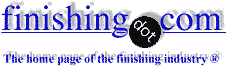
-----
Seeking Expert Witness in Chrome Plating Lawsuit
Q. I am an attorney in Grand Rapids, Michigan. I represent a Plating facility who is involved in a lawsuit as it relates to chrome plating the facility performed. The claim is that the chrome was not thick enough or up to another company's spec as requested which allegedly caused failure in the part because the Plaintiff claims that the chrome was not flash but for strength purposes. The plating was only for chrome although the parts were brass couplings coated with nickel and then shipped to us for chrome plating. We are a sub contractor. Is there any persons willing to be experts who are familiar enough with the plating industry who would help support and defend this type of lawsuit and be able to read the specs and blueprints and recite industry standards?
Thanks!
Weesner [last name deleted for privacy by Editor]- Grand Rapids, Michigan
2001
Ed. note: This RFQ is outdated, but technical replies are welcome, and readers are encouraged to post their own RFQs. But no public commercial suggestions please ( huh? why?).
A. MIL-Spec FED QQ-C-320 specifies a maximum of 25 microinches for decorative (Read Corrosion) chromium plating over nickel. Higher thicknesses result in macro-cracking of the chromium film. Hard chromium plating would be unusual over the nickel base due to the softness of the nickel, allowing the heavy chromium plate to fracture under load.
Ron SchmittMETAL FINISHER - COLORADO SPRINGS
2001
2001
A. I was plater 18 or so years ago , I have ran decorative chrome and hard chrome lines , so I have experience in both.
1] Decorative chrome is just that, decorative , the corrosion resistance is derived from the nickel base , it has no strength characteristics that I know of unless solely incidental
2] hard chrome- hard chrome is typically a wear surface , or a repair to an existing steel part for a worn surface. Hard chrome is extremely strong as a wear surface.
Your letter doesn't really describe the part failure, just that it failed. I have never used hard chrome to increase mechanical strength , such as shear or tensile strength. And I don't feel that trying to use it for that would be an accurate depiction of hard chrome's intended purpose.
When spec'ing a plate for a product , a minimum thickness is usually specified, and a set of dimensions is provided to hold to. When I ran mil spec work , it was our job to advise a customer if the provided product could not be plated within the specs provided , i.e., if the mil spec thickness could not be applied within the provided dimensions because the provided product was out of spec.
Also, Hard chrome heavy buildups are typically ground to the qualified dimension after plating, i.e., the product is severely overplated in thickness purposely so the end product can be precision ground after plate to a final dimension.
So, to try to answer your question, if the provided product was correctly prepared prior to plate [critical] and the chrome was plated correctly to the thickness the customer specified , there is no way the chrome should be able to cause a failure. If the chrome thickness was under spec , and was being used without final machining, a wear out / wear thru type failure is possible , especially if the thickness of the coating was minimal.
Example: if a shaft is to be plated with 3-5 tenths of chrome , and the vendor actually put on 1.5 to 2 tenths , and then lets say the product made its way thru to final product , as it was still in dimensional tolerance , it is possible that the product would fail , and the cause be the chrome ... hope this helps
Ron Landretteplating equipment supplier - Bristol, Connecticut
A. 1. Hard chrome used to restore a dimension like on a hydraulic shaft and engine crankshaft journals. Nickel underlay is always used to restore a finish dimension that will require more than .015 thick of finished chrome. If the finish deposit (after final grind) exceeds .015. the "chicken wire" cracking can cause base metal cracking in high strength steels (200 KSI and above). The nickel deposit never causes chrome failure due to the soft nickel deposit. (Boeing specs)
2. Hard chrome deposit used for a wear surface. - It is common to "flash plate", usually less than .0005, on surfaces that are subject to wear. This is applied to faces and mating surfaces and is never finish ground to size. Sometimes the deposit is lightly polished to knock down the rough edges that occur in high current density areas.
3. The only place I have seen the chrome deposit cause a part failure has been on high strength steels such as aircraft landing gear. The lack of proper thickness of flash chrome deposit may cause a premature wear problem but not an outright failure.
- Winston-Salem, North Carolina
June 20, 2009
Hi. The wildly different answers from Ron S, Ron L and Bob M -- all highly experienced experts -- tells you what the actual answer is: If the spec doesn't actually specify it, ya got nothin'.
Claims that people "are expected to know 'this' ", or " 'this' implies 'that' ", or "everyone knows that ..." are usually very weakly founded as these experts have just clearly demonstrated for you :-) And although chrome plating can be used for wear resistance, I've never heard of it being relied upon for strength. Hopefully a reader who feels that s/he can offer expert testimony will contact you in private.
Regards,
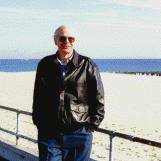
Ted Mooney, P.E.
Striving to live Aloha
finishing.com - Pine Beach, New Jersey
Q, A, or Comment on THIS thread -or- Start a NEW Thread