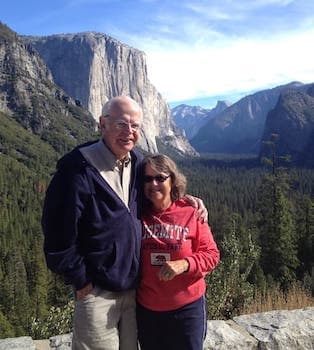
Sound technical content, curated with aloha by
Ted Mooney, P.E. RET
Pine Beach, NJ
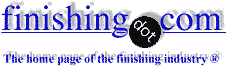
The authoritative public forum
for Metal Finishing since 1989
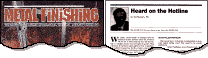
-----
Q&A, Anodized Parts are Pitting -- Problems & Solutions
2001
Q. I am seeing a blackening on some of our anodized (sulfuric anodize per BAC 5022, dichromate seal) aluminum parts that at first glance looks like pitting. However, it has no depth. I might be a burning of some sort (perhaps aluminum dust that detaches itself and creates an arc as it floats away from the substrate), but it cannot be scraped away. It goes through the anodic coating but not into the substrate, so cannot be a scratch. It doesn't happen in a uniform pattern of any sort that I can tell. This has been a problem as long as we've anodized. Quantity depends; sometimes all the parts in a job will have it, some worse than others; sometimes we'll go days without seeing it; as I said before, I cannot see any common patterns or causes as of yet. Any idea what this is or what causes it?
All of our rinses and processes are run at the proper times and kept at the proper concentrations. Our process line for Sulfuric Anodize consists of the following:
- emulsion clean, dragout
- alkaline clean, dragout, rinse
- deox, dragout, rinse
- sulfuric anodize, dragout, rinse
- dichromate seal, dragout, rinse
- dry
- alkaline clean, dragout, rinse
Thanks for any help!
Benjamin Curto- Ponderay, Idaho, USA
A. My first question would be: At what process does this happen? Do these "marks" happen after the Sulfuric Anodize?
I have had a problem similar to this where I was getting black spots on my Sulfuric Anodized parts, it turned out that my Deoxidizer rinses were contaminated with little black "floaties," which were very hard to remove after the Chrome Seal. Now I keep the final Deox rinse at a TDS of 60 constantly. The problem has gone away.....for now.
It really looks like scratches of some sort though. Do you have an Etch process?
Randy Mattson- Seattle, Washington, U.S.A.
2001
Q. It appears after the Dichromate seal. Our Deox final rinse is kept around <300 TDS (well bellow the 750 ppm allowed per spec), do you think it is necessary to keep it as low as 60? Our operators check after the rinse for particulates clinging to the part and a water break free surface, would they be able to see these black "floaties" with their naked eye? We also have particulate filters in all of our rinses, which should catch any particulates of that size. Yes we have an etch process, both an alkaline and an acid etch. Both of these processes are only used as needed though, so most jobs do not get processed through them. Normally I would just write these off as scratches, however they do not delve into the part...
Benjamin Curto [returning]Cygnus Inc. - Ponderay, Idaho, USA
2001
A. The phenomenon is corrosion on the part before anodizing. Remove the defect mechanically, strip the anodize film and anodize again.
Moshe Jakob- Lod, Israel
2004
Multiple threads merged: please forgive chronology errors and repetition 🙂
Q. During an anodizing process, MIL-A-8625 / MIL-PRF-8625 [on DLA] Type II Class II Black, on a few occasions, I have seen pitting that has appeared after anodizing. The alloy is 6061-T6. There parts are making connection because they show a mil thickness of .4-.5. Does anyone have any suggestions as to what causes the pitting?
TED NOVOTNE- Mpls, Minnesota, USA
2003
A. First look at the base metal before you start with 10x or 20x magnification. Little pits in = Large pits out.
Next look for chlorides all up and down the line. Chlorides must be under 50 ppm in the anodizing solution. Some municipal tap waters have more then this. Make up with deI water.
Fluorides cause pitting. Drag in from home made deox? Poor rinsing, blind holes, entrapments can bring the deox into the anodizing solution.
Look at some parts after deox and before anodizing under 10X or 20X, again small pits in= large pits out.
Let us all know what happens next.
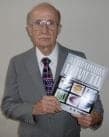
Robert H Probert
Robert H Probert Technical Services

Garner, North Carolina
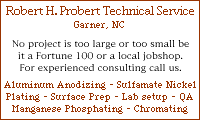
2003
A. Perhaps you may try to isolate the carry bar and process tank (all process tanks) support to prevent pitting due to galvanic effect. Isolation material must be non conductive and porous material like PVC sheet. Let me the result. TQ.
