios of metal copper powder to resin? Any company that could do this plating I would love to know about or is it possible to do myself?
Sydney Pener- Kansas City, Missouri
privately respond to this RFQ
Ed. note: As always, gentle readers: technical replies in public and commercial replies in private please (huh? why?)
A. I think that you can electroform or electroplate (2 different processes!) your mask. It is possible but expensive. If you want to electroform your mask you must make negative mold of it first (silicone based molds are contemporary solution). After that step you must make that mold conductive (fine bronze or copper powder are simplest way to do that, but you can use graphite or even chemical silver or copper plating). Then you can use any electroforming electrolyte, cheapest is copper based, and after copper plating is done you can gold plate it.
P.S.: A fine description of that process you can find in Oppi Untractht's book Jewelry Concepts and Technology
Also see en.wikipedia.org/wiki/Electrotyping#Electrotyping_in_art
Hope it helps and good luck!
Goran Budija- Cerovski vrh Croatia
February 14, 2022
⇩ Related postings, oldest first ⇩
Q. I need to electroplate some of my sculptures made from fiberglass. I need to know the different conducting paints available in the market. I also need to know the process to be used to electroplate the fiberglass sculptures.
Expecting a reply. Thanks in advance
Sushil Saraf1998
A. Hello, Sushil. We have a FAQ on Plating Non-metallic Materials. Three common metallization approaches are:
1. - silver paint (or copper, graphite, or other conductive paint) paint;
2. - two-part silvering process which uses a soluble silver salt plus a reducing solution as in mirror making; and
3. - catalyzing with a palladium chloride salt (the most complicated and robust, and used for automotive exterior parts).
Your first job is to decide which approach is most appropriate for your product. One thing not to be dismissed is that it may be necessary to lacquer or otherwise seal the fiberglass if the resin system isn't suitable for immersion in electroplating solutions. Good luck.Regards,
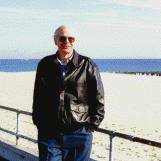
Ted Mooney, P.E.
Striving to live Aloha
finishing.com - Pine Beach, New Jersey
1998
(to help readers better understand the Q&A's)
This thread introduces several different concepts. Hopefully this sidebar will help readers not get lost ...
First, please recognize that not every shiny plastic surface is real chrome plating. One alternative to chrome plating for strictly decorative use is painting the plastic with very shiny, or "chrome look" paint -- and both real chrome plating and "chrome look paint" are discussed on this page.
Secondly, even when we are talking about real chrome electroplating, there are several alternative procedures to make the plastic conductive (as mentioned in the first answer above). The simplest ways may be fine for a sculpture kept indoors, but for the robust needs of an automotive grill (blazing hot sun to frigid winters, road salt, gravel impacts, carwash brushes, multi-year guarantees) rather exotic metallization is required.
Q. I own a replica Ferrari Dino which is supplied with fiberglass bumpers. I need to find a method of chrome plating these items to make the vehicle look more like the original.
Thanks for any help.
Derek E [last name deleted for privacy by Editor]- London, England
2001
A. Hi Derek.
It is obviously possible to chrome plate fiberglass (please see our FAQs on Understanding Chrome Plating in addition to the Plating Non-metallic Materials previously mentioned). But it can prove impractical to affordably electroplate tightly adherent nickel-chrome plating on a onesy-twosy basis when the plater has no control over the selection of the type of resin or the manufacturing process. Letter 1020 explains the production steps involved in OEM-quality chrome plating of plastics.
All things considered, I think "chrome look paint" is a more promising approach for these replica cars. Good luck.
Regards,
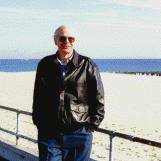
Ted Mooney, P.E.
Striving to live Aloha
finishing.com - Pine Beach, New Jersey
Multiple threads merged: please forgive chronology errors and repetition 🙂
2002
Q. I need to try to "chrome" plate some fiberglass bumpers for a custom sports car I'm building.
I've read in the FAQ and archives about the difficulties of plating large pieces of plastic, but I'm hoping to find some workable method.
Unless I get better advice here, I am planning to start with my highly polished, waxed fiberglass molds, dust the molds with conductive copper powder, then mix more copper powder into a polyester 2-part primer/gelcoat, catalyze and spray that into the molds, and embed copper wire leads before it sets up. Then lay up polyester resin & fiberglass as usual to the appropriate thickness. Then remove the bumpers, trim the edges, touch them up with conductive copper paint, and deliver to the plater for acid copper plating, followed by nickel and maybe chrome.
