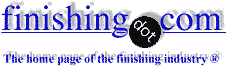
-----
Tumbling/Polishing/Vibratory Finishing vs. Electropolishing of Titanium
Q. I would like any information on the best methods of polishing Titanium. Please include procedures, tools, and abrasives or compounds used.
Kurt Hauswirth- Islip New York
1998
1998
A. Kurt:
A nice mass finishing process for Titanium is available from REM Chemicals, Inc. in Southington, CT. It is a vibratory process (TIMIL) that utilizes a proprietary chemical compound to rapidly refine surfaces ending with very low Ra surface values. It is successfully in use to refine Titanium turbine blades and other engine components, surgical implants and golf clubs to name just a few. Most installation use standard vibratory equipment, high density non-abrasive media and of course, the magical chemical compound.
I hope this is useful and best of luck in your search for information.
Bill
A. Hi Kurt. If you can give us an idea of the size of the parts, production rates, and degree of polish necessary -- so that we can dismiss some swaths of alternatives like automatic buffing machines, electropolishing, manual deburring with a Dremel tool, and stuff like that -- I think we can present some alternatives for your consideration. In the meanwhile ASM Metals Handbook Vol. 5 has some concise info on different approaches for different situations but emphasizes that, regardless of method, you'll probably need multiple stages (you need fine abrasive as the last step, but getting from rough to fine with a fine abrasive would take forever). Good luck.
Regards,
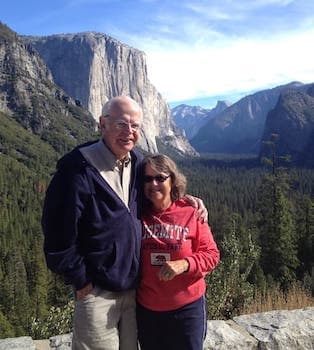
Ted Mooney, P.E. RET
Striving to live Aloha
finishing.com - Pine Beach, New Jersey
Multiple threads merged: please forgive chronology errors and repetition 🙂
Seeking Titanium Surface Finishing
⇦ on eBay or Amazon [affil links]RFQ: This is both a RFQ and a general question. We have some welded titanium parts that need a nice surface finish. In the past we have used glass bead blasting to put both a smooth finish on the part and for the improvement in fatigue characteristics. We recently switched vendors and our new vendor cannot supply a glass bead finish. The best they can do is a rough brushed finish. So at this point we need to find a finisher to provide a similar quality finish.
I have considered ball burnishing the parts instead. This seems to me like it would be a more automated process, and therefore less expensive. Though I suppose there are ways to automate the bead blasting too. So the general question is: What factors affect the pricing for different finishes, i.e., labor, cost of machinery, degree of automation, etc.
I would like to have a better understanding of how different finishes (and levels of the same finish) affect the price. If you can provide a finish that is uniform and smooth - say somewhat satin or better,we would be interested in receiving a quote from you. These parts are welded titanium tubing, total size fits within a 2"x2"x7" envelope (it is essentially 4" of 1 5/8" tubing with fittings welded on each end. This lot is about 400 pieces, and there will be additional regular production runs in the future.
cycles - Sunnyvale, California, USA
2001
Ed. note: This RFQ is outdated, but technical replies are welcome, and readers are encouraged to post their own RFQs. But no public commercial suggestions please ( huh? why?).
A. A couple of thoughts. You never did mention a specific surface finish except nice. If you were getting your parts with a blast finish the RMS was probably around 25 or higher. If you are looking to mechanically surface harden parts shot peening is probably about the best, which is blasting with steel shot.
From your description of your part, peening might be possible and would give you a brighter appearance than glass bead. Then again, another good surface hardening system is a mass finishing system using steel ball media. The latter will not improve your RMS much without a cut down or deburring step first; however, a 2 step process would probably be the best hardened surface finish and could achieve maybe a 12-14 RMS.
The amount of parts you mention probably would not justify a large deburring or blasting system alone. However, a 1 cu.ft. vibratory mill plus ceramic and steel media can do the job for under $2500.
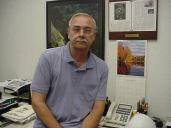
AF Kenton
retired business owner - Hatboro, Pennsylvania
2001
Best media for tumbling titanium
Q. I am vibratory polishing Ti 6Al4V Eli, and I am looking for the best media to de burr, and then end with a mirror finish, can someone please advise me on the correct products, as I am not having luck with current ceramic media. Is stainless shot good to use, or should it be tumbled dry alone for part to part burnishing?
Please help.
