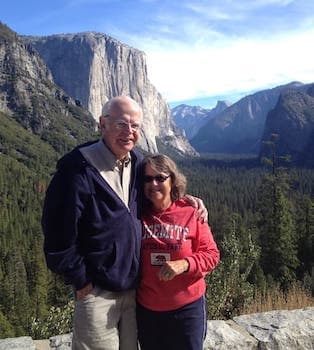
Curated with aloha by
Ted Mooney, P.E. RET
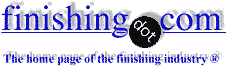
The authoritative public forum
for Metal Finishing 1989-2025
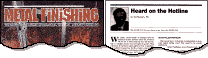
-----
Black Oxide vs Phosphate
(to provide context, hopefully helping readers more quickly understand the Q&A's)
Black Oxide (sometimes called 'Blackodizing' in other countries) is a process where steel parts are immersed in a boiling hot (well over 212 °F / 100 °C) vat of strong caustic soda and nitrite/nitrate salts as oxidizers to impart a very very thin film of black 'rust' onto parts such as firearms, gears and sprockets, etc., primarily for decorative reason. The parts are always subsequently oiled or waxed, and it offers mild corrosion resistance. It is a 'final finish' not a pretreatment.
Phosphating or 'phosphatization' is actually a number of somewhat different treatments, sometimes roughly categorized as iron phosphate, zinc phosphate, and manganese phosphate. None are decorative.
Manganese phosphate is done by immersion is a warm to hot, but not boiling, solution and it builds a thick, soft, oil-absorbing coating which is frequently used on automobile parts as a 'break-in' coating on internal engine and power transmission parts. Zinc and iron phosphates are applied by spray or immersion and are intended as pretreatments for painted surfaces; they are not a 'final finish'.
Q. Dear sir,
Thank you for usual support.
The Black Oxide coating is not the traditional Phosphate process?
Thank you.
- Jeddah
August 18, 2021
A. Hi Abdulla. No it's not. We've now added a FAQs & TUTORIAL to this page which will answer you.
Luck & Regards,
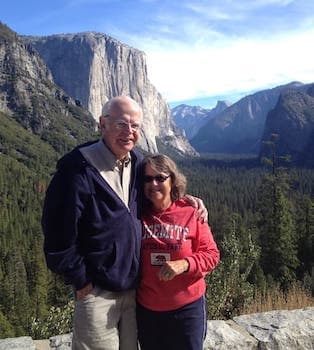
Ted Mooney, P.E. RET
Striving to live Aloha
finishing.com - Pine Beach, New Jersey
August 2021
Q. I am purchasing bolts, slotted spring pins, and other elements from a wholesaler who is unable to provide additional information. Is there an easy way to test and find what finish (black oxide, black phosphate,...) has been applied to these parts?
JP Garcia- Santiago, Chile
September 18, 2021
A. Hi JP. If you are certain that it's an either/or situation, I think a quick test can be devised ... maybe as simple as a sample board for visual identification.
But if they are a mishmash and might also be black zinc, black nickel, black electroless nickel, black chrome, PVD, autophoretic, cathodic electrodeposition, etc., sorting them could be a totally impractical job.
Luck & Regards,
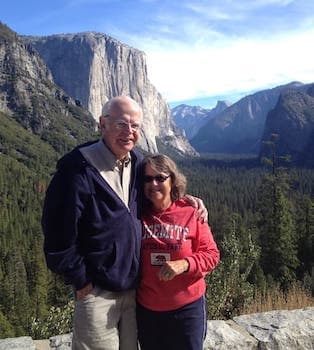
Ted Mooney, P.E. RET
Striving to live Aloha
finishing.com - Pine Beach, New Jersey
September 2021
⇩ Related postings, oldest first ⇩
Q. I am bringing up a product line from Forest City, North Carolina to the plant here in Elyria, Ohio. In NC, they phosphate coat their bodies; and in OH, we black oxide our bodies. What are the pros and cons to using a black oxide finish vs. a phos finish on cast iron parts?