The bumpers will be about 48" long and 5" wide. Can such a long item be made conductive enough to plate? I am hoping that by embedding the conductive copper powder into surface of the fiberglass, the amount of current necessary to plate the chrome won't damage the surfaces. How do I calculate how much powder to use? Will one copper wire at each end be sufficient or do I need copper wires at intervals? What size wire? What thickness of copper plate needs to be built up to make the bumper sufficiently conductive? Would tinning help?
Any advice or alternatives would be much appreciated.
Tom Haugen- Los Angeles, California
A. Dear sir,
Plating of fiberglass is not difficult like you said. Here in Egypt we made a collection of king TUOT ANK AMUNE from reinforced [polyester and fiberglass]. We plated it gold over nickel and copper.
RAAFAT ALBENDARY- CAIRO, EGYPT
2002
A. Hi. I deeply admire Raafat's outstanding knowledge of metal finishing, and greatly appreciate his yeoman work in answering questions here. But I would remind him and Tom and the readers that a big problem with plating on automotive plastic can be securing adequate adhesion. It is one thing to plate a piece of statuary, but it is something else entirely to plate a bumper and expect it to survive the contraction of arctic cold, the expansion of blazing desert sun, the abrasion of carwash brushes, the impact of gravel strikes, etc. for a decade or more ...
For this reason, no car manufacturer in the world starts with copper paint or any other paint, but with electroless nickel plating precipitated by palladium seeds imbedded in spongey etched plastic. If Tom's car will only appear at car shows in exhibition centers, that's one thing; if he wants it to survive something approaching real automobile use, that's another :-)
Regards,
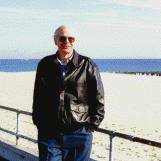
Ted Mooney, P.E.
Striving to live Aloha
finishing.com - Pine Beach, New Jersey
Q. I would like to know how to make a graphite conductive layer so I can plate fiberglass.
Ed Schusterhobby - LA, California, USA
2004
A. Hi, Ed -- graphite may not necessarily be the best route to plating fiberglass --but our FAQ on metallizing non conductive articles is a start.
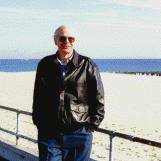
Ted Mooney, P.E.
Striving to live Aloha
finishing.com - Pine Beach, New Jersey
2004
A. You can use graphite based spray (Maver is just one of brands; a can cost 'round six USD)! Good luck!
Goran Budija- Zagreb ,Croatia
2004
Q. Would Maver work to make plastics conductive to plate over?
Davie Scott- Scotland
2007
A. That's what Mr. Budija claimed, Davie, and I have a reasonable amount of confidence in that based on the generally high quality of his postings. Good luck.
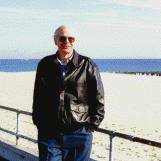
Ted Mooney, P.E.
Striving to live Aloha
finishing.com - Pine Beach, New Jersey
2007
Q. The reason I asked is I have a large amount of graphite that I have experimented with and I have never been able to make a part conductive I have also tried copper conductive paint and a tin dip with no results. I should mention that I am at the moment Brush plating and I know that some conductive substances that work with tank plating won't work with brush plating.
Has anyone here ever had any success with graphite or graphite when brush plating as a lot of plating companies recommends it.
- Scotland
2007
A. That's a brand name that isn't familiar to me, and graphite probably wouldn't be my first choice for metallizing (conductive paint from Acheson, or a two-part silvering solution might be better choices). But brush plating equipment suppliers like Gold Touch [a finishing.com supporting advertiser] can probably answer your question. Good luck.
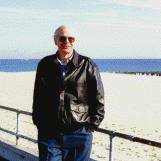
Ted Mooney, P.E.
Striving to live Aloha
finishing.com - Pine Beach, New Jersey
2007
Q. Hi,
I have recently been interested in learning more about electroplating, and specifically for prop making. Due to safety concerns, many events do not permit Weapons or props made from metal, and so I have been searching for ways in which to electroplate props made of fiberglass/carbon/resin.
My main concern is the Current and Voltage Requirements per surface area that would be required in order to electroplate these pieces which will be predominantly Over-Sized swords with a surface area of up to 32 sq feet. If it is ridiculous to put together a system that would cover that much area I'd like to make my mistake before I purchase the components.
I am entirely new to the concept of electroplating though I understand that the current requirements might also vary by the surface material as well as the plating. I foresee predominantly using chrome, nickel, and tin for the plating material
Thank you for your responses,
College Student, Hobbyist - Harrison, Tennessee, United States of America
February 19, 2013
A. Hi Etienne. Considering that you are only going for the look of metal, I think you will find today's "chrome look paint" entirely satisfactory and much much easier and much less hazardous than real electroplating. Good luck.
Regards,
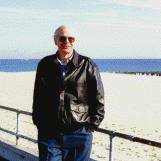
Ted Mooney, P.E.