- Copenhagen, Denmark
2001
A. Ryan,
I just ran into problem with another customer concerning titanium. The biggest problem we had to over come was the roughness of the existing surface finish or profile. The raw material looked like a sand blasted finish. That means that the RMS was well over 75 or 95. That's rough. I tried an aggressive vibratory mill for over 96 hours and still couldn't get the surface finish within the polishing tolerances of 16 to 18 RMS. The only way we succeeded in getting a mirror finish was to go to a high energy centrifugal system. Even was a 3 step process and took over an hour for each process. Parts looked beautiful but this took a lot of time. If you can improve the surface finish by wheel or belt systems down to at least 35 RMS, you can significantly reduce over all finishing time.
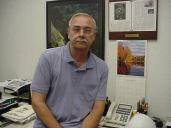
AF Kenton
retired business owner - Hatboro, Pennsylvania
2001
A. I have run across companies that are achieving mirror finishes on titanium from rough castings and they are using a chemical accelerator in a two step process. The first step is to cut down the rough surface with the acid accelerator and then a chemical burnishing compound is used to achieve the mirror finish. This process still takes several hours to do in a vibratory machine and the chemicals must be flushed between the two steps. The described process uses a non-abrasive, high density ceramic media to scrub away at the surface of the metal that has been softened by the chemicals.
Arnold Walker- Independence, Kentucky
2001
Q. Hello Mr. Walker!
Do you know what kind of acid accelerator that is used for Titanium vibratory process? I tried with a regular accelerator (for carbon steel) on Titanium, but it didn't work. Please advise!
Thank you in advance,
- Garland, Texas
2005
Mirror finish on cast titanium?
Q. In my free time I like to produce titanium jewelry(generally grade 23, 6AL/4V ELI), and have recently been looking into titanium cast components to speed up my creation times... The problem I am having is discerning a finishing method for working with cast titanium. Right now finishing is primarily done with sanding/polishing/buffing... But if I am to switch over to a more complex cast titanium part, I know I will encounter a much harder casting surface outer layer and surface areas that cannot be reached with conventional hand finishing means... So, my question would be, before I spend $600+ US on a casting run, what are my options for producing a smooth surface with a mirror finish in titanium? Keeping in mind that this is hobbyist work, done at home, and although I don't mind working with chemicals, I would like to avoid anything particularly life threatening...
Jason Klymjewelry/medical - Winnipeg, Manitoba, Canada
2003
A. Not sure if it would work for your type of designs but I use a vibratory tumbler on our jewelry (titanium, stainless steel, brass, aluminum etc etc) and it works very well. Mirror polishes are easy and much less time consuming. You will need a "jewelry" type setup not a machine shop setup. Most machine shops just tumble to deburr. Jewelry setups work down to a rouge. The abrasive media lasts years..our setup cost about $500 altogether and other then buying fresh rouge its all lasted for 7+ years, and we tumble on average 2,000 earrings at a time.
Jason Aube- Flint, Michigan
2003
A. If you wish to try polishing - ref a book. Please read MSDS first 6% HF BY WEIGHT + 6% water + 88% ethylene glycol. Room temperature or around 40 °C 8-11 A/sq dm but not less than 5.4 A/sq dm. Good luck and TAKE CARE WITH HYDROFLUORIC ACID .
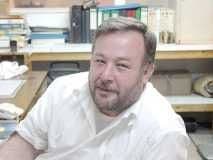
Khair Shishani
aircraft maintenance - Al Ain, UAE
2004
Titanium tumbling media for 6 RMS finishing
2004Q. We are a small prototype low/medium volume company with lots of experience machining industrial metals and parts. We are equipped with both a CNC mill and lathe and can produce low/medium volume of machined products for distribution.
At this point though, we would like to add to our area of distribution to a new consumer base with metal sculpture, jewelry, art, etc. We can specialize in titanium goods to the general public, however we need to find a way to mass finish titanium with a variety of finishes, including a quality mirror finish (#6 RMS or better).
Our current equipment includes a small barrel rotary tumbler (non-vibratory) and media which gives us an attractive matte finish,
but we need to find a tumbling media to give us the desired mirror finish.
If anyone has finishing advice as well as suggested media for successful tumbling, we would be most appreciative.
industrial manufacturing - Bay Point, California, USA
A. Looking at the visuals posted you have a couple of problems. You can achieve a shiny part and still be rough per 2nd visual. The roughness of the parts must be refined and will probably require multiple steps. Unless you have plenty of time on your hands, your barrel system won't get you the 6RMS results you are looking for and vibratory is marginal for 40 hrs or more. Most good companies who sell or process parts will run sample parts and recommend media, time and equipment, including us. Cost is another factor.