Cintia Ulloa-Elyria, Ohio, USA
2001
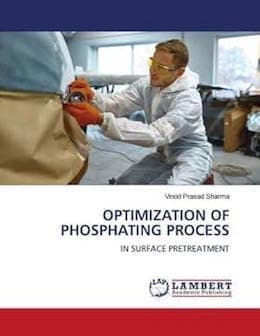
avail from AbeBooks, or Amazon
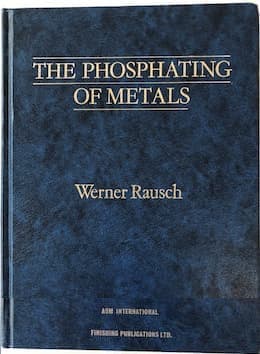
avail from eBay, AbeBooks, or Amazon
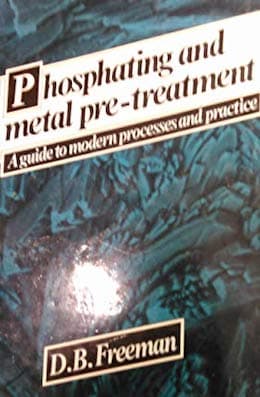
avail from eBay, AbeBooks, or Amazon
(as an Amazon Associate & eBay Partner, we earn from qualifying purchases)
A. Hello Cintia:
Below is a quick list of differences and likenesses.
- Slight dimensional change with Phosphate vs none with black oxide.
- Phosphate and oil affords more corrosion protection than black oxide with same oil.
- Castings can be difficult to black oxide. Sometimes they can turn reddish to mahogany color in the black oxide process.
- Phosphate runs at roughly 180 degrees F while black oxide runs at 290F.
- Both processes have similar pre-treatment steps.
- Black oxide gives a deep black color while phosphate coatings are grayish. Black oxide is more abrasion resistant than phosphate.
Springfield, Massachusetts
Friction characteristics of black phosphate vs. black oxide
Q. We use a spring clip which calls out "black phosphate and oil or 2nd choice - black oxide (bake to relieve hydrogen)". Sometimes the clips have a matte finish and sometimes they have a gloss finish.
The matte finish provides a little more friction which is desirable in our application.
Is the phosphate or the oxide providing the matte finish?
Steven E. Millermedical equipment manufacturer - Indiana, United States
2003
A. Hi Steven. It can't be said with 100 percent confidence, but I'd give it about 95 percent that the matte finish is phosphate and the glossy finish is black oxide. Good luck.
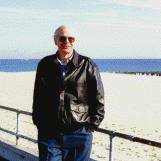
Ted Mooney, P.E.
Striving to live Aloha
finishing.com - Pine Beach, New Jersey
2003
Q. Hello, I am designing a small (indoor use) side table with a steel leg base composed of 1" tube stock steel welded in a 2' x 1' x 1' frame. I am interested in this black oxide treatment for my steel leg frame as it will resist rust but will retain a more "industrial" or "natural metal" look compared to a powder coat or other finishing methods I have entertained. Would this be an appropriate treatment? Also important, will this be cost effective?
Thank you very much for your time and expertise in advance.
Designer/student - Lexington, Kentucky, USA
April 16, 2015
April 2015
A. Hi Al. Hot black oxide with wax doesn't offer much corrosion resistance, but should be okay for indoor use if waxed. It will be cost competitive with high quality pretreatment and painting, but not with some of the junk that is out there. Black chrome plating would be a nicer and more durable finish, but much more expensive. Good luck.
Regards,
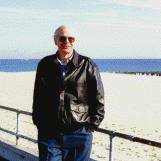
Ted Mooney, P.E.
Striving to live Aloha
finishing.com - Pine Beach, New Jersey
Q. Sir, We are using Hot phosphating process (class A1) for our finish products.
Now we are thinking to switch to Room temperature black oxide coating process.
Can you guide what may be impact if we switch to process.
pradeep
- Pune, Maharashtra, India
April 8, 2015
A. Hi Pradeep. First, you need to have some sample parts run and put into use before you think about changing production systems. Regardless of what you read, actually working with the parts will be critically informative. As the first quick observation, for example, I think you will find that cold blackened parts will be quite smutty; that might be no big deal or it could be completely unacceptable.
Please note that cold blackening is a completely different process than hot black oxide.
What are the parts made of, what is their function, and what environment will they see? Are they immersed in oil when used? Are they painted before use? What kind of phosphatization is currently done on them (iron, zinc, manganese)?
Finally, why might you want to do this? With full details I am confident that we can give you a good answer. Thanks.
