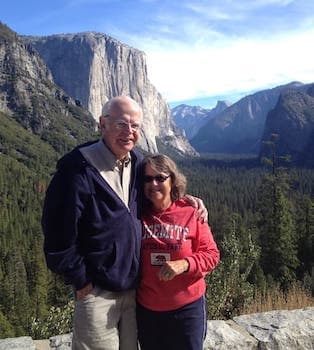
Curated with aloha by
Ted Mooney, P.E. RET
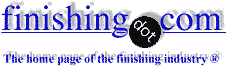
The authoritative public forum
for Metal Finishing 1989-2025
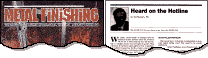
-----
Parker Parcolubrite -- history of zinc & manganese phosphate coatings
[editor appended this entry to this thread which already addresses it in lieu of spawning a duplicative thread]
Q. We've done Parco Lubrite #2 on our power piston skirts (large industrial 14"-20" diameter) for years, and our manufacturing wants to use just Manganese Phosphate as a substitute for cost reduction.
I'm curious about the difference between the two, Iron-Manganese vs. Manganese regarding break in wear resistance/protection.
Some of our piston skirts are tin plated (Potassium Stannate).
Maybe this is not the forum for these type questions, if so, please excuse my intrusion.
Thank You!! Regardless
Respectfully & Sincerely,
- Houston, Texas
August 18, 2023
A. Hi Michael,
Technical questions on these types of issues are what the site is about, so thanks for the question. But comparing one brand, supplier, or proprietary to another, or praising or condemning it in this largely anonymous forum has proven unworkable ( huh? why?).
Alternate brands of break-in appropriate phosphate coatings are certainly available. But in any case I think there is more to the process than just the manganese phosphate step. For example, another proprietary [Endurion] was a special postreatment tin salt for manganese phosphate processes; and most brands also suggest a grain refiner before the phosphate.
Final answer: it's not impossible to develop a fully non-proprietary system for applying a robust full break-in phosphate, but it's a big job, not just a matter of making up a magnesium phosphate tank.
Luck & Regards,
Ted Mooney, P.E. RET
Striving to live Aloha
finishing.com - Pine Beach, New Jersey
⇩ Related postings, oldest first ⇩
Q. Hi,
I am an After Market Salesperson for Voith Paper-Finishing Division. On a few parts requested by a customer our prints state that the items need: To be blasted with Aluminum Oxide Grit #124 (or equivalent) to receive Electrofilm 66C Finish. There has also been a modification to the print that states:
Parker Lubrite #2 Changed to blasting.
These parts are made of C.F. Steel. The application of these parts requires a constant contact with other metal items in the assembly of a paper machine winder. These parts are constantly moving and rubbing on the assembly. My division has moved and we can not locate the specs on this finish. My questions are:
1. What are the specs for this finish (enough to have these pieces manufactured)?
2. Is the Parker Lubrite #2 a spec for the blasting or the plating (chroming or whatever the finish is)?
My experience in metal finishing is non-existent. So please explain matters as you would to the common layperson or such that I can hand it off to a machine/chroming shop and have the job done properly.
I have tried all the local job shops and all of them came up empty-handed. I really hope these are recognized standards and not an internal Voith Paper Standard.
Thank you in advance for your reply. Rodney Johnson
Rodney Johnson-
2000
A. Hi
Parco Lubrite No.2 is a manganese phosphating process that chemically grows a finely crystalline manganese-iron phosphate coating on iron and steel. It is particularly recommended for wear resistance, in combination with oil or grease. Henkel is the current owner for this process, but there should be many outworkers about who can offer the service.
Walterisation (UK) Ltd - Croydon, UK
Q. I am looking for a supplier in Canada on a product called Parcolubrite or Chemplate with info on MSD of these products and proper temperatures with do's and don't. I am using Chemplate now for parts we manufacture but have hit and misses as we go as I am buying it second hand now. I had used Parcolubrite before and had better results but cannot remember where we got it from.