Eddy Lim- Selangor, Malaysia
2003
Multiple threads merged: please forgive chronology errors and repetition 🙂
Pitting of aluminium 6063 extruded parts during anodizing
June 8, 2008Q. I am a manufacturer of heatsink based in India. We use aluminum extrusion of 6063 grade. Since last three days we are facing a problem wherein the parts are getting pitted (black spots on the surface) during anodizing. We have observed the pitting after the jigs are removed from sulfuric acid anodizing tank. The jigs / racks are made of aluminum bar with titanium contacts. We are using acidic degreaser, caustic etch and nitric desmut baths before anodizing. We have replaced the sulfuric acid bath with anew one to do away with chlorides and other impurities but the problem still persists.
Please help.
Regards,
Manufacturer - India
A. Dear Mr Kamal
Kindly check sulfuric Acid Percentage in anodizing bath and check the anodes and connections to rectifier. Lastly check base material
NA - Aurangabad, Maharashtra, India
July 21, 2008
A. The picture is too small to see where the pits are. If they are not on a machined surface, then they probably are from an excess of lubricant during the extrusion process.
Hang one on a stout aluminum wire and process along with the racks of parts. Check all of the parts for pits or surface blemishes after each rinse step. You should not be seeing them "caused" by the anodizing, but that may be the first time that you can see it. After the anodize process ate away pits that were smeared over during machining.
The only time that I saw "pits" was with bad extrusions, some that I could see before any processing.
- Navarre, Florida
July 21, 2008
A. We had similar problems before and we got rid of it by using all Aluminium Jigs.Mixing Aluminium with Titanium is always not the best as the current doesn't flow uniformly.If possible try using aluminium jigs made of 6xxx series.You will find it will be cheaper as well but downside is when you strip them in Caustic Etch as they become weak.You can strip aly Jigs in a solution of Phosphoric & Chromic acid 3.5% : 2% respectively.
Robert Morrissa- London, UK
July 23, 2008
Random Anodized Parts are Pitting
March 29, 2011A quick background. I've been anodizing basically the same way with the same set-up for over 5 years now. I am self-taught with the help of Robert's "How To" book (life saver). I run a decent size shop 450 gallon anodizing tank.
My Set-Up: Caustic Cleaner, Caustic Etch, Sulfuric Acid Deox/Desmut, 160-180 gm/l Anodize tank, Multiple Dyes and a Nickel Acetate Mid Temp Seal. All Water is RO/DI 6 stage.
My parts as seen in the picture have started pitting and in the past I would sum this up to Chlorides getting in my tank. I would then dump and recharge this would fix the problem. Well I did that and I'm still having pitting problems. It only happens when parts are Racked on Ti racks, and only on 5052 parts that are grained like below. I have no issues with 6xxx on Ti. Now I use a Ti coil for chilling my tank and I've used it for years now with no issues but from what I've read it can cause pitting. I've read I need to have it anodically connected or something, I'm really confused by this.
The picture with 9 parts on it were ALL racked on the same Ti Disc rack and the widest panel lost contact near the end of the run and pitted way worse then the one on the left. Only 2 parts showed signs of pits the others were perfect.
I'm really baffled by what's going on and I need help asap. Thanks for the help.
Shop Foremen - Gainesville, Florida, USA
Multiple threads merged: please forgive chronology errors and repetition 🙂
April 2, 2011
Q. I design and produce iPhone cases in Brooklyn.
I'm having a hard time getting consistent results with local anodizers.
Every few batches I get back parts with heavy pitting. This only seems to happen with clear not colored parts.
The anodizer says it's my parts. Possibly water /cutting solution drying on my parts causing corrosion that is amplified by the anodizing. The pitting is totally invisible on the parts I bring to the Anodizer.
The pits are deep maybe 0.003 to 0.005
Out of batch 100 parts we bring him maybe 10 will come back with pits. Some batches come back with little or no problems.
Here is my process:
Material: 6061 bought from same supplier. Talked with supplier and he says all the material I have bought for the past few years comes from same mill. I use bar stock 1/4 x 3 x 192 each end part being about 2.5 by 3 x 0.24
I run material uncut through wet timesaver to 120 grit.
Machine inside of part leaving nice 120 grit surface. Machined under water soluble oil. Parts are blown with air gun to remove most water and left to dry.