Regards,
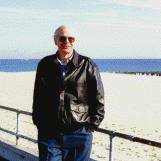
Ted Mooney, P.E.
Striving to live Aloha
finishing.com - Pine Beach, New Jersey
April 2015
Q. Sir, Thanks for reply. We are Transpower coupling manufacturer. Our 70% components are made of Cast iron and rest of Mild steel (EN 8, 19, 24 etc.)
We currently having Zn Phosphating process along with Oil Sealing. Our couplings are exported by sea.
Our main purpose to switch over is visual look & cost. Please reply.
Pradeep Tanksale [returning]- Pune, Maharashtra, India
April 21, 2015
A. Hi Pradeep. Both hot black oxide and cold blackening have been used on such components. They will probably not have the corrosion resistance of your current components, so it's hard to predict without investigation whether they will survive sea transport.
Regards,
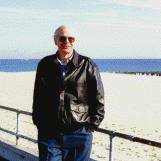
Ted Mooney, P.E.
Striving to live Aloha
finishing.com - Pine Beach, New Jersey
Q. Sir,
We are here to reply with clarification.
Also, we would like know shade difference than normal, i.e., greyish to black. In same basket some components are showing black shade while some greyish shade.
Is this shade difference going to change salt spray life?
Pradeep
Pradeep Tanksale [returning]- Pune, Maharashtra, India
July 17, 2015
by Larry Durney
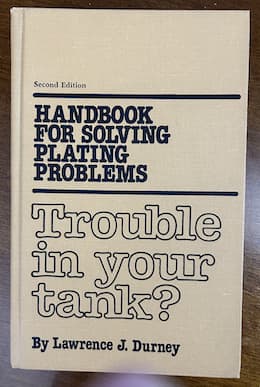
on eBay
(sometimes) or
AbeBooks
(rarely)
or Amazon
(sometimes)
(affil links)
A. Hi Pradeep. Sorry, but I am getting more confused. Have you switched from zinc phosphating to cold blackening or have you not switched?
May we assume that the components in any given basket are always the same part number, size and alloy? Is the problem as follows:
If this is the case, there is obviously something different in the alloy of the parts or their history.
Your question of whether the gray parts or black parts have a different salt spray life is backwards: the purpose of the salt spray test is to assist in process control. i.e., if there seems to be no reason for the color variation, and the variation does not represent a problem for you in some other way, you salt spray test the light grey parts vs. the blackish parts, so you now know whether the color variation is important. If there is no difference in their salt spray life, darkness becomes a factor that you can ignore.
I suspect that the process is not yet actually under control and as you study it you will find that what you have been told is incomplete. Good luck.
Regards,
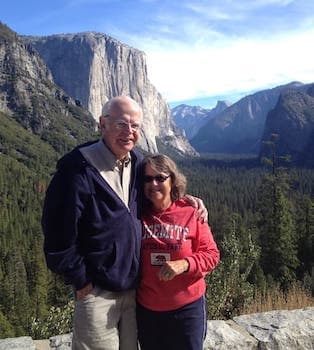
Ted Mooney, P.E. RET
Striving to live Aloha
finishing.com - Pine Beach, New Jersey
Blackodizing vs. Phosphating?
Q. What is the difference between Blackodizing & Phosphating?
Geeta Arvind Khandkar- Pune, Pimpri-Chinchwad,
December 4, 2015
A. Hi Geeta. "Blackodizing" is a term often used in India to mean the same thing as the USA term "Black Oxiding". We appended your inquiry to a thread which compares blackodizing and phosphating.
Regards,
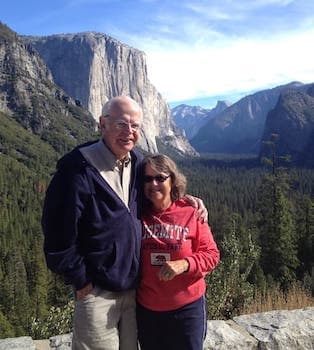
Ted Mooney, P.E. RET
Striving to live Aloha
finishing.com - Pine Beach, New Jersey
December 2015
Q. My company is looking to optimize the design and finish of our automotive chisels and punches and we are trying to decide between a black oxide and black phosphate finish. I have seen a number of threads comparing the benefits of the two coatings, but not for this specific application. Our manufacturer would prefer to use phosphating, but black oxide seems to be much more common for automotive tools in North America. Thank you kindly for your insight.