Help.
Pat Greenmanufacturing - Sexsmith, Alberta, Canada
2001
Ed. note: This RFQ is outdated, but technical replies are welcome, and readers are encouraged to post their own RFQs. But no public commercial suggestions please ( huh? why?).
A. Parcolubrite is a trademark of Chemetall, so you should be able to get it from Chemetall-Oakite or one of their distributors.
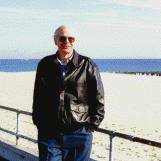
Ted Mooney, P.E.
Striving to live Aloha
finishing.com - Pine Beach, New Jersey
A. Parcolubrite is a Henkel Surface Technologies product. They have sales and manufacturing plants in Canada.
Paul Davis- New Castle, Pennsylvania
sometimes on
AbeBooks or Amazon
(affil links)
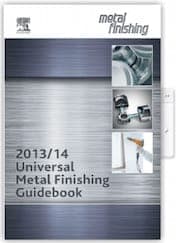
free pdf is currently available from academia.edu
Uh-oh it's listed as a phosphatizing process offered by Chemetall-Oakite in the Metal Finishing Guidebook. I guess it's time to call the trademark lawyers
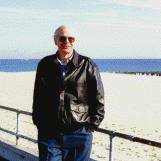
Ted Mooney, P.E.
Striving to live Aloha
finishing.com - Pine Beach, New Jersey
A. Parcolubrite is trade name of Parker Chemical for a series of phosphating solutions. The most common one was Parco Lubrite #2 which was a widely used manganese phosphate process called out in many military and arms applications. Amchem and Parker merged way back that tied in Parcolubrite and Alodine trade names and I know Henkel owns rights to Alodine. As far as I know, while Oakite has fine zinc phosphate line, I don't believe that they have any manganese processes.
Chemplate was a job shop, I believe, mainly doing electroless nickel in the greater LA area. It was a company name rather than a process I believe.
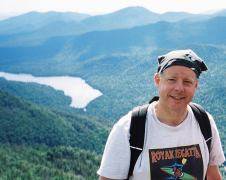
Milt Stevenson, Jr.
Syracuse, New York
2002
Multiple threads merged: please forgive chronology errors and repetition 🙂
Q. I am looking for a detailed description of Parco Lubrizing.
Susan Maahsaviation technology - Tulsa, Oklahoma
2006
PARCO LUBRITE is formulated to produce nonmetallic, oil-absorptive coatings on iron and steel bearing surfaces. These corrosion-resistant coatings consist chiefly of iron and manganese phosphates, and reduce wear on such articles as pistons, rings, liners, camshafts, tappets, motor blocks and similar bearing surfaces. Other beneficial effects may be summarized as follows:
A. Permits rapid break-in of moving parts without scuffing or welding by preventing metal to metal contact between the bearing surfaces.
B. Increases lubrication of treated surfaces due to the oil-absorptive coating.
C. Removes light metal scratches remaining from machining operations.
D. Retards corrosion.
- Oklahoma City, Oklahoma
April 21, 2010
Good job there. I worked an old Storm Vulcan lathe back in the 70's. Central Engine Exchange was the name. The company was from Chicago, but Bob Glassman moved it to So. Miami. Loved the job. I would just grind down the camshafts to the specs. All hydraulic now so no level. The manual fuel pump lobe was the main problem. Dirty or no oil would wear that lobe out. Garbage then. I memorized all of the firing orders to all of them. I even had a couple of HP cams, and made master discs for them, but never got a blank cam to do one. Also taper was an issue. All lobes on each camshafts had a a taper. WHY: The taper would spin the lifter for lubrication & wear. I've built many HP engines after this. 202 heads on a 350 4BM, Blueprinted. Not this new days' crap, but had right at 500 HP. 69 Chevy truck w/front wheels off the ground.