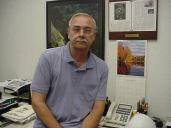
AF Kenton
retired business owner - Hatboro, Pennsylvania
2004
A. Sir,
You can try a centrifugal finishing machine for your components. Time required in the same is very less and for your components and the finish you want can be easily achieved. The process would be 2-3 step process.
Regards,
Finishing Machines - Thane, Mah, India
2004
How to get a better finish after polishing titanium medical implants
Q. We are having problems getting a good finish on titanium implants.
Dave MrakMedical implant mfg. (joint replacement) - Port Huron, Michigan, USA
2007
A. Titanium is a difficult metal to polish. It can be done in many ways; however, you are normally talking about long time cycles. Most of the samples we have run have been in high energy centrifugal systems. The cost of this equipment is relatively expensive. It can be done in vibratory systems but you a talking 24 hour cycles or more. The condition of the raw material is also very important. In most cases you need at least a 2 or 3 step process. If you need more specific info get in touch.
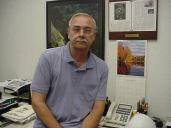
AF Kenton
retired business owner - Hatboro, Pennsylvania
2007
A. Dave, please tell us what you are doing, as it's hard to propose much useful with little to go on. We could say "try increasing the process time by 50 percent" as that is sometimes the answer -- but we don't have any info to tell us if such advise is actually helpful. Thanks.
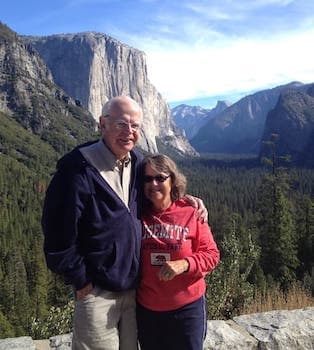
Ted Mooney, P.E. RET
Striving to live Aloha
finishing.com - Pine Beach, New Jersey
2007
2007
adv.
Titanium implants can be easily electropolished by safe simple to handle method in environmentally safe solution. There are no problems in receiving the same rate of removal during continuous polishing one load after another. No burrs, no uneven material removal, no additional passivation afterwards, no surface contamination with abrasive materials. Contact us for more information.
Anna Berkovich
Russamer Lab
Pittsburgh, Pennsylvania
Dirty Layer on Anodized Titanium?
Q. I have successfully achieved alkaline anodizing of titanium according to the AMS 2488d. but I am having a white like layer on the top of the coating which causes dirty look. how can I get rid of that dirty layer?
My bath is free of any oil or oil like contaminants. I have tried polishing with buffing wheel (cloth) and reached a good result but it is not suitable for industrial level usage. I have got also a tumble polishing machine(barrel polishing machine) here. I have used alumina balls and silicon carbide media but they have failed.
I need your suggestions.
Thank you very much
student - Karlsruhe, Germany
2007
Vibratory tumbling of Ti-6-4 plate coupons
August 3, 2015Q. Hello,
I am doing my masters in fatigue of titanium. I need to polish my samples down to a mirror finish (5 micron finish, peak-to-peak). The samples are hourglass plate specimens that are 2.00" x 0.75" by 1/16 thick
I am currently using a Vibratory tumbler (Lyman tumble-vibe 5) to do batches of 10 samples per shot.
Every step I extract my samples from the tumbler and they are evenly covered by a grey matte film that lightly attached to the metallic surface. Its is non soluble and will no be removed by ultra-sound bath. Although its is very thin and is quickly removed when lapped on 600 grit paper.
I use alumina compacts for first step deburring and follow with stainless steel shot and varying degrees of SiC grit (240, 600) and final pre-polish is 15um alumina powder. always cycled in water and soap.
1. Has anyone encountered this problem in tumbling?
2. Is it specific to Titanium?
3. What are my options for keeping this layer off of my samples and ending up with exposed polished metal surface at the end of each tumbling cycle?!
4. I also have a hard time getting the machining marks off of the samples in the first deburring step (I cycle in the ceramic for 48 hours!!!)
masters student - Montreal
A. Titanium is an SOB to finish. #1 The machine you are using is a low energy system and does not transmit a lot of energy to the mass, so you have to make up for that with time. Maybe 24-48 hours or more for first step. If you are starting out with flat parts, I suggest you use a 3/8" triangle of either a medium of coarse composition with a slightly acidic deburring compound. You need a flow though liquid system to eliminate film. If you can still see lines after the first cycle, you may want to follow up with a fine comp of the same size. A 2-step process might get you down to about 12-14 RMS. You may require a 3rd step fine abrasive to get down to an 8 RMS. Not sure if this is fine enough, but last step should be dry organic polishing media. This can be a 2-step process as well.