Best regards,
Automotive Tool Company Associate/Engineer - Vancouver, BC, Canada
October 25, 2016
March 25, 2017
A. Hi Paul,
Since the two coatings are so different in form and function, it's best to compare the pro's and con's of them. Since you stated that you're coating punches and chisels, neither offer much in the way of abrasion resistance, so after a few uses both coatings would be worn. The black oxide coating offers almost no corrosion protection on its own and relies on a top coat of wax or oil. The phosphate coating, either in manganese or zinc doesn't offer much more, except that the crystalline structure of the coating tends to hold more of the top coat than the black oxide. Also, the black oxide has no discernible change in dimension while the phosphate coating will slightly.
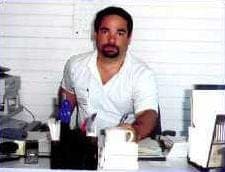
Jim Conner
Anoplex Software

Mabank, Texas USA
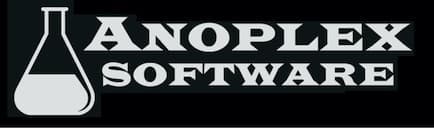
Q. I am interested in using Black Oxide coating of carbon steel for mild corrosion resistance, replacement of powder coat, and a need for some abrasion resistance.
Can you please comment on this posting and a recommendation for specification for the coating?
Best Retards,
Mike
SMARTfit Inc - Camarillo, California
May 2, 2018
May 2018
A. Hi Mike. It's generally a truism that if you are relying on several strengths of a particular finish or coating, it's probably the right one; but if you pick a coating which is not known for strengths in the qualities you seek, or the finish exhibits strengths you don't need, it may not be the ideal.
Black oxide offers nowhere near the corrosion resistance of powder coating, but it will exhibit mild corrosion resistance if it's waxed or oiled. Wax or oil are not a problem for you? On the other hand black oxide causes no dimension change unlike the couple of thousandths of an inch which thermoset powder coatings require ... is that important to you? Abrasion resistance is fair; Most gun barrels are black oxide to give you a qualitative idea of it's abrasion resistance.
Other choices might be black nickel, black chromium, black zinc ... or salt bath nitriding for great corrosion resistance and abrasion resistance. Good luck.
Regards,
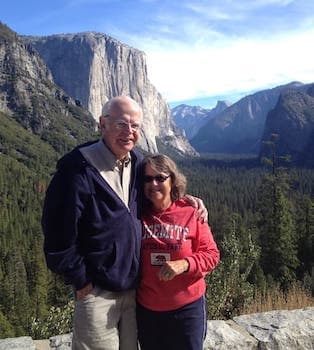
Ted Mooney, P.E. RET
Striving to live Aloha
finishing.com - Pine Beach, New Jersey
Q. Thanks for the fast response! I am not sure how much abrasion resistance I need. One plate will rub up against a smooth anodized surface with a very light load.
I know that black oxide coating is not expensive and we don't want to pay for what we don't need. We don't need much corrosion resistance as the product will be used indoors. With that extra information what coating would you recommend?
Best regards and thanks again for taking your valuable time to respond to me.
Mike Metier
SMARTfit Inc - Camarillo, California
May 3, 2018
Ed. note: This RFQ is outdated, but technical replies are welcome, and readers are encouraged to post their own RFQs. But no public commercial suggestions please ( huh? why?).
A. Hi Mike. I don't think anyone will actually "recommend" a specific coating for a specific application which they are not familiar with, any more than an engineer would recommend a specific wide flange beam size based on rough internet information. But if wax or light oil sounds okay, then black oxide doesn't sound inappropriate offhand; try to get a sample piece from a black oxide shop for some tests. Many will do a free sample for industrial customers. Good luck.
Regards,
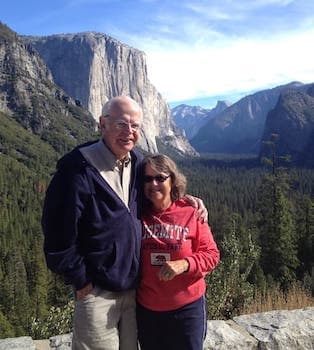
Ted Mooney, P.E. RET
Striving to live Aloha
finishing.com - Pine Beach, New Jersey
May 2018
Q, A, or Comment on THIS thread -or- Start a NEW Thread