Johns Jon's - Florida. USA
July 10, 2018
Multiple threads merged: please forgive chronology errors and repetition 🙂
Q. I'm trying to get a history, including time line, of the use of Parco-Lubrite, zinc phosphate and manganese phosphate, especially before and during World war Two. This is for research on the finishes used on certain U.S. firearms produced during the war. I have seen the data published on Wikipedia, https://en.wikipedia.org/wiki/Parkerizing. Does anyone know a source of in depth history on the use of parkerizing?
I also see that Parco-lubrite is currently a manganese phosphate solution, yet I'm pretty sure it was a zinc phosphate solution during the war. Does anyone know when the composition was changed?
If you know of a book that explains this in detail, I would be glad to purchase it. Your help is much appreciated.
researcher & writer - New York
January 23, 2009
A. Hi, Chris. I tend to believe Parker-lubrite was manganese based from the very beginning. I am looking at a 1939 book "Protective Coatings for Metals" by Burns and Schuh, which reports " ... in 1918 it was found by the Parker Company that the character of the coating was improved by the use of a solution of primary manganese phosphate. In this process, which came to be known as Parkerizing ...". I have some other references asserting the same. Sorry, I don't know offhand where the "Lubrite" term arose.
Without research I can't dispute the Wikipedia assertion as to whether or not there was a conversion to zinc phosphate during the war. My mentor Joseph Mazia was the director of the metals development lab at Frankfort Arsenal during the war, and later an employee of Parker+Amchem, and would have been able to give you the accurate and full history. Unfortunately he has passed away.
Regards,
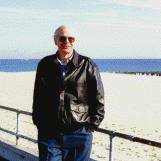
Ted Mooney, P.E.
Striving to live Aloha
finishing.com - Pine Beach, New Jersey
Q. From what I understand, the word "parkerizing" is a generic term for a phosphate coating. It could be zinc or manganese phosphate. The Parker Rust Proof Company filed for use of the trade name "Parco Lubrite" in 1940. According to the Wikipedia article, The Parker Company received two patents. One in 1938 for a phosphatizing process using zinc (which was more readily available during war than manganese). The second was granted in 1942 for an improved zinc phosphatizing process utilizing copper and a chlorate to make the process more economical.
While I have found nothing to show that Parco Lubrite was a zinc phosphatizing process during the war, it would seem that if the Parker Company was putting all that time into developing an economical zinc phosphatizing process, then that would be what they were selling/producing.
My primary area of interest is in the production of M-1 carbines during World War Two. There were ten different manufacturers of the carbine. The color of the phosphate finish varies among the producers. For some producers the finish is a light silvery gray that I'm sure is a zinc phosphate finish. Other producers have carbines where the finish is typically darker and some have a very greenish tint. Did all these companies use a phosphate coating that utilized the improved and economical process that was patented by the Parker Company in 1942? It would seem that the most economical method using the material (zinc) that was most readily available would be the on to use.
If all companies were not using the improved zinc phosphatizing process patented by the Parker Company, then what were they using? Does anyone have the names and companies that manufactured other phosphatizing products during World War Two? I have only seen the term "Parco Lubrite" in reference to the phosphatizing process on ordnance and carbine manufacturer documents of the period.
If all the companies were using Parco-Lubrite, be it zinc or manganese in composition, why all the variations in the color from a light silvery gray to a black?
There's one more thing that I'm curious about with regards to the color. Many World War Two firearms have a phosphate finish with a greenish tint. Many people have conjectured that this is caused by years of storage in
Cosmoline. I have my doubts about this. There are two possible ways that I think the greenish tint is on the finish. First, if the finishing process used was the improved one patented by Parker in 1942, it would have copper in the solution. Could there be enough residual copper in the finish to cause some greening through oxidation over time? The second possibility lies in the chromic acid rinse. Could the chromic acid combine with the zinc to form a greenish color? I know that zinc dust
⇦ this on
eBay or
Amazon [affil links]
is green. I again thank you for your time.
researcher & writer - New York
A. Parkerizing is nothing more than a trade name for phosphate coating, just as Kleenex is a trade name for tissue.
Parker very aggressively advertised and promoted their products, to the point that "Parkerizing" was included in military and commercial specifications and on drawings.