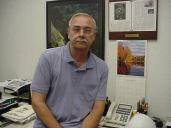
AF Kenton
retired business owner - Hatboro, Pennsylvania
August 4, 2015
A. Benjamin,
Titanium is hard to simply polish mechanically - the surface is soft and during vibratory finish the polishing media is incorporating into the titanium surface. Experienced polishers use chemical-mechanical polishing, with final etching-cleaning of the surface from polished particles. This process require use of hazardous chemicals.
Another option is to electropolish your samples.
adv.
You can send them to me for electropolishing job. Please contact me directly.
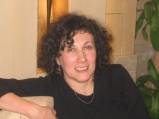
Anna Berkovich
Russamer Lab

Pittsburgh, Pennsylvania
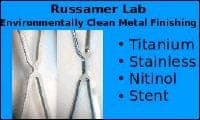
August 6, 2015
A. In my 25 years of finishing metal for the implant industry, no tumbling process can produce a mirror finish on titanium. Is has to be a hand buffed final. Tumbling can get it very close, but I need an RMS 4 finish and tumbling can't do that to titanium, from what I've seen with many other manufacturers. It works on SST quite well though. I'd like to see a process that CAN produce RMS 4-10 on titanium of anyone has any proof that it exists.
Jeff Swayze- Kelowna BC Canada
January 20, 2019
Want beadblast look on Titanium from tumbling or vibratory finishing
Q. Greetings,
I am currently using a bead blast on small (2-3 inch) titanium parts to obtain a consistent, matte finish. The purpose of the finish is purely cosmetic, and I have no desire to increase the finish beyond what the bead blast offers. I have both vibratory and rotary tumblers available and would like advice on specific media to use in either to mimic the bead blast finish on the parts so as to finish them en masse. The parts have already been de-burred and have clean edges. I've tried running the beads in the vibrator for several days, but I think I may need something with a bit of teeth.
Thanks
- Mobile, Alabama
November 8, 2019
A. Hi Tom,
It all depends on complexity of the titanium parts. Mass tumble does not work when titanium parts are of complex forms.
We used to buy Grainger glass beans buckets. Under microscope the beans are of equal rounded shape. They provide good matte finish. It takes about 30 seconds on each part to process at a distance of about 3 inches. The cheaper beans from some vendors can cause sparks and can damage the titanium surface. If you look under microscope, you will see that such cheap beans can have broken glass pieces with sharp edges. This is NO-NO for soft titanium surface.
Later we developed special regimes for titanium electropolishing that create dull surface and at the same time increase surface smoothness. The surface is surgically clean afterwards.
By using electropolishing there is no need for final etching (which is especially important for medical implants). If not properly rinsed and dried, etched acids can cause local corrosion and further troubles for implants.
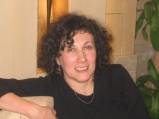
Anna Berkovich
Russamer Lab

Pittsburgh, Pennsylvania
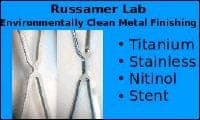
November 10, 2019
A. I have had some good looking titanium finishes using a dry burnishing process with porcelain. For a satin finish (shorter time cycle) I use a pumice organic mix
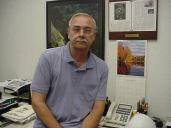
AF Kenton
retired business owner - Hatboro, Pennsylvania
January 22, 2020
Q. Hi there,
I have 4 parts from titanium that I need burs removed from the threads. I can't use electropolish due to tolerance. Any advice of the best method?
- WEST BABYLON, New York
September 29, 2020
A. Hi Eli,
If the parts are grade 5 (6Al-4Va) alloy, we can electropolish them for 30 seconds in low voltage plasma. The dimensions are not changed, because plasma impacts only burrs on the surface if electropolishing duration is short.
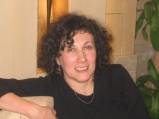
Anna Berkovich
Russamer Lab

Pittsburgh, Pennsylvania
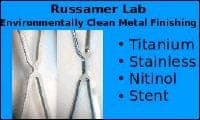
September 30, 2020
A. Hello Eli, I have found that magnetic deburring machines work very well for burrs on threads.
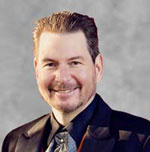
Mark Battles
Plymouth, Minnesota
October 16, 2020
Q, A, or Comment on THIS thread -or- Start a NEW Thread