Deburr and heavy scotch brite part. No visible pits perfect finish at this step. Wrap part in paper and deliver to anodizer. Sometime parts are wrapped and might sit for week waiting to go to the anodizer.
We do not see pitting on all the parts we bring to the anodizer. We do see in groups we tend to see it more in parts with larger surface areas.
This is second Anodizer we have used in area. Other Anodizers while having many other problems never had this specific one. The other Anodizers said the problems they had where also in our material/process but we do not see the same problems being carried form one Anodizer to another. But we a small company and we are developing a product so process and staff do change.
If the problem is at our end would something like a dishwasher or tank washing after each step likely to solve the problem? Or would drying with a paper towels be sufficient.
Is corrosion between steps a likely cause of the pits?
The Anodizer says the timesaver sanding is likely the cause but on the cases that have problems we see it on the machined surfaces (less but noticeable) as well as the sanded. He has also mentioned that aluminum oxide belts could cause the problem and recommended ceramic based belts.
I would like determine if the cause of this problem any advise to improving my process would be greatly appreciated.
Please note the photos are of parts that have been anodized but then stripped after pitting was found. The pits do not seem to change much after stripping.
Thanks
Manufacturer - Brooklyn, New York
A. You should try Impregnating the parts with a polyester resin after machining. This should fill the micro porosity
within the part's pores, it should also slow the oxidation process prior to anodize. Ref: MIL-STD-276
- West Islip, New York, USA
April 15, 2011
A. I have never seen a piece of aluminum coming out of a machine shop that has been "time saved" that we did not have some sort of problem. In your case, even if the wet sandpaper has been designated "aluminum only" some un-knowing member of your company ran some steel through the machine, and now you are imbedding iron particles in the soft "Kleenex-like" aluminum. The these iron particles set up galvanic corrosion sites and pit, then as the previous letter said, the anodizing magnifies the pits. Solution, get new sandpaper, lock the time saver up so no one can use it on iron.
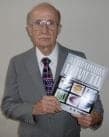
Robert H Probert
Robert H Probert Technical Services

Garner, North Carolina
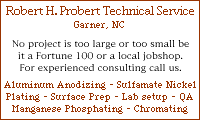
April 18, 2011
Q. Hi,
I have received a complaint from a customer regarding pitting on an anodised part. The part has been polished, bead blasted and then anodised. The pitting only showed after being anodised. I was hoping someone with some experience could help me try and find the root cause of this issue to prevent it occurring again.
The part is machined from Aluminium Extrusion BS EN 755-2 76.20 mm diameter Type 6082T6. The part is turned and then milled. Thank you for any help you can provide!
I have spoken to the material supplier who suggested these marks could be caused by Back End Defect, but I have never seen marks like this caused by Back End Defect before.
- Bath United Kingdom
October 16, 2020
A. It appears to me you may have gotten some type of contaminate (Fe?) in your blast media which became embedded in the substrate
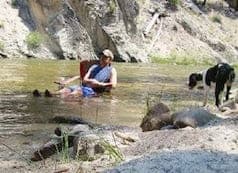
Marc Green
anodizer - Boise, Idaho
October 18, 2020
A. It doesn't look like a material defect (press end).
More like a problem from blasting, e.g. impurities or parts of the abrasive (splinters, used abrasive, excessive pressure).
Are foreign parts visible at a higher magnification?
How many parts are bad. From the blasting of the surface, then probably only a part and arranged irregularly.
- Hallau, Switzerland
October 19, 2020
Q. If I observe the picture which you had sent, shape of pitting does not seem "hollow". It seems like "burr". So I don't describe this problem as a pitting issue, because if it had been pitting like iron, chloride then it would be "hollow appearance" .My guess is this problem comes from extrusion after cold saw before heat treatment (T6). These burrs can be adhered to the surface of parts by effect of heat treatment and become like embedded in the surface of parts. Up to me, the most important issue here, "Survey" of each section. For example, before/after heat treatment and before/after anodizing or other mechanical processes.
alaattin tuna- TURKEY Sakarya
October 19, 2020

Ed. note Feb 2022: Sorry, no longer on ihanodizing.com site, but you can try googling the title
----
Ed. note: Pitting in anodizing is a perennial issue. Readers may wish to also review:
Thread 48164, "Pitting during Anodizing",
Thread 1594, "Pitting of parts in dye and seal tanks of aluminum anodizing line",
Thread 25790, "Having trouble with pits in bright anodizing",
and Search the site for many more.
They may also wish to review this outstanding presentation -->
Q, A, or Comment on THIS thread -or- Start a NEW Thread