As these parts were sourced through various sources over many years, some of them may have used Parker processes, and others used whatever phosphating process they had on hand. Some were proprietary, and some home-brewed.
I have myself processed parts which called for "Parkerizing" with both zinc phos and Manganese phos, none of it using Parker materials. Customers accepted this work just as though they had asked for a Kleenex and been given a Scott tissue.
As to color, zinc phos is usually light gray, but under some conditions it can be more nearly charcoal, and if chrome rinsed, may have a yellow or green tint.
Manganese phos is normally very dark gray, perhaps nearly black, but is sometimes charcoal. You may not be able to tell visually between a dark Zn phos and a light Mn phos.
In addition there can be a large variation in grain size in either process, and this, along with the visual difference between thin and thick coatings can make a significant difference in appearance.
Some specifications may call out "Parkerizing" and nothing else. Other specs may include requirements for coating weight, grain size and color.
Given the history involved, it is not surprising that "Parkerizing" done at different places and different times is different in appearance.
Is "Parkerizing" only that coating which is produced using Parker chemicals? Or, is Parkerizing any phosphate coating which serves the intended purposes of providing a low reflective surface which will absorb rust preventives.
It's the Kleenex versus bathroom tissue question, and you can argue either side ad infinitum.
And then there's the Thin Dense Chrome question, but I digress...
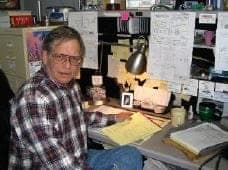
Jeffrey Holmes, CEF
Spartanburg, South Carolina
A. Try old Angiers book on bronzing of firearms Firearm Blueing and Browning [on
eBay ,
Amazon,
AbeBooks affil links]
-- According to that book phosphate finish is somewhat older -- there you can find some early variants of the process.
1906. Coslett's patent (zinc phosphate based)
1911. Richardson's patent (manganese phosphate based process).
Iron phosphate based processes are probably even older (late 19th century).
1929. German proprietary process (IG Farben)
According to W.Machu: Nichtmetallische anorganische ueberzuege (Nonmetallic inorganic coatings), Leipzig 1948.
Hope it helps and good luck!
- Cerovski vrh Croatia
A. I was a 35+ employee of Parker Rust Proof Company (name has changed with owners) presently retired. Was hired as a Chemist upon graduation of Missouri University. I was in upper sales management prior to retiring, and have used both systems in commercial installations. Parco Lubrite 2 (operates on the iron side Fe+2) gives heavy coating weights compared to Parco Lubrite 5 (operates on the NO2 side) no ferrous iron in solution.
Both coatings could be burnished for bearing surfaces. Coating weights can be reduced and/or refined by utilization of a conditioning agent prior to Phosphate e.g., Parcolene M. Some operational nuggets are given in this condensed response; should other information be required please ask me further. Individuals with knowledge concerning these pretreatments are becoming limited due to R&D efforts being focused in different more profitable areas and [loss of acquired knowledge] of personnel. The chemistry of this MnPO4 is very unique and I find it quite interesting regardless of profit margins.
- Shelby Township, Michigan
June 14, 2013
Tip: Readers want to learn from Your Situation 🙂
(little can be learned from abstract questions, so many readers skip them)
Q. Thomas, can you point me to where I can find the difference in the coating weights between the 2 and 5, and possibly the TDSs for both?
Russ Rohloff- Fort Collins, Colorado
November 1, 2022
Ed. note: Thomas' reply was from nearly 10 years ago, but we'll see if his e-mail still works :-)

Q, A, or Comment on THIS thread -or- Start a NEW Thread