Striving to live Aloha
finishing.com - Pine Beach, New Jersey
February 21, 2013
A. I've got two pieces of advice to throw in to this discussion.
1. Materials selection.
If you're going for a metallic look, use mylar or some other metal looking plastic or foil for your final coat on the finished piece. There are a great many types of plastics that can be used in lieu of plating for similar visual results.
2. Conductive coating of non-metallic objects.
I've had good results from using zinc paint for my initial coatings over non-metallic objects. A word of advice though, there is a reason such is not industry standard, it's not going to hold up as well as a professional plating job.
- Boone
February 24, 2013
Q. Dear Mr. Mooney
Would you please clear what is exactly Palladium to sensitizing the base coat?
And would please inform me what is the base coat for silvering plastic the best.
Amir
computer company - Dubai Emirate
October 20, 2013
October 23, 2013
A. Hi cousin Amir. If you can present the details of situation, I am sure we can help you! But I must apologize that little progress will probably be made here without you providing quite careful details ... because plating on plastic fills many books, and "chrome-look paint" has nothing to do with electroplating, and the techniques used by sculptors have nothing in common with those used by car makers -- but I'll try :-)
Palladium sensitizing may be vital to your needs or completely irrelevant, as there are many different ways to metallize plastic -- but it is almost universally used for automotive quality nickel-chrome plating of exterior plastics such as grills because the adhesion is spectacular, and the adhesion of other methods is usually questionable.
Palladium is a precious metal, element no. 46. But in this context we're talking about palladium chloride, a liquid. Usually it's bought from a metal finishing process supplier as part of the whole pre-plate cycle, rather than made up from raw chemicals by a plating shop because there are many steps in the preplate cycle, and the supplier will not take any responsibility for your palladium chloride to work after their etch step, or for their electroless nickel process to work on your palladium chloride.
After the plastic is suitably etched, so that it is spongy, it is immersed in tin chloride followed by this palladium chloride solution (or in some cases, mixed into it). The absorbed tin salt causes the palladium to precipitate as metallic "seeds". In the simplest theory, the plastic is then immersed in an autocatalytic electroless nickel solution, such that the palladium "seeds" initiate the catalytic deposition of the electroless nickel layer. But the various proprietary solution providers often suggest additional steps such as immersion in ammonium bifluoride accelerator. After electroless nickel, the item will be copper electroplated, semi-bright nickel plated, bright nickel plated, and chrome plated.
If I am correctly guessing at your situation, though, palladium has nothing to do with it, as it plays no part in "chrome-look" paint, which your other sentence seems to be talking about.
Chrome-look paint is also highly proprietary and involves the three general steps of
1). application of a smoothing organic base coat,
2). either a two-part silvering step or the deposition of a layer of tiny properly aligned aluminum flakes,
3). a hard UV-resistant top coat.
The general order and intention of the steps is widely known, but the details of how to best formulate and apply each layer naturally includes trade secrets. Each supplier will have their own tricks developed through years of research and trial & error. Nothing prevents you from trying to formulate the layers yourself, but when you ask for "best", you are asking people to give you the product of their years of research efforts for free; and, sorry, but that's probably not going to happen :-)
But best of luck.
Regards,
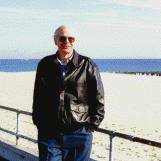
Ted Mooney, P.E.
Striving to live Aloha
finishing.com - Pine Beach, New Jersey
Q. I have a customer wanting some fiberglass parts chrome plated. I do run a full polishing and plating shop. I need some information on type of clear to use and where to get it from. As well as copper bearing paint to apply over clear so I can then acid copper plate.
Gary DuBois- St. Paul Minnesota United States
May 13, 2020
A. Hi Gary. Hopefully someone knowledgable on the best base coat and conductive paint will answer you here. The only thing I can add is that fiberglass isn't ABS, and copper paint isn't OEM-quality metalizing. As an accomplished chrome plater with a good reputation you'll want to be careful about managing your customer's expectations for the long term durability of chrome plating onto copper paint on fiberglass.
Regards,
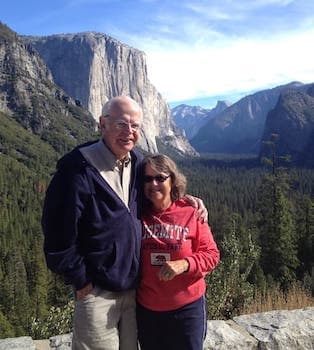
Ted Mooney, P.E. RET
Striving to live Aloha
finishing.com - Pine Beach, New Jersey
May 2020

Q, A, or Comment on THIS thread -or- Start a NEW Thread